Ein Vakuum ist für die Abscheidung von Dünnschichten unerlässlich, da es eine Umgebung schafft, die die Bildung von hochwertigen, reinen und haftenden Schichten gewährleistet.Durch die Verringerung des Gasdrucks erhöht das Vakuum die mittlere freie Weglänge der verdampften Atome und verhindert, dass sie zusammenstoßen und unerwünschte Partikel oder Ruß bilden.Außerdem wird die Verunreinigung durch Verunreinigungen wie Sauerstoff, Stickstoff und Kohlendioxid, die die Filmqualität beeinträchtigen können, minimiert.Darüber hinaus ermöglicht eine Vakuumumgebung eine präzise Steuerung der Gas- und Dampfzusammensetzung, erleichtert die Steuerung des Massenstroms und unterstützt die Schaffung einer Niederdruck-Plasmaumgebung.Diese Faktoren zusammen ermöglichen die Abscheidung von dünnen Schichten mit hoher Reinheit, starker Haftung und gewünschten Eigenschaften.
Die wichtigsten Punkte werden erklärt:
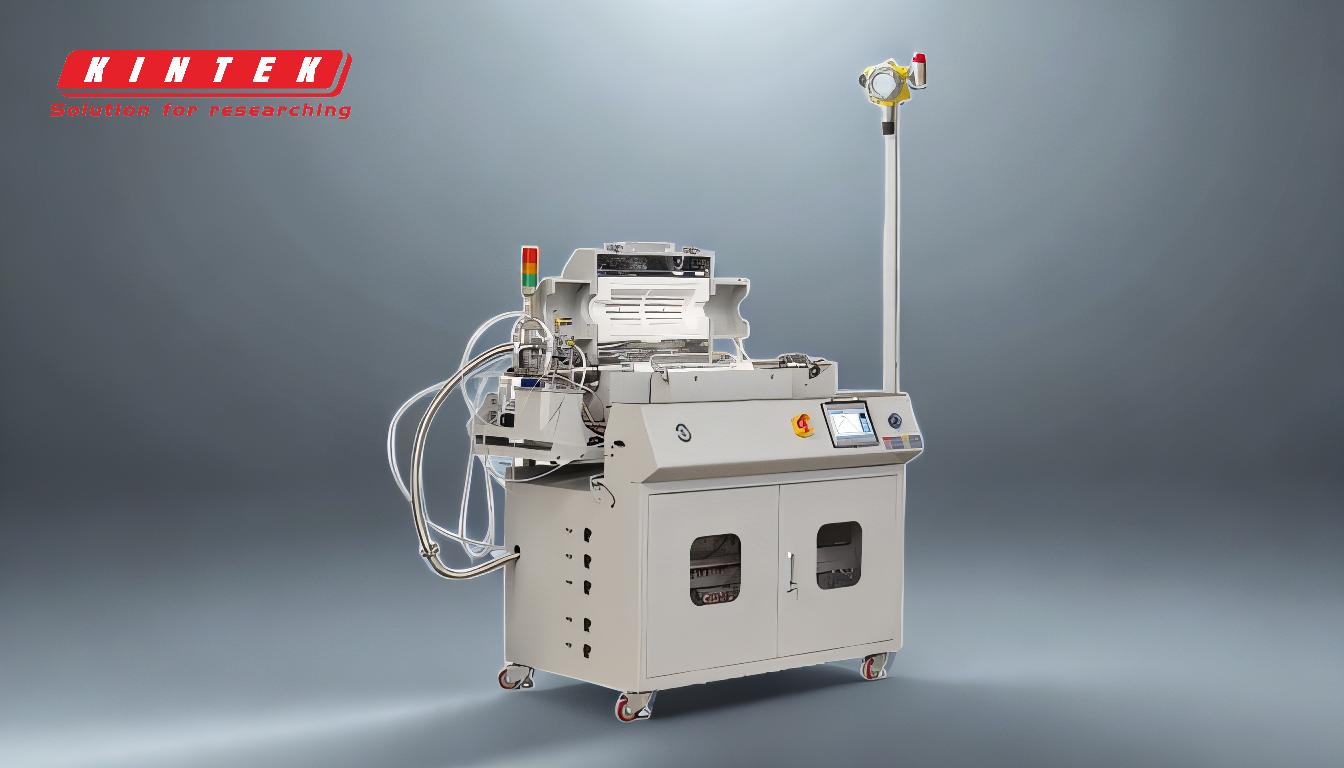
-
Erhöhter mittlerer freier Weg:
- Im Vakuum ist der Gasdruck deutlich geringer, wodurch sich die mittlere freie Weglänge der verdampften Atome erhöht.Die mittlere freie Weglänge ist die durchschnittliche Entfernung, die ein Atom zurücklegen kann, bevor es mit einem anderen Atom oder Molekül zusammenstößt.
