Dünnschichttechnologien sind vielfältig und werden für eine breite Palette von Anwendungen in verschiedenen Branchen eingesetzt. Sie werden anhand ihrer Eigenschaften und der verwendeten Abscheidungsmethoden in verschiedene Kategorien eingeteilt. Zu den wichtigsten Arten von Dünnschichten gehören optische, elektrische/elektronische, magnetische, chemische, mechanische und thermische Schichten. Diese Schichten werden mit verschiedenen Abscheidungstechnologien hergestellt, z. B. durch physikalische Gasphasenabscheidung (PVD), chemische Gasphasenabscheidung (CVD) und Epitaxieverfahren. Zu den Materialien, die für die Abscheidung von Dünnschichten verwendet werden, gehören chemische Grundstoffe, elektrochemische Abscheidungsmaterialien, Aufdampfmaterialien und Sputtertargets. Jede Art von Dünnschicht und jede Abscheidungsmethode hat einzigartige Eigenschaften und Anwendungen, die sie für spezifische industrielle Bedürfnisse geeignet machen.
Die wichtigsten Punkte werden erklärt:
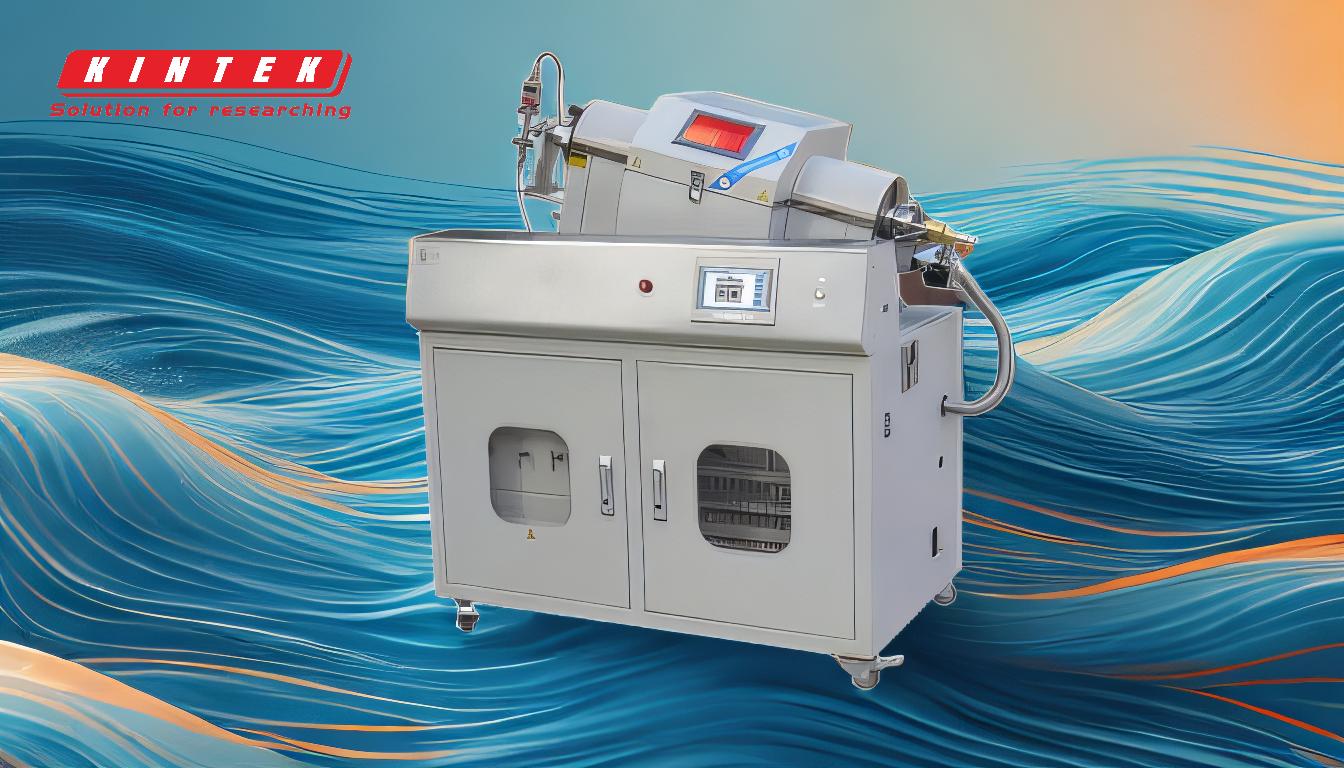
-
Arten von Dünnschichten auf der Grundlage ihrer Eigenschaften:
- Optische Schichten: Sie werden für reflektierende und antireflektierende Beschichtungen, Solarzellen, Monitore, Wellenleiter und optische Detektoranordnungen verwendet. Diese Schichten manipulieren das Licht, um die Reflexion zu verstärken oder zu verringern, den Wirkungsgrad von Solarzellen zu verbessern oder das Licht in optischen Geräten zu leiten.
