Sputtern ist ein weit verbreitetes Verfahren zur Abscheidung von Dünnschichten, bei dem Atome aus einem festen Targetmaterial auf ein Substrat geschleudert werden, um eine dünne, gleichmäßige Schicht zu bilden.Dieser Prozess findet in einer Vakuumkammer statt, in der eine Hochspannung zwischen der Kammer und einer Targetelektrode aus dem gewünschten Schichtmaterial angelegt wird.Inerte Gase wie Argon werden eingeleitet, ionisiert und in Richtung des Targets beschleunigt, wodurch Atome ausgestoßen werden und sich auf dem Substrat ablagern.Das Sputtern bietet eine präzise Kontrolle über Schichtdicke, Gleichmäßigkeit und Dichte und eignet sich daher für Anwendungen in der Elektronik, Optik und Beschichtung.Variationen wie Magnetron-, Ionenstrahl- und reaktives Sputtern erhöhen die Vielseitigkeit des Verfahrens für spezifische Material- und Anwendungsanforderungen.
Die wichtigsten Punkte werden erklärt:
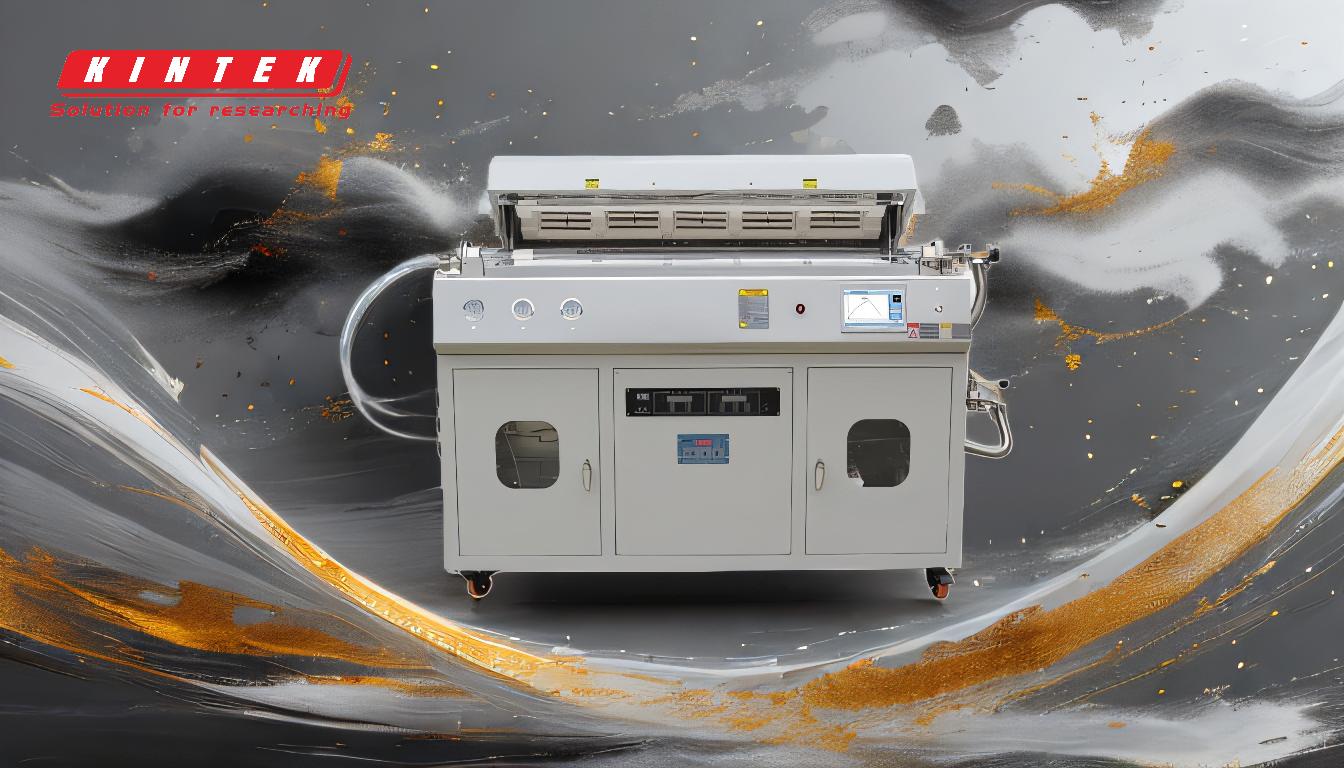
-
Grundprinzip des Sputterns:
- Beim Sputtern wird ein Zielmaterial (z. B. Metall oder Keramik) mit hochenergetischen Ionen beschossen, die in der Regel aus einem Inertgas wie Argon stammen.
- Die Ionen werden durch ein elektrisches Hochspannungsfeld beschleunigt, kollidieren mit dem Target und stoßen Atome von dessen Oberfläche ab.
- Diese ausgestoßenen Atome wandern durch die Vakuumkammer und lagern sich auf einem Substrat ab, wo sie eine dünne Schicht bilden.
-
Komponenten des Sputtering-Prozesses:
- Vakuumkammer:Bietet eine kontrollierte Umgebung zur Minimierung der Kontamination und zur Gewährleistung eines effizienten Ionenbeschusses.
