Das Schweißen von Edelstahl stellt aufgrund seiner einzigartigen Eigenschaften mehrere Herausforderungen dar, wie z. B. hohe Wärmeleitfähigkeit, Verformungsanfälligkeit und Empfindlichkeit gegenüber Verunreinigungen. Diese Herausforderungen erfordern eine sorgfältige Abwägung der Schweißtechniken, der Materialvorbereitung und der Nachbehandlungen nach dem Schweißen, um starke, korrosionsbeständige Verbindungen sicherzustellen. Zu den wichtigsten Themen gehören die Steuerung des Wärmeeintrags zur Verhinderung von Verformungen, die Vermeidung von Verunreinigungen durch Kohlenstoffstahl oder andere Verunreinigungen sowie die Auswahl geeigneter Zusatzmaterialien, die zur Zusammensetzung des Grundmetalls passen. Darüber hinaus kann die Neigung von rostfreiem Stahl, beim Schweißen Chromkarbide zu bilden, zu einer verringerten Korrosionsbeständigkeit führen, was eine ordnungsgemäße Wärmebehandlung oder die Verwendung kohlenstoffarmer Sorten erforderlich macht. Das Verständnis dieser Herausforderungen ist entscheidend für die Erzielung hochwertiger Schweißnähte bei Edelstahlanwendungen.
Wichtige Punkte erklärt:
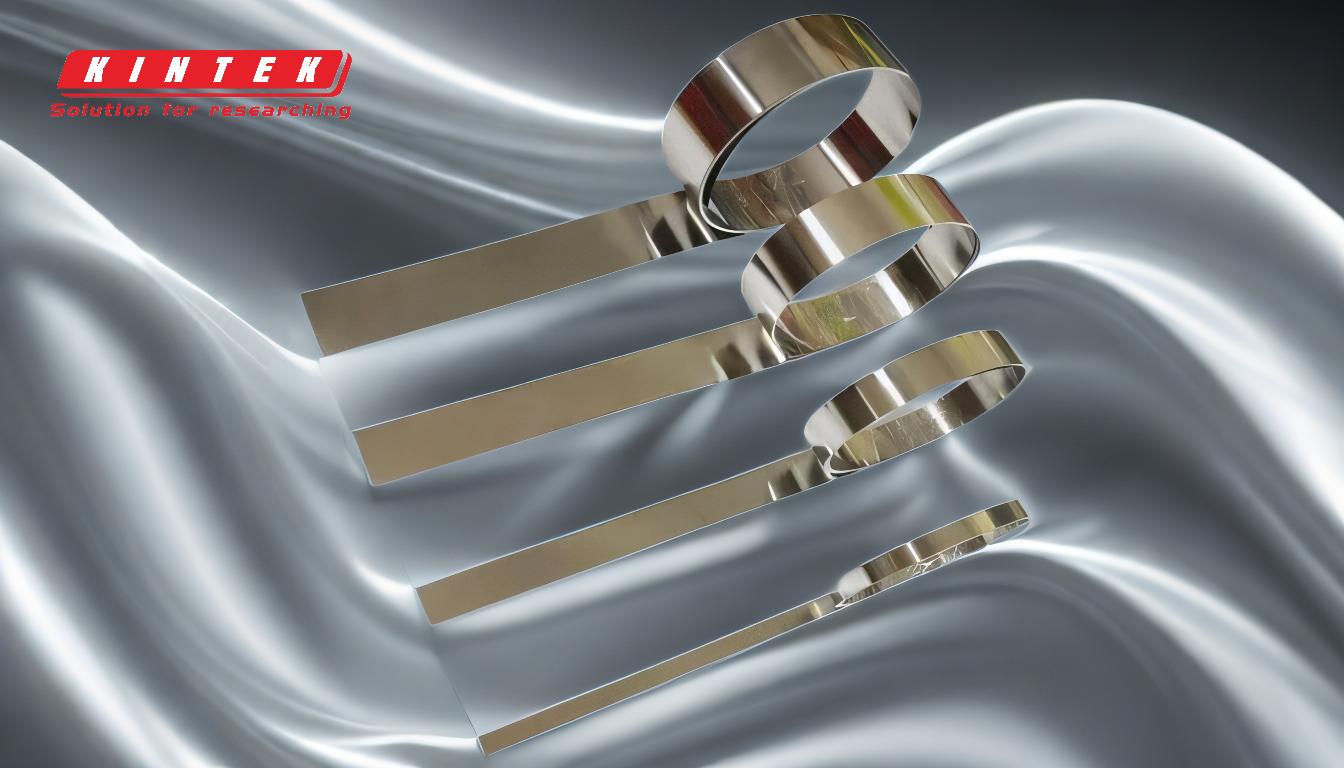
-
Hohe Wärmeleitfähigkeit und Wärmemanagement:
- Edelstahl hat im Vergleich zu Kohlenstoffstahl eine höhere Wärmeleitfähigkeit, was bedeutet, dass er die Wärme beim Schweißen schneller ableitet. Dies kann zu ungleichmäßiger Erwärmung und Abkühlung führen und das Risiko von Verformungen oder Verformungen erhöhen.
- Um dies zu mildern, ist eine präzise Steuerung der Wärmezufuhr unerlässlich. Techniken wie Impulsschweißen oder die Verwendung niedrigerer Stromstärkeneinstellungen können dabei helfen, die Wärmeverteilung zu steuern und Verformungen zu minimieren.
