Das Sintern in einem Hochofen ist ein entscheidender Prozess in der Stahlproduktion, bei dem Eisenerzpulver, Flussmittel und recycelte Materialien in Sinter umgewandelt werden, ein dichtes und konsistentes Material, das für den Einsatz im Hochofen optimiert ist.Bei diesem Prozess wird das Gemisch unter seinen Schmelzpunkt erhitzt, um die Partikel zu verschmelzen und eine feste, poröse Struktur zu schaffen.Dieser Sinter verbessert die Effizienz des Hochofens, indem er die Permeabilität erhöht, den Verkokungsgrad verringert und einen reibungslosen Ofenbetrieb gewährleistet.Der Sinterprozess stärkt nicht nur das Material, sondern verringert auch die Porosität, was es ideal für die Eisenerzeugung macht.Es handelt sich um eine kostengünstige Methode zur Herstellung hochwertiger Werkstoffe mit den gewünschten mechanischen Eigenschaften.
Die wichtigsten Punkte werden erklärt:
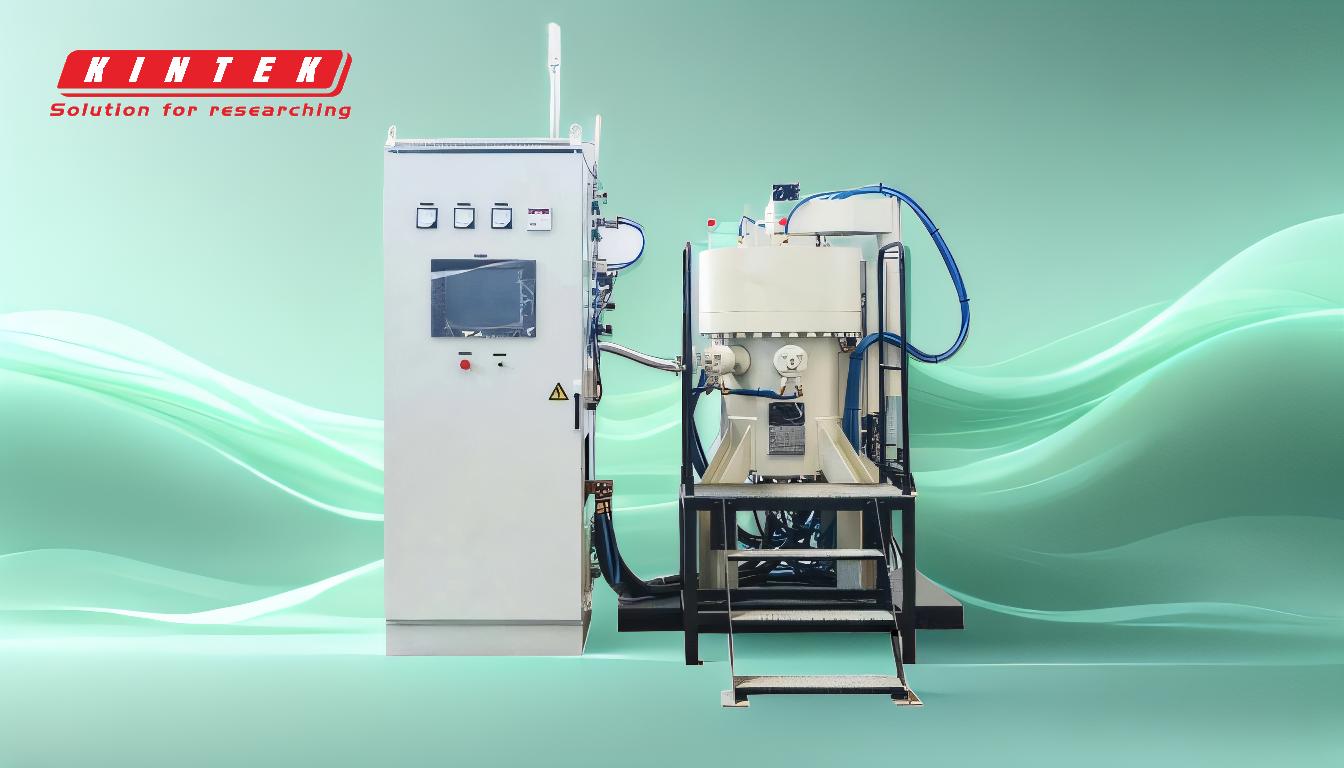
-
Definition und Zweck des Sinterns in Hochöfen:
- Beim Sintern werden pulverförmige Materialien wie Eisenerz in ein dichtes, konsistentes Produkt namens Sinter umgewandelt.
- Der Hauptzweck besteht darin, ein Material zu erzeugen, das die Leistung des Hochofens optimiert, indem es die Permeabilität verbessert, den Verkokungsgrad verringert und die Effizienz des Ofens erhöht.
