Einführung in das isostatische Pressen
Isostatisches Pressen ist ein Fertigungsverfahren, das zur Herstellung von Materialien mit hoher Dichte und verbesserten mechanischen Eigenschaften eingesetzt wird. Dabei wird gleichmäßiger Druck aus allen Richtungen auf das Material ausgeübt, um Hohlräume, Risse und Porosität zu beseitigen. Das Verfahren wird in zwei Kategorien unterteilt: das heißisostatische Pressen (HIP) und das kaltisostatische Pressen (CIP). Beim HIP-Verfahren werden Materialien bei hoher Temperatur und hohem Druck verdichtet, während das CIP-Verfahren bei Raumtemperatur und geringerem Druck arbeitet. Beide Verfahren werden in verschiedenen Industriezweigen eingesetzt, z. B. in der Luft- und Raumfahrt, der Biomedizin und der Energieerzeugung, um komplexe Formen und Teile mit hoher Festigkeit und Haltbarkeit herzustellen.
Zum Inhaltsverzeichnis
Überblick über das heißisostatische Pressen (HIP)
Heiß-Isostatisches Pressen (HIP) ist ein weit verbreitetes Verfahren zur Herstellung verschiedener Materialien, darunter Hochleistungslegierungen, Keramik und Verbundwerkstoffe. Dabei wird ein Material in einem versiegelten Behälter mit Hitze und Druck beaufschlagt, um seine mechanischen Eigenschaften wie Festigkeit, Duktilität und Zähigkeit zu verbessern. Während des HIP-Verfahrens wird das Material auf eine hohe Temperatur erhitzt, in der Regel auf über 1000 °C, und mit einem Inertgas, z. B. Argon, auf bis zu 200 MPa unter Druck gesetzt.
Wie funktioniert HIP?
Das HIP-Verfahren trägt dazu bei, innere Defekte wie Poren und Risse zu beseitigen, indem das Material verfestigt und gleichmäßig geschrumpft wird. Das Verfahren eignet sich für die Herstellung komplexer Formen und komplizierter Teile, darunter Turbinenschaufeln, Raketendüsen und medizinische Implantate. HIP hat auch den Vorteil, dass beschädigte Bauteile wie Turbinenschaufeln repariert und wiederhergestellt werden können, indem Risse entfernt und die ursprünglichen Eigenschaften wiederhergestellt werden.
Vergleich mit Heißpressen
Im Vergleich zum Heißpressen kann das HIP-Verfahren Materialformen liefern, die sich nach dem Druck nicht wesentlich von der ursprünglichen Form unterscheiden. Ein Material kann auch nach einer Formänderung seine ursprüngliche Form beibehalten und wird durch die Verarbeitung der Produkte relativ wenig eingeschränkt. Durch die volle Ausnutzung dieser Eigenschaften wurde HIP in verschiedenen Bereichen eingesetzt.
HIP-Anwendung
HIP wird in vielen Bereichen eingesetzt, z. B. beim Drucksintern von Pulver, beim Diffusionsverbinden verschiedener Arten von Werkstoffen, bei der Beseitigung von Restporen in gesinterten Teilen, bei der Beseitigung innerer Defekte in Gussteilen, bei der Verjüngung von durch Ermüdung oder Kriechen beschädigten Teilen, bei der hochdruckimprägnierten Karbonisierungsmethode usw.
Druckmedium
Argongas mit einer Temperatur von 1000°C und einem Druck von 98 MPa verursacht aufgrund seiner geringen Dichte und Viskosität sowie seines hohen thermischen Ausdehnungskoeffizienten wahrscheinlich eine starke Konvektion. Daher sind die Wärmeübergangskoeffizienten von HIP-Anlagen höher als die eines gewöhnlichen elektronischen Ofens.
