Historische Entwicklung der Vakuumbeschichtungstechnologie
Frühe Herausforderungen und CVD-Technologie
Die Vakuumbeschichtungstechnologie machte ihre ersten bedeutenden Schritte in den 1960er Jahren mit der Einführung der chemischen Gasphasenabscheidung (CVD). Diese bahnbrechende Technik war damals zwar revolutionär, aber nicht ohne Herausforderungen. Eine der größten Hürden war das Erfordernis hoher Temperaturen, was die Arten von Substraten, die effektiv beschichtet werden konnten, einschränkte. Die hohen thermischen Anforderungen der CVD-Verfahren bedeuteten, dass nur Materialien mit hoher thermischer Stabilität den Abscheidebedingungen standhalten konnten, was das Feld der möglichen Anwendungen erheblich einschränkte.
Außerdem war die frühe CVD-Technologie durch die begrenzte Vielfalt der herstellbaren Schichten eingeschränkt. Die Komplexität und Spezifizität der chemischen Reaktionen, die bei der CVD zum Einsatz kommen, bedeutete, dass nur eine Handvoll von Materialien zuverlässig abgeschieden werden konnte, was den Nutzen weiter einschränkte. Diese Einschränkungen stellten die Entwicklung und Verbreitung der Vakuumbeschichtungstechnologie vor erhebliche Herausforderungen und machten die Suche nach alternativen Methoden zur Überwindung dieser Hindernisse notwendig.
In den folgenden Jahrzehnten ebneten diese frühen Herausforderungen den Weg für die Entwicklung vielseitigerer und effizienterer Beschichtungstechnologien, wie z. B. der physikalischen Gasphasenabscheidung (PVD), die in den 1970er Jahren aufkam und eine anpassungsfähigere und umweltfreundlichere Lösung bot.
Das Aufkommen der PVD-Technologie
In den 1970er Jahren erfuhr die Landschaft der Vakuumbeschichtungstechnologie mit dem Aufkommen der Physical Vapor Deposition (PVD)-Technologie einen bedeutenden Wandel. Diese neue Methode räumte nicht nur einige der Umweltprobleme aus, die mit ihrem Vorgänger, der chemischen Gasphasenabscheidung (CVD), verbunden waren, sondern ermöglichte auch eine Vielzahl vielseitiger Oberflächeneigenschaften, die zuvor unerreichbar waren. Die Umstellung von CVD auf PVD war gekennzeichnet durch eine Senkung der Betriebstemperaturen und eine Erweiterung des Spektrums an Beschichtungen, die aufgebracht werden konnten, wodurch sich die Anwendungsmöglichkeiten in verschiedenen Branchen erweiterten.
Die Umweltvorteile von PVD waren besonders bemerkenswert. Im Gegensatz zum CVD-Verfahren, das häufig hohe Temperaturen und potenziell gefährliche Chemikalien erfordert, arbeitet das PVD-Verfahren unter kontrollierteren Bedingungen, was zu einem geringeren Energieverbrauch und niedrigeren Emissionen führt. Diese Umweltfreundlichkeit in Verbindung mit der Fähigkeit, Beschichtungen mit hervorragender Härte, Verschleißfestigkeit und Korrosionsschutz zu erzeugen, erregte schnell die Aufmerksamkeit von Forschern und Industrievertretern.
Die rasche Entwicklung der PVD-Technologie in dieser Zeit ist auf ihre Anpassungsfähigkeit und die erheblichen Verbesserungen zurückzuführen, die sie für die Qualität und Haltbarkeit von Beschichtungen mit sich brachte. Branchen von der Automobil- bis zur Luft- und Raumfahrtindustrie begannen, PVD wegen seiner Fähigkeit, die Leistung von Werkzeugen und Bauteilen zu verbessern, zu übernehmen, was zu höherer Effizienz und längerer Produktlebensdauer führte. Diese weit verbreitete Akzeptanz förderte die Weiterentwicklung der PVD-Techniken, trieb die Technologie voran und festigte ihren Platz in der Welt der modernen industriellen Prozesse.
