Die Pulvermetallurgie ist ein vielseitiges Herstellungsverfahren, das zahlreiche Vorteile bietet, wie z. B. Energieeffizienz, Kosteneffizienz und die Möglichkeit, komplexe, hochpräzise Teile mit minimalem Abfall herzustellen. Aufgrund seiner Fähigkeit, homogene und einheitliche Teile mit außergewöhnlichen Toleranzen herzustellen, ist es besonders für Branchen wie die Automobil- und Luft- und Raumfahrtindustrie von Vorteil. Es weist jedoch auch Einschränkungen auf, darunter Größenbeschränkungen, Herausforderungen bei der Herstellung hochkomplexer Formen sowie eine geringere Festigkeit und Duktilität im Vergleich zu herkömmlichen Guss- oder Schmiedeverfahren. Trotz dieser Nachteile bleibt die Pulvermetallurgie eine wichtige und umweltfreundliche Technologie in der modernen Fertigung.
Wichtige Punkte erklärt:
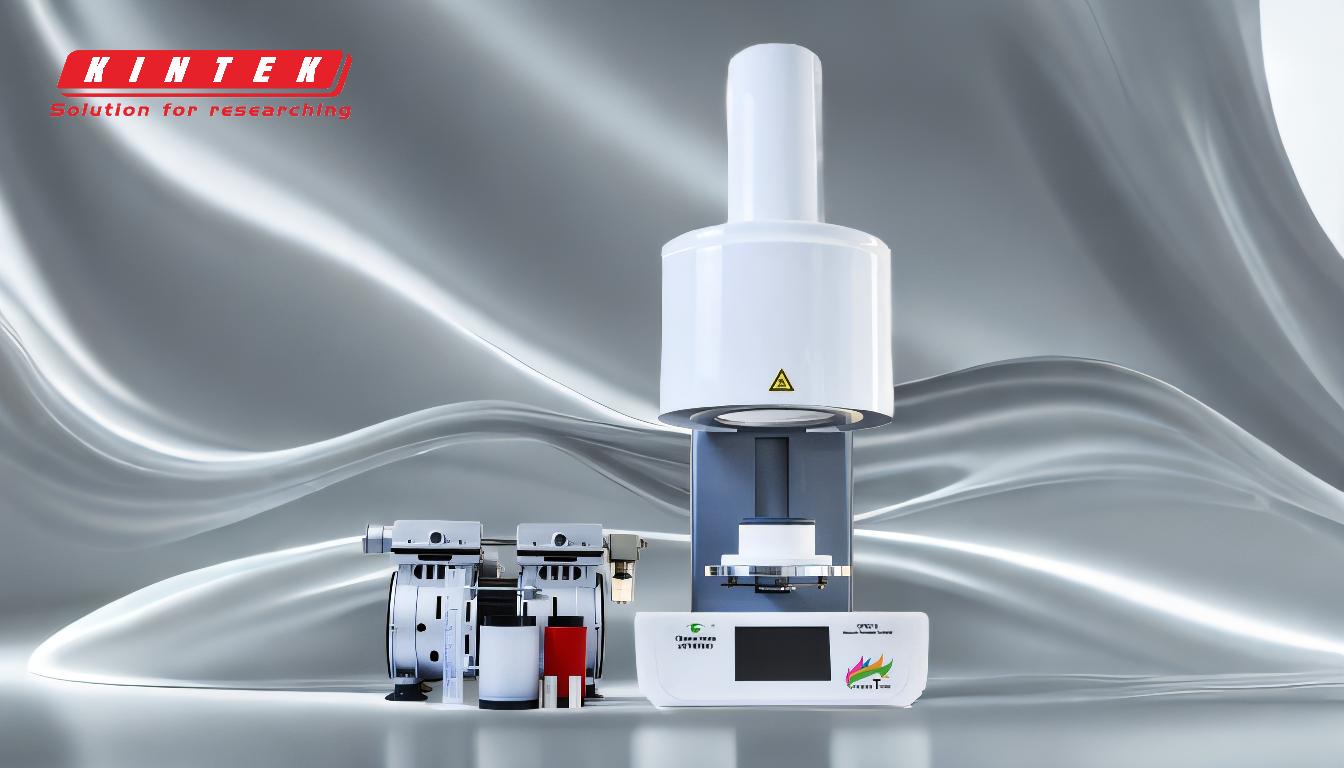
-
Vorteile der Pulvermetallurgie:
- Energieeffizienz und Kosteneffizienz: Pulvermetallurgie ist ein kurzer und effizienter Prozess, der den Energieverbrauch und die Materialverschwendung reduziert. Ungefähr 97 % des verwendeten Materials werden Teil des Endprodukts, wodurch der Ausschuss minimiert und die Kosten gesenkt werden.
