Die physikalische Gasphasenabscheidung (PVD) ist ein wichtiger Prozess in der modernen Fertigung, insbesondere für die Herstellung dünner Schichten und Beschichtungen auf Substraten.Die Durchführung von PVD in einer Vakuumumgebung ist aus mehreren Gründen von entscheidender Bedeutung, u. a. um Verunreinigungen zu verringern, die mittlere freie Weglänge der Partikel zu erhöhen und eine präzise Steuerung des Abscheidungsprozesses zu ermöglichen.Ein Vakuum minimiert das Vorhandensein unerwünschter Atome und Moleküle und gewährleistet eine saubere und kontrollierte Umgebung, die für hochwertige Beschichtungen erforderlich ist.Außerdem ermöglicht es einen effizienten Materialtransfer und eine gute Haftung, die für Anwendungen in der Mikroelektronik, Optik und anderen fortschrittlichen Technologien entscheidend sind.
Die wichtigsten Punkte werden erklärt:
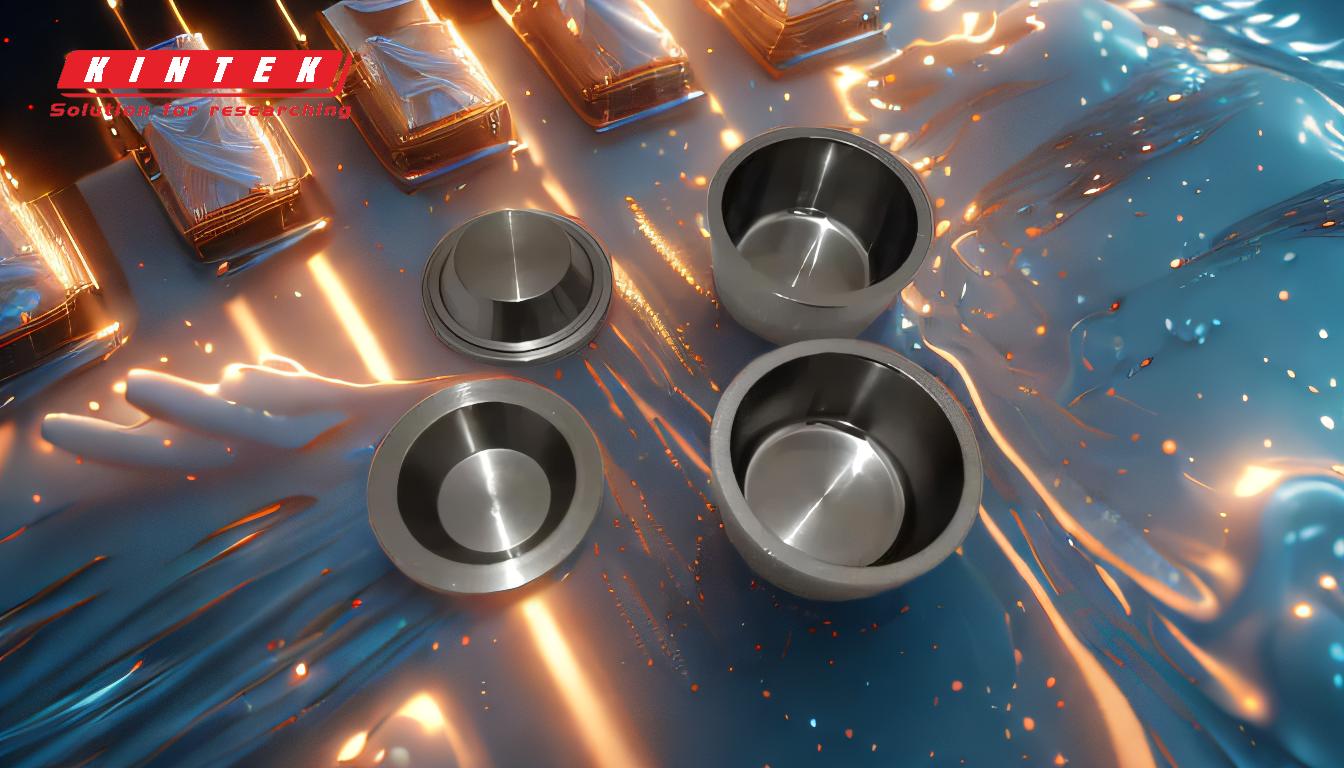
-
Verringerung der Partikeldichte und Erhöhung der mittleren freien Weglänge:
- In einer Vakuumumgebung ist die Dichte der Gasmoleküle erheblich reduziert.Dadurch erhöht sich die mittlere freie Weglänge der Teilchen, d. h. die durchschnittliche Entfernung, die ein Teilchen zurücklegt, bevor es mit einem anderen Teilchen zusammenstößt.Eine längere mittlere freie Weglänge sorgt dafür, dass das verdampfte Material direkt zum Substrat gelangen kann, ohne gestreut oder durch Zusammenstöße mit Gasmolekülen verlangsamt zu werden.Dieser direkte Weg ist entscheidend, um gleichmäßige und hochwertige Beschichtungen zu erzielen.
-
Minimierung von Verunreinigungen:
- Eine Vakuumumgebung reduziert das Vorhandensein unerwünschter Atome und Moleküle, wie Sauerstoff, Stickstoff und Wasserdampf, die die abgeschiedene Schicht verunreinigen können.Verunreinigungen können die Qualität der Beschichtung beeinträchtigen, was zu Defekten, verminderter Haftung und Leistungseinbußen führen kann.Durch die Aufrechterhaltung eines Hochvakuums sorgt das Verfahren für eine sauberere und kontrolliertere Umgebung, was besonders für Anwendungen wie die Mikrochip-Herstellung wichtig ist, wo selbst kleinste Verunreinigungen erhebliche Probleme verursachen können.