HIP-Behandlung
Die Materialien müssen je nach Situation unterschiedlich behandelt werden. Zu den typischsten Methoden gehören die "Kapselmethode" und die "kapselfreie Methode". Isostatisches Pressen ist ein pulvermetallurgisches (PM) Formgebungsverfahren, bei dem ein Pulverpressling in alle Richtungen mit gleichem Druck beaufschlagt wird, wodurch eine maximale Einheitlichkeit von Dichte und Mikrostruktur ohne die geometrischen Einschränkungen des einachsigen Pressens erreicht wird.
Vorteile von HIP
Das heißisostatische Pressen ist ein bewährtes Verfahren zur Verbesserung einer Vielzahl von Werkstoffen wie Titan, Stahl, Aluminium und Superlegierungen. Es kann den Ausschuss reduzieren, die Ausbeute verbessern, Knetkomponenten durch Gussteile ersetzen, die Anforderungen an die Qualitätskontrolle durch Verbesserung der Materialeigenschaften und Verringerung der Streuung der Eigenschaften reduzieren, die Materialeigenschaften optimieren, die Anforderungen an die nachfolgende Wärmebehandlung minimieren, die Zuverlässigkeit und die Verlängerung der Lebensdauer erhöhen, die Gesamtproduktionskosten eines Produkts senken, usw.
Zusammenfassend lässt sich sagen, dass das heißisostatische Pressen eine äußerst effektive Methode zur Verbesserung der mechanischen Eigenschaften von Werkstoffen und zur Herstellung komplexer Teile mit hoher Präzision und Genauigkeit ist.
Vorteile von HIP
Das Heiß-Isostatische Pressen (HIP) ist ein hervorragendes Herstellungsverfahren für Laborgeräte, da es vollständig konsolidierte Teile mit hoher Dichte und hervorragenden mechanischen Eigenschaften erzeugt. Hier sind einige der Vorteile von HIP:
Vollständig konsolidierte Teile
Mit HIP werden vollkonsolidierte Teile mit hoher Dichte hergestellt, d. h. das Material ist frei von Porosität. Dies führt zu verbesserten mechanischen Eigenschaften, wie z. B. hohe Festigkeit, Zähigkeit und Duktilität, und ist somit ideal für Anwendungen, die Hochleistungsmaterialien erfordern.
Komplexe Formen und hohe Maßgenauigkeit
HIP kann zur Herstellung komplexer Formen und Teile mit hoher Maßgenauigkeit verwendet werden, da Schrumpfung und Verformung während des Prozesses vermieden werden. Dies wird durch die gleichzeitige Anwendung von hoher Temperatur und hohem Druck in allen Richtungen erreicht, was zu einer gleichmäßigen Dichte des Materials führt.
Vielseitigkeit
Mit dem HIP-Verfahren kann eine breite Palette von Materialien verarbeitet werden, darunter Metalle, Keramik und Verbundwerkstoffe, was es zu einem vielseitigen Verfahren für die Herstellung von Laborgeräten macht. Es ermöglicht auch die gleichzeitige Verdichtung und Bindung von Pulvern oder porösen Körpern.
Kostengünstig
HIP ist ein kosteneffizientes Verfahren, da zusätzliche Verarbeitungsschritte, wie z. B. das Sintern, entfallen, was den Materialabfall und den Energieverbrauch reduziert. Es ermöglicht auch die Verarbeitung größerer Teile, was zu Einsparungen bei den Produktionskosten führen kann.
Verbesserte Eigenschaften
HIP verbessert die mechanischen Eigenschaften der zu bearbeitenden Teile. Erreicht wird dies durch die Beseitigung interner Porosität, die Erzielung einer feinkörnigen Struktur, die die Gleichmäßigkeit der Teile fördert, und die Ermöglichung der Diffusionsbindung ähnlicher und ungleicher Materialien, entweder in Pulver- oder in fester Form. Dies führt unter anderem zu einer verbesserten Schlagzähigkeit, Duktilität und Ermüdungsfestigkeit.
