Das Aufkohlungsverfahren wird zwar häufig zur Oberflächenhärtung von Stahlbauteilen eingesetzt, weist jedoch je nach verwendeter Methode (Atmosphären- oder Vakuumaufkohlung) mehrere Nachteile auf. Dazu gehören hohe Anfangskapitalkosten, die Notwendigkeit einer empirischen Prozesskontrolle, Umwelt- und Sicherheitsbedenken sowie Herausforderungen im Zusammenhang mit der Wartung und Nachbearbeitung der Ausrüstung. Jede Methode hat ihre eigenen Nachteile, wie z. B. Ruß- und Teerbildung beim Vakuumaufkohlen oder Qualitätsprobleme bei der Härtetiefe beim Atmosphärenaufkohlen. Das Verständnis dieser Nachteile ist für Käufer von Geräten und Verbrauchsmaterialien von entscheidender Bedeutung, um fundierte Entscheidungen treffen zu können.
Wichtige Punkte erklärt:
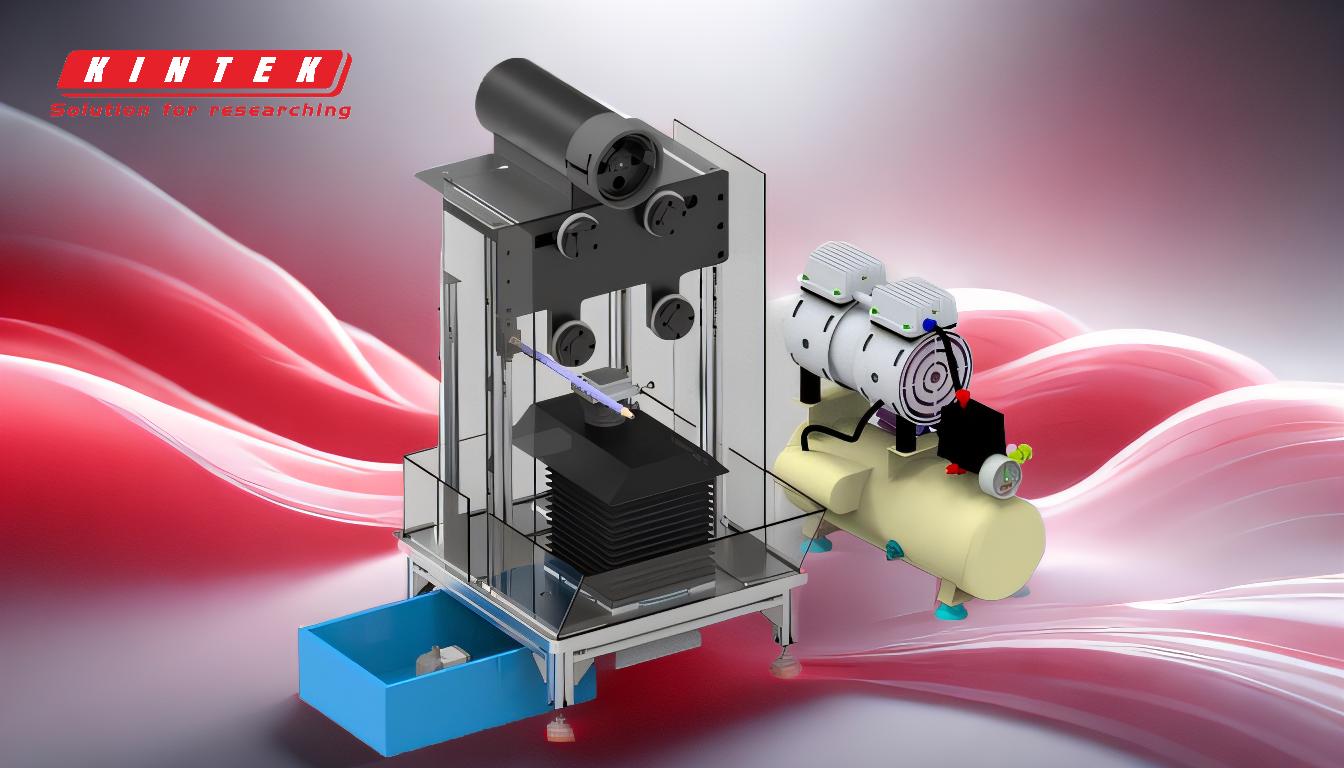
-
Hohe Erstinvestitionskosten für die Ausrüstung:
- Erläuterung: Vakuumaufkohlung erfordert spezielle Ausrüstung, die im Vergleich zur herkömmlichen Atmosphärenaufkohlung oft mit einer höheren Anfangsinvestition verbunden ist. Dazu gehören fortschrittliche Vakuumkammern, Gashandhabungssysteme und präzise Temperaturkontrollmechanismen.
- Auswirkungen: Für Unternehmen bedeutet dies einen erheblichen finanziellen Vorabaufwand, der für kleinere Betriebe oder solche mit begrenzten Budgets möglicherweise nicht machbar ist.
-
Empirische Prozesskontrolle:
- Erläuterung: Sowohl das Atmosphären- als auch das Vakuumaufkohlen stützen sich stark auf empirische Daten, um wiederholbare Ergebnisse zu erzielen. Das bedeutet, dass die Bediener über umfassende Erfahrung verfügen und zahlreiche Probeläufe durchführen müssen, um die optimalen Einstellungen für jede spezifische Last zu ermitteln.
- Auswirkungen: Diese Abhängigkeit von Versuch und Irrtum kann aufgrund des Bedarfs an qualifiziertem Personal und potenzieller Materialverschwendung beim Testen zu Ineffizienzen, längerer Produktionszeit und höheren Kosten führen.
