Das Magnetronsputtern ist ein Verfahren zur physikalischen Gasphasenabscheidung (PVD), das häufig für die Abscheidung dünner Materialschichten auf Substraten verwendet wird.Das Verfahren arbeitet in einer Vakuumumgebung, in der ein Zielmaterial (Kathode) mit hochenergetischen Ionen beschossen wird, wodurch Atome aus der Zieloberfläche herausgeschleudert werden.Diese ausgestoßenen Atome wandern dann durch das Vakuum und lagern sich auf einem Substrat ab und bilden einen dünnen Film.Das Verfahren wird durch den Einsatz eines Magnetrons verbessert, das starke magnetische und elektrische Felder erzeugt, um die Elektronen in der Nähe der Zieloberfläche zu konzentrieren und die Ionisierung und Plasmadichte zu erhöhen.Dies führt zu einem effizienten Sputtern und einer qualitativ hochwertigen Schichtabscheidung, wodurch es sich für Anwendungen in der Optik, Elektronik und für industrielle Beschichtungen eignet.
Die wichtigsten Punkte erklärt:
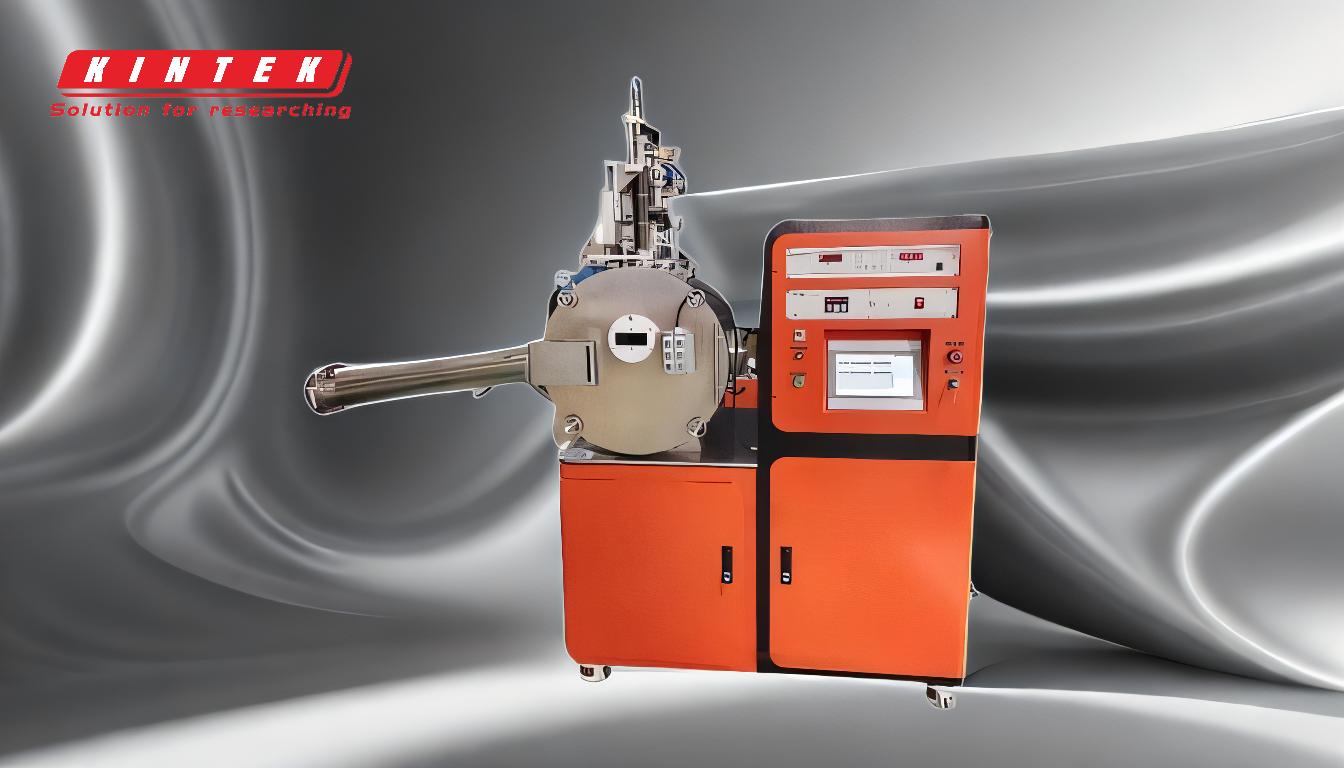
-
Grundlegender Mechanismus des Sputterns:
- Beim Magnetronsputtern wird ein Zielmaterial mit hochenergetischen Ionen beschossen, die in der Regel aus einem Inertgas wie Argon stammen.
- Die Ionen werden durch eine negative Spannung, die an das Target (Kathode) angelegt wird, auf das Target beschleunigt.
