Wirbelschichtsysteme, insbesondere Wirbelschichtreaktoren (FBR) und Pyrolyseure, sind in Branchen wie der chemischen Verarbeitung, der Erdölraffination und der Biomasseumwandlung weit verbreitet.Diese Systeme bieten beträchtliche Vorteile, darunter eine gleichmäßige Temperaturverteilung, eine effiziente Wärmeübertragung und eine hohe Ausbeute an gewünschten Produkten wie Bioölen.Sie bringen jedoch auch Herausforderungen mit sich, wie z. B. die Notwendigkeit kleiner Partikelgrößen, hohe Betriebskosten und der Bedarf an großen Mengen von Inertgasen.Das Verständnis dieser Vor- und Nachteile ist für die Bewertung ihrer Eignung für bestimmte Anwendungen von entscheidender Bedeutung.
Die wichtigsten Punkte erklärt:
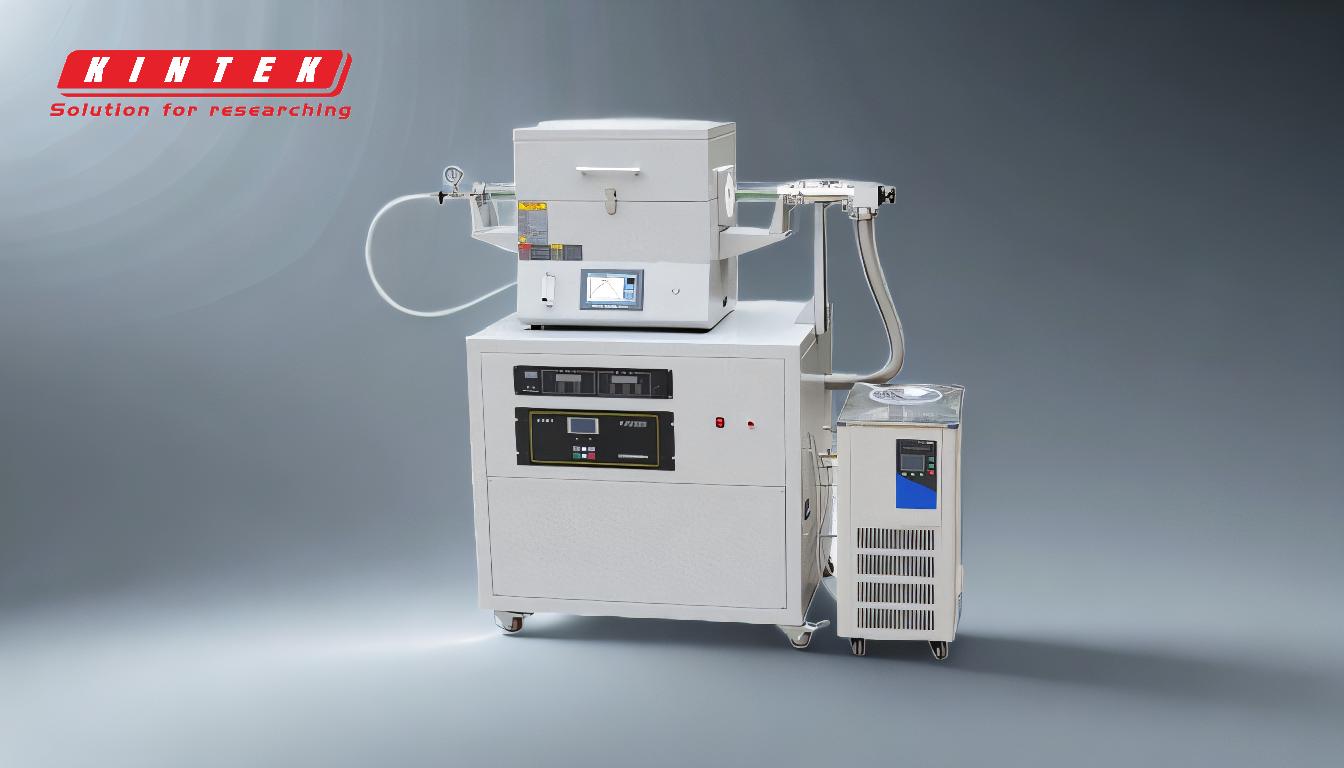
-
Vorteile von Wirbelschichtsystemen
-
Gleichmäßige Temperaturverteilung:
Wirbelschichtsysteme sorgen für ein gleichmäßiges Temperaturgefälle, das heiße oder kalte Stellen verhindert.Dies ist besonders bei exothermen Reaktionen von Vorteil, da es das Risiko eines thermischen Durchgehens minimiert und eine gleichbleibende Produktqualität gewährleistet. -
Effiziente Wärmeübertragung:
Das flüssigkeitsähnliche Verhalten der festen Partikel im Bett verbessert die Wärmeübertragung zwischen den Partikeln und dem umgebenden Gas.Dies führt zu einer schnelleren und effizienteren Erwärmung, was für Prozesse wie die Pyrolyse entscheidend ist. -
Hohe Ausbeute an erwünschten Produkten:
Mit Wirbelschichtpyrolyseuren beispielsweise lassen sich hohe Bioölerträge von bis zu 75 % erzielen.Damit sind sie äußerst effektiv bei der Umwandlung von Biomasse in wertvolle Nebenprodukte wie Bioöle und Gase. -
Gleichmäßige Partikelvermischung:
Der Fluidisierungsprozess sorgt für eine vollständige Durchmischung der Partikel und eliminiert radiale und axiale Konzentrationsgradienten.Dies verbessert die Reaktionseffizienz und die Produktkonsistenz. -
Mittlere Komplexität in Konstruktion und Betrieb:
Wirbelschichtsysteme sind zwar komplexer als einige Alternativen, aber im Vergleich zu anderen fortschrittlichen Reaktoren im Allgemeinen einfacher zu konstruieren und zu betreiben. -
Einfaches Skalieren:
Wirbelschichtsysteme lassen sich für industrielle Anwendungen relativ leicht vergrößern und eignen sich daher für die Produktion in großem Maßstab. -
Kontinuierlicher Betrieb:
Im Gegensatz zu Batch-Prozessen können Wirbelschichtreaktoren kontinuierlich betrieben werden, so dass häufige An- und Abfahrvorgänge nicht erforderlich sind.Dies verbessert die Produktionseffizienz und verringert die Ausfallzeiten.
-
Gleichmäßige Temperaturverteilung:
-
Nachteile von Wirbelschichtsystemen
-
Erfordernis kleiner Partikelgrößen:
Bei Wirbelschichtsystemen müssen die Einsatzstoffe fein gemahlen werden, um eine gute Fluidisierung zu erreichen.Dieser Vorverarbeitungsschritt kann die Betriebskomplexität und die Kosten erhöhen. -
Hohe Betriebskosten:
Der Bedarf an großen Mengen an Inertgasen (z. B. Stickstoff) zur Aufrechterhaltung des fluidisierten Zustands und zur Vermeidung unerwünschter Reaktionen kann die Betriebskosten erheblich erhöhen. -
Große Mengen von Inertgasen:
Die Verwendung von Inertgasen führt nicht nur zu höheren Kosten, sondern auch zu logistischen Herausforderungen, wie Lagerung und Handhabung. -
Erosion und Abnutzung:
Die ständige Bewegung der Partikel im Bett kann zu Erosion und Verschleiß der Reaktorkomponenten führen, was häufige Wartung und Austausch erfordert. -
Komplexität bei der Handhabung feiner Partikel:
Feine Partikel können schwierig zu handhaben sein und zu Problemen wie Verstopfung oder Materialverlust während der Verarbeitung führen. -
Eingeschränkte Anwendbarkeit für bestimmte Einsatzstoffe:
Wirbelschichtsysteme eignen sich zwar gut für partikelförmige Substrate wie holzige Biomasse, aber nicht für alle Arten von Rohstoffen, insbesondere für solche mit unregelmäßigen Formen oder hohem Feuchtigkeitsgehalt.