Aktueller Stand und Herausforderungen
Unausgewogene Entwicklung
Trotz der weiten Verbreitung der Vakuumbeschichtungstechnologie für dekorative Zwecke ist die Anwendung dieser Beschichtungen im industriellen Formenbau nach wie vor mit Herausforderungen behaftet. Das Haupthindernis liegt in den strengen Anforderungen an die Haftung von Industrieformen, die eine robuste und dauerhafte Verbindung zwischen der Beschichtung und dem Substrat erfordern. Diese erhöhten Anforderungen können von den derzeitigen Beschichtungstechnologien nicht ohne weiteres erfüllt werden, da diese häufig der Ästhetik den Vorrang vor der funktionalen Beständigkeit geben.
Das Fehlen umfassender Prozesstechnologien, die speziell auf die Beschichtung von Industrieformen zugeschnitten sind, verschärft diese Herausforderungen noch weiter. Im Gegensatz zu dekorativen Beschichtungen, die es sich leisten können, in ihren Anwendungsmethoden weniger streng zu sein, erfordern industrielle Formenbeschichtungen präzise und kontrollierte Prozesse, um optimale Leistung und Langlebigkeit zu gewährleisten. Diese Ungleichheit in der technologischen Entwicklung hat zu einem unausgewogenen Wachstum in der Vakuumbeschichtungsindustrie geführt, da die Fortschritte bei den dekorativen Beschichtungen nicht in angemessener Weise in die industriellen Anwendungen eingeflossen sind.
Um diese Probleme anzugehen, besteht ein dringender Bedarf an der Entwicklung spezieller Technologien und Methoden, die den besonderen Anforderungen der industriellen Formenbeschichtung gerecht werden. Dazu gehört nicht nur die Verbesserung der Haftungseigenschaften der Beschichtungen, sondern auch die Verfeinerung der gesamten Prozesskette, von der Vorbehandlung bis zur Qualitätskontrolle nach dem Auftragen. Durch die Konzentration auf diese Bereiche kann die Branche die Kluft zwischen dekorativen und industriellen Beschichtungen überbrücken und so eine ausgewogenere und umfassendere Entwicklung fördern.
Technische Disparitäten
Im Bereich der Vakuumbeschichtungstechnologie, insbesondere im Zusammenhang mit PVD (Physical Vapor Deposition), bleiben die inländischen technischen Möglichkeiten oft hinter den internationalen Standards zurück. Diese Diskrepanz ist nicht nur eine Frage der Ausgereiftheit der Anlagen, sondern umfasst auch ein breiteres Spektrum an Faktoren, einschließlich Prozessoptimierung, Fortschritte in der Materialwissenschaft und Methoden der Qualitätskontrolle.
Um diese Lücke zu schließen, muss die einheimische Industrie dringend nicht nur fortschrittliche Anlagen einführen, sondern auch Spitzentechnologien übernehmen und integrieren. Dies erfordert einen vielschichtigen Ansatz, der Folgendes umfasst:
- Aufrüstung der Ausrüstung: Investitionen in hochmoderne Vakuumkammern, Stromversorgungen und Gaszufuhrsysteme, die in der Lage sind, komplexe PVD-Prozesse mit Präzision durchzuführen.
- Technologische Absorption: Zusammenarbeit in Forschung und Entwicklung mit internationalen Partnern, um die besten Verfahren in der PVD-Technologie zu verstehen und umzusetzen.
- Prozess-Optimierung: Verfeinerung bestehender Prozesse, um eine einheitliche Beschichtungsqualität zu gewährleisten, wobei Fragen wie Haftung und Schichtkonsistenz behandelt werden.