- Präzision und Einheitlichkeit: Das Verfahren ermöglicht die Herstellung homogener und einheitlicher Teile mit außergewöhnlichen Toleranzen und ist somit ideal für hochpräzise Anwendungen.
- Materialflexibilität: Die Pulvermetallurgie ermöglicht den Aufbau von Materialstrukturen zur genauen Steuerung der Eigenschaften und eignet sich daher für die Herstellung hochwertiger Materialien, insbesondere Legierungen mit hohen Schmelzpunkten oder schlechter Gießbarkeit.
- Umweltfreundliche Herstellung: Mit minimalem Abfall und keinem Ausschuss gilt die Pulvermetallurgie als umweltfreundliche Fertigungstechnologie und steht im Einklang mit nachhaltigen Produktionspraktiken.
-
Anwendungen in Schlüsselindustrien:
- Automobil und Luft- und Raumfahrt: Die Fähigkeit, leichte, langlebige und hochpräzise Komponenten herzustellen, macht die Pulvermetallurgie zu einem lebenswichtigen Prozess für diese Branchen.
- Handwerkzeuge: Mit Pulvermetallurgie hergestellte Werkzeuge weisen eine überlegene Verschleißfestigkeit, Zähigkeit und Härtebeständigkeit auf und halten bis zu fünfmal länger als mit anderen Methoden hergestellte Werkzeuge.
-
Nachteile der Pulvermetallurgie:
- Größenbeschränkungen: Die größten Pressen der Branche wiegen etwa 1.500 Tonnen, was die praktische Größe der Teile auf etwa 40–50 Quadratzoll planarer Fläche begrenzt.
- Komplexe Formen: Während qualifizierte Hersteller einige Herausforderungen meistern können, kann die Herstellung hochkomplex geformter Teile immer noch schwierig sein.
- Festigkeit und Duktilität: Pulvermetallurgische Teile sind im Allgemeinen nicht so fest oder duktil wie durch Gießen oder Schmieden hergestellte Teile, was ihre Verwendung in Anwendungen, die eine hohe mechanische Leistung erfordern, einschränken kann.
-
Zukunftsaussichten:
- Die Präzision und Effizienz der Pulvermetallurgie machen sie zu einer vielversprechenden Technologie für die zukünftige Fertigung, insbesondere da die Industrie weiterhin Wert auf Nachhaltigkeit und Hochleistungsmaterialien legt. Es ist wahrscheinlich, dass in naher Zukunft weitere Branchen, darunter auch die Herstellung von Handwerkzeugen, diese Methode übernehmen werden.
Zusammenfassend lässt sich sagen, dass die Pulvermetallurgie erhebliche Vorteile hinsichtlich Effizienz, Präzision und Nachhaltigkeit bietet, jedoch auch Einschränkungen hinsichtlich der Teilegröße, Komplexität und mechanischen Eigenschaften aufweist. Das Verständnis dieser Kompromisse ist für Hersteller und Käufer von entscheidender Bedeutung, wenn sie diese Technologie für bestimmte Anwendungen in Betracht ziehen.
Übersichtstabelle:
Aspekt | Vorteile | Nachteile |
---|---|---|
Energieeffizienz | Reduziert den Energieverbrauch und die Materialverschwendung (97 % Materialausnutzung). | Begrenzt durch die Pressengröße (bis zu 1.500 Tonnen). |
Präzision und Gleichmäßigkeit | Produziert homogene, hochpräzise Teile mit außergewöhnlichen Toleranzen. | Herausforderungen bei der Herstellung hochkomplexer Formen. |
Materialflexibilität | Ermöglicht die Kontrolle über Materialeigenschaften, ideal für Legierungen mit hohem Mehrwert. | Geringere Festigkeit und Duktilität im Vergleich zum Gießen oder Schmieden. |
Umweltfreundlich | Minimaler Abfall und kein Ausschuss, im Einklang mit nachhaltigen Praktiken. | Die Teilegröße ist auf ca. 40–50 Quadratzoll begrenzt. |
Entdecken Sie, wie die Pulvermetallurgie Ihren Fertigungsprozess verbessern kann – Kontaktieren Sie noch heute unsere Experten !