- Wenn die Ionen auf das Target treffen, übertragen sie kinetische Energie auf die Targetatome, wodurch diese von der Oberfläche abgestoßen werden (Sputtern).
-
Die Rolle des Magnetrons:
- Das Magnetron erzeugt ein Magnetfeld in der Nähe der Target-Oberfläche, das die Elektronen auf einer kreisförmigen Bahn einfängt.
- Dieser Einschluss erhöht die Verweilzeit der Elektronen im Plasma, was zu mehr Zusammenstößen mit Gasatomen und höheren Ionisierungsraten führt.
- Durch die erhöhte Ionisierung steigt die Dichte der für die Sputternutzung verfügbaren Ionen, was die Effizienz des Prozesses verbessert.
-
Plasmabildung und Wartung:
- Der Sputterprozess findet in einer Vakuumkammer statt, die mit einem Inertgas (z. B. Argon) gefüllt ist.
- Mit Hilfe elektrischer Energie wird das Gas ionisiert, wodurch ein Plasma aus Ionen, Elektronen und neutralen Atomen entsteht.
- Die beim Sputtern vom Target emittierten Sekundärelektronen stoßen mit den Gasatomen zusammen und tragen so zur Aufrechterhaltung des Plasmas bei.
-
Abscheidung von Dünnschichten:
- Aus dem Target ausgestoßene Atome (Sputteratome) wandern durch das Vakuum und lagern sich auf einem Substrat ab.
- Die abgeschiedenen Atome bilden einen dünnen, gleichmäßigen Film mit Eigenschaften wie hoher Dichte, guter Haftung und kontrollierter Dicke.
- Das Verfahren eignet sich für die Abscheidung einer breiten Palette von Materialien, darunter Metalle, Legierungen und Isolatoren.
-
Vorteile des Magnetronsputterns:
- Niedrige Abscheidetemperatur:Geeignet für temperaturempfindliche Substrate.
- Hochwertige Filme:Erzeugt dichte, gleichmäßige und fehlerfreie Beschichtungen.
- Vielseitigkeit:Abscheidung einer Vielzahl von Materialien, darunter Metalle, Keramiken und Polymere.
- Skalierbarkeit:Geeignet für die Beschichtung großflächiger Substrate mit gleichmäßiger Dicke.
-
Anwendungen:
- Optische Beschichtungen:Wird für Antireflex-, Reflexions- und transparente leitfähige Beschichtungen verwendet.
- Elektronik:Beschichtet dünne Schichten für Halbleiter, Sensoren und Displays.
- Industrielle Beschichtungen:Bietet verschleißfeste, korrosionsbeständige und dekorative Beschichtungen.
-
Prozesskontrolle:
- Parameter wie Gasdruck, Zielspannung, Magnetfeldstärke und Substrattemperatur können zur Optimierung der Schichteigenschaften eingestellt werden.
- Das Verfahren ist in hohem Maße steuerbar und ermöglicht eine präzise Abstimmung von Schichtdicke, Zusammensetzung und Mikrostruktur.
-
Herausforderungen und Überlegungen:
- Die Ausnutzung des Ziels kann aufgrund des lokal begrenzten Ionenbeschusses ungleichmäßig sein.
- Das Verfahren erfordert eine Hochvakuumumgebung, deren Aufrechterhaltung kostspielig sein kann.
- Eine sorgfältige Auswahl des Zielmaterials und der Prozessparameter ist notwendig, um die gewünschten Schichteigenschaften zu erreichen.
Wenn man diese Schlüsselpunkte versteht, kann man die Komplexität und Vielseitigkeit des Magnetronsputterns als Beschichtungsverfahren verstehen, was es zu einem wertvollen Werkzeug für verschiedene industrielle und wissenschaftliche Anwendungen macht.
Zusammenfassende Tabelle:
Aspekt | Einzelheiten |
---|---|
Mechanismus | Beschuss eines Targets mit hochenergetischen Ionen, um Atome zur Abscheidung auszustoßen. |
Die Rolle des Magnetrons | Hält die Elektronen in der Nähe des Targets, wodurch die Ionisierung und die Effizienz erhöht werden. |
Plasmabildung | Inertes Gas, das zur Erzeugung eines Plasmas ionisiert wird, das den Sputterprozess unterstützt. |
Vorteile | Niedrige Abscheidetemperatur, hochwertige Schichten, Vielseitigkeit, Skalierbarkeit. |
Anwendungen | Optische Beschichtungen, Elektronik, industrielle Beschichtungen. |
Prozesskontrolle | Einstellbare Parameter für präzise Folieneigenschaften. |
Herausforderungen | Ungleichmäßige Targetnutzung, hohe Vakuumkosten, Materialauswahl. |
Sind Sie daran interessiert, Magnetronsputtern für Ihre Projekte zu nutzen? Kontaktieren Sie uns noch heute um mehr zu erfahren!