Zusammenfassend lässt sich sagen, dass das heißisostatische Pressen eine wesentliche Technologie für die Herstellung moderner Laborgeräte ist, die Hochleistungsmaterialien erfordern. Seine Fähigkeit, voll verfestigte Teile mit hoher Dichte und hervorragenden mechanischen Eigenschaften herzustellen, macht es zu einem vielseitigen und kosteneffizienten Verfahren, das für die Herstellung komplexer Formen aus einer Vielzahl von Materialien eingesetzt werden kann.
Nachteile von HIP
Hohe Kosten für Ausrüstung und Wartung
Für das HIP-Verfahren sind spezielle Anlagen erforderlich, die hohem Druck und hohen Temperaturen standhalten können und in der Anschaffung und Wartung teuer sein können. Außerdem erfordert das Verfahren einen erheblichen Energieaufwand, um die hohen Temperaturen aufrechtzuerhalten, was die Gesamtkosten der Produktion erhöhen kann.
Eingeschränkte Auswahl an Materialien, die verarbeitet werden können
Das HIP-Verfahren wird in der Regel für Metalle und Keramiken eingesetzt, eignet sich aber nicht unbedingt für die Verarbeitung von Polymeren oder anderen Materialien, die empfindlich auf hohe Temperaturen und Drücke reagieren. Dies schränkt die Vielseitigkeit des Verfahrens ein und kann zusätzliche Verarbeitungsmethoden erfordern, um die gewünschten Materialeigenschaften zu erzielen.
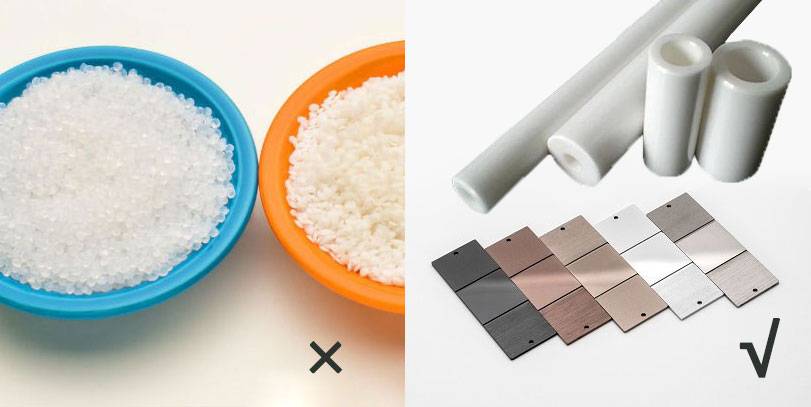
Eigenspannungen im Material
HIP kann auch zur Bildung von Eigenspannungen im Material führen, die Risse oder Verformungen verursachen können. Diese Spannungen können durch ungleichmäßige Erwärmung oder Abkühlung während des Prozesses oder durch ungleichmäßige Druckausübung entstehen. Um dieses Problem zu entschärfen, können Nachbearbeitungsmethoden erforderlich sein, um die Eigenspannungen abzubauen und sicherzustellen, dass das Material die gewünschten Spezifikationen erfüllt.
Zusammenfassend lässt sich sagen, dass das HIP-Verfahren zwar mehrere Vorteile für die Verdichtung von Materialien bietet, aber auch einige Nachteile aufweist, die es zu berücksichtigen gilt. Dazu gehören die hohen Kosten für Ausrüstung und Wartung, die eingeschränkte Auswahl an Materialien, die verarbeitet werden können, und das Potenzial für Eigenspannungen im Material. Wenn Ingenieure und Forscher diese Einschränkungen kennen, können sie fundierte Entscheidungen darüber treffen, wann sie HIP einsetzen und wie sie das Verfahren für ihre spezifischen Anwendungen optimieren können.
