Die Wahl der richtigen Kalzinierungstemperatur ist ein entscheidender Schritt, um die gewünschten Materialeigenschaften und Leistungen zu gewährleisten. Die Kalzinierungstemperatur hat einen direkten Einfluss auf die chemischen und physikalischen Umwandlungen des Materials, wie Zersetzung, Phasenübergänge und Kristallisation. Um die geeignete Kalzinierungstemperatur zu bestimmen, muss man die thermische Stabilität des Materials, die gewünschte Phase oder Struktur und die Möglichkeiten der Anlage berücksichtigen. Im Folgenden werden die wichtigsten Faktoren, die bei der Auswahl der Kalzinierungstemperatur zu berücksichtigen sind, ausführlich erläutert.
Die wichtigsten Punkte werden erklärt:
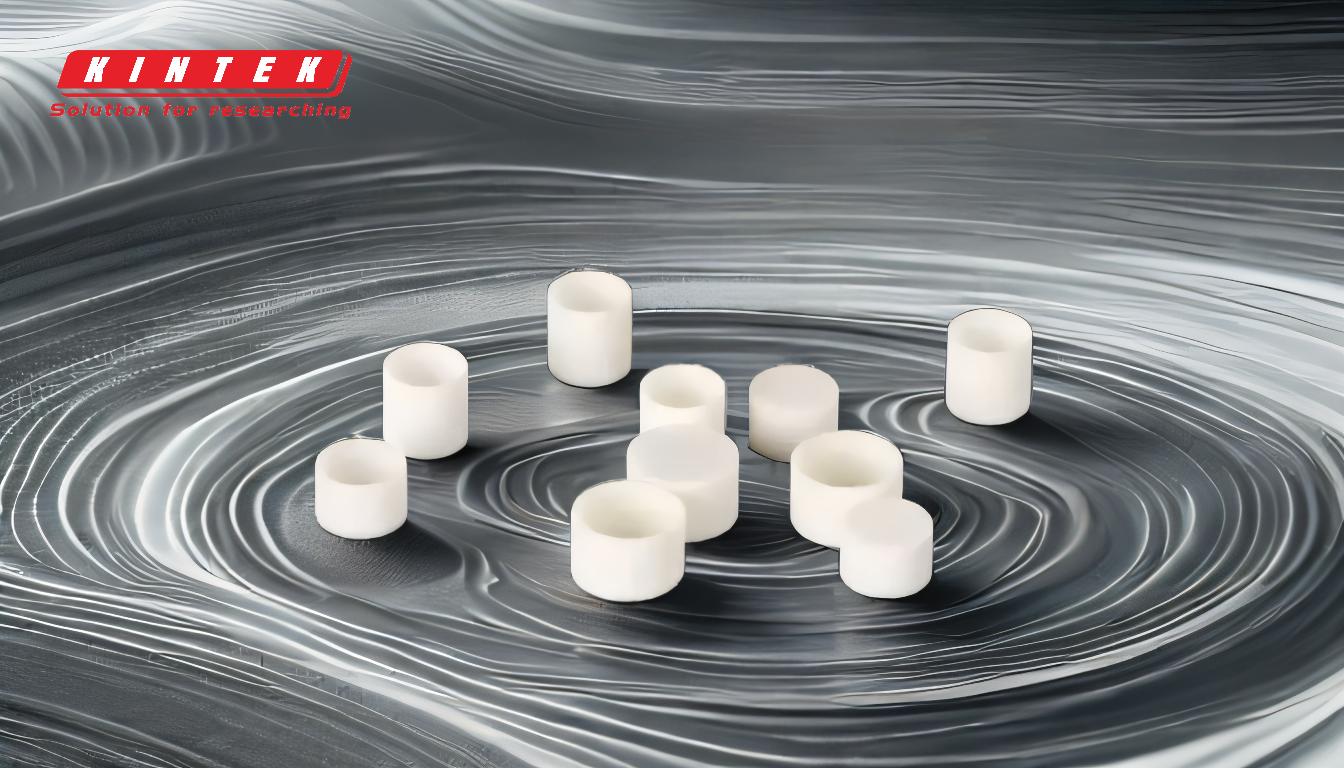
-
Verstehen Sie das thermische Verhalten des Materials
- Thermische Zersetzungstemperatur: Bestimmen Sie die Temperatur, bei der sich das Material zersetzt oder in der es zu Phasenveränderungen kommt. Dies kann durch Techniken wie die thermogravimetrische Analyse (TGA) oder die Differentialscanningkalorimetrie (DSC) ermittelt werden.
- Temperatur des Phasenübergangs: Bestimmen Sie den Temperaturbereich, in dem das Material in die gewünschte kristalline oder amorphe Phase übergeht.
- Thermische Stabilität: Stellen Sie sicher, dass das Material bei der gewählten Kalzinierungstemperatur nicht abgebaut wird oder seine vorgesehenen Eigenschaften verliert.
