Das Kalzinieren erfolgt normalerweise nicht in einem Hochofen.Stattdessen wird sie in erster Linie in speziellen Öfen, wie z. B. in einem Flammofen oder einem Drehrohrofen, durchgeführt, die so konzipiert sind, dass sie kontrollierte Erhitzungsbedingungen unterhalb des Schmelzpunkts des Materials bieten.Bei der Kalzinierung werden Materialien unter Abwesenheit oder begrenzter Zufuhr von Luft erhitzt, um eine thermische Zersetzung einzuleiten, flüchtige Stoffe zu entfernen oder Phasenübergänge zu bewirken.Während das Rösten in kleinem Maßstab, bei dem nur wenig Sauerstoff benötigt wird, in einem Hochofen stattfinden kann, ist das Kalzinieren etwas anderes und erfordert in der Regel andere Anlagen.Der Hochofen wird eher mit Schmelzprozessen in Verbindung gebracht, bei denen hohe Temperaturen und spezifische chemische Reaktionen eingesetzt werden, um Metalle aus Erzen zu gewinnen.
Die wichtigsten Punkte erklärt:
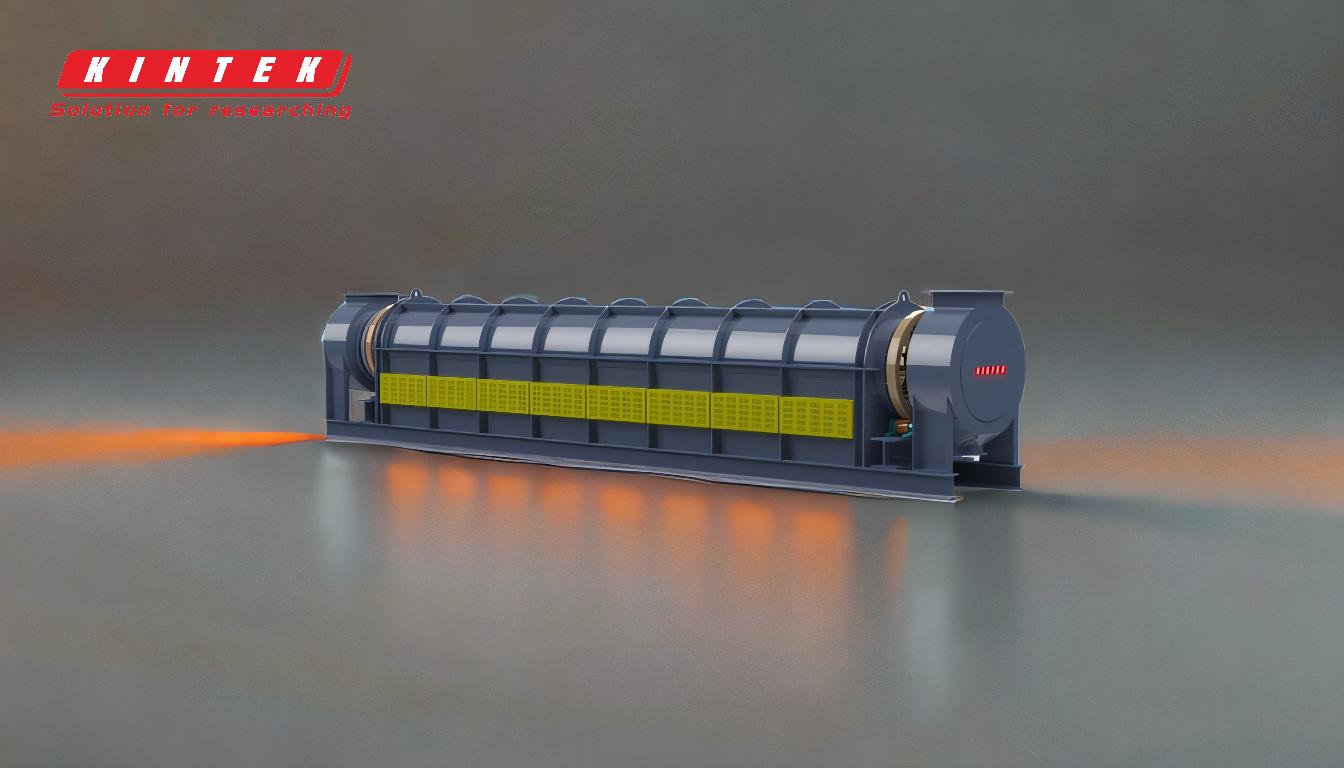
-
Definition der Kalzination:
- Das Kalzinieren ist ein Wärmebehandlungsverfahren, bei dem feste Materialien, wie z. B. Erze, unter Abwesenheit oder begrenzter Zufuhr von Luft oder Sauerstoff unter ihren Schmelzpunkt erhitzt werden.Dieser Prozess führt zu einer thermischen Zersetzung, entfernt flüchtige Bestandteile oder bewirkt Phasenübergänge.