-
Anfälligkeit für Kontamination:
- Edelstahl reagiert sehr empfindlich auf Verunreinigungen durch Kohlenstoffstahl, Schmutz, Öle oder andere Verunreinigungen. Schon geringe Mengen an Verunreinigungen können zu Schweißfehlern wie Porosität oder Einschlüssen führen und die Korrosionsbeständigkeit des Materials beeinträchtigen.
- Die ordnungsgemäße Reinigung des Grundmetalls und der Schweißumgebung ist von entscheidender Bedeutung. Werkzeuge und Geräte, die für Kohlenstoffstahl verwendet werden, sollten nicht für Edelstahl verwendet werden, um Kreuzkontaminationen zu vermeiden.
-
Chromkarbidbildung und interkristalline Korrosion:
- Beim Schweißen kann Edelstahl an den Korngrenzen Chromkarbide bilden, wenn er Temperaturen zwischen 450 °C und 850 °C ausgesetzt wird. Dadurch verringert sich der Chromgehalt in den umliegenden Bereichen, was die Korrosionsbeständigkeit des Materials verringert.
- Um dies zu verhindern, werden häufig kohlenstoffarme Edelstahlsorten (z. B. 304L oder 316L) verwendet. Alternativ kann eine Wärmebehandlung nach dem Schweißen oder die Verwendung stabilisierender Elemente wie Titan oder Niob dazu beitragen, die Karbidbildung zu verringern.
-
Auswahl an Füllmaterialien:
- Die Wahl des richtigen Zusatzmaterials ist entscheidend, um die Zusammensetzung des Grundmetalls anzupassen und die mechanischen und korrosionsbeständigen Eigenschaften der Schweißnaht aufrechtzuerhalten. Nicht aufeinander abgestimmte Füllmaterialien können zu schwachen Verbindungen oder verminderter Leistung führen.
- Beispielsweise werden beim Schweißen von austenitischem Edelstahl typischerweise Füllmaterialien mit ähnlichem Nickel- und Chromgehalt verwendet, um die Kompatibilität sicherzustellen.
-
Verformung und Eigenspannungen:
- Der geringere Wärmeausdehnungskoeffizient von Edelstahl im Vergleich zu Kohlenstoffstahl kann nach dem Schweißen zu erheblichen Eigenspannungen und Verformungen führen. Dies ist insbesondere bei dünnen Abschnitten oder komplexen Geometrien problematisch.
- Techniken wie Backstep-Schweißen, Klemmen oder Vorwärmen können helfen, Verformungen zu kontrollieren. Darüber hinaus können bei kritischen Anwendungen stresslindernde Behandlungen erforderlich sein.
-
Oxidation und Verfärbung:
- Edelstahl neigt beim Schweißen zu Oxidation und Verfärbung, insbesondere in der Wärmeeinflusszone (HAZ). Dies beeinträchtigt nicht nur das Aussehen, sondern kann auch die Korrosionsbeständigkeit verringern.
- Durch die Verwendung inerter Schutzgase wie Argon oder Helium und die Gewährleistung einer ordnungsgemäßen Gasabdeckung kann die Oxidation minimiert werden. Durch eine Reinigung nach dem Schweißen mit Beizpaste oder Passivierungsbehandlungen können die Oberflächeneigenschaften des Materials wiederhergestellt werden.
-
Spezialisierte Schweißtechniken:
- Bestimmte Edelstahlsorten, wie Duplex- oder martensitische Edelstähle, erfordern aufgrund ihrer einzigartigen Mikrostrukturen und Eigenschaften spezielle Schweißtechniken.
- Duplex-Edelstähle erfordern beispielsweise eine präzise Wärmezufuhr, um eine ausgewogene Austenit-Ferrit-Mikrostruktur aufrechtzuerhalten, während martensitische Sorten möglicherweise ein Vorwärmen und eine Wärmebehandlung nach dem Schweißen erfordern, um Risse zu verhindern.
Durch die Bewältigung dieser Herausforderungen durch sorgfältige Planung, Materialauswahl und Schweißverfahren können hochwertige Schweißnähte aus Edelstahl erzielt werden, die Haltbarkeit und Leistung in anspruchsvollen Anwendungen gewährleisten.
Übersichtstabelle:
Herausforderung | Wichtige Überlegungen |
---|---|
Hohe Wärmeleitfähigkeit | Verwenden Sie Impulsschweißen oder eine niedrigere Stromstärke, um die Wärmezufuhr zu steuern und Verformungen zu minimieren. |
Anfälligkeit für Kontamination | Grundmetall gründlich reinigen; Vermeiden Sie Kreuzkontaminationen durch Werkzeuge aus Kohlenstoffstahl. |
Chromkarbidbildung | Verwenden Sie kohlenstoffarme Sorten (z. B. 304L, 316L) oder stabilisieren Sie sie mit Titan/Niob. |
Auswahl des Füllmaterials | Passen Sie das Füllmaterial für Kompatibilität und Leistung an die Zusammensetzung des Grundmetalls an. |
Verformung und Eigenspannungen | Verwenden Sie Backstep-Schweißen, Klemmen oder Vorwärmen, um Verformungen zu kontrollieren. |
Oxidation und Verfärbung | Verwenden Sie inerte Schutzgase und eine Reinigung nach dem Schweißen, um die Oberflächeneigenschaften wiederherzustellen. |
Spezialisierte Schweißtechniken | Wenden Sie bei Duplex-Sorten eine präzise Wärmezufuhr an; Vorwärmen und Nachschweißen martensitisch behandeln. |
Haben Sie Probleme beim Schweißen von Edelstahl? Kontaktieren Sie noch heute unsere Experten für maßgeschneiderte Lösungen!