Thermisches Verdampfen und Magnetronsputtern sind zwei weit verbreitete Verfahren zur Abscheidung von Dünnschichten, die jeweils unterschiedliche Merkmale und Anwendungen aufweisen.Bei der thermischen Verdampfung wird ein Material im Vakuum erhitzt, bis es verdampft und eine dünne Schicht auf einem Substrat bildet.Dieses Verfahren bietet hohe Abscheideraten und eignet sich für Anwendungen wie OLEDs und Dünnschichttransistoren.Beim Magnetronsputtern hingegen werden mit Hilfe eines hochenergetischen Plasmas Atome aus einem Zielmaterial ausgestoßen und auf einem Substrat abgeschieden.Dieses Verfahren bietet eine bessere Schichthaftung, eine größere Gleichmäßigkeit und eine größere Vielfalt an Farboptionen, was es ideal für elektrische und optische Anwendungen macht.Die Wahl zwischen den beiden Verfahren hängt von Faktoren wie Abscheiderate, Folienqualität und spezifischen Anwendungsanforderungen ab.
Die wichtigsten Punkte werden erklärt:
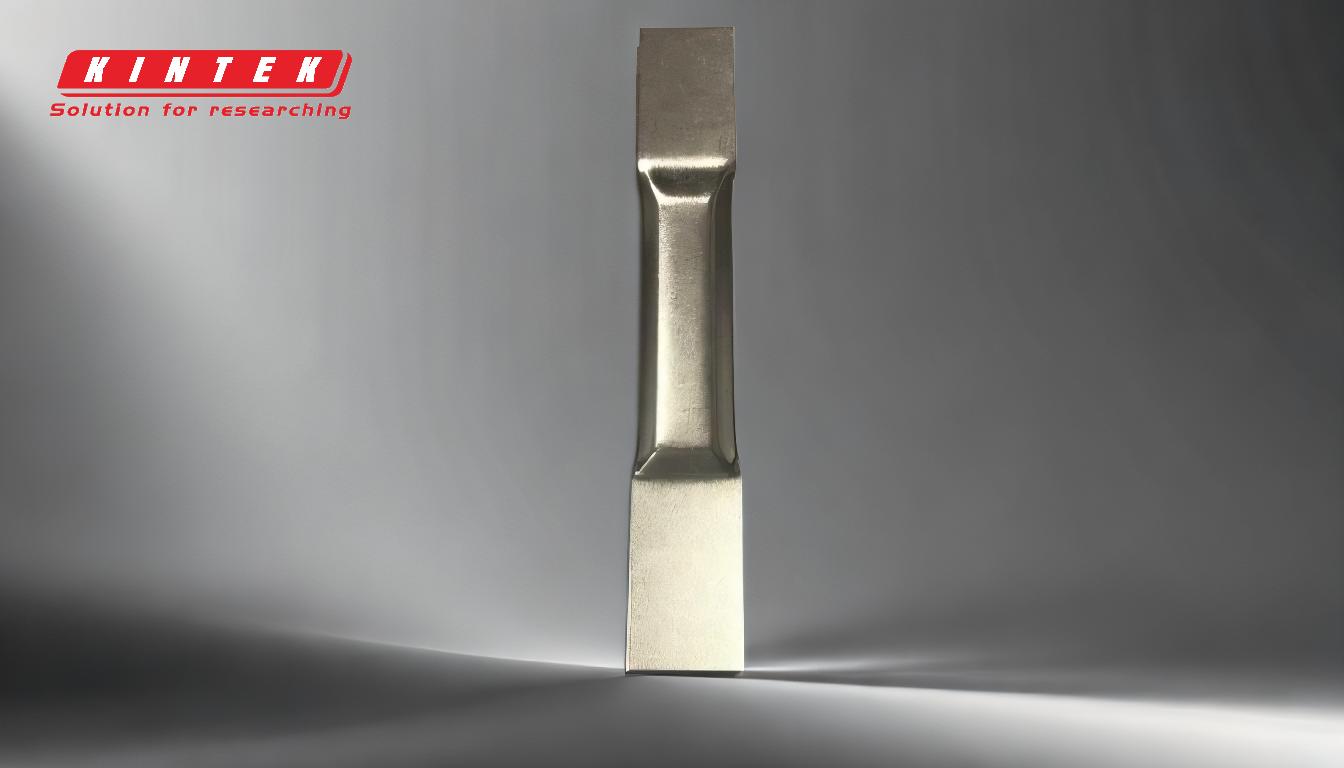
1. Mechanismus der Abscheidung
-
Thermische Verdampfung:
- Verwendet eine Widerstands-Wärmequelle zum Verdampfen eines festen Materials im Vakuum.
- Erzeugt einen robusten Dampfstrom, der höhere Abscheideraten ermöglicht.
- Geeignet für die Herstellung von Legierungen und sequenziellen Beschichtungen.
-
Magnetron-Sputtern:
- Bei diesem Verfahren werden positiv geladene Ionen mit einem negativ geladenen Zielmaterial zur Kollision gebracht.
- Es werden einzelne Atome oder Cluster ausgestoßen, was zu einer besseren Gleichmäßigkeit und Haftung des Films führt.
- Arbeitet innerhalb eines geschlossenen Magnetfeldes, was eine höhere Skalierbarkeit und Automatisierung ermöglicht.
