Die Verdampfungsmethode bei der physikalischen Gasphasenabscheidung (PVD) ist eine weit verbreitete Technik zur Abscheidung dünner Materialschichten auf einem Substrat.Bei dieser Methode wird das Material erhitzt, bis es verdampft und einen Dampf bildet, der dann auf dem Substrat kondensiert und eine dünne Schicht bildet.Das Verfahren ist sehr gut steuerbar und ermöglicht die Herstellung von Schichten mit hervorragender Reinheit, Gleichmäßigkeit und Haftung.Zu den gängigen Techniken innerhalb der Verdampfungsmethode gehören die thermische Verdampfung und die Elektronenstrahlverdampfung, die jeweils unterschiedliche Heizmechanismen nutzen, um die gewünschte Verdampfung des Materials zu erreichen.
Die wichtigsten Punkte werden erklärt:
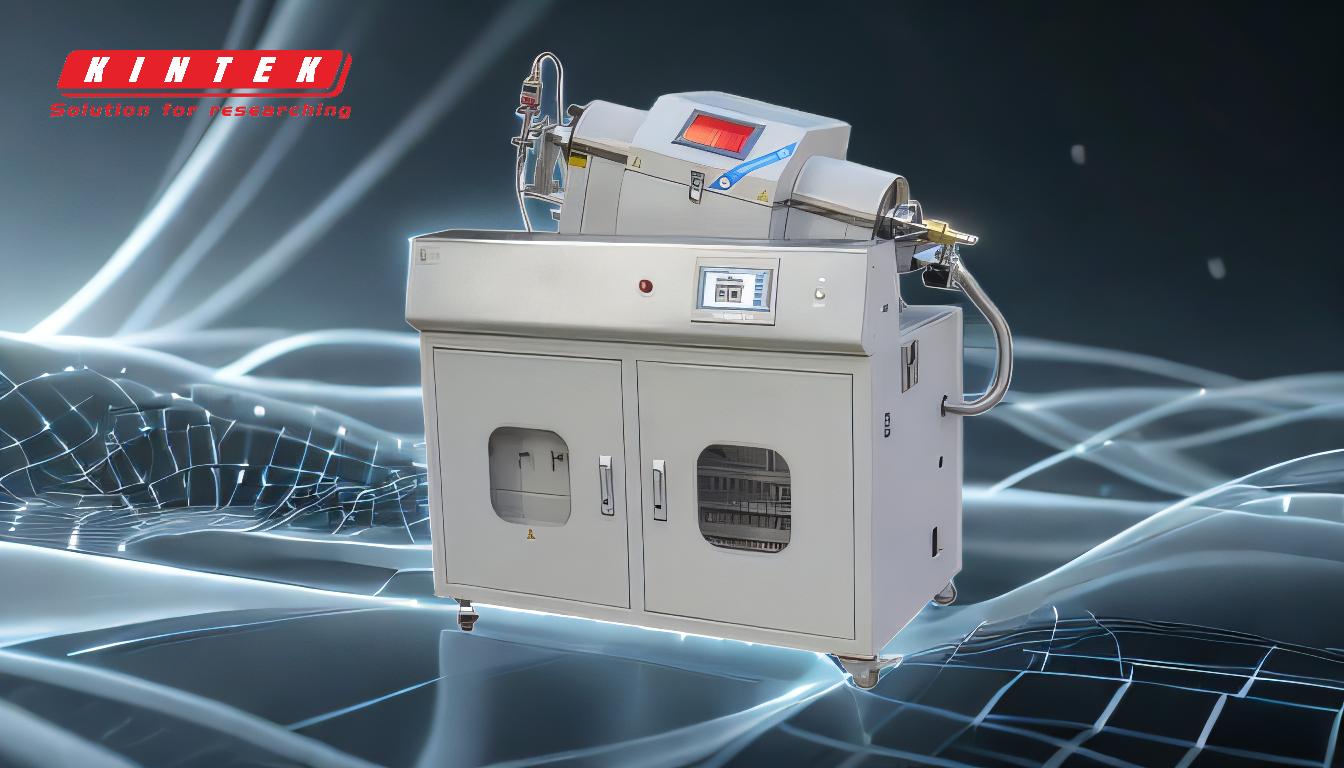
-
Thermische Verdampfungsabscheidung:
- Bei der thermischen Verdampfung wird das abzuscheidende Material in ein Widerstandsschiff oder eine Spule gelegt, die normalerweise aus einem breiten Metallband mit einer großen Vertiefung besteht.In die Vertiefung werden Materialpellets gelegt, und durch das Band wird ein elektrischer Strom geleitet, um es zu erhitzen.Durch diese Erwärmung schmelzen die Pellets und verdampfen schließlich.Der Dampf strömt dann durch das Vakuum und setzt sich auf dem Substrat ab, wo er einen dünnen Film bildet.
