Das Sintern ist ein wichtiger Prozess in der Materialwissenschaft, insbesondere bei der Herstellung von Keramik und Metallen, bei dem pulverförmige Materialien erhitzt werden, um eine feste Masse zu bilden, ohne zu schmelzen. Die physikalischen Eigenschaften von gesinterten Werkstoffen werden durch verschiedene Faktoren wie Temperatur, Druck, Partikelgröße und die Zusammensetzung der Werkstoffe beeinflusst. Diese Faktoren wirken sich auf das Mikrogefüge, die Porosität und die mechanischen Eigenschaften des Endprodukts aus. Das Verständnis dieser Eigenschaften ist wichtig für die Optimierung des Sinterprozesses, um die gewünschten Materialeigenschaften zu erzielen.
Die wichtigsten Punkte werden erklärt:
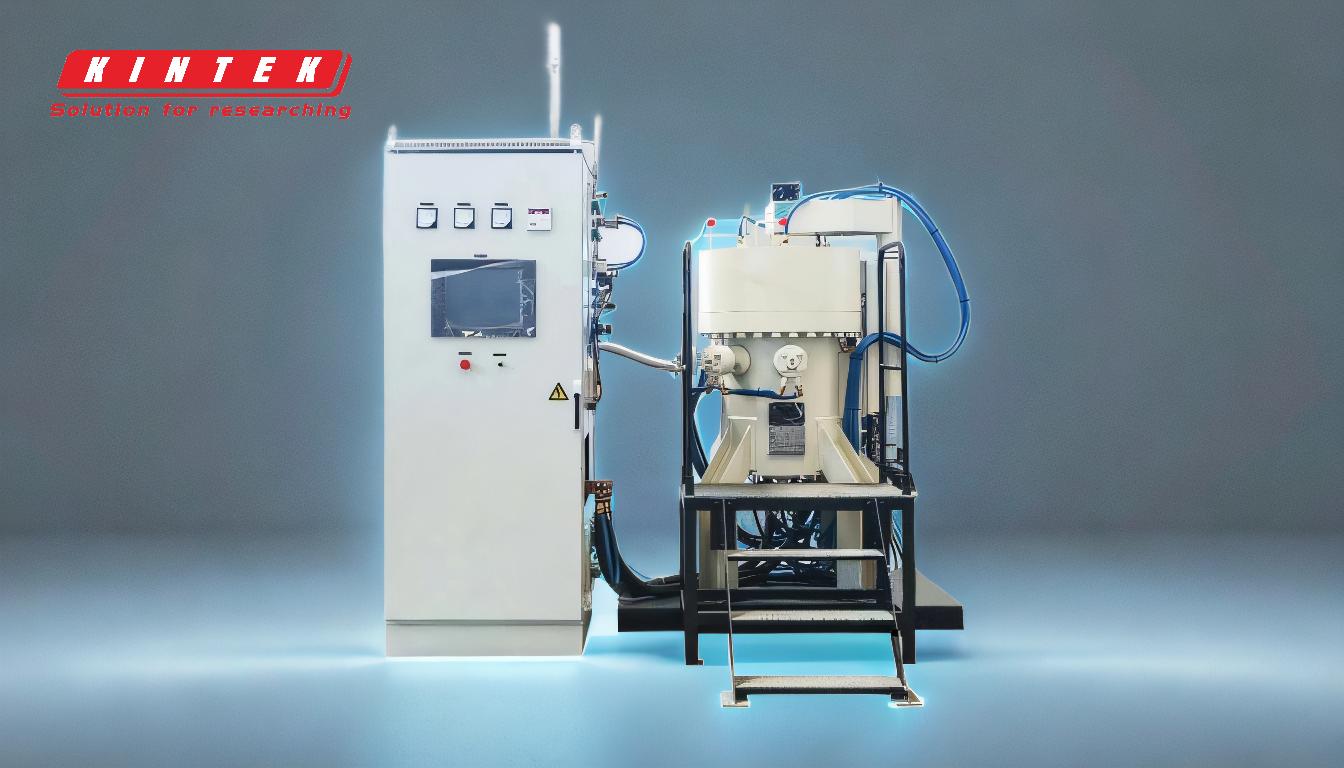
-
Mikrostruktur - Zusammensetzung:
- Das Mikrogefüge von gesinterten Werkstoffen umfasst in der Regel Phasen wie Hämatit, Magnetit und Kalziumferrit.