Aspekt | Nationaler Status | Internationale Normen |
---|---|---|
Ausrüstung | Einfach oder veraltet | Fortschrittlich und hochpräzise |
Prozesskontrolle | Manuell oder halbautomatisch | Vollautomatisch mit AI-Unterstützung |
Materialwissenschaft | Begrenzter Forschungsschwerpunkt | Umfassende Forschung und Innovation |
Qualitätskontrolle | Ad-hoc-Methoden | Systematische und strenge FQC |
Auf dem Weg zur Parität geht es nicht nur um den Erwerb von Technologie, sondern auch um die Entwicklung eines robusten Ökosystems, das kontinuierliche Innovation und Verbesserung unterstützt. Dieser ganzheitliche Ansatz ist unerlässlich, um die heimischen Fähigkeiten zu verbessern und sicherzustellen, dass sie im globalen Wettbewerb bestehen können.
Grundlegende Konzepte und Merkmale der PVD-Beschichtung
Methoden und Techniken
Die physikalische Gasphasenabscheidung (PVD) umfasst mehrere fortschrittliche Verfahren mit jeweils einzigartigen Eigenschaften und Anwendungen. Zwei herausragende Verfahren innerhalb der PVD sind die Multibogenbeschichtung und die Magnetronsputtern.
Bei der Multibogenbeschichtung wird das Zielmaterial mit Hilfe eines elektrischen Lichtbogens verdampft, der das Material ionisiert und auf das Substrat treibt. Diese Methode ist bekannt für ihre hohen Abscheideraten und die Fähigkeit, komplexe Geometrien zu beschichten. Es kann jedoch mit Problemen wie Partikelkontamination und ungleichmäßiger Schichtdicke behaftet sein.
Beim Magnetronsputtern hingegen wird ein Magnetfeld zur Verstärkung der Ionisierung der Zielatome eingesetzt, die dann auf das Substrat beschleunigt werden. Dieses Verfahren bietet eine bessere Kontrolle über die Schichteigenschaften, einschließlich Dichte und Gleichmäßigkeit, und ist daher ideal für Anwendungen, die präzise Beschichtungen erfordern. Trotz dieser Vorteile ist das Magnetron-Sputtern im Vergleich zum Multi-Arc-Plating langsamer und energieaufwändiger.
Verfahren | Vorteile | Nachteile |
---|---|---|
Multi-Arc-Beschichtung | Hohe Abscheideraten, geeignet für komplexe Geometrien | Partikelkontamination, ungleichmäßige Schichtdicke |
Magnetron-Zerstäubung | Ausgezeichnete Kontrolle über die Schichteigenschaften, hohe Dichte und Gleichmäßigkeit | Langsamerer Prozess, höherer Energieverbrauch |
Das Verständnis dieser Methoden und ihrer jeweiligen Vor- und Nachteile ist entscheidend für die Auswahl der am besten geeigneten PVD-Technik für bestimmte industrielle Anwendungen.
Kombination von Technologien
Die Integration von Multi-Arc- und Magnetron-Technologien stellt einen bedeutenden Fortschritt auf dem Gebiet der Vakuumbeschichtung dar. Diese Kombination ist nicht einfach die Summe ihrer Teile, sondern ein synergetischer Ansatz, der die Vorteile beider Technologien maximiert und die Herstellung stabiler und hochwertiger Beschichtungen gewährleistet.
Die Multilichtbogenbeschichtung, die für ihre hohen Abscheideraten und ihre Fähigkeit zur Herstellung dichter Schichten bekannt ist, ergänzt das Magnetronsputtern, das sich durch die Herstellung gleichmäßiger und konformer Schichten bei minimaler Erwärmung des Substrats auszeichnet. Durch die Kombination dieser Verfahren können die Hersteller ein Gleichgewicht zwischen Abscheidegeschwindigkeit und Gleichmäßigkeit der Beschichtung erreichen, was für Anwendungen, die sowohl Effizienz als auch Präzision erfordern, von entscheidender Bedeutung ist.
Darüber hinaus ermöglicht die Hybridisierung dieser Technologien die Optimierung der Schichteigenschaften. So können beispielsweise durch die Einbindung von Multibogen-Ionen in den Magnetron-Sputterprozess die Haftung und die Härte der Beschichtungen verbessert werden, was bei der Beschichtung von Industrieformen, bei der eine höhere Haftung und Haltbarkeit von größter Bedeutung sind, häufig vorkommt.
