Gesinterte Metallteile werden in einer Reihe genau festgelegter Schritte hergestellt, die pulverförmige Metalle in feste, dauerhafte Komponenten verwandeln.Der Prozess umfasst in der Regel die Aufbereitung des Pulvers, die Verdichtung und das Sintern, gefolgt von optionalen Nachbehandlungsschritten zur Verbesserung der Eigenschaften des Endprodukts.Durch die sorgfältige Auswahl von Metallpulvern, die Anwendung präziser Verdichtungstechniken und die Steuerung der Sinterumgebung können die Hersteller Teile mit spezifischen mechanischen, thermischen und chemischen Eigenschaften herstellen.Dieses Verfahren ist in Branchen wie der Automobil-, Luft- und Raumfahrt- sowie der Elektronikindustrie weit verbreitet, da sich damit komplexe Formen mit hoher Präzision und Materialeffizienz herstellen lassen.
Die wichtigsten Punkte erklärt:
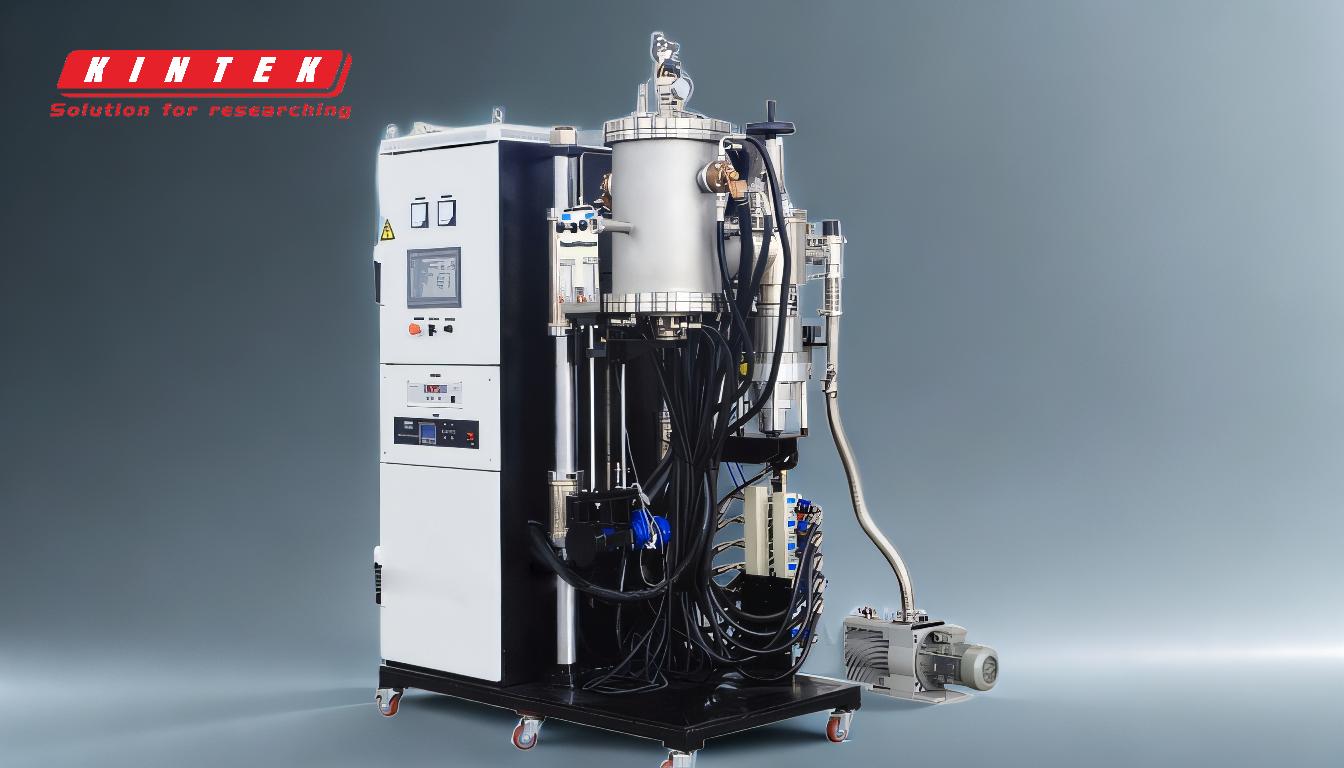
-
Vorbereitung des Pulvers
- Zweck:Der erste Schritt besteht in der Herstellung oder Auswahl der geeigneten Metallpulverzusammensetzung, die die endgültigen Eigenschaften des Sinterteils bestimmt.
- Verfahren:Metallpulver wie Eisen, Nickel, Molybdän oder Kupfer werden oft mit Legierungselementen, Schmiermitteln oder Zusatzstoffen gemischt, um die gewünschten Eigenschaften wie Festigkeit, Härte oder Korrosionsbeständigkeit zu erreichen.
- Überlegungen:Die Partikelgröße, -form und -verteilung des Pulvers sind entscheidend, da sie das Verdichtungs- und Sinterverhalten beeinflussen.
-
Mischen und Vermengen
- Zweck:Gewährleistet die Gleichmäßigkeit der Pulvermischung, die für gleichbleibende Eigenschaften der Teile unerlässlich ist.
