Beim Diffusionsschweißen handelt es sich um einen Festkörperverbindungsprozess, der bei hohen Temperaturen stattfindet, typischerweise im Bereich von 50 % bis 75 % des Schmelzpunkts der zu verbindenden Materialien. Dieser Prozess beruht auf der Atomdiffusion über die Grenzfläche der Materialien, die durch erhöhte Temperaturen erleichtert wird. Die genaue Temperatur hängt von den jeweiligen Materialien ab, liegt jedoch im Allgemeinen im Bereich von 900 bis 1400 °C, wie man es bei Prozessen wie CVD (Chemical Vapour Deposition) sieht, bei denen die Diffusionskontrolle bei hohen Temperaturen erreicht wird.
Wichtige Punkte erklärt:
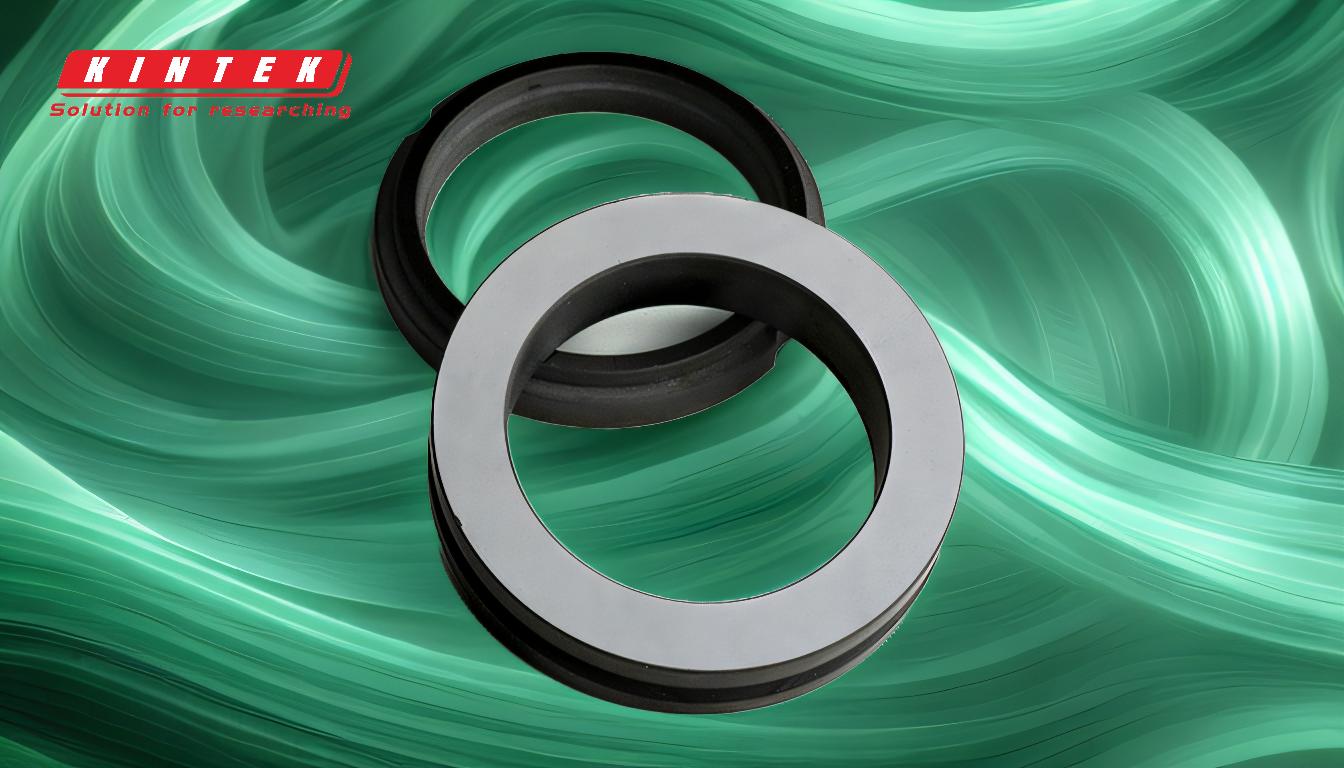
-
Temperaturbereich für das Diffusionsschweißen:
- Das Diffusionsschweißen erfolgt typischerweise bei hohen Temperaturen, oft zwischen 50 % und 75 % des Schmelzpunkts der zu verbindenden Materialien. Für viele Metalle entspricht dies einem Bereich von etwa 900 bis 1400 ℃.