Diese Integration eröffnet auch neue Möglichkeiten für die Materialauswahl und Prozesskontrolle. Durch die Nutzung der Stärken beider Technologien ist es möglich, eine breitere Palette von Materialien mit maßgeschneiderten Eigenschaften abzuscheiden, von harten, verschleißfesten Beschichtungen bis hin zu komplexeren Mehrschichtstrukturen. Das Ergebnis ist eine vielseitigere und robustere Beschichtungslösung, die den unterschiedlichen Anforderungen der verschiedenen industriellen Anwendungen gerecht wird.
Zusammenfassend lässt sich sagen, dass die Kombination von Multi-Arc- und Magnetron-Technologien nicht nur die Qualität und Stabilität von Beschichtungen verbessert, sondern auch die Bandbreite der erreichbaren Materialeigenschaften und Prozesseffizienz erweitert. Dieser Fortschritt ist ausschlaggebend dafür, dass die Grenzen der Vakuumbeschichtungstechnologie immer weiter hinausgeschoben werden, was sie zu einem Eckpfeiler in der Entwicklung der industriellen Beschichtung macht.
Moderne Beschichtungsanlagen und -verfahren
Komponenten und Systeme
Moderne Beschichtungsanlagen sind ein ausgeklügeltes System aus wichtigen Komponenten, die alle eine entscheidende Rolle im Vakuumbeschichtungsprozess spielen. Das Herzstück dieses Systems ist dieVakuumkammereine versiegelte Umgebung, die das Substrat von den atmosphärischen Bedingungen isoliert und eine makellose Oberfläche für die Beschichtung gewährleistet. Die Vakuumkammer wird in der Regel aus Materialien wie Edelstahl hergestellt, die für ihre Langlebigkeit und Korrosionsbeständigkeit bekannt sind.
Um das erforderliche Vakuum zu erreichen,vakuumerhaltende Teile eingesetzt. Dazu gehören Vakuumpumpen wie Drehschieberpumpen und Turbomolekularpumpen, die im Tandem arbeiten, um den Druck in der Kammer auf die für PVD-Verfahren erforderlichen extrem niedrigen Werte zu senken. Die Effizienz dieser Pumpen ist entscheidend, da sie sich direkt auf die Qualität und Gleichmäßigkeit der Beschichtung auswirkt.
Eine weitere kritische Komponente sind die Stromversorgungen, die die für die Verdampfung des Beschichtungsmaterials erforderliche elektrische Energie liefern. Moderne Systeme verwenden häufigMittelfrequenz-Netzteile oderImpulstechnikdie eine präzise Steuerung des Beschichtungsprozesses ermöglichen, was zu einer höheren Qualität der Beschichtung führt. Diese fortschrittlichen Stromversorgungen tragen dazu bei, Probleme wie Lichtbogenbildung und ungleichmäßige Abscheidung, die bei herkömmlichen PVD-Anlagen häufig auftreten, zu vermeiden.
Schließlich sind dieProzessgaszufuhrsysteme ein wesentlicher Bestandteil des Betriebs. Diese Systeme leiten reaktive Gase in die Vakuumkammer ein und ermöglichen die Bildung komplexer Schichten mit maßgeschneiderten Eigenschaften. Die präzise Steuerung von Gasdurchsatz und -zusammensetzung ermöglicht die Herstellung von Beschichtungen mit spezifischen mechanischen, chemischen und optischen Eigenschaften, was die Vielseitigkeit und Anwendbarkeit der Technologie erhöht.
Zusammenfassend lässt sich sagen, dass moderne Beschichtungsanlagen ein komplexes Zusammenspiel von Vakuumkammern, vakuumerzeugenden Teilen, Stromversorgungen und Prozessgaszufuhrsystemen sind, die alle zur Präzision und Qualität des PVD-Prozesses beitragen.
