Synthetischer Graphit wird durch eine Reihe komplexer Verfahren hergestellt, die kohlenstoffreiche Materialien in hochreinen Graphit umwandeln.Die Herstellung umfasst in der Regel die folgenden Schritte: Auswahl des Rohmaterials, Verkohlung, Graphitierung und Reinigung.Das Verfahren beginnt mit kohlenstoffreichen Ausgangsstoffen wie Petrolkoks oder Steinkohlenteerpech, die auf hohe Temperaturen erhitzt werden, um flüchtige Bestandteile zu entfernen und eine Kohlenstoffstruktur zu bilden.Diese Kohlenstoffstruktur wird dann weiter auf extrem hohe Temperaturen (bis zu 3000 °C) erhitzt, um die Kohlenstoffatome in der kristallinen Struktur von Graphit auszurichten.Schließlich wird das Material gereinigt, um Verunreinigungen zu entfernen, so dass hochwertiger synthetischer Graphit entsteht.Dieses Material wird aufgrund seiner ausgezeichneten Leitfähigkeit, thermischen Stabilität und chemischen Beständigkeit häufig in Branchen wie Batterien, Elektronik und Metallurgie eingesetzt.
Die wichtigsten Punkte erklärt:
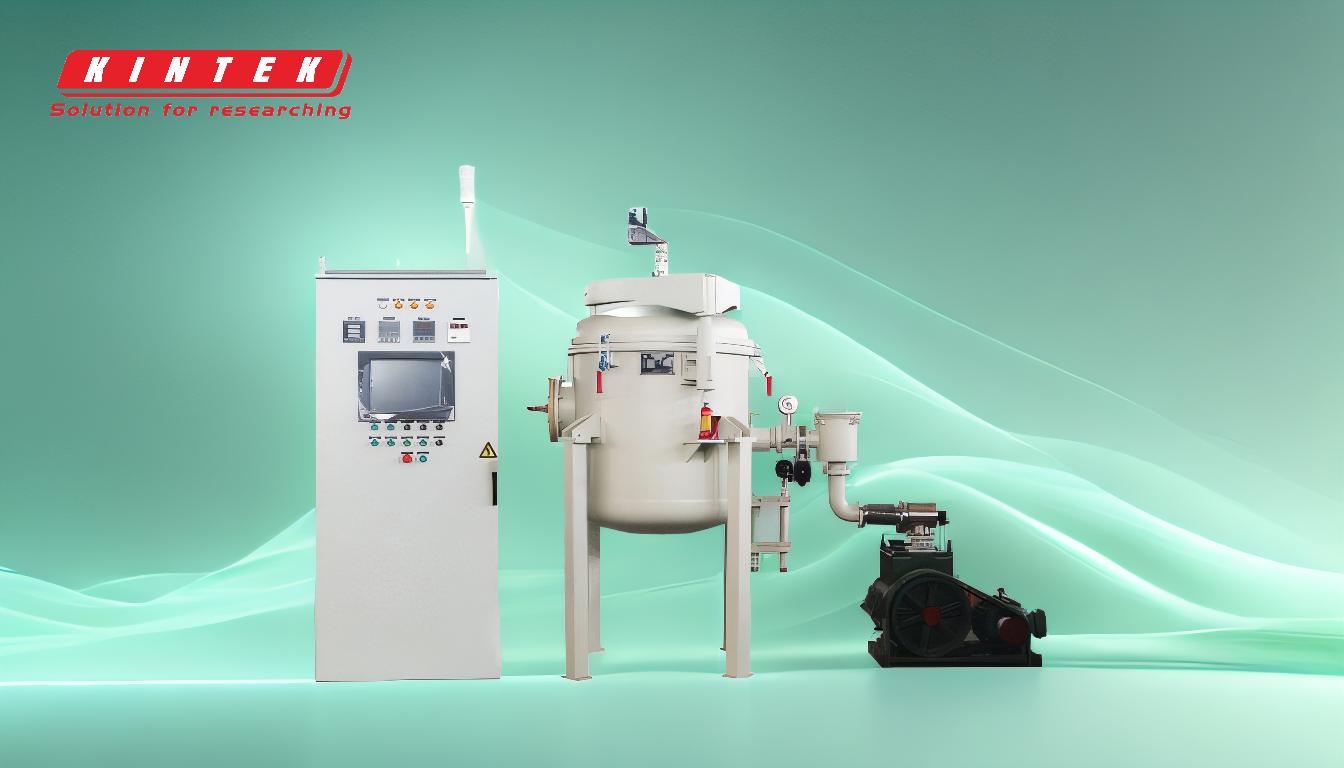
-
Auswahl der Rohmaterialien:
- Der Herstellungsprozess beginnt mit der Auswahl kohlenstoffreicher Ausgangsstoffe, in der Regel Petrolkoks oder Steinkohlenteerpech.Diese Materialien werden aufgrund ihres hohen Kohlenstoffgehalts und ihrer Fähigkeit, beim Erhitzen eine stabile Kohlenstoffstruktur zu bilden, ausgewählt.
