Das Sintern in Keramik ist ein kritischer Prozess, der pulverförmige Materialien durch die Anwendung von Wärme, typischerweise unterhalb des Schmelzpunkts des Primärmaterials, in eine feste, zusammenhängende Struktur umwandelt. Dieser Prozess umfasst mehrere Schritte, einschließlich Pulvervorbereitung, Formung und kontrolliertes Erhitzen in einem Sinterofen , was die Partikelbindung und -verdichtung erleichtert. Das Ergebnis ist ein langlebiges Keramikprodukt mit geringer Porosität und verbesserten mechanischen und thermischen Eigenschaften. Das Verständnis des Sinterprozesses ist für die Optimierung der Keramikproduktion und das Erreichen gewünschter Materialeigenschaften von entscheidender Bedeutung.
Wichtige Punkte erklärt:
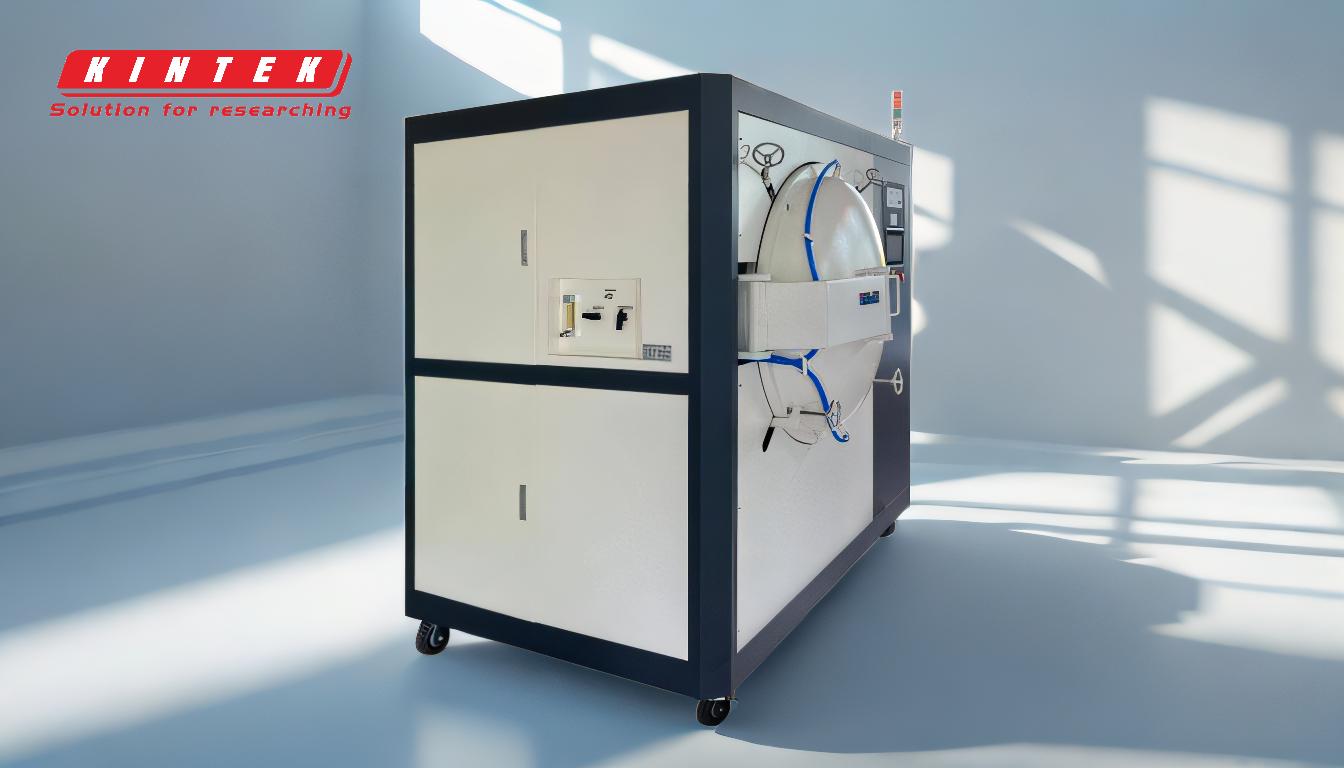
-
Definition und Zweck des Sinterns in Keramik:
- Sintern ist ein thermischer Behandlungsprozess, bei dem Keramikpartikel zu einer festen Struktur verbunden werden, ohne dass das Primärmaterial schmilzt.
- Das Hauptziel besteht darin, die Porosität zu verringern, die Dichte zu erhöhen und die mechanische Festigkeit und thermische Stabilität des Keramikprodukts zu verbessern.
-
Phasen des Sinterprozesses:
- Pulverzubereitung: Keramische Rohmaterialien werden zu feinen Pulvern gemahlen und mit Zusatzstoffen wie Bindemitteln oder Haftvermittlern vermischt, um die Handhabung und Formgebung zu verbessern.
