Das Sintern ist ein entscheidender Prozess in der Werkstoffkunde, der die Mikrostruktur von Werkstoffen erheblich beeinflusst und zu Veränderungen der Korngröße, der Porengröße und der Korngrenzenverteilung führt.Diese mikrostrukturellen Veränderungen haben einen direkten Einfluss auf die mechanischen Eigenschaften des Materials, wie z. B. Festigkeit, Härte und Haltbarkeit.Durch die Bindung und Verdichtung von Partikeln durch kontrollierte Erhitzung und Diffusionsmechanismen verbessert das Sintern die allgemeine mechanische Integrität des Materials.Außerdem verringert das Sintern die Porosität, verbessert die Materialkonsistenz und bietet Vorteile für die Umwelt, da es im Vergleich zu Schmelzverfahren weniger Energie benötigt.Das Verfahren ermöglicht auch die Herstellung hochfester, nahezu netzförmiger Objekte und ist damit eine vielseitige und effiziente Fertigungstechnik.
Die wichtigsten Punkte erklärt:
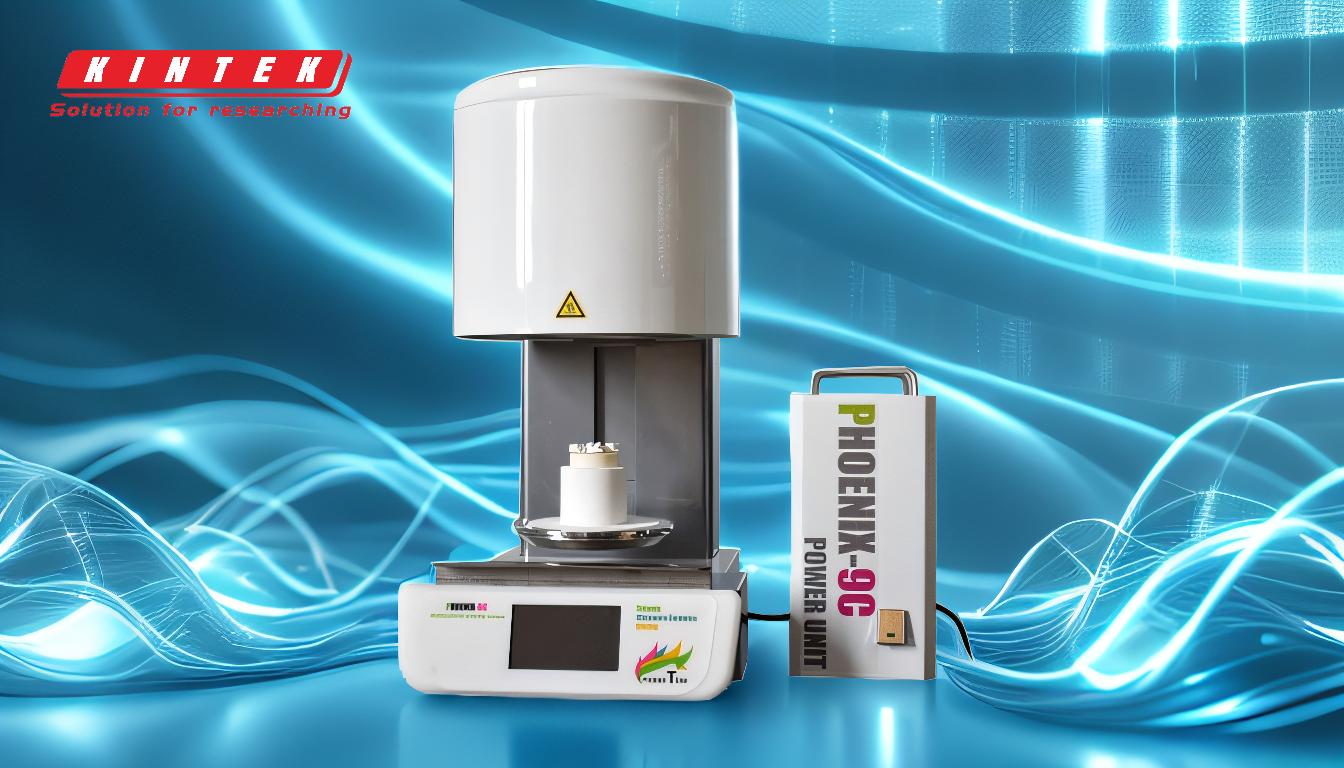
-
Wirkung auf die Korngröße:
- Erläuterung:Beim Sintern verbinden sich die Partikel und verdichten sich, was zu einem Kornwachstum führt.Dieses Kornwachstum ist das Ergebnis von Materialwanderung, Rekristallisation und Diffusionsmechanismen während des Erhitzungsprozesses.
- Aufprall:Größere Körner können die Festigkeit und Härte des Werkstoffs verbessern, aber ein übermäßiges Kornwachstum kann die Zähigkeit verringern.Kontrolliertes Sintern gewährleistet die optimale Korngröße für die gewünschten mechanischen Eigenschaften.
-
Verringerung der Porosität:
- Erläuterung:Das Sintern minimiert die Oberflächenporosität, indem Hohlräume und Lücken zwischen den Partikeln gefüllt werden.Dieser Verdichtungsprozess ist entscheidend für das Erreichen eines vollständig dichten Teils.