- Eine längere mittlere freie Weglänge gewährleistet, dass die verdampften Atome direkt auf das Substrat gelangen, ohne zusammenzustoßen und unerwünschte Partikel oder Ruß zu bilden.Dies ist entscheidend für die Erzielung einer gleichmäßigen und hochwertigen Dünnschicht.
-
Verringerung der Kontamination:
- Eine Vakuumumgebung minimiert die Anwesenheit von Verunreinigungen wie Sauerstoff, Stickstoff, Kohlendioxid und Wasserdampf.Diese Verunreinigungen können mit dem Filmmaterial reagieren und zu Defekten, schlechter Haftung oder unerwünschten chemischen Eigenschaften führen.
- Durch die Verringerung der Verunreinigungen sorgt das Vakuum dafür, dass die abgeschiedene Schicht eine hohe Reinheit aufweist und fest auf dem Substrat haftet, was für Anwendungen, die präzise Materialeigenschaften erfordern, unerlässlich ist.
-
Kontrolle der Gas- und Dampfzusammensetzung:
- In einem Vakuum kann die Zusammensetzung der Gase und Dämpfe in der Beschichtungskammer genau gesteuert werden.Dies ermöglicht die Einleitung bestimmter Gase oder Dämpfe, die für bestimmte Abscheidungsverfahren wie reaktives Sputtern oder chemische Gasphasenabscheidung (CVD) erforderlich sind.
- Die kontrollierte Gaszusammensetzung gewährleistet, dass das Filmmaterial in der gewünschten Weise reagiert oder sich abscheidet, was zu Filmen mit maßgeschneiderten Eigenschaften führt.
-
Erleichterung der Massenflusskontrolle:
- Eine Vakuumumgebung ermöglicht eine präzise Steuerung des Gas- und Dampfstroms in die Prozesskammer.Dies ist entscheidend für Verfahren wie die Atomlagenabscheidung (ALD) oder die plasmaunterstützte chemische Gasphasenabscheidung (PECVD), bei denen eine genaue Dosierung der Reaktanten erforderlich ist.
- Die Steuerung des Massenstroms gewährleistet eine gleichmäßige Schichtdicke und -zusammensetzung, die für Anwendungen in der Mikroelektronik, Optik und Beschichtung unerlässlich sind.
-
Schaffung einer Niederdruck-Plasmaumgebung:
- Viele Verfahren zur Abscheidung von Dünnschichten, wie z. B. das Sputtern und die plasmaunterstützte Abscheidung, beruhen auf der Erzeugung eines Plasmas.Eine Vakuumumgebung unterstützt die Bildung eines stabilen Niederdruckplasmas, das für die Ionisierung von Gasen und die Steigerung der Abscheideraten erforderlich ist.
- Das Plasma erhöht die Energie der Partikel, verbessert die Schichthaftung und ermöglicht die Abscheidung von Materialien bei niedrigeren Temperaturen.
-
Verhinderung von Keimbildung im Dampf:
- In Abwesenheit eines Vakuums können verdampfte Atome kollidieren und Keime bilden, die sich zu Clustern oder Ruß zusammenballen, anstatt sich als dünner Film abzulagern.Dies kann zu ungleichmäßigen Schichten mit schlechten mechanischen und optischen Eigenschaften führen.
- Ein Vakuum verhindert die Keimbildung, indem es dafür sorgt, dass die Atome direkt zum Substrat wandern, was zu einem glatten und gleichmäßigen Film führt.
