Kalzinieren und Sintern sind beides thermische Verfahren, die in der Metallurgie und der Werkstoffkunde eingesetzt werden, aber unterschiedlichen Zwecken dienen. Beim Kalzinieren werden in erster Linie Metallerze oder andere Materialien auf hohe Temperaturen erhitzt, um flüchtige Bestandteile wie Wasser, Kohlendioxid oder andere Verunreinigungen zu entfernen, ohne das Material zu schmelzen. Dieses Verfahren wird häufig zur Zersetzung von Karbonaten, Hydroxiden oder anderen Verbindungen in Oxide eingesetzt. Beim Sintern hingegen werden pulverförmige Metall- oder Keramikmaterialien auf eine Temperatur unterhalb ihres Schmelzpunkts erhitzt, um die Partikel miteinander zu verbinden, so dass eine feste Masse mit verbesserten mechanischen Eigenschaften entsteht. Bei beiden Verfahren wird zwar erhitzt, aber beim Kalzinieren liegt der Schwerpunkt auf der Reinigung, während beim Sintern die Verfestigung und Verfestigung im Vordergrund steht.
Die wichtigsten Punkte werden erklärt:
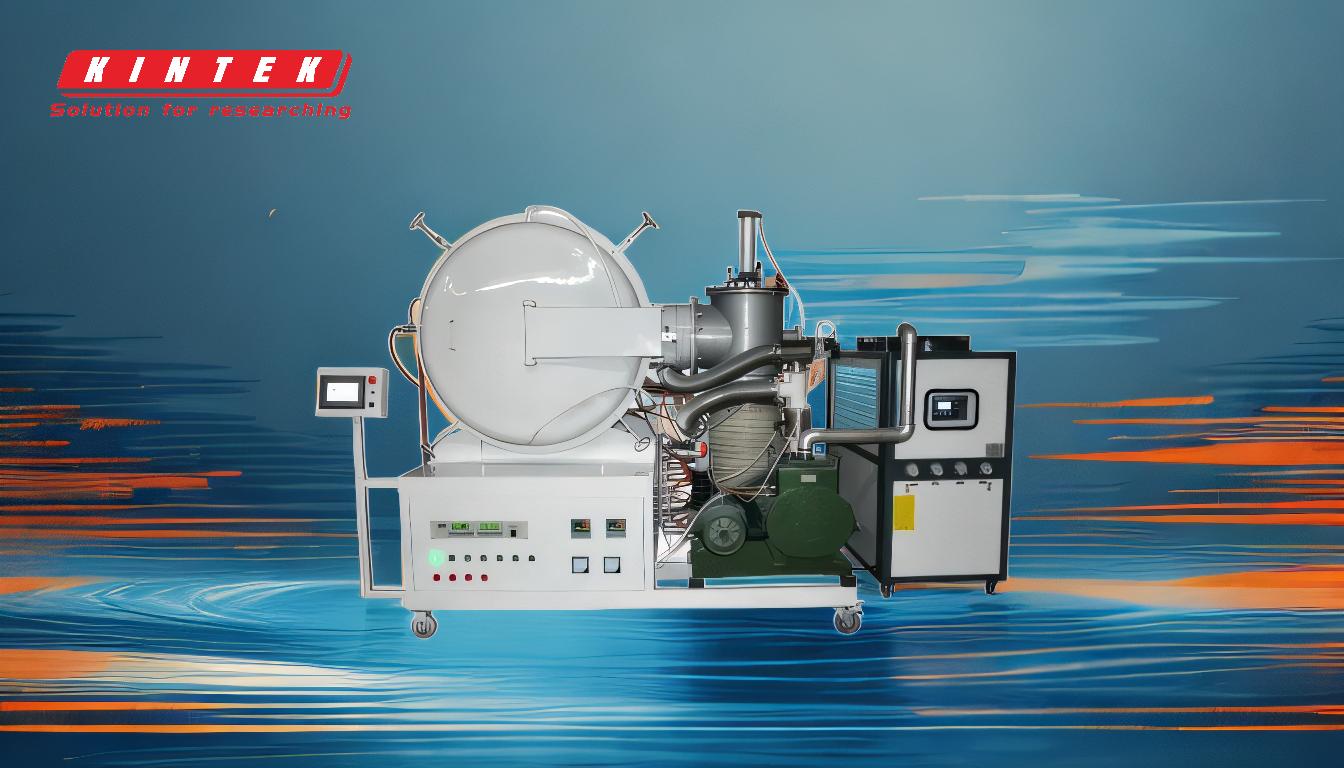
-
Definition und Zweck:
- Kalzinierung: Ein thermisches Verfahren, bei dem Materialien, in der Regel Metallerze, auf hohe Temperaturen erhitzt werden, um flüchtige Stoffe wie Wasser, Kohlendioxid oder Verunreinigungen zu entfernen. Das Ziel ist die Zersetzung von Verbindungen (z. B. Karbonate in Oxide) und die Reinigung des Materials.
- Sintern: Ein Verfahren, bei dem pulverförmige Materialien wie Metalle oder Keramiken auf eine Temperatur unterhalb ihres Schmelzpunkts erhitzt werden, um die Partikel miteinander zu verbinden. Ziel ist es, eine feste, zusammenhängende Struktur mit verbesserten mechanischen Eigenschaften zu schaffen.