- Elektrische/elektronische Schichten: Sie werden für Isolatoren, Leiter, Halbleiterbauelemente, integrierte Schaltungen und piezoelektrische Antriebe verwendet. Diese Folien sind in der Elektronikindustrie für die Herstellung von Komponenten, die Elektrizität leiten oder isolieren, unerlässlich.
- Magnetische Filme: Hauptsächlich für Speicherplatten verwendet. Diese Folien speichern Daten magnetisch und sind in der Datenspeichertechnologie von entscheidender Bedeutung.
- Chemische Schichten: Bieten Widerstand gegen Legierung, Diffusion, Korrosion und Oxidation. Sie werden auch in Gas- und Flüssigkeitssensoren verwendet. Diese Schichten schützen Oberflächen vor chemischem Abbau und werden in der Sensorik eingesetzt.
- Mechanische Schichten: Werden für tribologische Beschichtungen verwendet, um vor Abrieb zu schützen, die Härte und Haftung zu erhöhen und mikromechanische Eigenschaften zu nutzen. Diese Schichten verbessern die Haltbarkeit und Leistung mechanischer Komponenten.
- Thermische Schichten: Werden für Isolierschichten und Wärmesenken verwendet. Diese Folien steuern die Wärmeübertragung und sind daher für Wärmemanagementanwendungen unerlässlich.
-
Technologien zur Dünnschichtabscheidung:
- Physikalische Gasphasenabscheidung (PVD): Hierbei handelt es sich um physikalische Verfahren wie Sputtern und Verdampfen. Beim Sputtern werden Atome oder Moleküle von einem Zielmaterial abgeschlagen und auf einem Substrat abgelagert. Bei der Verdampfung werden die Materialien erhitzt, bis sie verdampfen und dann auf einem Substrat kondensieren.
- Chemische Gasphasenabscheidung (CVD): Die Abscheidung dünner Schichten erfolgt durch chemische Reaktionen. Vorläufergase reagieren auf der Substratoberfläche, um die gewünschte Schicht zu bilden. Diese Methode wird häufig für die Herstellung hochwertiger, gleichmäßiger Schichten verwendet.
- Epitaxie-Verfahren: Hierbei handelt es sich um das Wachstum eines kristallinen Films auf einem kristallinen Substrat. Diese Methode wird zur Herstellung von Schichten mit präzisen Kristallstrukturen verwendet, die für Halbleiteranwendungen unerlässlich sind.
-
Bei der Dünnschichtabscheidung verwendete Materialien:
- Chemische Grundstoffe: Lagerprodukte in flüssiger, fester oder gasförmiger Form, die sich chemisch verändern, um sich auf einem Substrat abzulagern. Sie werden bei der CVD und anderen chemischen Abscheidungsmethoden verwendet.
- Elektrochemische Abscheidungsmaterialien: Sie werden in einem elektrochemischen Nassverfahren auf einem Substrat abgeschieden. Diese Methode wird häufig für die Herstellung von Metallschichten verwendet.
- Aufdampfende Materialien: Drähte, Bleche oder feste Stoffe, die gekocht oder sublimiert werden, um Dämpfe zu erzeugen, die dann auf einem Substrat kondensieren. Dies ist eine gängige PVD-Technik.