Fortgeschrittene Techniken
Im Bereich der Vakuumbeschichtungstechnologie haben sich mehrere fortschrittliche Techniken herausgebildet, die die Qualität und Anwendbarkeit der Beschichtungen erheblich verbessern. Eine dieser Techniken ist die Verwendung vonNicht-Gleichgewichts-Magnetfeldern. Diese Felder ermöglichen eine präzisere Steuerung des Abscheidungsprozesses und damit die Herstellung von Beschichtungen mit hervorragender Gleichmäßigkeit und Haftung. Dies ist besonders bei industriellen Anwendungen von Vorteil, bei denen die Haltbarkeit und Leistung der Beschichtung entscheidend sind.
Ein weiterer entscheidender Fortschritt ist die Einführung vonMittelfrequenz-Stromversorgungen. Im Gegensatz zu herkömmlichen Stromversorgungen bieten diese Mittelfrequenzsysteme eine höhere Stabilität und Effizienz. Sie ermöglichen die Abscheidung dickerer und robusterer Schichten, ohne die Integrität des darunter liegenden Materials zu beeinträchtigen. Diese Innovation ist besonders nützlich für Branchen, die Hochleistungsbeschichtungen für Formen und Werkzeuge benötigen.
Zusätzlich,Impulstechnologie hat den Beschichtungsprozess revolutioniert. Durch die Abgabe von Energie in kurzen, kontrollierten Stößen minimiert die Pulstechnologie die thermische Belastung des Substrats und verhindert so Verformungen und Beschädigungen. Diese Methode ist besonders vorteilhaft für empfindliche Materialien oder solche, die eine komplizierte Oberflächenbehandlung erfordern. Die präzise Energiezufuhr sorgt auch dafür, dass die Beschichtung besser haftet, was zu länger anhaltenden und zuverlässigeren Ergebnissen führt.
Diese fortschrittlichen Techniken tragen insgesamt zur Weiterentwicklung der Vakuumbeschichtungstechnologie bei und machen sie für verschiedene industrielle Anwendungen vielseitiger und effektiver. Die Integration von Nicht-Gleichgewichtsmagnetfeldern, Mittelfrequenz-Stromversorgungen und Impulstechnologie verbessert nicht nur die Qualität der Beschichtungen, sondern erweitert auch ihre Anwendungsmöglichkeiten und erfüllt die immer strengeren Anforderungen der modernen Industrie.
Anwendung und Qualitätskontrolle bei PVD für Gussformen
Vorbehandlungs- und Beschichtungsprozesse
Vorbehandlungsmethoden sind entscheidende Schritte bei der Vorbereitung von Oberflächen für die PVD-Beschichtung (Physical Vapor Deposition). Zu diesen Verfahren gehört die Hochtemperatur-Dampfreinigung, die Verunreinigungen wirksam entfernt und ein sauberes Substrat gewährleistet. Eine weitere wichtige Technik ist das Sandstrahlen, das eine raue Oberfläche schafft, die die Haftung der Beschichtung verbessert. Der PVD-Beschichtungsprozess selbst hängt stark von einer präzisen Temperaturkontrolle und gleichmäßiger Erwärmung ab, um optimale Ergebnisse zu erzielen.
Eine gleichmäßige Erwärmung ist von entscheidender Bedeutung, da sie gewährleistet, dass das Substrat gleichmäßig erwärmt wird, was wiederum eine gleichmäßige Abscheidung des Beschichtungsmaterials ermöglicht. Die Temperaturregelung ist ebenso wichtig, da Abweichungen zu Unregelmäßigkeiten in der Schichtdicke und -qualität führen können. Moderne Techniken wie Mittelfrequenz-Stromversorgungen und Impulstechnik werden häufig eingesetzt, um stabile und gleichmäßige Heizbedingungen aufrechtzuerhalten und so die Gesamtqualität der PVD-Beschichtung zu verbessern.