-
Typische Ausrüstung für die Kalzinierung:
- Die Kalzinierung erfolgt in der Regel in speziellen Anlagen wie Flammrohröfen oder Drehrohröfen .Diese Öfen sind für kontrollierte Heizbedingungen ausgelegt und eignen sich für Prozesse, die eine präzise Temperaturregelung erfordern.
- So haben zum Beispiel Kammeröfen eine horizontale "S"-Form und können je nach den spezifischen Anforderungen des Prozesses mit oder ohne Sauerstoff betrieben werden.
-
Hochofen und Kalzinierung:
- A Hochofen wird hauptsächlich verwendet für Schmelzen Schmelzen ist ein Verfahren, das hohe Temperaturen und chemische Reaktionen zur Gewinnung von Metallen aus Erzen erfordert.Er wird in der Regel nicht zur Kalzinierung verwendet.
- Während das Rösten (ein der Kalzinierung ähnlicher Prozess, bei dem jedoch nur wenig Sauerstoff benötigt wird) in kleinem Umfang in einem Hochofen stattfinden kann, ist die Kalzinierung selbst etwas anderes und erfordert im Allgemeinen andere Anlagen.
-
Zweck der Kalzinierung:
- Der Hauptzweck der Kalzinierung besteht darin, flüchtige Verunreinigungen zu entfernen oder eine chemische Dissoziation in den Materialien zu bewirken.Bei der Herstellung von Kalk aus Kalkstein zum Beispiel wird durch die Kalzinierung Kohlendioxid ausgetrieben, so dass der Kalk in Pulverform zurückbleibt.
-
Beispiele für die Kalzinierung:
- Ein klassisches Beispiel für die Kalzinierung ist die Umwandlung von Kalkstein (CaCO₃) auf Kalk (CaO) .Wenn Kalkstein erhitzt wird, zersetzt er sich thermisch, wobei Kohlendioxid (CO₂) freigesetzt wird und Kalk entsteht.
- Andere Materialien, wie Dolomit und Magnesit, werden ebenfalls gebrannt, um bestimmte chemische oder physikalische Eigenschaften zu erzielen.
-
Drehrohröfen für die Kalzinierung:
- Drehrohröfen werden häufig zum Kalzinieren verwendet, insbesondere für Materialien mit einer Korngröße von 60 mm oder weniger.Diese Öfen bieten eine gleichmäßige Erwärmung und sind effizient für die Herstellung hochwertiger, gleichmäßiger Produkte.
-
Kontrast zum Rösten:
- Das Rösten ist ein ähnliches Verfahren, bei dem die Erze jedoch in der Regel in Gegenwart von überschüssiger Luft oder Sauerstoff erhitzt werden.Es wird häufig zur Oxidation von sulfidischen Erzen eingesetzt, während beim Kalzinieren der Schwerpunkt auf der thermischen Zersetzung oder der Entfernung flüchtiger Stoffe liegt.
-
Hauptunterschiede zwischen Kalzinierung und Hochofenverfahren:
- Die Kalzinierung ist ein thermischer Zersetzungsprozess der unterhalb des Schmelzpunktes des Materials stattfindet, während Hochofenprozesse Schmelzen die bei viel höheren Temperaturen erfolgt und oft eine chemische Reduktion beinhaltet.
- Die Kalzinierung erfolgt in der Regel in Flammöfen oder Drehrohröfen wohingegen Hochöfen verwendet werden für Eisenerzeugung und andere Metallgewinnungsverfahren.
Zusammenfassend lässt sich sagen, dass die Kalzinierung nicht in einem Hochofen erfolgt.Stattdessen wird sie in speziellen Anlagen durchgeführt, die für eine kontrollierte Erhitzung und thermische Zersetzung ausgelegt sind.Der Hochofen ist dem Schmelzen und anderen Hochtemperaturprozessen vorbehalten und daher für die präzisen Anforderungen der Kalzinierung nicht geeignet.
Zusammenfassende Tabelle:
Hauptpunkt | Einzelheiten |
---|---|
Definition von Kalzinierung | Thermische Zersetzung unterhalb des Schmelzpunktes, oft unter Ausschluss von Luft/Sauerstoff. |
Typische Ausrüstung | Hochöfen, Drehrohröfen. |
Verwendung von Hochöfen | In erster Linie zum Schmelzen, nicht zum Kalzinieren. |
Zweck der Kalzinierung | Entfernen flüchtiger Verunreinigungen oder Herbeiführen einer chemischen Dissoziation. |
Beispiel | Umwandlung von Kalkstein (CaCO₃) in Kalk (CaO). |
Drehrohröfen | Ideal für die gleichmäßige Erwärmung von Materialien ≤60 mm. |
Gegensatz zum Rösten | Beim Rösten wird überschüssige Luft verwendet; beim Kalzinieren steht die thermische Zersetzung im Vordergrund. |
Sie benötigen den richtigen Ofen für Ihr Kalzinierungsverfahren? Kontaktieren Sie noch heute unsere Experten um die perfekte Lösung zu finden!