-
Hohe thermische Verdampfungsrate:
- Eine Vakuumumgebung ermöglicht hohe thermische Verdampfungsraten, die für Verfahren wie die thermische Verdampfungsbeschichtung erforderlich sind.Der reduzierte Druck sorgt dafür, dass das verdampfte Material das Substrat ohne nennenswerte Verluste oder Streuung erreicht.
- Dies ist besonders wichtig für die Abscheidung von Materialien mit hohen Schmelzpunkten oder für die Herstellung von Schichten mit besonderen optischen oder elektrischen Eigenschaften.
-
Minimierung der gasförmigen Verunreinigung:
- Durch die Verringerung der Dichte unerwünschter Atome und Moleküle sorgt ein Vakuum dafür, dass sich das Filmmaterial nicht mit Verunreinigungen in der Luft verbindet.Dies ist entscheidend für Anwendungen, die hochreine Filme erfordern, wie z. B. die Halbleiterherstellung oder optische Beschichtungen.
- Die Minimierung der gasförmigen Verunreinigung verbessert auch die mechanische und chemische Stabilität der Folie.
-
Starke Adhäsion und hohe Reinheit:
- Eine Hochvakuumumgebung sorgt dafür, dass die abgeschiedene Schicht fest auf dem Substrat haftet und eine hohe Reinheit beibehält.Dies wird durch die Beseitigung von Verunreinigungen und die Bereitstellung einer sauberen Abscheidungsoberfläche erreicht.
- Starke Haftung und hohe Reinheit sind entscheidend für Filme, die in anspruchsvollen Anwendungen wie Schutzbeschichtungen, Sensoren und elektronischen Geräten eingesetzt werden.
-
Verhinderung von Filmdegradation:
- Ohne Vakuum können Verunreinigungen wie Sauerstoff und Feuchtigkeit mit dem Folienmaterial reagieren und Oxidation, Korrosion oder andere Formen des Abbaus verursachen.Dies kann die Leistung und Langlebigkeit der Folie beeinträchtigen.
- Eine Vakuumumgebung verhindert solche Reaktionen und sorgt dafür, dass der Film seine gewünschten Eigenschaften über lange Zeit beibehält.
Zusammenfassend lässt sich sagen, dass ein Vakuum für die Abscheidung von Dünnschichten unverzichtbar ist, da es eine kontrollierte Umgebung schafft, die die Bildung hochwertiger, reiner und haftender Schichten gewährleistet.Durch die Berücksichtigung von Faktoren wie Verschmutzung, mittlere freie Weglänge und Gaszusammensetzung ermöglicht das Vakuum präzise und zuverlässige Abscheidungsprozesse, die für fortschrittliche Anwendungen in verschiedenen Branchen entscheidend sind.
Zusammenfassende Tabelle:
Hauptnutzen | Beschreibung |
---|---|
Erhöhter mittlerer freier Weg | Verringert Kollisionen und gewährleistet gleichmäßige und hochwertige dünne Schichten. |
Verringerung von Verunreinigungen | Minimiert Verunreinigungen wie Sauerstoff und Stickstoff für hochreine Filme. |
Kontrolle der Gaszusammensetzung | Ermöglicht die präzise Einführung spezifischer Gase für maßgeschneiderte Filmeigenschaften. |
Erleichterung der Massenflusskontrolle | Gewährleistet eine gleichbleibende Schichtdicke und -zusammensetzung für kritische Anwendungen. |
Niederdruck-Plasmaumgebung | Unterstützt ein stabiles Plasma für verbesserte Abscheidungsraten und Haftung. |
Verhinderung von Keimbildung | Verhindert die Bildung von Clustern und sorgt für glatte und gleichmäßige Filme. |
Hohe thermische Verdampfungsrate | Ermöglicht die effiziente Abscheidung von Materialien mit hohem Schmelzpunkt. |
Starke Adhäsion & hohe Reinheit | Sorgt dafür, dass die Filme stark haften und ihre Reinheit für anspruchsvolle Anwendungen erhalten bleibt. |
Verhinderung von Filmverschlechterung | Schützt die Filme vor Oxidation und Korrosion und bewahrt so die Leistung über lange Zeit. |
Sind Sie bereit für eine hochwertige Dünnschichtabscheidung? Kontaktieren Sie uns noch heute um mehr über unsere Vakuumlösungen zu erfahren!