-
Im Sinterprozess verwendete Materialien:
- Eisenerzpulver: Der Hauptrohstoff.
- Schmelzmittel:Materialien wie Kalkstein oder Dolomit, die zur Entfernung von Verunreinigungen beitragen.
- Recycelte Stoffe:Abfallstoffe aus Stahlwerken, wie Staub und Schlacke, werden wiederverwendet, um Abfall und Kosten zu reduzieren.
- Nicht-tabakhaltige Kohle:Wird als Brennstoffquelle zur Bereitstellung von Wärme für den Sinterprozess verwendet.
-
Stadien des Sinterprozesses:
- Mischen und Vermengen:Eisenerzpulver, Flussmittel und recycelte Materialien werden in bestimmten Verhältnissen gemischt, um die Gleichmäßigkeit zu gewährleisten.
- Bildung von Grünsinter:Die Mischung wird in die gewünschte Form gebracht, wobei häufig ein Bindemittel wie Wachs oder Polymer verwendet wird, um die Partikel zusammenzuhalten.
- Erhitzen und Brennen:Der grüne Sinter wird in einem Ofen bei Temperaturen unterhalb des Schmelzpunkts der Materialien erhitzt.Das Bindemittel verdampft oder verbrennt, und die Partikel beginnen an ihren Oberflächen zu verschmelzen.
- Abkühlung und Zerkleinerung:Nach dem Sintern wird das Material abgekühlt, zerkleinert und gesiebt, um den Staub zu entfernen und die gewünschte Körnung zu erreichen.
-
Die wichtigsten Vorteile des Sinterns in Hochöfen:
- Verbesserter Wirkungsgrad des Hochofens:Sinter verbessert die Durchlässigkeit des Hochofens und ermöglicht einen reibungsloseren Betrieb und einen besseren Gasfluss.
- Verringertes Verkokungsverhältnis:Sinter reduziert die im Hochofen benötigte Koksmenge und senkt so die Produktionskosten.
- Verbesserte Materialeigenschaften:Das Sintern verleiht Festigkeit, verringert die Porosität und verbessert die mechanischen Eigenschaften des Materials, wie z. B. die Härte und Zähigkeit.
- Kosten-Nutzen-Verhältnis:Die Verwendung recycelter Materialien und der geringere Energiebedarf machen das Sintern zu einem wirtschaftlichen Verfahren.
-
Anwendungen des Sinterns in der Metallurgie:
- Das Sintern wird häufig bei der Herstellung von Metallteilen wie Zahnrädern, Lagern, Buchsen und Automobilteilen eingesetzt.
- Es ermöglicht die Herstellung komplizierter Formen und Geometrien, die mit herkömmlichen Fertigungsmethoden nur schwer zu erreichen sind.
- Beim Sintern werden die Eigenschaften mehrerer Werkstoffe, wie Zähigkeit und Abriebfestigkeit, kombiniert, um Hochleistungsbauteile herzustellen.
-
Bedeutung des Sinterns in der Stahlproduktion:
- Das Sintern ist ein entscheidender Schritt im Stahlproduktionsprozess, da es die Herstellung von hochwertigem Sintererz mit ausreichender Festigkeit und Körnung gewährleistet.
- Es trägt zur Gesamteffizienz und Nachhaltigkeit der Stahlproduktion bei, indem es Abfälle reduziert und die Ressourcennutzung verbessert.
Durch das Verständnis des Sinterprozesses in Hochöfen können die Hersteller ihre Abläufe optimieren, die Kosten senken und hochwertige Werkstoffe herstellen, die den Anforderungen der modernen Stahlproduktion entsprechen.
Zusammenfassende Tabelle:
Aspekt | Einzelheiten |
---|---|
Definition | Verfahren zur Umwandlung von pulverförmigen Materialien in dichten, gleichmäßigen Sinter. |
Zweck | Verbessert den Wirkungsgrad des Hochofens, reduziert den Verkokungsgrad und verbessert den Betrieb. |
Verwendete Materialien | Eisenerzpulver, Flussmittel (Kalkstein/Dolomit), recycelte Stoffe, Kohle. |
Stadien | Mischen und Vermengen, Bildung von grünem Sinter, Erhitzen und Brennen, Kühlen und Zerkleinern. |
Wesentliche Vorteile | Erhöhte Permeabilität, reduzierter Verkokungsgrad, verbesserte Materialeigenschaften. |
Anwendungen | Zahnräder, Lager, Automobilteile und komplizierte Metallteile. |
Bedeutung | Entscheidend für hochwertige Sintererze, Kosteneffizienz und Nachhaltigkeit. |
Entdecken Sie, wie die Sinterung Ihre Stahlproduktion revolutionieren kann - Kontaktieren Sie unsere Experten noch heute !