-
Bildung von Ruß und Teer (Vakuumaufkohlung):
- Erläuterung: Beim Vakuumaufkohlen können Art, Druck und Menge des eingeleiteten Kohlenwasserstoffgases zur Bildung von Ruß und Teer führen. Diese Nebenprodukte können die Ausrüstung und die verarbeiteten Teile verunreinigen.
- Auswirkungen: Dies erfordert eine häufige Reinigung und Wartung der Ausrüstung, was Ausfallzeiten und Betriebskosten erhöht. Darüber hinaus kann das Vorhandensein von Ruß und Teer die Qualität der aufgekohlten Schicht beeinträchtigen und möglicherweise zu Nacharbeit oder Verschrottung von Teilen führen.
-
Anlagenkonditionierung (Atmosphärenaufkohlung):
- Erläuterung: Atmosphärenaufkohlungsanlagen müssen ordnungsgemäß konditioniert werden, wenn sie für einen bestimmten Zeitraum im Leerlauf oder abgeschaltet sind. Dabei muss das System gespült und sichergestellt werden, dass die Atmosphäre korrekt ausgeglichen ist, bevor der Betrieb wieder aufgenommen wird.
- Auswirkungen: Diese Anforderung kann zu Produktionsverzögerungen führen, insbesondere wenn die Anlage häufig angehalten und gestartet wird. Es erhöht auch die betriebliche Komplexität und erfordert zusätzliche Ressourcen für die Wartung.
-
Große Materialzugabe für die Nachbearbeitung:
- Erläuterung: Beide Methoden erfordern häufig erhebliche Materialaufmaße, um Nachbearbeitungsvorgänge wie Schleifen oder maschinelle Bearbeitung zu ermöglichen. Dies ist notwendig, um nach dem Aufkohlen die endgültigen Abmessungen und die Oberflächenbeschaffenheit zu erreichen.
- Auswirkungen: Dies erhöht die Materialkosten und kann zu einem höheren Abfallaufkommen führen, was auf lange Sicht möglicherweise nicht nachhaltig oder kosteneffektiv ist.
-
Qualitätsprobleme bei der Falltiefe:
- Erläuterung: Das Erreichen einer gleichmäßigen Härtetiefe kann bei der Atmosphärenaufkohlung aufgrund von Schwankungen im Kohlenstoffpotenzial der Atmosphäre und anderen Prozessvariablen eine Herausforderung darstellen.
- Auswirkungen: Eine inkonsistente Gehäusetiefe kann dazu führen, dass Teile nicht den Spezifikationen entsprechen, was zu Nacharbeit, Ausschuss oder sogar zu Wartungsausfällen führt. Diese Variabilität kann auch Qualitätskontrollprozesse erschweren.
-
Umweltverschmutzung und Sicherheitsbedenken:
- Erläuterung: Beim Aufkohlen in der Atmosphäre kommen potenziell gefährliche Gase zum Einsatz, die eine ständige Überwachung erfordern, um Umweltverschmutzung zu verhindern und die Sicherheit am Arbeitsplatz zu gewährleisten.
- Auswirkungen: Dies erhöht die betriebliche Belastung und erfordert Investitionen in Sicherheitsausrüstung, Schulung und Einhaltung von Umweltvorschriften. Wenn diese Aspekte nicht ordnungsgemäß gehandhabt werden, kann dies zu Geldstrafen, rechtlichen Problemen und einer Rufschädigung des Unternehmens führen.
Zusammenfassend lässt sich sagen, dass das Aufkohlen zwar eine wirksame Methode zur Verbesserung der Oberflächeneigenschaften von Stahlbauteilen ist, jedoch mit mehreren Nachteilen verbunden ist, die sorgfältig abgewogen werden müssen. Dazu gehören hohe Anschaffungskosten, die Notwendigkeit einer empirischen Prozesskontrolle, Umwelt- und Sicherheitsbedenken sowie Herausforderungen im Zusammenhang mit der Wartung und Nachbearbeitung der Ausrüstung. Das Verständnis dieser Nachteile ist wichtig, um fundierte Entscheidungen bei der Auswahl und Implementierung von Aufkohlungsprozessen treffen zu können.
Übersichtstabelle:
Nachteil | Verfahren | Auswirkungen |
---|---|---|
Hohe Erstinvestitionskosten für die Ausrüstung | Vakuumaufkohlung | Erhebliche Vorabinvestition, eine Herausforderung für kleinere Betriebe |
Empirische Prozesskontrolle | Beide Methoden | Erfordert qualifiziertes Personal, Versuch und Irrtum und eine längere Produktionszeit |
Bildung von Ruß und Teer | Vakuumaufkohlung | Häufige Reinigung, Geräteverschmutzung und mögliche Nacharbeit von Teilen |
Gerätekonditionierung | Atmosphärenaufkohlung | Verzögerungen in der Produktion und zusätzliche betriebliche Komplexität |
Große materielle Zulagen | Beide Methoden | Erhöhte Materialkosten und höheres Abfallaufkommen |
Qualitätsprobleme bei der Falltiefe | Atmosphärenaufkohlung | Inkonsistente Ergebnisse, Nacharbeit oder Ausschuss von Teilen |
Umweltverschmutzung | Atmosphärenaufkohlung | Sicherheitsbedenken, Einhaltung gesetzlicher Vorschriften und mögliche Bußgelder |
Benötigen Sie Hilfe bei der Auswahl des richtigen Oberflächenhärtungsverfahrens? Kontaktieren Sie noch heute unsere Experten für maßgeschneiderte Lösungen!