Die Wärmebehandlung ist ein wichtiges Verfahren zur Veränderung der physikalischen und manchmal auch chemischen Eigenschaften von Werkstoffen, vor allem von Metallen, um die gewünschten Eigenschaften wie höhere Festigkeit, Härte oder Duktilität zu erreichen.Das Verfahren umfasst in der Regel vier wichtige Schritte: Erhitzen des Materials auf eine bestimmte Temperatur, Halten auf dieser Temperatur für eine bestimmte Zeit, Abkühlen nach bestimmten Methoden und manchmal zusätzliche Schritte wie Anlassen oder Spannungsarmglühen zur Feinabstimmung der Materialeigenschaften.Diese Schritte sind wichtig, um sicherzustellen, dass das Material die erforderlichen Leistungsstandards für die vorgesehene Anwendung erfüllt.
Die wichtigsten Punkte werden erklärt:
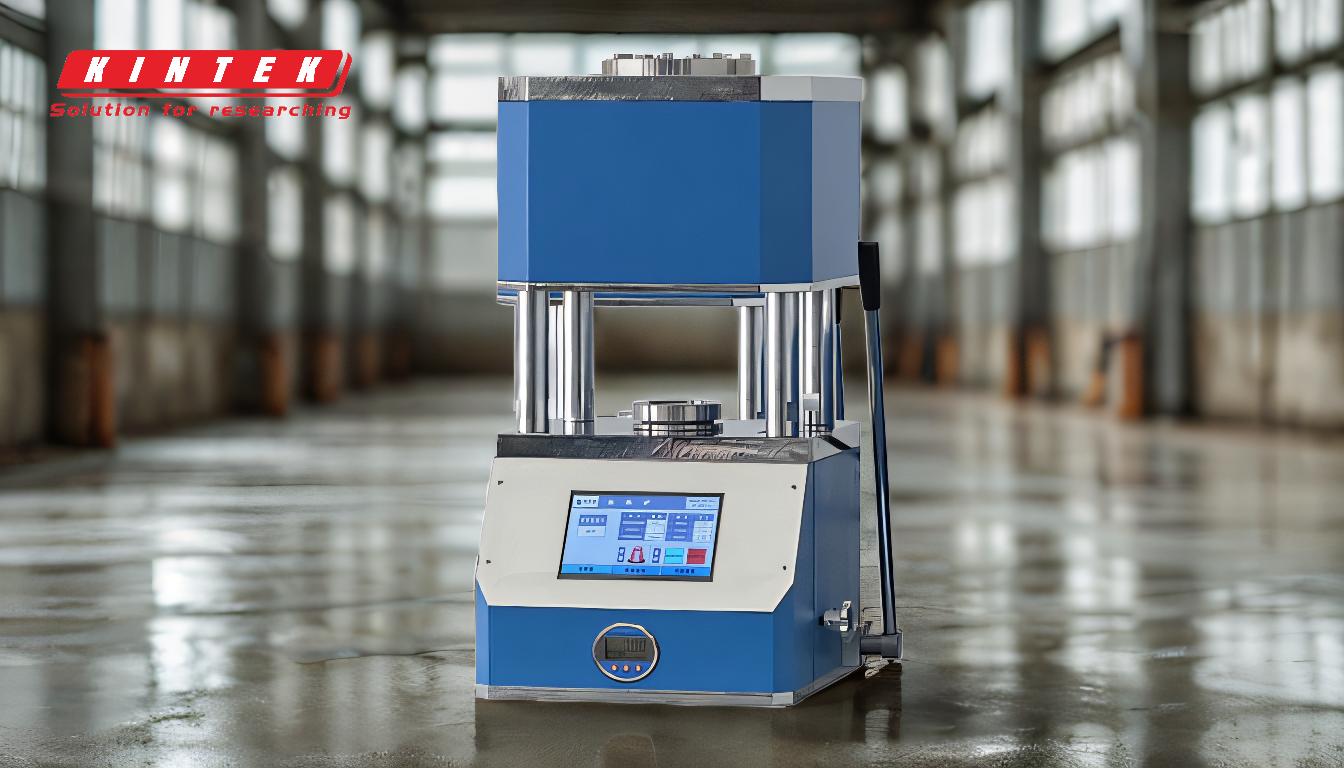
-
Erwärmung auf eine bestimmte Temperatur
- Der erste Schritt im Wärmebehandlungsprozess besteht darin, das Material auf eine bestimmte Temperatur zu erhitzen.Diese Temperatur variiert je nach Material und gewünschtem Ergebnis.Zum Beispiel erfordert das Glühen in der Regel niedrigere Temperaturen als das Härten.
- Die Erwärmung kann in verschiedenen Öfen erfolgen, wie z. B. in Elektro-, Gas- oder Induktionsöfen, je nach Material und Produktionsumfang.