- Verfahren:Pulver werden mit Zusatzstoffen wie Schmiermitteln (z. B. Wachs oder Stearinsäure) gemischt, um die Fließfähigkeit zu verbessern und die Reibung beim Verdichten zu verringern.
- Überlegungen:Eine ordnungsgemäße Mischung verhindert die Entmischung der Partikel und gewährleistet eine gleichmäßige Verteilung der Legierungselemente.
-
Verdichtung
- Zweck:Umwandlung von losem Pulver in ein "grünes" Teil mit einer bestimmten Form und Anfangsfestigkeit.
- Verfahren:Das Pulver wird unter hohem Druck (in der Regel 20-50 Tonnen pro Quadratzoll) in eine Matrize oder Form gepresst, um eine zusammenhängende Form zu erhalten.
- Erwägungen:Die Verdichtungskraft muss sorgfältig kontrolliert werden, um Mängel wie Risse oder ungleichmäßige Dichte zu vermeiden.Zur Erleichterung des Ausstoßens aus der Matrize werden häufig Schmiermittel verwendet.
-
Sintern
- Zweck:Verbindet die Partikel miteinander, um ein festes, haltbares Teil mit optimalen mechanischen Eigenschaften zu schaffen.
- Verfahren:Das Grünteil wird in einer kontrollierten Atmosphäre (z. B. Wasserstoff, Stickstoff oder Vakuum) auf eine Temperatur knapp unter dem Schmelzpunkt des Metalls erhitzt.Dies bewirkt, dass sich die Partikel durch Diffusion verbinden, wodurch die Porosität verringert und die Festigkeit erhöht wird.
- Überlegungen:Die Sintertemperatur, -zeit und -atmosphäre müssen genau kontrolliert werden, um die gewünschte Dichte, Härte und Mikrostruktur zu erreichen.
-
Nachbehandlung
- Zweck:Verbessert die Eigenschaften des Sinterteils, um spezifische Anwendungsanforderungen zu erfüllen.
-
Verfahren:Zu den üblichen Nachbehandlungsschritten gehören:
- Bearbeitungen:Präzisionsbearbeitung mit Diamantwerkzeugen oder Ultraschall, um enge Toleranzen zu erreichen.
- Wärmebehandlung:Verfahren wie Abschrecken und Anlassen zur Verbesserung von Härte und Festigkeit.
- Oberflächenbehandlung:Beschichtungen oder Plattierungen zur Verbesserung der Verschleißfestigkeit oder Korrosionsbeständigkeit.
- Zusammenbau:Verbindung von Sinterteilen mit anderen Komponenten durch Löten oder Metallisieren.
- Überlegungen:Die Nachbehandlungsschritte sind auf den Verwendungszweck des Teils zugeschnitten und gewährleisten, dass es den Leistungsstandards entspricht.
-
Vorteile von gesinterten Metallteilen
- Effizienz des Materials:Minimaler Abfall im Vergleich zur herkömmlichen Bearbeitung.
- Komplexe Formen:Möglichkeit zur Herstellung komplizierter Geometrien, die mit anderen Verfahren nur schwer oder gar nicht zu erreichen sind.
- Kosten-Nutzen-Verhältnis:Geringere Produktionskosten bei Großserienfertigung.
- Anpassungsfähigkeit:Maßgeschneiderte Materialeigenschaften durch präzise Steuerung der Pulverzusammensetzung und der Verarbeitungsparameter.
Durch die Einhaltung dieser Schritte können Hersteller Sintermetallteile mit außergewöhnlicher Präzision, Haltbarkeit und Leistung herstellen, die sich ideal für eine Vielzahl von industriellen Anwendungen eignen.
Zusammenfassende Tabelle:
Schritt | Zweck | Wichtige Überlegungen |
---|---|---|
Vorbereitung des Pulvers | Auswahl der Metallpulverzusammensetzung für die gewünschten Eigenschaften | Partikelgröße, -form und -verteilung beeinflussen Verdichtung und Sinterung. |
Mischen und Vermengen | Sicherstellung der Gleichmäßigkeit der Pulvermischung für gleichbleibende Teileigenschaften | Richtiges Mischen verhindert Entmischung und gewährleistet eine gleichmäßige Verteilung der Zusatzstoffe. |
Verdichtung | Umwandlung von losem Pulver in eine kohärente Form mit Anfangsfestigkeit | Kontrolle der Verdichtungskraft, um Defekte wie Risse oder ungleichmäßige Dichte zu vermeiden. |
Sintern | Verbinden von Partikeln zu einem festen, dauerhaften Teil mit optimalen Eigenschaften | Die genaue Kontrolle von Temperatur, Zeit und Atmosphäre ist entscheidend. |
Nachbehandlung | Verbessern der Eigenschaften zur Erfüllung spezifischer Anwendungsanforderungen | Beinhaltet Bearbeitung, Wärmebehandlung, Oberflächenbehandlung und Montage. |
Benötigen Sie kundenspezifische Sintermetallteile für Ihre Branche? Kontaktieren Sie uns noch heute für kompetente Lösungen!