Überblick über das kaltisostatische Pressen (CIP)
Kaltisostatisches Pressen (CIP) ist ein Verfahren zur Formgebung und Verdichtung von Pulvern zu Komponenten unterschiedlicher Größe und Form. Das Verfahren wird bei Raumtemperatur und niedrigerem Druck durchgeführt, im Gegensatz zum heißisostatischen Pressen (HIP), das bei höheren Temperaturen durchgeführt wird.
Wie funktioniert das CIP-Verfahren?
Beim CIP-Verfahren wird das Material in ein Bad mit einer unter Druck stehenden Flüssigkeit, in der Regel Wasser, getaucht und mit Hilfe eines isostatischen Druckbehälters aus allen Richtungen unter Druck gesetzt. Der Druck hilft, das Material zu komprimieren und Porosität oder Hohlräume im Material zu entfernen. Bei diesem Verfahren wird eine flexible Gummiform verwendet, die gleichmäßigen Druck auf das Material ausübt. Die Form wird in einem Druckbehälter in eine Hydraulikflüssigkeit eingelegt, auf die ein hoher Druck (in der Regel zwischen 10.000 und 60.000 psi) ausgeübt wird, der gleichmäßig auf das Material verteilt wird.
Vorteile von CIP
CIP ist ein beliebtes Verfahren, weil damit Teile mit einem hohen Maß an Gleichmäßigkeit, Festigkeit und Dichte hergestellt werden können, was sie ideal für den Einsatz in kritischen Anwendungen wie Luft- und Raumfahrt, Medizin und Verteidigung macht. Darüber hinaus lassen sich mit CIP komplexe Formen herstellen, die mit anderen Verfahren nur schwer zu realisieren sind.
Vergleich mit uniaxialem Pressen
Sowohl das uniaxiale Pressen als auch das CIP sind Verfahren zur Verdichtung von Pulverproben. Beim uniaxialen Pressen wird eine Kraft entlang einer Achse ausgeübt, während beim CIP die Probe in einen flexiblen Beutel oder eine Form gegeben und in einer Kammer in eine Hydraulikflüssigkeit eingelegt wird. Das flüssige Medium wird mit hohem Druck beaufschlagt, der wiederum einen gleichmäßigen Druck in alle Richtungen auf die Probe ausübt. Dieses Verfahren ermöglicht einen wesentlich höheren Verdichtungsgrad als das einachsige Pressen und kann daher zur Herstellung großer Proben verwendet werden.
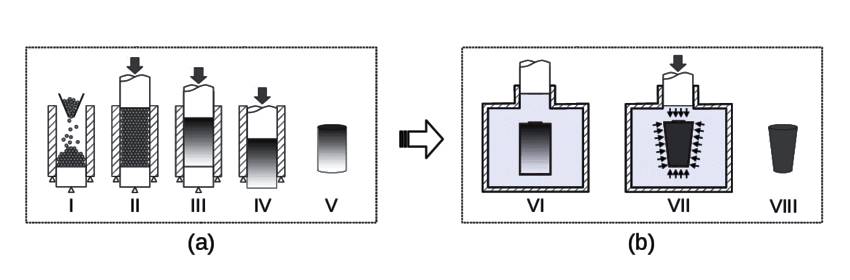
Arten von CIP
Es gibt zwei derzeit weltweit anerkannte CIP-Verfahren, die Nasssacktechnik und die Trockensacktechnik. Bei der Nasssacktechnik wird das Pulver in eine Form gefüllt und außerhalb des Druckbehälters dicht verschlossen. Nach dem Befüllen der Form mit Pulver wird die Form in die Druckflüssigkeit im Druckbehälter eingetaucht. Bei der Trockenbeuteltechnik hingegen wird die Form im Druckbehälter fixiert. Das Pulver wird in die Form gefüllt, während sie sich noch im Druckbehälter befindet.