- Ziel-Material:Die Quelle der abzuscheidenden Atome, die aus dem gewünschten Filmmaterial besteht.
- Substrat:Die Oberfläche, auf der die dünne Schicht abgeschieden wird.
- Inertes Gas (z. B. Argon):Ionisiert zur Erzeugung des Plasmas, das den Sputterprozess antreibt.
- Hochspannungs-Stromversorgung:Erzeugt das elektrische Feld, das notwendig ist, um die Ionen auf das Target zu beschleunigen.
-
Vorteile des Sputterns:
- Einheitliche Ablagerung:Das Sputtern erzeugt sehr gleichmäßige dünne Schichten, selbst auf großen oder komplexen Oberflächen.
- Präzise Kontrolle der Schichtdicke:Die Schichtdicke kann durch Anpassung der Abscheidungszeit und der Prozessparameter präzise gesteuert werden.
- Niedertemperatur-Beschichtung:Geeignet für temperaturempfindliche Substrate, da es im Vergleich zu anderen Abscheidungsmethoden bei niedrigeren Temperaturen arbeiten kann.
- Material Vielseitigkeit:Abscheidung einer breiten Palette von Materialien, einschließlich Metallen, Legierungen und Keramik.
-
Arten von Sputtering-Techniken:
- Magnetron-Sputtern:Nutzt Magnetfelder, um die Elektronen in der Nähe des Targets zu konzentrieren, wodurch die Ionisierungseffizienz und die Abscheidungsraten erhöht werden.
- Ionenstrahl-Sputtern:Ein fokussierter Ionenstrahl wird zum Sputtern des Targets eingesetzt und bietet hohe Präzision und Kontrolle für spezielle Anwendungen.
- Reaktives Sputtern:Einleiten reaktiver Gase (z. B. Sauerstoff oder Stickstoff) zur Bildung von Verbundschichten wie Oxiden oder Nitriden während der Abscheidung.
- Ionenunterstütztes Sputtern:Kombiniert Ionenbeschuss mit Sputtern zur Verbesserung der Schichthaftung und -dichte.
- Gasfluss-Sputtern:Nutzt einen Gasfluss, um den Transport der gesputterten Atome zum Substrat zu verbessern.
-
Anwendungen des Sputterns:
- Elektronik:Für die Abscheidung von leitenden und isolierenden Schichten in Halbleiterbauelementen, Solarzellen und Displays.
- Optik:Herstellung von Antireflexions-, Reflexions- und Schutzschichten für Linsen, Spiegel und optische Filter.
- Beschichtungen:Wird in verschleißfesten, dekorativen und funktionellen Beschichtungen für Automobilteile, Kochgeschirr und Werkzeuge verwendet.
- Historische Verwendung:Thomas Edison setzte 1904 das Sputtern ein, um Wachsplatten für die Massenvervielfältigung mit Metall zu beschichten.
-
Prozesskontrolle und -optimierung:
- Gasdruck und Durchflussmenge:Zur Optimierung der Ionendichte und Abscheidungsrate eingestellt.
- Stromversorgungsparameter:Gesteuert zur Regulierung der Ionenenergie und der Sputtereffizienz.
- Temperatur des Substrats:Beeinflusst Filmeigenschaften wie Spannung und Haftung.
- Ziel-zu-Substrat-Abstand:Optimiert, um eine gleichmäßige Ablagerung zu gewährleisten und Fehler zu minimieren.
-
Herausforderungen und Überlegungen:
- Eigenspannung:Kann in der abgeschiedenen Schicht auftreten und deren mechanische Eigenschaften beeinträchtigen.
- Verunreinigung:Erfordert eine hochwertige Vakuumumgebung, um Verunreinigungen zu vermeiden.
- Ziel Erosion:Das Targetmaterial erodiert mit der Zeit, so dass ein regelmäßiger Austausch oder eine Überholung erforderlich ist.
Wenn der Käufer einer Sputteranlage oder von Verbrauchsmaterialien diese Schlüsselaspekte kennt, kann er fundierte Entscheidungen über die spezifischen Techniken und Parameter treffen, die er für seine Anwendung benötigt, um optimale Leistung und Kosteneffizienz zu gewährleisten.
Zusammenfassende Tabelle:
Hauptaspekt | Einzelheiten |
---|---|
Grundprinzip | Beschuss eines Zielmaterials mit hochenergetischen Ionen, um Atome auszustoßen. |
Bestandteile | Vakuumkammer, Targetmaterial, Substrat, Inertgas, Hochspannungsversorgung. |
Vorteile | Gleichmäßige Abscheidung, präzise Dickenkontrolle, Betrieb bei niedrigen Temperaturen. |
Techniken | Magnetron-, Ionenstrahl-, reaktives, ionenunterstütztes und Gasfluss-Sputtern. |
Anwendungen | Elektronik, Optik, Beschichtungen und historische Anwendungen wie Phonoschallplatten. |
Herausforderungen | Eigenspannungen, Verunreinigungen und Zielerosion. |
Sind Sie bereit, Ihren Dünnschicht-Beschichtungsprozess zu optimieren? Kontaktieren Sie noch heute unsere Experten für maßgeschneiderte Sputtering-Lösungen!