Die Magnetronzerstäubung wurde 1974 von Chapin erfunden und stellte einen bedeutenden Fortschritt in der Dünnschichttechnologie dar.Mit dieser Innovation wurden die Einschränkungen der früheren Diodenzerstäubung, wie niedrige Abscheidungsraten und hohe Kosten, durch die Einführung einer effizienteren und kostengünstigeren Methode überwunden.Aufgrund der höheren Abscheideraten und der besseren Leistung wurde das Magnetronsputtern schnell zu einem Eckpfeiler in verschiedenen Branchen.Die Technologie hat sich seither weiterentwickelt, mit Fortschritten beim reaktiven Gleichstromsputtern, beim gepulsten Sputtern und bei Hochionisationstechniken, was ihre Bedeutung in der modernen Fertigung und Forschung festigte.
Die wichtigsten Punkte werden erklärt:
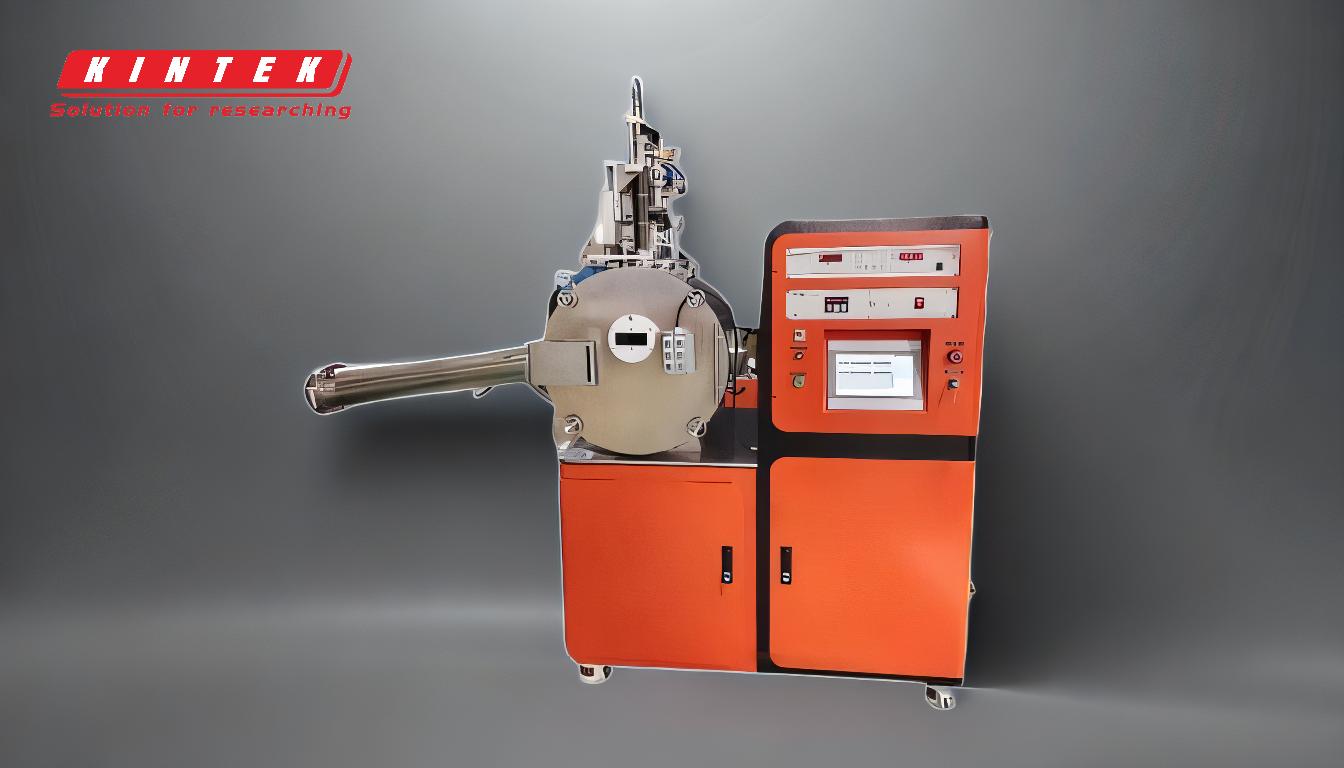
-
Erfindung des Magnetronsputterns:
- Die Magnetronzerstäubung wurde erfunden im 1974 von Chapin .