- Sputtering-Targets: Werden bei Sputtering-Verfahren verwendet, bei denen Atome oder Moleküle des Zielmaterials abgeschlagen und auf ein Substrat aufgebracht werden. Diese Methode wird häufig bei der Herstellung von Dünnschichten für die Elektronik und Optik eingesetzt.
-
Anwendungen von Dünnschichttechnologien:
- Optische Anwendungen: Verbesserung der Leistung optischer Geräte, Verbesserung der Energieeffizienz von Solarzellen und Herstellung von Antireflexionsschichten für Linsen und Displays.
- Elektronische Anwendungen: Herstellung von Halbleiterbauelementen, integrierten Schaltkreisen und piezoelektrischen Komponenten. Diese Schichten sind entscheidend für die Miniaturisierung und Leistungsverbesserung elektronischer Geräte.
- Magnetische Anwendungen: Datenspeicherung in Speicherplatten und anderen magnetischen Speichergeräten. Diese Filme sind für die Speicherung digitaler Informationen mit hoher Dichte unerlässlich.
- Chemische Anwendungen: Schutz von Oberflächen vor Korrosion und Oxidation und Herstellung von Sensoren zum Nachweis von Gasen und Flüssigkeiten. Diese Folien sind in Branchen, in denen chemische Beständigkeit erforderlich ist, unverzichtbar.
- Mechanische Anwendungen: Verbesserung der Haltbarkeit und Leistung von mechanischen Komponenten durch tribologische Beschichtungen. Diese Schichten verringern den Verschleiß und verlängern die Lebensdauer mechanischer Teile.
- Thermische Anwendungen: Steuerung der Wärmeübertragung in elektronischen Geräten und anderen Anwendungen, die eine thermische Isolierung oder Wärmeableitung erfordern. Diese Schichten helfen bei der Aufrechterhaltung optimaler Betriebstemperaturen.
-
Industrie-spezifische Techniken:
- Magnetron-Sputtering: Ein spezielles PVD-Verfahren, das für die Abscheidung dünner Schichten mit hoher Präzision und Gleichmäßigkeit eingesetzt wird. Sie wird häufig bei der Herstellung von optischen und elektronischen Schichten eingesetzt.
- Molekularstrahlepitaxie (MBE): Ein Epitaxieverfahren, das für die Herstellung hochwertiger kristalliner Schichten verwendet wird. Diese Technik ist in der Halbleiterindustrie für die Herstellung präziser Schichten in elektronischen Geräten unerlässlich.
Wenn man die verschiedenen Arten von Dünnschichten, ihre Abscheidungsmethoden und die verwendeten Materialien kennt, kann man die geeignete Technologie für bestimmte Anwendungen auswählen und so eine optimale Leistung und Effizienz in verschiedenen Branchen gewährleisten.
Zusammenfassende Tabelle:
Kategorie | Arten von Dünnschichten | Abscheidungsmethoden | Wichtigste Anwendungen |
---|---|---|---|
Optisch | Reflektierend, antireflektierend | PVD, CVD | Solarzellen, Monitore, optische Geräte |
Elektrisch/Elektronisch | Leiter, Isolatoren | PVD, CVD, epitaktische Verfahren | Halbleiterbauelemente, integrierte Schaltungen, piezoelektrische Antriebe |
Magnetisch | Speicherplatten | PVD | Datenspeichertechnologien |
Chemisch | Korrosionsbeständige Beschichtungen | CVD, elektrochemisch | Gas-/Flüssigkeitssensoren, Oberflächenschutz |
Mechanisch | Tribologische Beschichtungen | PVD | Abrasionsschutz, Härteerhöhung |
Thermisch | Isolationsschichten, Wärmesenken | PVD, CVD | Wärmemanagement in der Elektronik und bei industriellen Anwendungen |
Benötigen Sie Hilfe bei der Auswahl der richtigen Dünnschichttechnologie für Ihre Anwendung? Kontaktieren Sie unsere Experten noch heute!