Diese Vorbehandlungs- und Beschichtungsprozesse sind ein wesentlicher Faktor für den Erfolg von PVD-Anwendungen in industriellen Formen. Sie verbessern nicht nur die Haltbarkeit und Leistung der Formen, sondern verlängern auch deren Lebensdauer, was sie in hochpräzisen Fertigungsumgebungen unverzichtbar macht.
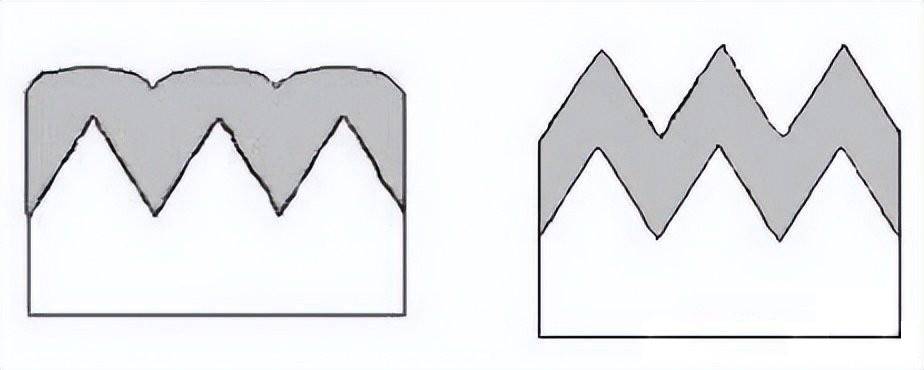
Maßnahmen zur Qualitätskontrolle
Die Funktionsqualitätskontrolle (FQC) ist ein entscheidender Aspekt bei der Gewährleistung der Zuverlässigkeit und Leistung beschichteter Formen. Dieser Prozess umfasst mehrere sorgfältige Kontrollen, um zu gewährleisten, dass die Beschichtungen den erforderlichen Standards entsprechen.
Eine der wichtigsten Methoden der FQC ist diePrüfung des Aussehens. Dabei handelt es sich um eine gründliche Sichtprüfung, bei der Oberflächenmängel wie Kratzer, Vertiefungen oder Verfärbungen festgestellt werden. Diese Mängel können die Funktionalität und Lebensdauer der Form erheblich beeinträchtigen, weshalb dieser Schritt unerlässlich ist.
Eine weitere wichtige Methode ist dieSchichttiefenprüfung. Mit dieser Technik wird die Dicke der Beschichtungsschichten gemessen, um sicherzustellen, dass sie die vorgegebenen Parameter einhalten. Verschiedene Instrumente, wie Profilometer und Rasterelektronenmikroskope, werden eingesetzt, um die Tiefe und Gleichmäßigkeit der Beschichtung genau zu bestimmen.
DieHaftfestigkeitsprüfung ist ebenfalls entscheidend. Bei diesem Verfahren wird die Haftfestigkeit zwischen der Beschichtung und dem Formsubstrat bewertet. Zu den gängigen Methoden gehören Kratz-, Zug- und Gitterschnitttests. Diese Tests helfen dabei, potenzielle Delaminierungs- oder Abblätterungsprobleme zu erkennen und die Haltbarkeit und Wirksamkeit der Beschichtung zu gewährleisten.
Durch die Integration dieser FQC-Methoden können Hersteller sicherstellen, dass ihre beschichteten Formen nicht nur den Industriestandards entsprechen, sondern diese sogar übertreffen, und so zuverlässige und leistungsstarke Werkzeuge für verschiedene industrielle Anwendungen bereitstellen.
Kontaktieren Sie uns für eine kostenlose Beratung
Die Produkte und Dienstleistungen von KINTEK LAB SOLUTION werden von Kunden auf der ganzen Welt anerkannt. Unsere Mitarbeiter helfen Ihnen gerne bei allen Fragen weiter. Kontaktieren Sie uns für eine kostenlose Beratung und sprechen Sie mit einem Produktspezialisten, um die am besten geeignete Lösung für Ihre Anwendungsanforderungen zu finden!