Kalzinieren und Rösten sind pyrometallurgische Verfahren, die in der Metallurgie eingesetzt werden, um Metallerze zu behandeln und sie in besser verwertbare Formen umzuwandeln.Bei der Kalzinierung werden Karbonaterze unter Ausschluss oder bei begrenzter Luftzufuhr erhitzt, um flüchtige Verunreinigungen zu entfernen und das Erz in seine Oxidform zu zerlegen.Beim Rösten hingegen werden sulfidische Erze in Gegenwart von überschüssiger Luft erhitzt, um sie in Oxide oder andere Verbindungen umzuwandeln und dabei auch Verunreinigungen wie Schwefel zu entfernen.Beide Verfahren zielen darauf ab, das Erz zu reinigen und es für die weitere Reduktion oder Gewinnung des reinen Metalls vorzubereiten.
Die wichtigsten Punkte erklärt:
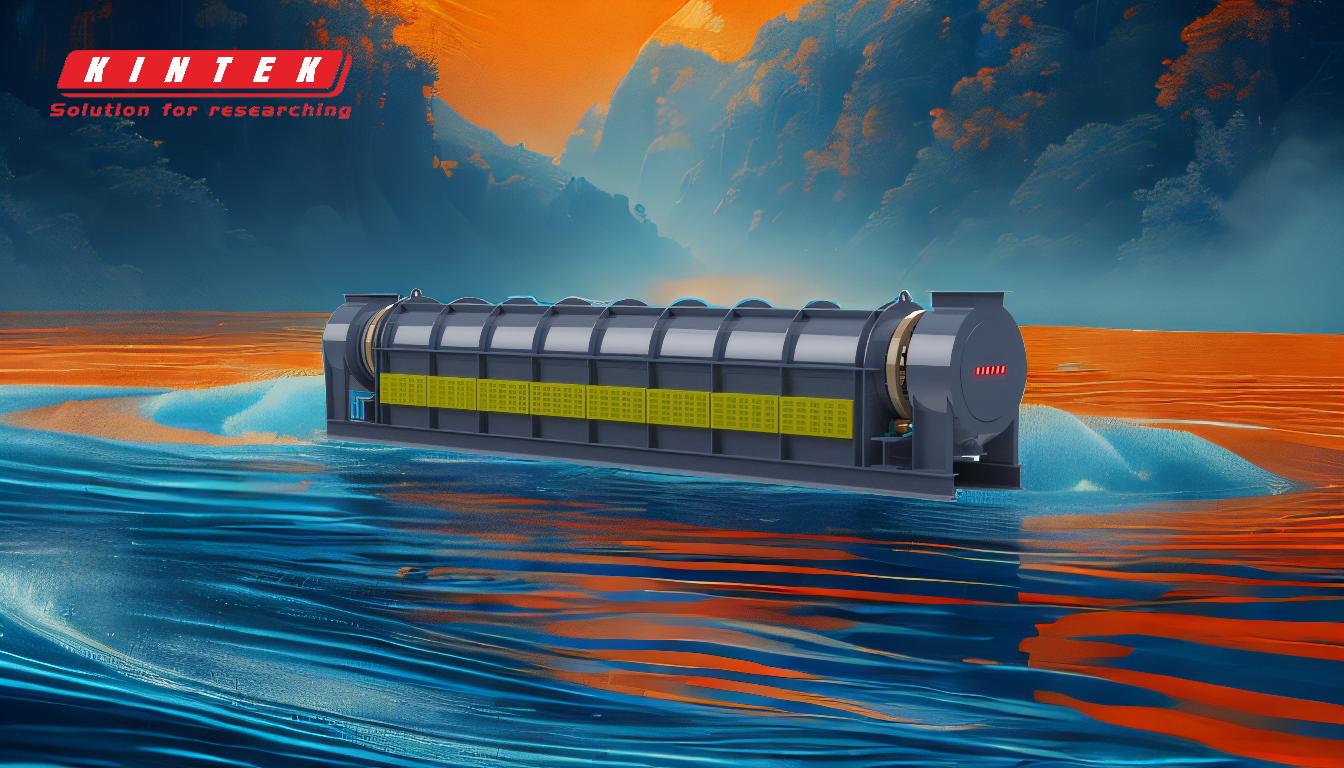
-
Definition und Zweck der Kalzinierung:
- Bei der Kalzinierung handelt es sich um ein thermisches Verfahren, bei dem Karbonaterze unter Abwesenheit oder begrenzter Zufuhr von Luft erhitzt werden.