- Der Temperaturbereich kann bei bestimmten Legierungen bis zu 1.315°C (2.400°F) betragen, um sicherzustellen, dass das Material die erforderliche Phasenumwandlung oder Rekristallisation erreicht.
-
Halten bei der angegebenen Temperatur
- Sobald das Material die gewünschte Temperatur erreicht hat, wird es für eine bestimmte Dauer bei dieser Temperatur gehalten.Dieser Schritt gewährleistet die Gleichmäßigkeit der Mikrostruktur des Materials und ermöglicht vollständige Umwandlungs- oder Diffusionsprozesse.
- Die Haltezeit kann von wenigen Sekunden für dünne Materialien bis zu mehreren Stunden oder sogar Tagen für dickere oder komplexere Bauteile reichen.
- Dieser Schritt ist entscheidend für die Erzielung gleichmäßiger Ergebnisse, da eine unzureichende Zeit zu unvollständigen Umwandlungen führen kann, während eine zu lange Zeit Kornwachstum oder andere unerwünschte Effekte verursachen kann.
-
Abkühlung nach vorgeschriebenen Methoden
- Nachdem das Material auf der vorgegebenen Temperatur gehalten wurde, wird es mit kontrollierten Methoden abgekühlt.Die Abkühlgeschwindigkeit ist entscheidend und hängt von den gewünschten Eigenschaften ab.Schnelles Abkühlen (Abschrecken) wird beispielsweise verwendet, um Metalle zu härten, während langsames Abkühlen zum Glühen verwendet wird, um sie weicher zu machen.
- Zu den Abkühlungsmethoden gehören Luftkühlung, Ölabschreckung, Wasserabschreckung oder Ofenabkühlung, die jeweils auf der Grundlage des Materials und des gewünschten Ergebnisses ausgewählt werden.
- Eine unsachgemäße Abkühlung kann zu Problemen wie Rissbildung, Verformung oder Eigenspannungen führen, weshalb dieser Schritt für den Erfolg des Wärmebehandlungsprozesses entscheidend ist.
-
Zusätzliche Schritte (optional)
- Je nach Anwendung können nach dem ersten Wärmebehandlungsprozess zusätzliche Schritte wie Anlassen, Spannungsarmglühen oder Oberflächenbehandlungen durchgeführt werden.
- Das Anlassen wird beispielsweise häufig nach dem Härten durchgeführt, um die Sprödigkeit zu verringern und die Zähigkeit zu verbessern, indem das Material auf eine niedrigere Temperatur erwärmt wird.
- Beim Spannungsarmglühen wird das Material auf eine Temperatur unterhalb seines Umwandlungsbereichs erwärmt, um innere Spannungen zu beseitigen, die durch Bearbeitung, Schweißen oder Umformen entstanden sind.
Diese vier Schritte bilden die Grundlage des Wärmebehandlungsprozesses und ermöglichen es den Herstellern, Werkstoffe so anzupassen, dass sie spezifische Leistungsanforderungen in Branchen wie der Luft- und Raumfahrt, der Automobilindustrie und dem Werkzeugbau erfüllen.Das Verständnis und die Kontrolle jedes einzelnen Schritts sind entscheidend für das Erreichen der gewünschten Materialeigenschaften und die Gewährleistung der Langlebigkeit und Zuverlässigkeit des Endprodukts.
Zusammenfassende Tabelle:
Schritt | Beschreibung | Wichtige Details |
---|---|---|
Heizung | Erhitzen des Materials auf eine bestimmte Temperatur. | - Die Temperatur variiert je nach Material und Verfahren (z. B. Glühen vs. Härten). |
- Heizmethoden: Elektro-, Gas- oder Induktionsöfen. | ||
- Die Temperaturen können bei bestimmten Legierungen bis zu 1.315°C (2.400°F) erreichen. | ||
Halten | Hält das Material für eine bestimmte Dauer auf der angegebenen Temperatur. | - Gewährleistet ein gleichmäßiges Mikrogefüge und eine vollständige Umwandlung. |
- Die Haltedauer reicht von Sekunden bis zu Tagen, je nach Materialstärke und Komplexität. | ||
Kühlung | Kühlen Sie das Material mit kontrollierten Methoden ab. | - Die Abkühlungsgeschwindigkeit wirkt sich auf die Materialeigenschaften aus (z. B. Abschrecken zum Härten, langsames Abkühlen zum Glühen). |
- Zu den Methoden gehören Luftkühlung, Ölabschreckung, Wasserabschreckung oder Ofenkühlung. | ||
Zusätzliche Schritte | Optionale Schritte wie Anlassen oder Spannungsarmglühen. | - Durch das Anlassen wird die Sprödigkeit verringert und die Zähigkeit verbessert. |
- Durch Spannungsarmglühen werden durch Bearbeitung oder Schweißen verursachte innere Spannungen beseitigt. |
Optimieren Sie Ihre Materialeigenschaften mit fachkundigen Wärmebehandlungslösungen. Kontaktieren Sie uns noch heute !