Abscheideverfahren können je nach Methode sehr unterschiedlich sein, aber Wärme spielt oft eine entscheidende Rolle bei der Beeinflussung von Qualität, Geschwindigkeit und Eigenschaften der abgeschiedenen Schicht.Zwar ist nicht für alle Abscheidungsverfahren unbedingt Wärme erforderlich, doch profitieren viele von kontrollierten Temperaturen, um Filmeigenschaften wie Dichte, Zusammensetzung und Haftung zu optimieren.Wärme kann die Oberflächenreaktionen verstärken, die Filmqualität verbessern und die Abscheidungsrate bei Verfahren wie der thermischen Verdampfung erhöhen.Die Notwendigkeit von Wärme hängt jedoch von der jeweiligen Abscheidungstechnik und den gewünschten Schichteigenschaften ab.So führen höhere Temperaturen im Allgemeinen zu dichteren Schichten, können aber auch Einschränkungen aufgrund des Substrats oder der Anwendungsanforderungen mit sich bringen.
Die wichtigsten Punkte erklärt:
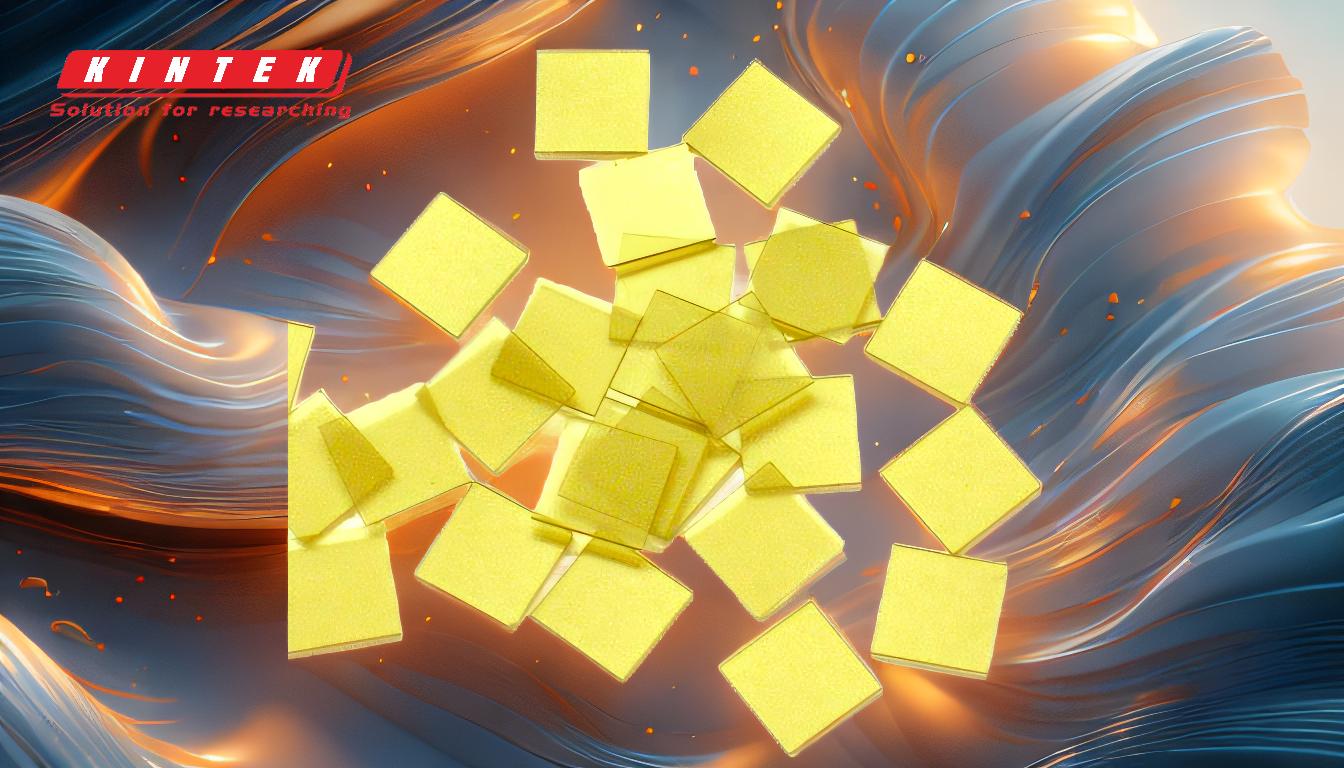
-
Die Rolle der Wärme bei Abscheidungsvorgängen:
- Wärme wird häufig eingesetzt, um die Qualität und die Eigenschaften der abgeschiedenen Schichten zu verbessern.So können beispielsweise höhere Substrattemperaturen die Oberflächenreaktionen verbessern, was zu dichteren und gleichmäßigeren Schichten führt.
- Bei der thermischen Verdampfung wird durch eine höhere Temperatur der Dampfdruck des Materials erhöht, was zu höheren Abscheideraten führt, da mehr Material verdampft und auf dem Substrat abgeschieden wird.
-
Einfluss der Temperatur auf die Filmeigenschaften:
- Höhere Temperaturen verbessern im Allgemeinen die Qualität der Filme, da sie eine bessere Haftung, dichtere Strukturen und eine bessere Zusammensetzung fördern.Dies liegt daran, dass Wärme die Mobilität der Atome und die Oberflächendiffusion erleichtert, was zu stabileren und gleichmäßigeren Filmen führt.
