Das Magnetronsputtern ist ein vielseitiges Verfahren zur Abscheidung von Dünnschichten, das die Beschichtung verschiedener Materialien mit präziser Kontrolle über Dicke und Gleichmäßigkeit ermöglicht.Die Dicke der gesputterten Schichten kann je nach Anwendung, Zielmaterial und Prozessparametern zwischen einigen Nanometern und mehreren Mikrometern liegen.Faktoren wie der Abstand zwischen Target und Substrat, die Ionenenergie, der Gasdruck und die Temperatur spielen eine wichtige Rolle bei der Bestimmung der endgültigen Dicke und Gleichmäßigkeit der abgeschiedenen Schicht.Diese Technik wird in vielen Branchen eingesetzt, in denen hochwertige Beschichtungen erforderlich sind, z. B. bei Halbleitern, in der Optik und bei verschleißfesten Oberflächen.
Die wichtigsten Punkte werden erklärt:
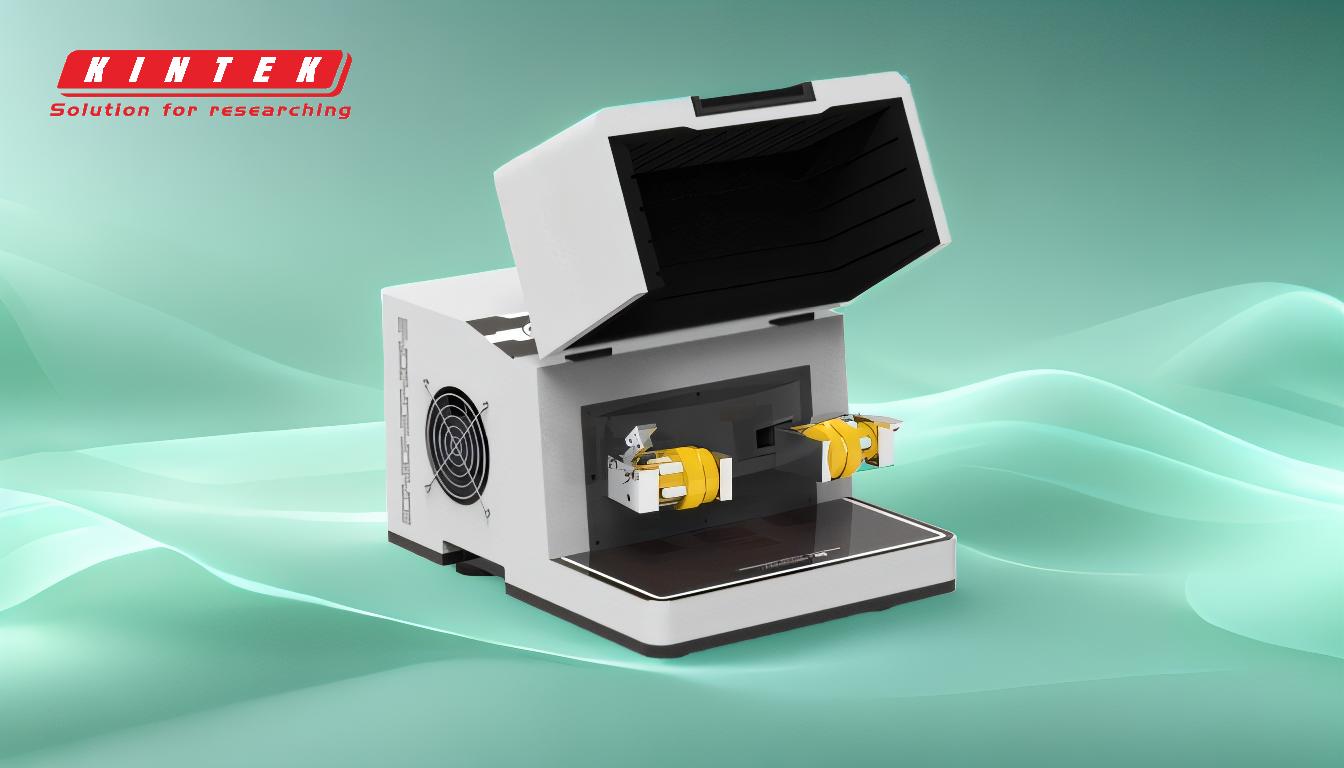
-
Schichtdickenbereich beim Magnetronsputtern:
- Durch Magnetronsputtern lassen sich dünne Schichten mit einer Dicke von Nanometern bis Mikrometern .Dank dieser Flexibilität eignet es sich für eine breite Palette von Anwendungen, von optischen Beschichtungen bis hin zu Halbleiterbauelementen.