-
Kontrollierte Gas- und Dampfzusammensetzung:
- Ein Vakuum ermöglicht eine genaue Kontrolle der Zusammensetzung von Gasen und Dämpfen in der Prozesskammer.Diese Kontrolle ist wichtig, um die Eigenschaften der abgeschiedenen Schicht, wie z. B. ihre Dicke, Gleichmäßigkeit und chemische Zusammensetzung, maßzuschneidern.Durch Anpassung des Drucks und der Gaszusammensetzung können die Hersteller spezifische Materialeigenschaften erzielen, die für verschiedene Anwendungen erforderlich sind, z. B. optische Beschichtungen, verschleißfeste Schichten oder leitfähige Filme.
-
Hohe thermische Verdampfungsrate:
- Im Vakuum ist die thermische Verdampfungsrate von Stoffen im Vergleich zu atmosphärischen Bedingungen deutlich höher.Dies liegt daran, dass der reduzierte Druck den Siedepunkt der Materialien senkt, so dass sie bei niedrigeren Temperaturen verdampfen können.Eine hohe Verdampfungsrate sorgt für einen effizienten Materialtransfer und -auftrag, was für das Erreichen der gewünschten Schichtdicke und -qualität in einer angemessenen Zeitspanne entscheidend ist.
-
Verbesserte Materialhaftung:
- Da in einer Vakuumumgebung keine Luft oder andere Flüssigkeiten vorhanden sind, kann das verdampfte Material das Substrat mit mehr Energie erreichen.Diese erhöhte Energie verbessert die Haftung des Materials auf dem Substrat, was zu einer stärkeren und haltbareren Beschichtung führt.Eine verbesserte Haftung ist besonders wichtig für Anwendungen, bei denen die Beschichtung mechanischer Belastung, Temperaturschwankungen oder korrosiven Umgebungen ausgesetzt ist.
-
Wiederholbarer und kontrollierter Abscheidungsprozess:
- Eine Vakuumumgebung bietet einen stabilen und wiederholbaren Prozess, der für industrielle Anwendungen unerlässlich ist.Durch die Aufrechterhaltung konstanter Druck- und Temperaturbedingungen können die Hersteller einheitliche Beschichtungen mit vorhersehbaren Eigenschaften erzielen.Diese Wiederholbarkeit ist entscheidend für die Massenproduktion, bei der Konsistenz und Qualitätskontrolle von größter Bedeutung sind.
-
Niederdruck-Plasmaumgebung:
- Ein Vakuum erleichtert die Erzeugung einer Niederdruck-Plasmaumgebung, die häufig bei PVD-Verfahren wie dem Sputtern verwendet wird.Das Plasma verbessert die Ionisierung des verdampften Materials, wodurch sich die Energie und die Ausrichtung der Partikel bei der Ablagerung auf dem Substrat verbessern.Dies führt zu einer besseren Filmdichte, Haftung und Gesamtqualität.
-
Anwendungsspezifische Anforderungen:
- Bestimmte Anwendungen, wie die Herstellung von Mikrochips, CDs und DVDs, erfordern extrem saubere und kontrollierte Umgebungen.Ein Hochvakuum sorgt dafür, dass auch die kleinsten Partikel entfernt werden, um Defekte zu vermeiden, die die Funktionalität des Endprodukts beeinträchtigen könnten.Dieser Grad an Sauberkeit ist unter atmosphärischen Bedingungen unerreichbar.
Zusammenfassend lässt sich sagen, dass die PVD-Beschichtung in einer Vakuumumgebung unerlässlich ist, um hochwertige, gleichmäßige und kontaminationsfreie Schichten zu erhalten.Das Vakuum bietet die notwendigen Bedingungen für einen effizienten Materialtransfer, eine kontrollierte Abscheidung und eine verbesserte Haftung und ist daher für eine Vielzahl industrieller und technischer Anwendungen unverzichtbar.
Zusammenfassende Tabelle:
Hauptnutzen | Beschreibung |
---|---|
Reduzierte Kontamination | Minimiert unerwünschte Atome/Moleküle und sorgt für sauberere und hochwertigere Beschichtungen. |
Erhöhter mittlerer freier Weg | Vergrößert die Bewegungsstrecke der Partikel für eine gleichmäßige und präzise Abscheidung. |
Kontrollierte Gaszusammensetzung | Ermöglicht maßgeschneiderte Filmeigenschaften wie Dicke, Gleichmäßigkeit und chemische Zusammensetzung. |
Hohe thermische Verdampfungsrate | Ermöglicht einen effizienten Materialtransfer und eine schnellere Abscheidung. |
Verbesserte Adhäsion | Verbessert die Festigkeit und Haltbarkeit der Beschichtung bei anspruchsvollen Anwendungen. |
Wiederholbarer Prozess | Gewährleistet konsistente und vorhersehbare Ergebnisse für die Massenproduktion. |
Niederdruck-Plasmaumgebung | Erhöht die Filmdichte und -qualität durch verbesserte Ionisierung. |
Anwendungsspezifische Sauberkeit | Erfüllt die strengen Anforderungen für Branchen wie Mikroelektronik und Optik. |
Benötigen Sie eine Vakuum-PVD-Lösung für Ihre Fertigungsanforderungen? Kontaktieren Sie uns noch heute um mehr zu erfahren!