- Übermäßige Hitze kann jedoch die Schichteigenschaften verändern oder temperaturempfindliche Substrate beschädigen, so dass die Temperaturkontrolle von entscheidender Bedeutung ist, um ein Gleichgewicht zwischen Qualität und Anwendungsbeschränkungen herzustellen.
-
Abscheiderate und Temperatur:
- Bei vielen Abscheidungsverfahren, wie z. B. der thermischen Verdampfung, korrelieren höhere Temperaturen mit höheren Abscheidungsraten aufgrund des erhöhten Dampfdrucks und der Materialverdampfung.
- Bei anderen Verfahren wie der chemischen Gasphasenabscheidung (CVD) beeinflusst die Temperatur die Geschwindigkeit der chemischen Reaktionen, was sich wiederum auf die Abscheidungsrate und die Schichteigenschaften auswirkt.
-
Wärme als Variable bei verschiedenen Abscheidetechniken:
- Thermische Verdampfung:Wärme ist für die Verdampfung des Materials unerlässlich und daher ein Schlüsselfaktor bei diesem Verfahren.
- Sputtern:Während das Sputtern bei niedrigeren Temperaturen durchgeführt werden kann, kann die Erwärmung des Substrats die Schichtqualität und die Haftung verbessern.
- Chemische Gasphasenabscheidung (CVD):Oft ist Wärme erforderlich, um die für die Filmbildung notwendigen chemischen Reaktionen in Gang zu setzen.
- Physikalische Gasphasenabscheidung (PVD):Einige PVD-Verfahren, wie die Elektronenstrahlverdampfung, benötigen Wärme, um die Materialien zu verdampfen, während andere, wie das Magnetron-Sputtern, keine nennenswerte Erwärmung erfordern.
-
Substrattemperatur und Schichtqualität:
- Die Substrattemperatur hat einen erheblichen Einfluss auf die Schichtqualität, auch wenn sie sich nicht immer auf die Abscheiderate auswirkt.Höhere Temperaturen können zu dichteren Schichten mit weniger Defekten führen, da sie eine bessere atomare Anordnung und Oberflächenreaktionen fördern.
- Bei temperaturempfindlichen Substraten können niedrigere Temperaturen oder alternative Abscheidungsmethoden erforderlich sein, um Schäden zu vermeiden.
-
Ausgleich zwischen Wärme und Anwendungsanforderungen:
- Die Anwendung gibt oft die Temperaturgrenzen für die Abscheidung vor.Bei der Halbleiterherstellung beispielsweise kann übermäßige Hitze empfindliche Komponenten beschädigen, so dass die Abscheidungsprozesse sorgfältig kontrolliert werden müssen.
- Im Gegensatz dazu können bei Anwendungen, die Hochleistungsbeschichtungen erfordern, wie z. B. bei Komponenten für die Luft- und Raumfahrt, höhere Temperaturen von Vorteil sein, um bessere Schichteigenschaften zu erzielen.
-
Alternative Ansätze für die Niedertemperaturabscheidung:
- Einige Abscheidetechniken, wie die plasmaunterstützte chemische Gasphasenabscheidung (PECVD), ermöglichen die Filmbildung bei niedrigeren Temperaturen, indem sie ein Plasma zum Antrieb chemischer Reaktionen verwenden, anstatt sich nur auf Wärme zu verlassen.
- Diese Verfahren sind besonders nützlich für die Abscheidung von Schichten auf temperaturempfindlichen Substraten, wie z. B. Polymeren oder biologischen Materialien.
Zusammenfassend lässt sich sagen, dass Wärme zwar nicht immer zwingend für die Abscheidung erforderlich ist, dass sie aber bei vielen Verfahren ein entscheidender Faktor ist, um die gewünschten Schichteigenschaften zu erzielen.Die Notwendigkeit von Wärme hängt von der jeweiligen Abscheidungstechnik, dem abzuscheidenden Material und den Temperatureinschränkungen der Anwendung ab.Durch eine sorgfältige Temperaturkontrolle können die Hersteller die Abscheideraten, die Schichtqualität und die Gesamtleistung optimieren.
Zusammenfassende Tabelle:
Aspekt | Einzelheiten |
---|---|
Die Rolle der Wärme | Fördert Oberflächenreaktionen, verbessert die Filmqualität und erhöht die Abscheideraten. |
Auswirkungen auf die Filmeigenschaften | Höhere Temperaturen führen zu dichteren Schichten, besserer Adhäsion und weniger Defekten. |
Abscheidungsrate | Höhere Temperaturen führen oft zu höheren Abscheideraten. |
Techniken, die Wärme erfordern | Thermische Verdampfung, chemische Gasphasenabscheidung (CVD), einige PVD-Verfahren. |
Niedertemperatur-Alternativen | Plasmaunterstütztes CVD (PECVD) für temperaturempfindliche Substrate. |
Überlegungen zur Anwendung | Die Temperaturgrenzen hängen vom Substrat und den Anwendungsanforderungen ab. |
Sind Sie bereit, Ihren Beschichtungsprozess zu optimieren? Kontaktieren Sie noch heute unsere Experten für maßgeschneiderte Lösungen!