-
Erfordernis kleiner Partikelgrößen:
-
Anwendungen und Eignung
-
Umwandlung von Biomasse:
Wirbelschichtanlagen sind hocheffektiv bei der Umwandlung von Biomasse in Bioöle, Gase und andere wertvolle Nebenprodukte.Ihre Fähigkeit, partikelförmige Substrate zu verarbeiten, macht sie ideal für holzartige Biomasse und ähnliche Materialien. -
Chemie- und Erdölindustrie:
Diese Systeme werden häufig in der Chemie- und Erdölindustrie für Prozesse wie katalytisches Cracken und Vergasung eingesetzt, bei denen eine gleichmäßige Temperatur und eine effiziente Wärmeübertragung entscheidend sind. -
Exotherme Reaktionen:
Aufgrund der gleichmäßigen Temperaturgradienten in Wirbelschichtreaktoren eignen sie sich besonders für exotherme Reaktionen, bei denen die Kontrolle der Wärmeabgabe entscheidend ist.
-
Umwandlung von Biomasse:
-
Überlegungen für Einkäufer
-
Kosten-Nutzen-Analyse:
Die Käufer sollten die hohen Anschaffungs- und Betriebskosten gegen die Vorteile einer hohen Produktausbeute und eines effizienten Betriebs abwägen. -
Kompatibilität der Einsatzstoffe:
Es muss sichergestellt werden, dass das Einsatzmaterial mit dem Wirbelschichtsystem kompatibel ist, insbesondere im Hinblick auf die Partikelgröße und den Feuchtigkeitsgehalt. -
Anforderungen an die Wartung:
Das Erosions- und Verschleißpotenzial sollte in den Wartungsplänen und -budgets berücksichtigt werden. -
Skalierbarkeit:
Für die großtechnische Produktion ist die einfache Skalierbarkeit von Wirbelschichtsystemen ein wesentlicher Vorteil.
-
Kosten-Nutzen-Analyse:
Zusammenfassend lässt sich sagen, dass Wirbelschichtsysteme zahlreiche Vorteile bieten, darunter gleichmäßige Temperaturverteilung, effiziente Wärmeübertragung und hohe Produktausbeute.Ihre Nachteile, wie hohe Betriebskosten und der Bedarf an kleinen Partikelgrößen, müssen jedoch sorgfältig abgewogen werden.Durch die Bewertung dieser Faktoren können Käufer feststellen, ob Wirbelschichtsysteme die richtige Wahl für ihre spezifischen Anwendungen sind.
Zusammenfassende Tabelle:
Blickwinkel | Vorteile | Nachteile |
---|---|---|
Temperaturkontrolle | Gleichmäßige Temperaturverteilung, verhindert heiße/kalte Stellen | Erfordert kleine Partikelgrößen für eine gute Fluidisierung |
Wärmeübertragung | Effiziente Wärmeübertragung, schnellere Erwärmung für Prozesse wie Pyrolyse | Hohe Betriebskosten aufgrund von Inertgasanforderungen |
Produktausbeute | Hohe Ausbeute an gewünschten Produkten (z. B. Bioöle bis zu 75 %) | Große Mengen an Inertgasen erforderlich, was die logistischen Herausforderungen erhöht |
Partikelmischung | Vollständige Durchmischung, eliminiert Konzentrationsgefälle | Erosion und Verschleiß von Reaktorkomponenten durch ständige Partikelbewegung |
Skalierbarkeit | Einfache Skalierbarkeit für industrielle Anwendungen | Komplexe Handhabung von feinen Partikeln, Verstopfungsgefahr oder Materialverlust |
Betrieb | Kontinuierlicher Betrieb, reduzierte Ausfallzeiten und verbesserte Effizienz | Eingeschränkte Anwendbarkeit bei Rohstoffen mit unregelmäßigen Formen oder hohem Feuchtigkeitsgehalt |
Sind Sie bereit, Ihre industriellen Prozesse mit Wirbelschichtsystemen zu optimieren? Kontaktieren Sie noch heute unsere Experten für maßgeschneiderte Lösungen!