Vorteile von CIP gegenüber einachsigem Pressen
CIP bietet einheitlichere Produkteigenschaften, eine größere Homogenität und eine genauere Kontrolle der Abmessungen des fertigen Produkts. Es bietet eine größere Flexibilität bei der Form und Größe des Endprodukts, und es sind längere Aspektverhältnisse möglich. Die verbesserte Verdichtung des Pulvers führt zu einer besseren Verdichtung, und CIP kann Materialien mit unterschiedlichen Eigenschaften und Formen verarbeiten. Und schließlich kann CIP die Zykluszeiten verkürzen und die Produktivität steigern.
Zusammenfassend lässt sich sagen, dass CIP eine leistungsstarke Technik ist, um Pulver zu Komponenten unterschiedlicher Größe und Form zu formen und zu verdichten. Es bietet mehrere Vorteile gegenüber dem einachsigen Pressen und ist ein bevorzugtes Verfahren zur Herstellung hochwertiger Materialien für kritische Anwendungen.
Vorteile von CIP
Das kaltisostatische Pressen (CIP) bietet mehrere Vorteile gegenüber anderen ähnlichen Verfahren. Einige der wichtigsten Vorteile von CIP sind die folgenden
Gleichmäßige Festigkeit
Beim Kalt-Isostatischen Pressen wird der Druck in alle Richtungen gleichmäßig ausgeübt, was zu Materialien mit gleichmäßiger Festigkeit führt. Diese gleichmäßige Festigkeit macht die Materialien effizienter und effektiver.
Vielseitigkeit
Mit dem CIP-Verfahren können komplexe Formen hergestellt werden, die mit anderen Fertigungsmethoden nur schwer zu realisieren sind. Auch großformatige Werkstoffe können ohne Qualitätseinbußen hergestellt werden.
Korrosionsbeständigkeit
CIP verbessert die Korrosionsbeständigkeit von Materialien, was zu einer längeren Lebensdauer als bei den meisten anderen Materialien führt.
Verbesserte mechanische Eigenschaften
CIP verbessert die mechanischen Eigenschaften von Werkstoffen, einschließlich Duktilität und Festigkeit.
Geeignet für die Pulvermetallurgie
CIP wird für den Verdichtungsschritt in der Pulvermetallurgie verwendet, der unmittelbar vor dem Sinterschritt erfolgt. Es wird häufig zur Herstellung komplexer Formen und Abmessungen verwendet.
Herstellung von Refraktärmetallen
CIP wird für die Herstellung von Refraktärmetallen wie Wolfram, Molybdän und Tantal verwendet. Diese Metalle haben einen hohen Schmelzpunkt und sind widerstandsfähig gegen Verschleiß.
Herstellung von Sputtering Targets
CIP kann Indium-Zinn-Oxid (ITO)-Pulver in große keramische Vorformlinge pressen, die dann unter bestimmten Bedingungen gesintert werden. Mit dieser Methode können theoretisch keramische Targets mit einer Dichte von 95 % hergestellt werden.
Verwendung in Automobilen
CIP wird bei der Herstellung von Automobilkomponenten wie Lagern und Ölpumpenzahnrädern eingesetzt.
Schnelleres Sintern
Kaltisostatisch gepresste Produkte haben eine hohe Grünfestigkeit, die es ermöglicht, sie schneller zu sintern als andere Materialien.
Zusammenfassend lässt sich sagen, dass das CIP-Verfahren aufgrund seiner zahlreichen Vorteile gegenüber ähnlichen Herstellungsverfahren immer beliebter wird. Seine Vielseitigkeit, die Fähigkeit zur Herstellung komplexer Formen und die verbesserten mechanischen Eigenschaften machen es zu einer ausgezeichneten Wahl für Fertigungsunternehmen, die nach hochwertigen, komplexen Teilen für ihre Produkte suchen.