- Dieser Temperaturbereich stellt sicher, dass die Atomdiffusion ausreichend aktiv ist, damit sich die Materialien verbinden können, ohne dass sie ihre Schmelzpunkte erreichen.
-
Rolle der Temperatur bei der Diffusionskontrolle:
- Bei hohen Temperaturen nimmt die atomare Beweglichkeit zu, was für die Diffusionsbindung unerlässlich ist. Der Prozess beruht auf der Bewegung von Atomen über die Grenzfläche der Materialien, um eine starke Bindung herzustellen.
- In der CVD-Technologie beispielsweise wird die Diffusionskontrolle bei hohen Temperaturen (900 bis 1400 °C) erreicht, was den Bedingungen entspricht, die für eine effektive Diffusionsbindung erforderlich sind.
-
Materialspezifische Überlegungen:
- Die genaue Temperatur für das Diffusionsschweißen variiert je nach den beteiligten Materialien. Beispielsweise können für Titanlegierungen Temperaturen um 900 bis 1000 °C erforderlich sein, während für Superlegierungen auf Nickelbasis möglicherweise Temperaturen von etwa 1200 bis 1400 °C erforderlich sind.
- Das Verständnis der Schmelzpunkte und Diffusionseigenschaften der Materialien ist entscheidend für die Bestimmung der optimalen Verbindungstemperatur.
-
Kinetische vs. Diffusionskontrolle:
- Die kinetische Kontrolle, die typischerweise bei niedrigeren Temperaturen durchgeführt wird, konzentriert sich auf die Geschwindigkeit chemischer Reaktionen. Im Gegensatz dazu betont die Diffusionskontrolle, die bei höheren Temperaturen stattfindet, die Bewegung von Atomen über Materialgrenzflächen hinweg.
- Beim Diffusionsschweißen ist ein Hochtemperaturbereich (900 bis 1400 °C) erforderlich, um sicherzustellen, dass Diffusionsprozesse dominieren und eine starke und dauerhafte Verbindung entsteht.
-
Praktische Auswirkungen für Käufer von Geräten und Verbrauchsmaterialien:
- Bei der Auswahl von Geräten für das Diffusionsschweißen ist es wichtig, Systeme zu wählen, die in der Lage sind, konstant hohe Temperaturen im erforderlichen Bereich (900 bis 1400 °C) aufrechtzuerhalten.
- Auch Verbrauchsmaterialien wie Schutzatmosphären oder Füllmaterialien sollten auf der Grundlage ihrer Kompatibilität mit der für das Diffusionsschweißen erforderlichen Hochtemperaturumgebung ausgewählt werden.
Durch das Verständnis dieser Schlüsselpunkte können Käufer fundierte Entscheidungen über die Ausrüstung und Materialien treffen, die für erfolgreiche Diffusionsschweißprozesse erforderlich sind.
Übersichtstabelle:
Aspekt | Details |
---|---|
Temperaturbereich | 900 bis 1400 ℃ (50 %–75 % des Materialschmelzpunkts) |
Rolle der hohen Temperatur | Verbessert die Atomdiffusion für eine starke Bindung |
Materialspezifische Beispiele | Titanlegierungen: 900–1000 ℃, Superlegierungen auf Nickelbasis: 1200–1400 ℃ |
Kinetik vs. Diffusion | Die Diffusionskontrolle erfordert hohe Temperaturen für die Atombewegung |
Überlegungen zur Ausrüstung | Systeme müssen konstant hohe Temperaturen (900–1400 ℃) aufrechterhalten. |
Benötigen Sie Hilfe bei der Auswahl der richtigen Ausrüstung für das Diffusionsschweißen? Kontaktieren Sie noch heute unsere Experten !