Die für die Wärmebehandlung von Metall erforderliche Zeit variiert erheblich und hängt von der Art des Metalls, dem spezifischen Wärmebehandlungsprozess, den gewünschten Eigenschaften sowie der Größe und Form des Metallstücks ab. Wärmebehandlungsprozesse wie Glühen, Härten, Anlassen und Einsatzhärten haben alle unterschiedliche Zeitanforderungen. Beispielsweise kann das Glühen mehrere Stunden dauern, um eine gleichmäßige Erwärmung und langsame Abkühlung zu gewährleisten, während das Härten weniger Zeit in Anspruch nehmen könnte, aber eine präzise Temperaturkontrolle und schnelle Abkühlung erfordert. Darüber hinaus beeinflussen Größe und Dicke des Metallstücks die Aufheiz- und Abkühlgeschwindigkeit, wobei größere oder dickere Stücke mehr Zeit benötigen. Insgesamt können die Wärmebehandlungszeiten bei komplexen Prozessen von wenigen Minuten bis zu mehreren Stunden oder sogar Tagen reichen.
Wichtige Punkte erklärt:
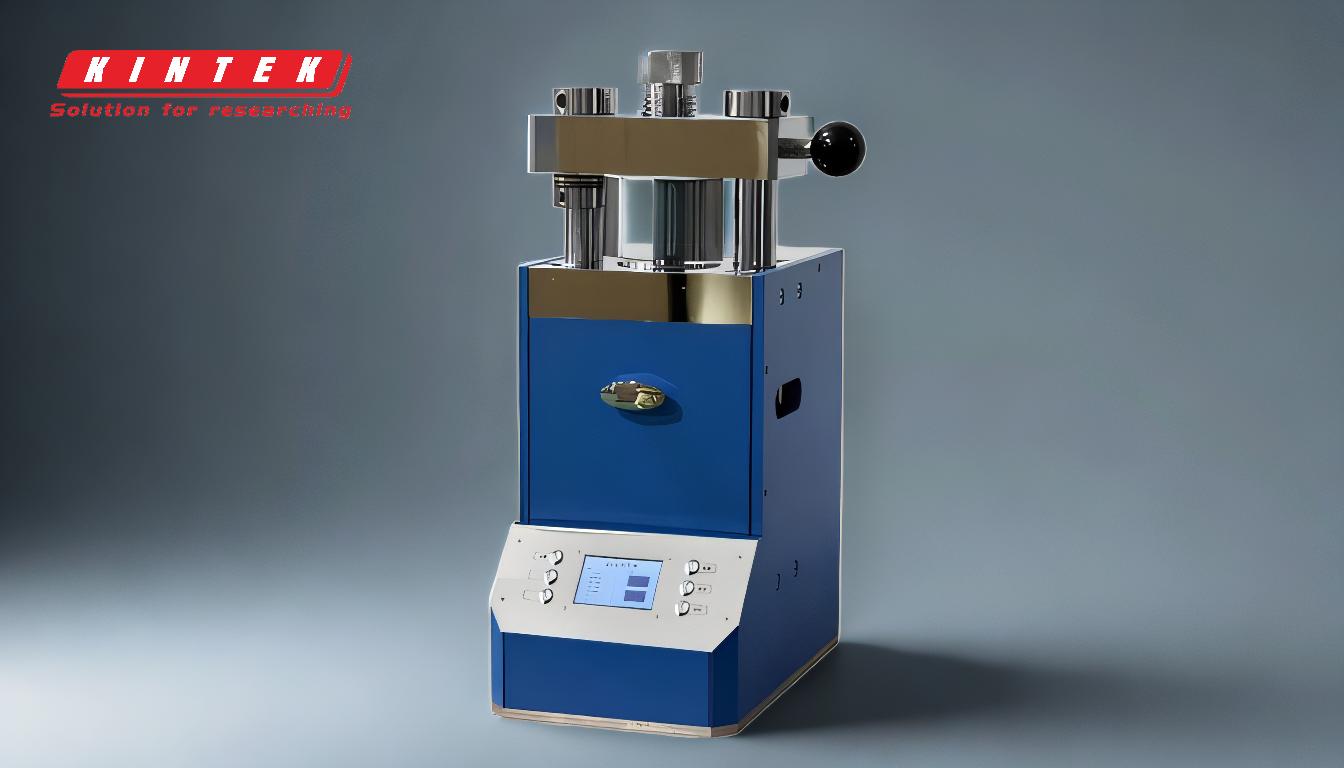
-
Art des Metalls:
- Verschiedene Metalle haben unterschiedliche Anforderungen an die Wärmebehandlung. Beispielsweise erfordern Stahl und Aluminium unterschiedliche Temperaturen und Abkühlgeschwindigkeiten. Stahl wird häufig Prozessen wie Glühen, Abschrecken und Anlassen unterzogen, während Aluminium möglicherweise lösungsgeglüht und gealtert wird. Die einzigartigen Eigenschaften jedes Metalls bestimmen die Dauer des Wärmebehandlungsprozesses.