Nachteile von CIP
Kalt-Isostatisches Pressen (CIP) ist eine wirksame Methode, um pulverförmige Materialien vor der Bearbeitung oder dem Sintern zu einer festen, homogenen Masse zu verdichten. Es gibt jedoch einige Nachteile von CIP, die berücksichtigt werden müssen, bevor dieses Verfahren für eine bestimmte Anwendung ausgewählt wird.
Nicht geeignet für Hochtemperaturwerkstoffe
Einer der größten Nachteile von CIP ist, dass es sich nicht für Materialien eignet, die hohe Temperaturen benötigen, um optimale Eigenschaften zu erreichen. Dies liegt daran, dass bei CIP Druck auf das Material bei Raumtemperatur ausgeübt wird, wodurch das Material nur begrenzt komprimiert werden kann. Daher ist CIP kein geeignetes Verfahren für Materialien, die bei hohen Temperaturen verarbeitet werden müssen, wie z. B. Metalle, Legierungen oder Keramiken.
Einführung von unerwünschter Porosität
CIP kann zu einer unerwünschten Porosität im Material führen, die sich negativ auf die mechanischen Eigenschaften auswirken kann. Dies liegt daran, dass der während des CIP-Prozesses ausgeübte Druck zur Bildung von Hohlräumen oder Lücken im Material führen kann, was dessen Festigkeit und Haltbarkeit beeinträchtigen kann. Das Ausmaß der in das Material eingebrachten Porosität hängt von mehreren Faktoren ab, u. a. von der Qualität des Pulvers, der Konstruktion des Werkzeugs und dem während des CIP-Prozesses aufgebrachten Druck.
Beschränkungen bei der Komplexität von Formen
Das CIP-Verfahren ist nicht für alle Formen von Bauteilen geeignet. Es ist auf die Herstellung von Bauteilen mit einfachen Formen, wie z. B. dünne Fliesen, beschränkt. Dies liegt daran, dass der während des CIP-Prozesses ausgeübte Druck aufgrund von Druckgradienten zu einer ungleichmäßigen Partikelpackung führen kann, was bei komplex geformten Bauteilen zu Verformungen und Rissen führen kann.
Begrenzter Druckbereich
Ein weiterer Nachteil des CIP-Verfahrens ist der begrenzte Druckbereich. CIP ist in der Regel auf einen Druckbereich von etwa 200 MPa bis 400 MPa beschränkt. Dies liegt daran, dass höhere Drücke eine speziellere Ausrüstung erfordern und zu einer Verformung oder einem Versagen der im CIP-Prozess verwendeten Werkzeuge führen können.
Zusammenfassend lässt sich sagen, dass das CIP-Verfahren zwar für einige Anwendungen eine nützliche Technik ist, jedoch mehrere Nachteile aufweist, die vor der Auswahl dieser Methode für eine bestimmte Anwendung berücksichtigt werden müssen.
Vergleich zwischen HIP und CIP
Heiß-Isostatisches Pressen (HIP) und Kalt-Isostatisches Pressen (CIP) sind zwei gängige Verfahren zur Herstellung hochdichter Materialien. Der Unterschied zwischen den beiden Verfahren liegt in der Temperatur, bei der sie durchgeführt werden. Hier sind einige der wichtigsten Unterschiede zwischen HIP und CIP:
Temperatur und Druck
Das HIP-Verfahren wird bei hoher Temperatur und hohem Druck durchgeführt, das CIP-Verfahren dagegen bei Raumtemperatur. Beim HIP-Verfahren wird das Material zunächst in eine Form gelegt und dann hoher Hitze und hohem Druck ausgesetzt, wodurch es dichter und in seiner Zusammensetzung einheitlicher wird. Die hohe Temperatur ermöglicht auch die Beseitigung von Restporosität oder Defekten im Material. Beim CIP-Verfahren hingegen wird das Material in einen flexiblen Behälter gegeben und von allen Seiten mit hohem Druck beaufschlagt.