- Die Entwicklung dieser Phasen während des Sinterns wird von der Basizität der Sintermischung beeinflusst, was sich auf die Eigenschaften des Endprodukts auswirkt.
-
Einfluss der Sintervariablen:
- Atmosphäre: Die Sinteratmosphäre (Luft, Vakuum oder Inertgase wie Argon/Stickstoff) kann die Eigenschaften des gesinterten Materials erheblich beeinflussen.
- Temperatur: Höhere Sintertemperaturen erhöhen im Allgemeinen die Zugfestigkeit, die Biegewechselfestigkeit und die Kerbschlagarbeit.
- Abkühlungsrate: Die Geschwindigkeit, mit der das gesinterte Material abgekühlt wird, kann sich ebenfalls auf seine endgültigen Eigenschaften auswirken.
-
Verfahren und Parameter:
- Die verschiedenen Sintertechniken hängen von der Verwendung elektrischer Ströme, dem Druck, den Wärmequellen und den spezifischen Materialien ab, die gesintert werden.
- Parameter wie die Sintertemperatur, der angewandte Druck, die durchschnittliche Korngröße und die Gasatmosphäre sind entscheidend für die Optimierung des Sinterprozesses.
-
Porosität und Verdichtung:
- Die endgültige Porosität der gesinterten Keramik wird durch die anfängliche Porosität des Grünlings sowie durch die Temperatur und die Dauer des Sinterprozesses beeinflusst.
- Die Anwendung von Druck während des Sinterns kann die Porosität und die Sinterzeit verringern, insbesondere bei reinen Oxidkeramiken, die aufgrund der Diffusion von Feststoffpartikeln längere Sinterzeiten und höhere Temperaturen erfordern.
-
Prozesskontrolle:
- Während des Sinterprozesses werden Faktoren wie Luftmenge, Vakuum, Schichtdicke, Geschwindigkeit und Endpunkt des Sintervorgangs gesteuert.
- Beispielsweise beträgt das Luftvolumen typischerweise 3200 m³ pro Tonne Sintererz, und die Sinterfläche wird mit 70-90 m³/(cm²-min) berechnet.
-
Materialeigenschaften:
- Die mit der Partikelgröße verbundene Bindungsfläche ist entscheidend für die Bestimmung von Eigenschaften wie Festigkeit und Leitfähigkeit.
- Kontrollierbare Variablen wie Temperatur und Ausgangskorngröße spielen eine wichtige Rolle, da der Dampfdruck temperaturabhängig ist.
-
Kinetik der Sinterung:
- Die Temperatur bestimmt die Kinetik der Sinterung und die daraus resultierenden Materialeigenschaften.
- Die Erhitzungsrate beeinflusst die Verdichtung, wobei schnellere Erhitzungsraten zu einer besseren Verdichtung führen können.
-
Partikelgröße und -zusammensetzung:
- Kleinere Partikel und homogene Zusammensetzungen begünstigen eine bessere Verdichtung während des Sinterns.
- Auch die Zusammensetzung des Materials wirkt sich auf das Sinterverhalten aus, wobei unterschiedliche Materialien maßgeschneiderte Sinterbedingungen erfordern.
Das Verständnis dieser Schlüsselpunkte hilft bei der Entwicklung von Sinterprozessen, die Materialien mit den gewünschten physikalischen Eigenschaften hervorbringen und eine optimale Leistung in den vorgesehenen Anwendungen gewährleisten.
Zusammenfassende Tabelle:
Faktor | Auswirkung auf gesinterte Materialien |
---|---|
Temperatur | Höhere Temperaturen erhöhen die Zugfestigkeit, die Biegewechselfestigkeit und die Kerbschlagarbeit. |
Atmosphäre | Luft, Vakuum oder Inertgase (Argon/Stickstoff) beeinflussen die Materialeigenschaften. |
Abkühlungsrate | Beeinflusst die endgültigen Eigenschaften; kontrollierte Abkühlung gewährleistet die gewünschte Mikrostruktur. |
Partikelgröße | Kleinere Partikel verbessern die Verdichtung und erhöhen die Materialfestigkeit. |
Zusammensetzung | Homogene Zusammensetzungen und maßgeschneiderte Bedingungen optimieren das Sinterverhalten. |
Druck | Reduziert die Porosität und die Sinterzeit, insbesondere bei Oxidkeramik. |
Aufheizrate | Schnellere Heizraten können zu einer besseren Verdichtung führen. |
Optimieren Sie Ihren Sinterprozess mit fachkundiger Beratung - Kontaktieren Sie uns noch heute !