- Das Hauptziel besteht darin, flüchtige Verunreinigungen wie Wasser, Kohlendioxid oder organische Stoffe zu entfernen.
- Dabei wird das Karbonaterz in seine Oxidform zersetzt, was die Gewinnung des reinen Metalls in den nachfolgenden Schritten erleichtert.
- Beispiel:Erhitzen von Kalkstein (CaCO₃) zur Erzeugung von Kalk (CaO) und Kohlendioxid (CO₂).
-
Definition und Zweck des Röstens:
- Das Rösten ist ein thermisches Behandlungsverfahren, bei dem sulfidische Erze in Gegenwart von Luft- oder Sauerstoffüberschuss erhitzt werden.
- Das Hauptziel besteht darin, Sulfiderze in Oxide oder andere Verbindungen umzuwandeln und dabei auch Schwefel in Form von Schwefeldioxid (SO₂) zu entfernen.
- Es hilft bei der Beseitigung von Verunreinigungen und der Vorbereitung des Erzes für die weitere Reduktion zur Gewinnung des Metalls.
- Beispiel:Rösten von Zinksulfid (ZnS) zur Herstellung von Zinkoxid (ZnO) und Schwefeldioxid (SO₂).
-
Hauptunterschiede zwischen Kalzinierung und Röstung:
- Luftversorgung:Die Kalzinierung erfolgt bei fehlender oder begrenzter Luftzufuhr, während das Rösten einen Überschuss an Luft oder Sauerstoff erfordert.
- Art der Erze:Die Kalzinierung wird vor allem bei Karbonaterzen angewandt, während das Rösten bei Sulfiderzen zum Einsatz kommt.
- Chemische Reaktionen:Beim Kalzinieren kommt es zu Zersetzungsreaktionen, während beim Rösten Oxidationsreaktionen ablaufen.
- Nebenprodukte:Beim Kalzinieren werden Gase wie CO₂ freigesetzt, während beim Rösten SO₂ entsteht.
-
Anwendungen in der Metallurgie:
- Beide Verfahren sind wichtige Schritte bei der Gewinnung von Metallen wie Eisen, Zink, Kupfer und Aluminium.
- Das Kalzinieren wird bei der Herstellung von Zement, Kalk und anderen industriellen Materialien eingesetzt.
- Das Rösten ist von entscheidender Bedeutung bei der Gewinnung von Metallen aus sulfidischen Erzen, z. B. bei der Herstellung von Zink, Blei und Kupfer.
-
Bedeutung bei der Reinigung und Metallgewinnung:
- Kalzinierung und Röstung tragen dazu bei, Verunreinigungen zu entfernen, was die Effizienz der nachfolgenden Reduktionsprozesse verbessert.
- Sie wandeln Erze in reaktivere Formen (Oxide) um, die sich mit Hilfe von Reduktionsmitteln wie Kohlenstoff oder Wasserstoff leichter zu reinen Metallen reduzieren lassen.
- Diese Verfahren gewährleisten die Herstellung von hochreinen Metallen, die für industrielle und kommerzielle Anwendungen unerlässlich sind.
Indem sie die Ziele und Mechanismen des Kalzinierens und Röstens verstehen, können die Käufer von Ausrüstungen und Verbrauchsmaterialien die geeigneten Materialien und Technologien für ihre metallurgischen Prozesse besser auswählen.
Zusammenfassende Tabelle:
Aspekt | Kalzinierung | Rösten |
---|---|---|
Luftzufuhr | Fehlende oder eingeschränkte Luftzufuhr | Überschuss an Luft oder Sauerstoff |
Art der Erze | Karbonaterze | Sulfidische Erze |
Chemische Reaktionen | Zersetzungsreaktionen | Oxidationsreaktionen |
Nebenprodukte | CO₂, Wasserdampf | SO₂ |
Anwendungen | Zement, Kalkherstellung | Gewinnung von Zink, Blei, Kupfer |
Entdecken Sie, wie Kalzinierung und Röstung Ihre metallurgischen Prozesse optimieren können. Kontaktieren Sie unsere Experten noch heute !