Hartlöten ist ein Metallverbindungsverfahren, bei dem ein Schweißzusatzwerkstoff mit einem Schmelzpunkt über 450 °C (840 °F) verwendet wird, um zwei oder mehr Grundwerkstoffe zu verbinden, ohne sie zu schmelzen.Es unterscheidet sich vom Löten, bei dem Zusatzwerkstoffe mit niedrigeren Schmelzpunkten verwendet werden, und vom Schweißen, bei dem die Grundwerkstoffe geschmolzen werden.Das Hartlöten bietet Vorteile wie eine präzise Kontrolle der Toleranzen, minimale Verformung und Verbindungen, die so fest sind wie die Grundwerkstoffe, wodurch es sich für hochpräzise Anwendungen eignet.Der Prozess beinhaltet eine Kapillarwirkung, um das Zusatzmetall zu verteilen, wodurch starke, dauerhafte Verbindungen entstehen.Das Verständnis der Unterschiede zwischen Hartlöten, Löten und Schweißen hilft bei der Auswahl der geeigneten Verbindungsmethode für bestimmte Anwendungen.
Die wichtigsten Punkte werden erklärt:
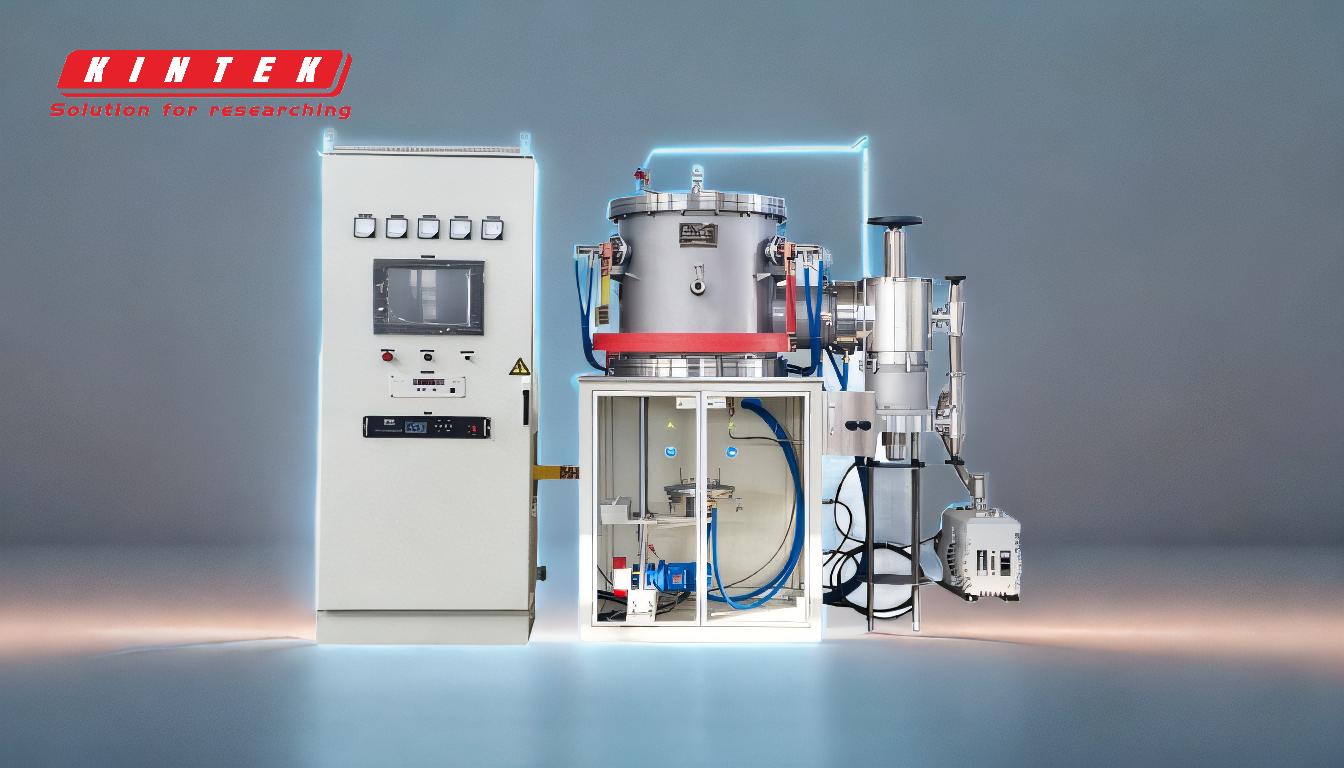
-
Definition und Temperaturbereich des Hartlötens:
- Das Hartlöten ist ein Verfahren zum Verbinden von Metallen, bei dem ein Lot mit einem Schmelzpunkt von über 450 °C verwendet wird.Damit unterscheidet es sich vom Löten, bei dem Zusatzwerkstoffe mit niedrigeren Schmelzpunkten verwendet werden.