Dichte und Gleichmäßigkeit
Beim HIP-Verfahren werden Materialien hergestellt, die im Vergleich zum CIP-Verfahren dichter und gleichmäßiger in ihrer Zusammensetzung sind. Die hohe Temperatur und der hohe Druck beim HIP-Verfahren führen zur Beseitigung von Restporosität oder Defekten im Material, was zu einer gleichmäßigeren Dichte und einer Verringerung von Defekten führt. Beim CIP-Verfahren werden Materialien hergestellt, die im Vergleich zum HIP-Verfahren eine geringere Dichte aufweisen, aber immer noch gleichmäßig dicht sind und eine geringe Fehlerquote haben.
Anwendungen
HIP wird häufig in der Luft- und Raumfahrtindustrie für die Herstellung von Hochleistungslegierungen und -keramiken verwendet, während CIP in der Regel für die Herstellung keramischer Bauteile eingesetzt wird, wie sie in der Elektronikindustrie verwendet werden. Der Grund dafür ist, dass bei der HIP-Herstellung Werkstoffe entstehen, die fester und widerstandsfähiger gegen hohe Temperaturen und Druck sind und sich daher für Anwendungen in der Luftfahrt eignen. Beim CIP-Verfahren hingegen werden Materialien hergestellt, die eine geringere, aber immer noch gleichmäßige Dichte aufweisen und sich daher für elektronische Anwendungen eignen.
Kosten und Zeit
HIP ist im Vergleich zu CIP ein teureres und zeitaufwändigeres Verfahren. Das liegt daran, dass es hohe Temperaturen und Drücke erfordert, deren Aufrechterhaltung kostspielig sein kann. CIP hingegen ist im Vergleich zu HIP ein kostengünstigeres und schnelleres Verfahren, da es bei Raumtemperatur durchgeführt wird und keine hohen Temperaturen und Drücke erfordert.
Zusammenfassend lässt sich sagen, dass sowohl das HIP- als auch das CIP-Verfahren ihre eigenen Vor- und Nachteile haben, und dass die Wahl zwischen den beiden Verfahren von den spezifischen Anforderungen der jeweiligen Anwendung abhängt. Beim HIP-Verfahren werden Werkstoffe hergestellt, die fester und widerstandsfähiger gegen hohe Temperaturen und Druck sind, was sie für Anwendungen in der Luft- und Raumfahrt geeignet macht. Mit CIP werden Materialien hergestellt, die eine geringere, aber immer noch gleichmäßige Dichte aufweisen, was sie für elektronische Anwendungen geeignet macht. Allerdings ist CIP im Vergleich zu HIP ein kostengünstigeres und schnelleres Verfahren.
Fazit
Sowohlheißisostatisches Pressen (HIP) und kaltisostatisches Pressen (CIP) haben ihre eigenen Vor- und Nachteile. HIP ist zwar ein teureres Verfahren, liefert aber qualitativ hochwertigere Produkte mit besseren mechanischen Eigenschaften. Andererseits ist das CIP-Verfahren eine kostengünstigere Lösung, die für die Herstellung komplexer Formen in großem Maßstab eingesetzt werden kann. Letztendlich hängt die Entscheidung zwischen HIP und CIP von den spezifischen Anforderungen der jeweiligen Anwendung ab. HIP wird häufig in der Luft- und Raumfahrt, der Medizintechnik und der Nuklearindustrie eingesetzt, während CIP in der Automobil- und Elektronikindustrie bevorzugt wird.
Kontaktieren Sie uns für eine kostenlose Beratung
Die Produkte und Dienstleistungen von KINTEK LAB SOLUTION werden von Kunden auf der ganzen Welt anerkannt. Unsere Mitarbeiter helfen Ihnen gerne bei allen Fragen weiter. Kontaktieren Sie uns für eine kostenlose Beratung und sprechen Sie mit einem Produktspezialisten, um die am besten geeignete Lösung für Ihre Anwendungsanforderungen zu finden!