-
Definieren Sie das erwünschte Ergebnis
- Reinheit der Phase: Wenn eine bestimmte kristalline Phase erreicht werden soll, muss die Kalzinierungstemperatur mit der Phasenbildungstemperatur übereinstimmen.
- Partikelgröße und Morphologie: Höhere Temperaturen können zu Kornwachstum oder Sinterung führen, während niedrigere Temperaturen zu unvollständigen Reaktionen führen können.
- Chemische Zusammensetzung: Stellen Sie sicher, dass die Kalzinierungstemperatur keine unerwünschten Reaktionen oder den Verlust von flüchtigen Bestandteilen verursacht.
-
Beschränkungen der Ausrüstung berücksichtigen
- Temperaturbereich des Ofens: Die Höchsttemperatur des Ofens sollte die erforderliche Kalzinierungstemperatur um 100-200°C übersteigen, um eine gleichmäßige Leistung zu gewährleisten und den Betrieb am oberen Limit des Ofens zu vermeiden.
- Heizrate und Gleichmäßigkeit: Der Ofen sollte eine gleichmäßige Erwärmung und eine präzise Temperaturregelung gewährleisten, um thermische Gradienten zu vermeiden, die die Eigenschaften des Materials beeinträchtigen könnten.
- Atmosphärische Kontrolle: Wenn für die Kalzinierung eine bestimmte Atmosphäre erforderlich ist (z. B. inert, oxidierend oder reduzierend), muss sichergestellt werden, dass der Ofen die erforderlichen Bedingungen einhalten kann.
-
Optimieren durch experimentelle Versuche
- Pilot-Experimente: Durchführung von Experimenten im kleinen Maßstab, um verschiedene Kalzinierungstemperaturen und -dauern zu testen. Analysieren Sie die resultierenden Materialeigenschaften, um die optimale Temperatur zu ermitteln.
- Iterative Verfeinerung: Passen Sie die Temperatur auf der Grundlage der Versuchsergebnisse an und berücksichtigen Sie dabei Faktoren wie Ausbeute, Phasenreinheit und Partikelgröße.
- Charakterisierung: Verwenden Sie Techniken wie Röntgenbeugung (XRD), Rasterelektronenmikroskopie (SEM) und Fourier-Transform-Infrarot-Spektroskopie (FTIR), um das Material nach der Kalzinierung zu bewerten.
-
Berücksichtigung praktischer Zwänge
- Energie-Effizienz: Höhere Temperaturen können den Energieverbrauch und die Betriebskosten erhöhen. Bringen Sie die gewünschten Materialeigenschaften mit der Energieeffizienz in Einklang.
- Sicherheitserwägungen: Stellen Sie sicher, dass die gewählte Temperatur innerhalb des sicheren Betriebsbereichs des Geräts liegt und keine Risiken wie Überhitzung oder Materialverschlechterung birgt.
- Skalierbarkeit: Überlegen Sie, ob die gewählte Temperatur in einer größeren Produktion konstant erreicht werden kann.
-
Referenz-Industrienormen und Literatur
- Veröffentlichte Forschung: Überprüfen Sie Studien zu ähnlichen Materialien, um die häufig verwendeten Kalzinierungstemperaturen und ihre Ergebnisse zu ermitteln.
- Hersteller-Empfehlungen: Informieren Sie sich bei den Geräteherstellern über die optimalen Betriebstemperaturen für bestimmte Materialien.
- Historische Daten: Verwenden Sie ggf. Daten aus früheren Versuchen oder Produktionsläufen, um die Entscheidung zu unterstützen.
Durch sorgfältige Berücksichtigung dieser Faktoren können Sie eine Kalzinierungstemperatur wählen, die die gewünschten Materialeigenschaften erzielt und gleichzeitig einen effizienten und sicheren Betrieb gewährleistet. Der Prozess umfasst eine Kombination aus theoretischem Verständnis, experimenteller Validierung und praktischen Überlegungen zur Optimierung der Kalzinierungsbedingungen.
Zusammenfassende Tabelle:
Schlüsselfaktor | Beschreibung |
---|---|
Thermisches Verhalten von Materialien | Ermittlung der Zersetzungs-, Phasenübergangs- und Wärmestabilitätstemperaturen. |
Gewünschtes Ergebnis | Definieren Sie Ziele für Phasenreinheit, Partikelgröße, Morphologie und chemische Zusammensetzung. |
Einschränkungen der Ausrüstung | Berücksichtigen Sie den Temperaturbereich des Ofens, die Heizrate, die Gleichmäßigkeit und die Atmosphäre. |
Experimentelle Versuche | Durchführung von Pilotversuchen und iterative Verfeinerung der Temperatur. |
Praktische Sachzwänge | Gleichgewicht zwischen Energieeffizienz, Sicherheit und Skalierbarkeit. |
Industrie-Normen | Referenzforschung, Herstellerempfehlungen und historische Daten. |
Benötigen Sie Hilfe bei der Auswahl der perfekten Kalzinierungstemperatur? Kontaktieren Sie unsere Experten noch heute für maßgeschneiderte Beratung!