-
Temperaturbereich:
- Kalzinierung: Dies geschieht in der Regel bei Temperaturen, die hoch genug sind, um Verbindungen zu zersetzen, aber unter dem Schmelzpunkt des Materials liegen. Kalziumkarbonat zersetzt sich beispielsweise bei etwa 825 °C in Kalziumoxid.
- Sintern: Findet bei Temperaturen statt, die unter dem Schmelzpunkt des Materials liegen, aber hoch genug sind, um eine Partikelbindung durch Diffusion zu ermöglichen. Die genaue Temperatur hängt vom Material ab, ist aber im Allgemeinen niedriger als die Kalzinierungstemperatur.
-
Chemische vs. physikalische Veränderungen:
- Kalzinierung: In erster Linie handelt es sich um chemische Veränderungen, wie die Zersetzung von Karbonaten oder Hydroxiden in Oxide, wobei Gase wie CO₂ oder H₂O freigesetzt werden.
- Sintern: In erster Linie handelt es sich um physikalische Veränderungen, wie z. B. die Bindung von Partikeln durch Diffusion, die zu einer Verdichtung und verbesserten mechanischen Festigkeit führt.
-
Anwendungen:
- Kalzinierung: Sie werden in der Zementindustrie (zur Herstellung von Kalk aus Kalkstein), in der Metallraffination (zur Entfernung von Verunreinigungen aus Erzen) und in der Katalysatoraufbereitung (zur Aktivierung von Materialien durch Entfernung flüchtiger Bestandteile) eingesetzt.
- Sintern: Weit verbreitet in der Pulvermetallurgie zur Herstellung von Metallteilen, in der Keramikherstellung zur Herstellung fester, dichter Komponenten und in der additiven Fertigung (3D-Druck) zur Verschmelzung von pulverförmigen Materialien.
-
Ergebnis:
- Kalzinierung: Ergibt ein gereinigtes Material, oft in Form eines Oxids, mit reduzierter Masse aufgrund der Entfernung flüchtiger Bestandteile.
- Sintern: Das Ergebnis ist ein dichteres, festeres Material mit verbesserten mechanischen Eigenschaften wie Härte, Festigkeit und Verschleißfestigkeit.
-
Materieller Zustand:
- Kalzinierung: Beginnt in der Regel mit einem festen Material (z. B. einem Erz oder einer Verbindung) und endet mit einem festen Produkt nach der Entfernung von Verunreinigungen.
- Sintern: Beginnt mit pulverförmigen Materialien und endet mit einer festen, kohäsiven Struktur nach der Partikelbindung.
-
Industrielle Bedeutung:
- Kalzinierung: Entscheidend für die Herstellung hochreiner Materialien, die in verschiedenen industriellen Prozessen benötigt werden, z. B. in der Stahlerzeugung, der Glasherstellung und der chemischen Produktion.
- Sintern: Unverzichtbar für die Herstellung von Bauteilen mit präzisen Formen und Eigenschaften, wie z. B. Zahnräder, Lager und Schneidwerkzeuge, insbesondere in der Automobil-, Luft- und Raumfahrt- sowie der Elektronikindustrie.
Zusammenfassend lässt sich sagen, dass sowohl beim Kalzinieren als auch beim Sintern Materialien auf hohe Temperaturen erhitzt werden, dass sie sich jedoch in ihren Zielen, Mechanismen und Ergebnissen unterscheiden. Das Kalzinieren ist ein Reinigungsverfahren, das auf die Entfernung von Verunreinigungen und die Zersetzung von Verbindungen abzielt, während das Sintern ein Verfestigungsverfahren ist, das darauf abzielt, Partikel zu binden, um feste, dichte Materialien zu schaffen. Das Verständnis dieser Unterschiede ist entscheidend für die Auswahl des geeigneten Verfahrens für bestimmte industrielle Anwendungen.
Zusammenfassende Tabelle:
Aspekt | Kalzinierung | Sintern |
---|---|---|
Zweck | Reinigung durch Entfernung flüchtiger Bestandteile (z. B. Wasser, CO₂) | Verfestigung und Verstärkung durch bindende Partikel |
Temperaturbereich | Hoch genug, um Verbindungen zu zersetzen (z. B. 825 °C für CaCO₃) | Unterhalb des Schmelzpunkts, um eine Partikelbindung zu ermöglichen |
Änderungen | Chemisch (Zersetzung von Verbindungen) | Physikalisch (Partikelbindung und Verdichtung) |
Anwendungen | Zementherstellung, Metallraffination, Katalysatorherstellung | Pulvermetallurgie, Keramikherstellung, additive Fertigung (3D-Druck) |
Ergebnis | Gereinigtes Material (z. B. Oxide) mit reduzierter Masse | Dichteres, stärkeres Material mit verbesserten mechanischen Eigenschaften |
Materieller Zustand | Beginnt und endet als solide | Beginnt als Pulver, endet als feste kohäsive Struktur |
Industrielle Nutzung | Stahlerzeugung, Glasherstellung, chemische Produktion | Automobilindustrie, Luft- und Raumfahrt, Elektronikindustrie |
Benötigen Sie Hilfe bei der Auswahl des richtigen thermischen Verfahrens für Ihre Anwendung? Kontaktieren Sie unsere Experten noch heute!