- Gestaltung: Das Pulver wird durch Techniken wie Pressen oder Formen in die gewünschte Form verdichtet und bildet einen „Grünkörper“.
- Bindemittelentfernung: Der Grünkörper wird auf eine niedrige Temperatur erhitzt, um das Bindemittel auszubrennen oder zu verdampfen, wodurch eine poröse Struktur zurückbleibt.
- Hochtemperatursintern: Das Material wird in einem erhitzt Sinterofen auf eine Temperatur unterhalb seines Schmelzpunkts, wodurch sich die Partikel durch Diffusion und Halsbildung verbinden können.
- Kühlung: Das gesinterte Produkt wird allmählich abgekühlt, um zu einer starren, zusammenhängenden Struktur zu erstarren.
-
Rolle des Sinterofens:
- A Sinterofen Bietet kontrollierte Heiz- und Kühlumgebungen, die für den Sinterprozess unerlässlich sind.
- Es sorgt für eine gleichmäßige Temperaturverteilung und verhindert Defekte wie Verformungen oder Risse.
- Fortschrittliche Öfen ermöglichen eine präzise Steuerung der Heizraten, Verweilzeiten und Abkühlraten, die für die Erzielung optimaler Materialeigenschaften entscheidend sind.
-
Mechanismen des Sinterns:
- Diffusion: Atome bewegen sich über Partikeloberflächen, was zur Bildung von Hälsen und zur Partikelbindung führt.
- Kornwachstum: Partikel verschmelzen, wodurch die Porosität verringert und die Dichte erhöht wird.
- Flüssigphasensintern: In einigen Fällen bildet sich eine kleine Menge flüssiger Phase, die die Neuordnung und Bindung der Partikel unterstützt.
-
Einflussfaktoren auf das Sintern:
- Temperatur: Höhere Temperaturen beschleunigen die Diffusion und Bindung, müssen jedoch kontrolliert werden, um ein Schmelzen zu vermeiden.
- Zeit: Längere Sinterzeiten ermöglichen eine vollständigere Verdichtung, können jedoch zu übermäßigem Kornwachstum führen.
- Atmosphäre: Die Sinterumgebung (z. B. Luft, Vakuum oder Inertgas) kann Oxidation, Reduktion oder Kontamination beeinflussen.
- Partikelgröße und -form: Kleinere, gleichmäßige Partikel sintern aufgrund der größeren Oberfläche und Kontaktpunkte effizienter.
-
Anwendungen von Sinterkeramik:
- Gesinterte Keramik wird in Branchen wie der Elektronik (Isolatoren, Substrate), der Luft- und Raumfahrt (Wärmebarrieren), der Automobilindustrie (Bremsscheiben) und der Medizintechnik (Implantate, Prothetik) eingesetzt.
- Das Verfahren ermöglicht die Herstellung komplexer Formen mit hoher Präzision und Konsistenz.
-
Vorteile des Sinterns:
- Erzeugt Materialien mit hoher Festigkeit, Verschleißfestigkeit und thermischer Stabilität.
- Ermöglicht die Erstellung komplizierter Geometrien und endkonturnaher Komponenten.
- Reduziert den Materialabfall im Vergleich zu herkömmlichen Bearbeitungsprozessen.
-
Herausforderungen und Überlegungen:
- Kontrolle von Schrumpfung und Dimensionsänderungen während des Sinterns.
- Vermeidung von Mängeln wie Rissen, Hohlräumen oder Verwerfungen.
- Ausbalancieren der Sinterparameter, um die gewünschten Eigenschaften ohne übermäßigen Energieverbrauch zu erreichen.
Durch das Verständnis des Sinterprozesses und seiner wichtigsten Phasen können Hersteller die Keramikproduktion optimieren und so qualitativ hochwertige, langlebige Produkte gewährleisten, die auf spezifische Anwendungen zugeschnitten sind. Der Sinterofen spielt in diesem Prozess eine entscheidende Rolle und sorgt für die kontrollierte Umgebung, die für ein erfolgreiches Sintern erforderlich ist.
Übersichtstabelle:
Schlüsselaspekt | Einzelheiten |
---|---|
Zweck | Verbindet Keramikpartikel, verringert die Porosität und erhöht die Festigkeit. |
Stufen | Pulveraufbereitung, Formgebung, Entbinderung, Hochtemperatursintern, Abkühlen. |
Rolle des Sinterofens | Bietet kontrollierte Erwärmung/Kühlung für eine gleichmäßige Temperaturverteilung. |
Mechanismen | Diffusion, Kornwachstum und Flüssigphasensintern. |
Anwendungen | Elektronik-, Luft- und Raumfahrt-, Automobil- und Medizinindustrie. |
Vorteile | Hohe Festigkeit, Verschleißfestigkeit und thermische Stabilität. |
Optimieren Sie Ihre Keramikproduktion unter fachkundiger Anleitung – Kontaktieren Sie uns noch heute !