2. Eigenschaften des Films
-
Haftvermögen:
- Thermisch aufgedampfte Schichten weisen aufgrund der geringeren Energie der Abscheidung eine relativ schwache Haftung auf.
- Gesputterte Schichten haften aufgrund des Hochenergieverfahrens besser auf dem Substrat.
-
Gleichmäßigkeit:
- Die thermische Verdampfung sorgt für eine hervorragende Gleichmäßigkeit des Films.
- Das Sputtern kann Partikel enthalten, was zu einer etwas geringeren Gleichmäßigkeit, aber insgesamt zu einer besseren Schichtqualität führt.
-
Korngröße:
- Beim Sputtern entstehen kleinere Körner, die die Eigenschaften der Folie wie Härte und Haltbarkeit verbessern.
- Die thermische Verdampfung führt zu größeren Körnern, die die mechanischen Eigenschaften der Folie beeinträchtigen können.
3. Abscheiderate und Wirkungsgrad
-
Thermische Verdampfung:
- Höhere Abscheidungsraten, daher geeignet für Anwendungen, die eine schnelle Beschichtung erfordern.
- Kürzere Laufzeiten aufgrund des robusten Dampfstroms.
-
Magnetron-Sputtern:
- Geringere Abscheideraten, außer bei reinen Metallen.
- Längere Laufzeiten, bietet aber eine bessere Kontrolle der Schichteigenschaften.
4. Farb- und Materialvielfalt
-
Thermische Verdampfung:
- Begrenzt auf die echte Farbe des Aluminiums.
- Für andere Farben ist eine zusätzliche Spritzlackierung erforderlich.
-
Magnetron-Zerstäubung:
- Bietet eine größere Farbvielfalt durch Modulation.
- Kann einen realistischeren und gleichmäßigeren Metalleffekt erzeugen.
5. Anwendungen
-
Thermische Verdampfung:
- Wird häufig für die Herstellung von OLEDs und Dünnschichttransistoren verwendet.
- Effektiv für Anwendungen, die hohe Abscheidungsraten und einfache Beschichtungen erfordern.
-
Magnetron-Sputtering:
- Ideal für die elektrische oder optische Produktion.
- Geeignet für Anwendungen, die hochwertige Folien mit ausgezeichneter Haftung und Gleichmäßigkeit erfordern.
6. Vakuum und Umweltbedingungen
-
Thermische Verdampfung:
- Erfordert eine Hochvakuumumgebung.
- Weniger absorbiertes Gas in der Schicht, was zu reineren Beschichtungen führt.
-
Magnetron-Sputtern:
- Funktioniert bei niedrigerem Vakuum.
- Höherer Gehalt an absorbierten Gasen, was sich auf die Folieneigenschaften auswirken kann, aber auch für eine bessere Haftung sorgt.
7. Energie und Partikeldynamik
-
Thermische Verdampfung:
- Abgeschiedene Arten haben eine geringere Energie, was zu weniger dichten Schichten führt.
- Die atomisierten Partikel sind stärker dispergiert, was zu einer weniger gerichteten Abscheidung führt.
-
Magnetron-Sputtering:
- Abgeschiedene Arten haben eine höhere Energie, was zu dichteren und haltbareren Schichten führt.
- Zerstäubte Partikel sind gerichteter und ermöglichen eine bessere Kontrolle der Schichtdicke und Gleichmäßigkeit.
8. Skalierbarkeit und Automatisierung
-
Thermische Verdampfung:
- Weniger skalierbar und aufgrund der Art des Prozesses schwieriger zu automatisieren.
-
Magnetron-Sputtern:
- Hochgradig skalierbar und kann für viele Anwendungen automatisiert werden, wodurch es sich für die Großproduktion eignet.
Zusammenfassend lässt sich sagen, dass die Wahl zwischen thermischer Verdampfung und Magnetronsputtern von den spezifischen Anforderungen der Anwendung abhängt, einschließlich Faktoren wie Abscheiderate, Schichtqualität, Haftung und Farbvielfalt.Jedes Verfahren hat seine eigenen Vorteile und Grenzen, so dass es sich für unterschiedliche Projekte und Branchen eignet.
Zusammenfassende Tabelle:
Merkmal | Thermische Verdampfung | Magnetronzerstäubung |
---|---|---|
Mechanismus | Widerstandsheizung im Vakuum | Hochenergetisches Plasma stößt Atome aus einem Target aus |
Abscheiderate | Hoch | Geringer (außer bei reinen Metallen) |
Filmhaftung | Schwächer | Stärker |
Gleichmäßiger Film | Hervorragend | Etwas niedriger, aber bessere Gesamtqualität |
Korngröße | Größer | Kleiner |
Farbliche Vielseitigkeit | Begrenzt auf Aluminium | Größere Farboptionen |
Anwendungen | OLEDs, Dünnschichttransistoren | Elektrische und optische Produktion |
Vakuum-Anforderungen | Hochvakuum | Niedrigeres Vakuum |
Skalierbarkeit | Weniger skalierbar | Hochgradig skalierbar und automatisierbar |
Sind Sie noch unsicher, welche Dünnschichttechnik für Ihre Anforderungen geeignet ist? Kontaktieren Sie noch heute unsere Experten für eine persönliche Beratung!