- Die Dicke hängt von der Abscheidungszeit, dem Zielmaterial und den Prozessbedingungen ab.So führt beispielsweise eine längere Abscheidungszeit im Allgemeinen zu einer dickeren Schicht.
-
Faktoren, die die Dicke und Gleichmäßigkeit beeinflussen:
- Ziel-Substrat-Abstand:Der Abstand zwischen dem Target und dem Substrat beeinflusst die Abscheiderate und die Gleichmäßigkeit.Ein geringerer Abstand führt in der Regel zu höheren Abscheideraten, kann aber die Gleichmäßigkeit beeinträchtigen.
- Ionenenergie:Eine höhere Ionenenergie erhöht die Sputtering-Rate und führt zu dickeren Schichten.Eine zu hohe Energie kann jedoch das Substrat beschädigen oder die Schichteigenschaften verändern.
- Gasdruck:Der Druck des Sputtergases (in der Regel Argon) beeinflusst die mittlere freie Weglänge der gesputterten Teilchen.Ein optimaler Druck gewährleistet eine effiziente Abscheidung und eine gleichmäßige Dicke.
- Temperatur:Die Temperatur des Substrats kann sich auf die Haftung und die Kristallinität des Films auswirken und damit indirekt die Gleichmäßigkeit der Schichtdicke beeinflussen.
- Erosionszielbereich:Das Erosionsprofil des Targetmaterials beeinflusst die Verteilung der gesputterten Partikel und wirkt sich auf die Gleichmäßigkeit der Schicht aus.
-
Vorteile des Magnetron-Sputterns für die Schichtdickenkontrolle:
- Hohe Präzision:Das Magnetron-Sputtern ermöglicht eine präzise Kontrolle der Schichtdicke und ist damit ideal für Anwendungen, die eine Genauigkeit im Nanobereich erfordern.
- Gleichmäßige Abscheidung:Durch den Einsatz von Magnetfeldern zum Einfangen von Sekundärelektronen in der Nähe der Zieloberfläche wird die Plasmadichte erhöht, was zu einer gleichmäßigeren Abscheidung führt.
- Vielseitigkeit:Es kann eine breite Palette von Materialien, einschließlich Metallen, Legierungen und Keramiken, mit gleichbleibender Dicke und Qualität abscheiden.
-
Vergleich mit anderen Abscheidetechniken:
- Im Vergleich zur Elektronenstrahlbeschichtung Das Magnetronsputtern bietet eine bessere Kontrolle über die Schichtdicke und die Gleichmäßigkeit, insbesondere bei exotischen Materialien und wärmeempfindlichen Substraten.
- Diodenzerstäubung , eine frühere Technik, wies Einschränkungen in Bezug auf Abscheidungsraten und Gleichmäßigkeit auf, die mit der Einführung des Magnetron-Sputterns im Jahr 1974 überwunden wurden.
-
Anwendungen, die bestimmte Schichtdicken erfordern:
- Optische Beschichtungen:Dünne Schichten mit präzisen Dicken sind für Antireflexionsbeschichtungen, Spiegel und Filter unerlässlich.
- Halbleiterbauelemente:Gleichmäßige dünne Schichten sind entscheidend für integrierte Schaltungen und mikroelektronische Komponenten.
- Verschleißbeständige Beschichtungen:Für Anwendungen wie Schneidwerkzeuge und mechanische Teile werden häufig dickere Schichten benötigt.
Zusammenfassend lässt sich sagen, dass das Magnetronsputtern eine äußerst anpassungsfähige und präzise Technik für die Abscheidung dünner Schichten mit kontrollierter Dicke und Gleichmäßigkeit ist.Seine Fähigkeit, eine breite Palette von Materialien und Anwendungen zu verarbeiten, in Verbindung mit seinen hohen Abscheideraten und seiner verbesserten Plasmastabilität, macht es zu einer bevorzugten Wahl in vielen Branchen.
Zusammenfassende Tabelle:
Aspekt | Einzelheiten |
---|---|
Dickenbereich | Nanometer bis Mikrometer |
Wichtige Einflussfaktoren | Ziel-Substrat-Abstand, Ionenenergie, Gasdruck, Temperatur |
Vorteile | Hohe Präzision, gleichmäßige Abscheidung, Vielseitigkeit |
Anwendungen | Optische Beschichtungen, Halbleiterbauelemente, verschleißfeste Beschichtungen |
Benötigen Sie präzise Dünnschichtlösungen? Kontaktieren Sie uns heute um mehr über Magnetronsputtern zu erfahren!