- Beim Hartlöten hat das Lot einen niedrigeren Schmelzpunkt als die zu verbindenden Grundwerkstoffe, wodurch sichergestellt wird, dass die Grundwerkstoffe während des Prozesses nicht schmelzen.
-
Vergleich mit Löten:
- Beim Löten werden Zusatzwerkstoffe mit Schmelzpunkten unter 450°C (840°F) verwendet, wodurch es sich für Anwendungen eignet, die eine geringere Hitze erfordern.
- Sowohl das Hartlöten als auch das Weichlöten beruhen auf der Kapillarwirkung zur Verteilung des Zusatzwerkstoffs, aber beim Hartlöten entstehen aufgrund des höheren Schmelzpunkts und der stärkeren Zusatzwerkstoffe stabilere Verbindungen.
-
Vergleich mit Schweißen:
- Beim Schweißen werden die Grundwerkstoffe geschmolzen, oft mit einem Zusatzwerkstoff, um eine metallurgische Verbindung herzustellen.Dieses Verfahren erfordert einen hohen Energieaufwand und kann zu erheblichen wärmebeeinflussten Zonen führen.
- Beim Hartlöten hingegen werden die Grundwerkstoffe nicht geschmolzen, was eine genauere Kontrolle der Toleranzen und minimale Verformungen ermöglicht.
-
Vorteile des Hartlötens:
- Präzision und minimale Verzerrung:Da die Grundwerkstoffe nicht schmelzen, ermöglicht das Hartlöten eine präzise Kontrolle der Toleranzen und minimale Verformung, was es ideal für hochpräzise Anwendungen macht.
- Festigkeit der Verbindung:Hartgelötete Verbindungen sind so stark wie die unedlen Metalle und bieten dauerhafte und zuverlässige Verbindungen.
- Vielseitigkeit:Das Hartlöten kann unterschiedliche Metalle verbinden und eignet sich für eine Vielzahl von Anwendungen, einschließlich solcher, die hohe Festigkeit und Präzision erfordern.
-
Verfahren und Mechanismus:
- Beim Hartlöten werden die Grundwerkstoffe und der Zusatzwerkstoff auf eine Temperatur über dem Schmelzpunkt des Zusatzwerkstoffs, aber unter dem Schmelzpunkt der Grundwerkstoffe erhitzt.
- Das Zusatzmetall wird durch Kapillarwirkung in die Verbindung gezogen und bildet beim Abkühlen und Erstarren eine feste Verbindung.
- Dieses Verfahren kann mit verschiedenen Wärmequellen durchgeführt werden, darunter Brenner, Öfen und Induktionserwärmung.
-
Anwendungen des Hartlötens:
- Hartlöten wird in vielen Branchen eingesetzt, in denen starke, präzise und dauerhafte Verbindungen erforderlich sind, z. B. in der Luft- und Raumfahrt, im Automobilbau, in der Elektronik und in HLK-Systemen.
- Es ist besonders nützlich für die Verbindung unterschiedlicher Metalle und die Herstellung komplexer Baugruppen mit minimaler Verformung.
Wenn die Käufer von Geräten und Verbrauchsmaterialien diese wichtigen Punkte kennen, können sie fundierte Entscheidungen darüber treffen, wann und wie sie das Hartlöten einsetzen, um optimale Ergebnisse für ihre spezifischen Anwendungen zu gewährleisten.
Zusammenfassende Tabelle:
Aspekt | Einzelheiten |
---|---|
Temperaturbereich | Zusatzwerkstoff schmilzt über 450°C (840°F), Grundwerkstoffe bleiben fest. |
Vergleich mit Löten | Beim Löten werden niedrigere Schmelzpunkte (<450°C) verwendet, beim Hartlöten entstehen festere Verbindungen. |
Vergleich mit Schweißen | Beim Schweißen schmelzen die Grundwerkstoffe, beim Hartlöten wird das Schmelzen vermieden, um die Verformung zu minimieren. |
Vorteile | Präzise Toleranzen, minimaler Verzug, feste Verbindungen, vielseitig für unterschiedliche Metalle. |
Anwendungen | Luft- und Raumfahrt, Automobilindustrie, Elektronik, HVAC und mehr. |
Entdecken Sie, wie Hartlöten Ihre Projekte verbessern kann. Kontaktieren Sie unsere Experten noch heute für maßgeschneiderte Lösungen!