- Petrolkoks ist ein Nebenprodukt der Erdölraffination, während Steinkohlenteerpech aus der Kohleverarbeitung gewonnen wird.Beide Materialien sind kostengünstig und liefern das notwendige Kohlenstoffgerüst für die Herstellung von synthetischem Graphit.
-
Verkohlung:
- Die ausgewählten Rohstoffe werden einer Karbonisierung unterzogen, einem Verfahren, bei dem sie in einer sauerstofffreien Umgebung auf Temperaturen zwischen 500°C und 1500°C erhitzt werden.Bei diesem Schritt werden flüchtige Bestandteile wie Wasserstoff, Sauerstoff und Stickstoff entfernt, so dass eine feste Kohlenstoffstruktur zurückbleibt.
- Der Verkohlungsprozess ist entscheidend für die Bildung des anfänglichen Kohlenstoffgerüsts, das später in Graphit umgewandelt wird.
-
Graphitisierung:
- Nach der Karbonisierung wird das Material einer Graphitierung unterzogen, bei der es in einer inerten Atmosphäre auf extrem hohe Temperaturen (bis zu 3000 °C) erhitzt wird.In diesem Schritt werden die Kohlenstoffatome zu einer kristallinen Graphitstruktur ausgerichtet.
- Die Graphitierung ist eine wesentliche Voraussetzung für die Erzielung der gewünschten Eigenschaften von synthetischem Graphit, wie hohe elektrische Leitfähigkeit, thermische Stabilität und mechanische Festigkeit.
-
Reinigung:
- Der letzte Schritt im Herstellungsprozess ist die Reinigung, bei der der Graphit behandelt wird, um alle verbleibenden Verunreinigungen zu entfernen.Dies geschieht in der Regel durch chemische oder thermische Verfahren wie das Waschen mit Säure oder die Hochtemperaturbehandlung in einer Chlorgasumgebung.
- Durch die Reinigung wird sichergestellt, dass der synthetische Graphit die hohen Reinheitsstandards erfüllt, die für Anwendungen in Branchen wie Elektronik und Batterien erforderlich sind.
-
Anwendungen von synthetischem Graphit:
- Synthetischer Graphit wird aufgrund seiner einzigartigen Eigenschaften in verschiedenen Industriezweigen eingesetzt.In der Batterieindustrie ist er ein wichtiger Bestandteil von Lithium-Ionen-Batterien und dient als Anodenmaterial.
- Er wird auch bei der Herstellung von Elektroden für Elektrolichtbogenöfen in der Stahlindustrie sowie bei Hochtemperaturanwendungen wie Tiegeln und Wärmemanagementsystemen verwendet.
-
Vorteile von synthetischem Graphit:
- Synthetischer Graphit bietet gegenüber natürlichem Graphit mehrere Vorteile, darunter eine höhere Reinheit, eine bessere Konsistenz und die Möglichkeit, seine Eigenschaften für spezifische Anwendungen anzupassen.
- Seine ausgezeichnete elektrische Leitfähigkeit, thermische Stabilität und chemische Beständigkeit machen ihn zu einem vielseitigen Material für eine breite Palette industrieller Anwendungen.
Wenn die Käufer die einzelnen Schritte der Herstellung von synthetischem Graphit kennen, können sie fundierte Entscheidungen über die Eignung des Materials für ihre spezifischen Bedürfnisse treffen.Der Prozess stellt sicher, dass das Endprodukt die hohen Anforderungen für anspruchsvolle Anwendungen erfüllt, was synthetischen Graphit zu einem wertvollen Material in der modernen Industrie macht.
Zusammenfassende Tabelle:
Schritt | Beschreibung | Wichtige Details |
---|---|---|
Auswahl des Rohmaterials | Auswahl von kohlenstoffreichen Ausgangsstoffen wie Petrolkoks oder Steinkohlenteerpech. | Hoher Kohlenstoffgehalt, kostengünstige und stabile Kohlenstoffstrukturbildung. |
Verkohlung | Erhitzen auf 500°C-1500°C in einer sauerstofffreien Umgebung, um flüchtige Bestandteile zu entfernen. | Bildet eine feste Kohlenstoffstruktur; entscheidend für das anfängliche Kohlenstoffgerüst. |
Graphitierung | Erhitzen auf bis zu 3000 °C, um die Kohlenstoffatome zu einer kristallinen Graphitstruktur auszurichten. | Verbessert die elektrische Leitfähigkeit, thermische Stabilität und mechanische Festigkeit. |
Reinigung | Entfernung von Verunreinigungen durch chemische oder thermische Verfahren wie Säurewaschen. | Gewährleistet hohe Reinheit für Anwendungen in Elektronik und Batterien. |
Entdecken Sie, wie synthetischer Graphit Ihre industriellen Anforderungen erfüllen kann. Kontaktieren Sie unsere Experten noch heute !