- Aufprall:Eine geringere Porosität erhöht die Festigkeit, Haltbarkeit und Verschleißfestigkeit des Materials.Sie verbessert auch die Fähigkeit des Materials, mechanischen Belastungen und Umwelteinflüssen zu widerstehen.
-
Form und Verteilung der Korngrenzen:
- Erläuterung:Das Sintern verändert die Form und die Verteilung der Korngrenzen, d. h. der Grenzflächen zwischen den einzelnen Körnern des Werkstoffs.
- Aufprall:Gut verteilte und kohärente Korngrenzen tragen zur mechanischen Integrität und Rissbeständigkeit des Materials bei.Eine ordnungsgemäße Sinterung gewährleistet eine gleichmäßige Verteilung der Korngrenzen und verbessert die Gesamtleistung.
-
Verbesserung der mechanischen Eigenschaften:
- Erläuterung:Der Sinterprozess verbessert die mechanischen Eigenschaften wie Festigkeit, Härte und Verschleißfestigkeit, indem er eine dichte und kohäsive Struktur schafft.
- Aufprall:Dank verbesserter mechanischer Eigenschaften eignen sich gesinterte Werkstoffe für Hochleistungsanwendungen wie Turbinenschaufeln und andere Bauteile, die eine hohe Festigkeit und Haltbarkeit erfordern.
-
Ökologische und wirtschaftliche Vorteile:
- Erläuterung:Das Sintern erfordert im Vergleich zum Schmelzen weniger Energie und ist damit eine umweltfreundliche Option.Außerdem ermöglicht es eine bessere Kontrolle über den Herstellungsprozess, was zu gleichmäßigeren Produkten führt.
- Aufschlag:Ein geringerer Energieverbrauch senkt die Produktionskosten und die Umweltbelastung.Die gleichbleibende Produktqualität gewährleistet Zuverlässigkeit und reduziert den Ausschuss.
-
Erzeugung von nahezu netzförmigen Objekten:
- Erläuterung:Das Sintern ermöglicht die Herstellung von nahezu netzförmigen Objekten, wodurch sich die Notwendigkeit einer umfangreichen Nachbearbeitung verringert.
- Aufschlag:Diese Fähigkeit ist besonders bei komplexen Geometrien und hochfesten Materialien von Vorteil, da sie den Materialabfall und die Produktionszeit minimiert.
-
Handhabung schwieriger Materialien:
- Erläuterung:Das Sintern eignet sich für die Bearbeitung von Materialien mit sehr hohem Schmelzpunkt, wie z. B. bestimmte Metalle und Keramiken.
- Aufprall:Dies macht das Sintern zu einem vielseitigen Verfahren zur Herstellung von Bauteilen aus Werkstoffen, die sonst nur schwer zu bearbeiten sind, und erweitert das Anwendungsspektrum von Sinterprodukten.
Zusammenfassend lässt sich sagen, dass das Sintern die Mikrostruktur von Werkstoffen tiefgreifend beeinflusst, was zu erheblichen Verbesserungen ihrer mechanischen Eigenschaften und ihrer Gesamtleistung führt.Durch das Verständnis und die Kontrolle des Sinterprozesses können Hersteller hochwertige, langlebige und effiziente Werkstoffe herstellen, die auf bestimmte Anwendungen zugeschnitten sind.
Zusammenfassende Tabelle:
Hauptaspekt | Erläuterung | Aufprall |
---|---|---|
Korngröße | Die Sinterung fördert das Kornwachstum durch Materialwanderung und Diffusion. | Verbessert Festigkeit und Härte; übermäßiges Wachstum kann die Zähigkeit verringern. |
Verringerung der Porosität | Füllt Hohlräume und Lücken zwischen den Partikeln und bewirkt eine Verdichtung. | Erhöht die Festigkeit, Haltbarkeit und Widerstandsfähigkeit gegen mechanische Beanspruchung. |
Korngrenzenverteilung | Verändert Form und Verteilung der Korngrenzen. | Verbessert die mechanische Integrität und die Rissbeständigkeit. |
Mechanische Eigenschaften | Erzeugt dichte, kohäsive Strukturen, die die Festigkeit und Verschleißbeständigkeit erhöhen. | Ideal für Hochleistungsanwendungen wie Turbinenschaufeln. |
Vorteile für die Umwelt | Benötigt im Vergleich zu Schmelzverfahren weniger Energie. | Reduziert den Energieverbrauch, senkt die Kosten und minimiert die Umweltauswirkungen. |
Netzgeformte Objekte | Erzeugt nahezu netzförmige Objekte, wodurch sich der Nachbearbeitungsbedarf verringert. | Minimiert den Materialabfall und die Produktionszeit, insbesondere bei komplexen Geometrien. |
Handhabung schwieriger Materialien | Wirksam für Materialien mit hohem Schmelzpunkt, wie Metalle und Keramik. | Erweitert den Anwendungsbereich für anspruchsvolle Materialien. |
Erfahren Sie, wie das Sintern Ihre Materialeigenschaften optimieren kann - Kontaktieren Sie unsere Experten noch heute !