- Diese Erfindung war eine direkte Reaktion auf die Einschränkungen der Diodenzerstäubung, die seit den 1940er Jahren kommerziell genutzt wurde, aber mit niedrigen Abscheideraten und hohen Betriebskosten zu kämpfen hatte.
- Die Einführung des Magnetronsputterns revolutionierte die Dünnschichtabscheidung durch die Bereitstellung einer effizienteren und kostengünstigeren Alternative.
-
Historischer Kontext des Sputterns:
- Das Phänomen des Sputterns wurde erstmals in den 1850s aber es blieb eine wissenschaftliche Kuriosität bis in die 1940s als die Diodenzerstäubung kommerziell nutzbar wurde.
- Die Diodenzerstäubung war damals zwar bahnbrechend, hatte aber erhebliche Nachteile, darunter niedrige Abscheideraten und hohe Kosten, was ihre breite Anwendung einschränkte.
-
Vorteile des Magnetronsputterns:
- Höhere Ablagerungsraten:Durch das Magnetron-Sputtern konnte die Abscheidungsrate für dünne Schichten erheblich gesteigert werden, so dass es sich besser für industrielle Anwendungen eignet.
- Kosteneffizienz:Die Technologie senkt die Betriebskosten und macht sie für ein breiteres Spektrum von Anwendungen zugänglich.
- Verbesserte Leistung:Das Magnetronsputtern bot eine bessere Kontrolle über den Abscheidungsprozess, was zu qualitativ hochwertigeren dünnen Schichten führte.
-
Technologische Entwicklung:
- 1980s:In diesem Jahrzehnt entwickelte sich das reaktive DC-Sputtern, das die Möglichkeiten des Magnetron-Sputterns weiter verbesserte.
- 1990s:Der Schwerpunkt verlagert sich auf das gepulste Sputtern und die Verbesserung der Targetnutzung, wodurch der Prozess noch effizienter wird.
- 2000s:Die Fortschritte in der Hochionisationstechnik haben die Grenzen dessen, was mit Magnetronsputtern erreicht werden kann, erweitert und zu neuen Anwendungen und verbesserter Leistung geführt.
-
Auswirkungen auf die Industrie:
- Die Erfindung des Magnetron-Sputterns hatte tiefgreifende Auswirkungen auf verschiedene Branchen, darunter Elektronik, Optik und Materialwissenschaft.
- Seine Fähigkeit, hochwertige Dünnschichten zu geringeren Kosten und mit höherer Geschwindigkeit herzustellen, machte es zu einem unverzichtbaren Werkzeug in der modernen Fertigung und Forschung.
Zusammenfassend lässt sich sagen, dass das Magnetronsputtern 1974 erfunden wurde und die Grenzen früherer Sputterverfahren überwunden und die Dünnschichtabscheidung revolutioniert hat.Seine Vorteile in Bezug auf Abscheidungsraten, Kosteneffizienz und Leistung haben es zu einem Eckpfeiler der Technologie in verschiedenen Industriezweigen gemacht, wobei kontinuierliche Weiterentwicklungen seine Fähigkeiten weiter verbessern.
Zusammenfassende Tabelle:
Hauptaspekt | Einzelheiten |
---|---|
Erfindungsjahr | 1974 |
Erfinder | Chapin |
Vorläufertechnologie | Diodenzerstäubung (1940er Jahre) |
Wesentliche Vorteile | Höhere Abscheideraten, Kosteneffizienz, verbesserte Leistung |
Technologische Entwicklung | Reaktives DC-Sputtern (1980er Jahre), gepulstes Sputtern (1990er Jahre), Hochionisierung (2000er Jahre) |
Auswirkung auf Industrien | Elektronik, Optik, Materialwissenschaft |
Erfahren Sie, wie Magnetronsputtern Ihren Fertigungsprozess verbessern kann. Kontaktieren Sie uns noch heute !