- Diese Methode eignet sich besonders für Materialien, die sich bei relativ niedrigen Temperaturen leicht verdampfen lassen.Es handelt sich um ein einfaches und kostengünstiges Verfahren, das sich in verschiedenen Anwendungsbereichen durchgesetzt hat, z. B. bei der Herstellung von optischen Beschichtungen und elektronischen Geräten.
-
Elektronenstrahlverdampfung:
- Die Elektronenstrahlverdampfung ist eine fortschrittlichere Technik, bei der ein Elektronenstrahl zum Erhitzen des Materials verwendet wird.Der Elektronenstrahl wird auf das Material fokussiert, wodurch es sich schnell erhitzt und verdampft.Der Dampf schlägt sich dann auf dem Substrat nieder und bildet einen dünnen Film.
- Diese Methode ist besonders nützlich für Materialien, die zum Verdampfen hohe Temperaturen benötigen, da der Elektronenstrahl eine konzentrierte Wärmequelle darstellen kann.Es wird häufig bei Anwendungen eingesetzt, die hochreine Schichten erfordern, wie z. B. in der Halbleiterindustrie.Die durch Elektronenstrahlverdampfung hergestellten Schichten weisen in der Regel hervorragende Reflexionseigenschaften auf und eignen sich daher für optische Anwendungen.
-
Vorteile der Verdampfungsmethode:
- Hohe Reinheit:Die Verdampfungsmethode ermöglicht die Herstellung von Folien mit extrem hoher Reinheit, da der Prozess im Vakuum abläuft und die Verunreinigung minimiert wird.
- Gleichmäßigkeit:Die erzeugten Filme sind sehr gleichmäßig, was für Anwendungen, die eine genaue Kontrolle der Dicke erfordern, entscheidend ist.
- Haftung:Die Folien haften gut auf dem Untergrund und gewährleisten Haltbarkeit und Langlebigkeit.
- Vielseitigkeit:Das Verfahren kann für eine breite Palette von Materialien eingesetzt werden, darunter Metalle, Halbleiter und Isolatoren.
-
Vergleich mit anderen PVD-Methoden:
- Thermische Gasphasenabscheidung:Ähnlich wie bei der thermischen Verdampfung, aber in der Regel wird das Material mit einem elektrischen Heizer erhitzt, bis es in die Gasphase übergeht.Diese Methode wird auch zur Herstellung reiner und gleichmäßiger Schichten verwendet.
- Molekularstrahlepitaxie (MBE):Eine speziellere Form des PVD, die für die Herstellung hochwertiger kristalliner Schichten verwendet wird.Dabei werden Molekularstrahlen in einer Ultrahochvakuumumgebung eingesetzt.
- Ionenstrahl-Sputterbeschichtung:Bei diesem Verfahren wird ein Zielmaterial mit Ionen beschossen, um Atome auszustoßen, die sich dann auf dem Substrat ablagern.Diese Methode ist bekannt für die Herstellung von Schichten mit hervorragender Haftung und Dichte.
-
Anwendungen der Verdampfungsmethode:
- Optische Beschichtungen:Wird zur Herstellung von reflektierenden und antireflektierenden Beschichtungen auf Linsen und Spiegeln verwendet.
- Elektronik:Unerlässlich für die Abscheidung dünner Schichten bei der Herstellung von Halbleitern und anderen elektronischen Bauteilen.
- Dekorative Beschichtungen:Zum Aufbringen dünner Schichten zu ästhetischen Zwecken, z. B. auf Schmuck oder Automobilteilen.
- Barriere-Schichten:Wird in Verpackungen verwendet, um Sperrschichten zu bilden, die Produkte vor Feuchtigkeit und Sauerstoff schützen.
Zusammenfassend lässt sich sagen, dass die PVD-Bedampfung eine vielseitige und effektive Technik für die Abscheidung dünner Schichten mit hoher Reinheit, Gleichmäßigkeit und Haftung ist.Es umfasst sowohl die thermische Verdampfung als auch die Elektronenstrahlverdampfung, die jeweils für unterschiedliche Materialien und Anwendungen geeignet sind.Das Verfahren wird in vielen Branchen von der Elektronik bis zur Optik eingesetzt und ist damit ein Eckpfeiler der modernen Dünnschichttechnologie.
Zusammenfassende Tabelle:
Aspekt | Einzelheiten |
---|---|
Techniken | Thermische Verdampfung, Elektronenstrahlverdampfung |
Vorteile | Hohe Reinheit, Gleichmäßigkeit, Haftung, Vielseitigkeit |
Anwendungen | Optische Beschichtungen, Elektronik, dekorative Beschichtungen, Barriereschichten |
Vergleich mit PVD | Thermische Gasphasenabscheidung, Molekularstrahlepitaxie, Ionenstrahlsputtern |
Entdecken Sie, wie das Aufdampfverfahren Ihre Dünnschichtprozesse verbessern kann. Kontaktieren Sie unsere Experten noch heute !