-
Wärmebehandlungsprozess:
- Glühen: Bei diesem Prozess wird das Metall auf eine bestimmte Temperatur erhitzt, dort eine Zeit lang gehalten, um eine gleichmäßige Temperaturverteilung zu erreichen, und dann langsam abgekühlt. Das Glühen kann insbesondere bei größeren Teilen mehrere Stunden dauern, um eine Spannungsentlastung und eine bessere Bearbeitbarkeit zu gewährleisten.
- Härten: Beim Härten wird das Metall typischerweise auf eine hohe Temperatur erhitzt und dann schnell abgekühlt (Abschrecken), um die Härte zu erhöhen. Die Aufheizphase kann im Vergleich zum Glühen weniger Zeit in Anspruch nehmen, die schnelle Abkühlung muss jedoch präzise gesteuert werden.
- Temperieren: Nach dem Härten wird häufig ein Anlassen durchgeführt, um die Sprödigkeit zu verringern. Dabei wird das Metall erneut auf eine niedrigere Temperatur erhitzt und für eine bestimmte Zeit gehalten, die von einigen Minuten bis zu mehreren Stunden reichen kann.
- Einsatzhärten: Dieser Prozess härtet nur die Oberfläche des Metalls, während der Kern weich bleibt. Die erforderliche Zeit hängt von der gewünschten Tiefe der ausgehärteten Schicht ab und kann zwischen einigen Stunden und einem ganzen Tag variieren.
-
Gewünschte Eigenschaften:
- Die gewünschten spezifischen mechanischen Eigenschaften wie Härte, Zähigkeit oder Duktilität beeinflussen die Dauer der Wärmebehandlung. Um beispielsweise eine hohe Härte zu erreichen, ist möglicherweise eine längere Anlasszeit erforderlich, um Härte und Zähigkeit auszugleichen.
-
Größe und Form des Metallstücks:
- Größere oder dickere Metallteile brauchen länger, um gleichmäßig zu erhitzen und gleichmäßig abzukühlen. Die Masse des Metalls beeinflusst die Wärmeübertragungsrate, was bedeutet, dass eine dicke Stahlplatte im Vergleich zu einem dünnen Blech mehr Zeit benötigt, um über ihr gesamtes Volumen die gewünschte Temperatur zu erreichen.
-
Heiz- und Kühlraten:
- Die Geschwindigkeit, mit der das Metall erhitzt und abgekühlt wird, spielt eine entscheidende Rolle im Wärmebehandlungsprozess. Schnelles Erhitzen kann zu thermischen Spannungen führen, während langsames Abkühlen für Prozesse wie Glühen unerlässlich ist, um Risse zu verhindern.
-
Ausrüstung und Umwelt:
- Die Art des verwendeten Ofens oder der verwendeten Heizausrüstung kann die Wärmebehandlungszeit beeinflussen. Moderne, hocheffiziente Öfen können im Vergleich zu älteren Modellen den Zeitaufwand verkürzen. Darüber hinaus kann die Umgebung (z. B. kontrollierte Atmosphäre oder Vakuum) die Prozessdauer beeinflussen.
Zusammenfassend lässt sich sagen, dass die für die Wärmebehandlung von Metall erforderliche Zeit von mehreren Faktoren beeinflusst wird, darunter der Art des Metalls, dem spezifischen Wärmebehandlungsprozess, den gewünschten Eigenschaften sowie der Größe und Form des Metallstücks. Das Verständnis dieser Faktoren hilft bei der Planung und Optimierung des Wärmebehandlungsprozesses, um die gewünschten Ergebnisse effizient zu erzielen.
Übersichtstabelle:
Faktor | Auswirkungen auf die Wärmebehandlungszeit |
---|---|
Art des Metalls | Unterschiedliche Metalle (z. B. Stahl, Aluminium) erfordern unterschiedliche Temperaturen und Abkühlgeschwindigkeiten. |
Wärmebehandlungsprozess | Glühen: Stunden; Aushärten: weniger Zeit; Temperierung: Minuten bis Stunden; Einsatzhärten: Stunden bis Tage. |
Gewünschte Eigenschaften | Härte-, Zähigkeits- oder Duktilitätsziele beeinflussen die Dauer. |
Größe und Form | Bei größeren oder dickeren Stücken dauert es länger, bis sie gleichmäßig erhitzt und abgekühlt sind. |
Heiz-/Kühlraten | Schnelles Erhitzen oder Abkühlen wirkt sich auf Zeit und Qualität aus. |
Ausrüstung/Umgebung | Moderne Öfen und kontrollierte Umgebungen können die Verarbeitungszeit verkürzen. |
Benötigen Sie Hilfe bei der Optimierung Ihres Wärmebehandlungsprozesses? Kontaktieren Sie noch heute unsere Experten!