Die physikalische Gasphasenabscheidung (PVD) ist ein vakuumbasiertes Beschichtungsverfahren, mit dem dünne Materialschichten auf ein Substrat aufgebracht werden.Bei diesem Verfahren wird ein festes Material durch Methoden wie thermisches Verdampfen, Sputtern oder Ionenbeschuss in eine Dampfphase umgewandelt und der Dampf anschließend auf einem Substrat kondensiert, um eine dünne, gleichmäßige Schicht zu bilden.PVD wird in vielen Branchen eingesetzt, in denen haltbare und leistungsstarke Beschichtungen benötigt werden, z. B. in der Elektronik, Optik und Werkzeugherstellung.Das Verfahren zeichnet sich durch seine Fähigkeit aus, Beschichtungen mit hervorragender Haftung, hoher Reinheit und präziser Kontrolle der Schichtdicke zu erzeugen, wodurch es sich für Anwendungen eignet, die Korrosionsbeständigkeit, Verschleißfestigkeit oder thermische Stabilität erfordern.
Die wichtigsten Punkte erklärt:
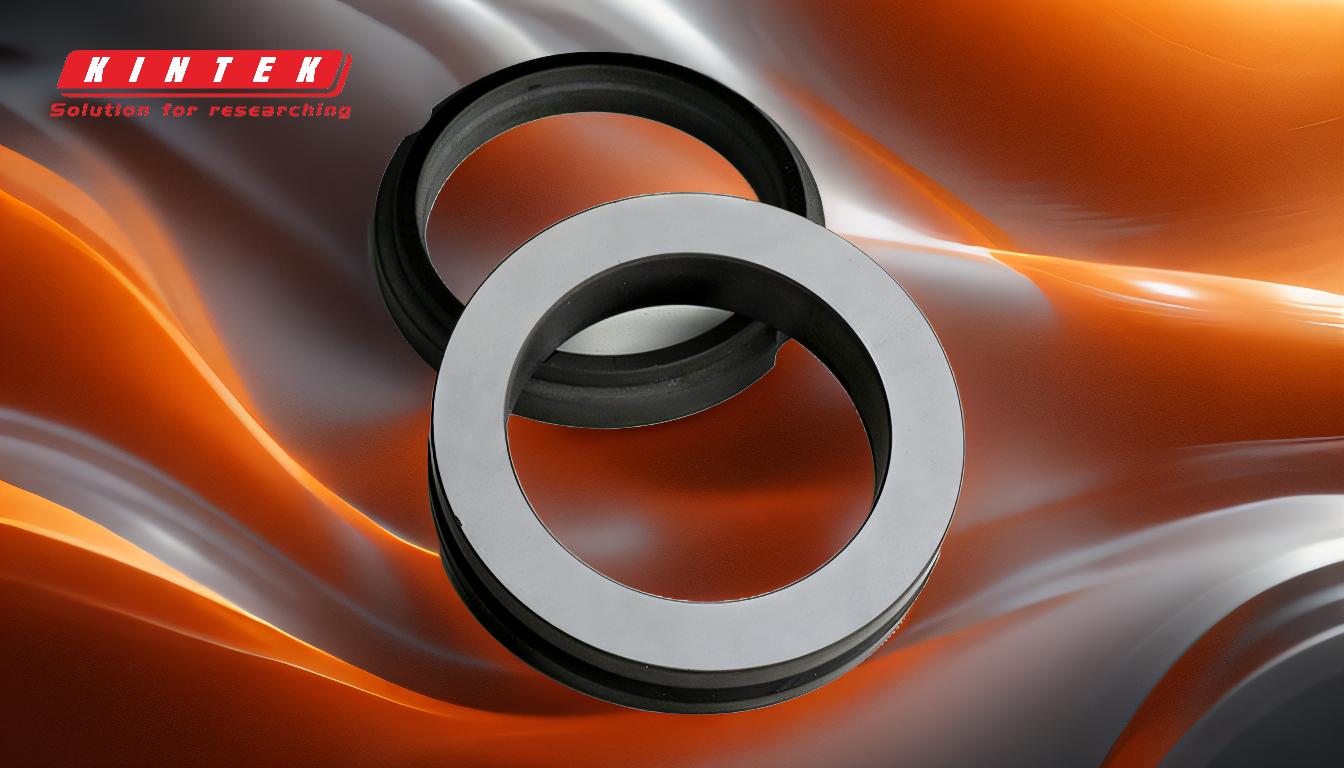
-
Vakuum Umwelt:
- PVD wird in einer Vakuumkammer durchgeführt, um die Verunreinigung durch Hintergrundgase zu minimieren und einen sauberen Beschichtungsprozess zu gewährleisten.
- Durch die Senkung des Drucks in der Kammer wird die Wahrscheinlichkeit chemischer Reaktionen zwischen den Hintergrundgasen und dem abgeschiedenen Material verringert, die die Qualität der Beschichtung beeinträchtigen könnten.
-
Verdampfung des Ausgangsmaterials:
-
Das feste Vorläufermaterial (Target) wird mit einer von mehreren Methoden in eine Dampfphase umgewandelt:
- Thermische Verdampfung:Das Zielmaterial wird erhitzt, bis es verdampft.Dies kann durch Widerstandsheizung oder Elektronenstrahlheizung geschehen.
- Sputtern:Hochenergetische Ionen beschießen das Zielmaterial und schlagen Atome von der Oberfläche in die Dampfphase ab.
- Ionenplattieren:Eine Kombination aus Sputtern und Verdampfen, bei der das Zielmaterial vor der Abscheidung verdampft und ionisiert wird.
-
Das feste Vorläufermaterial (Target) wird mit einer von mehreren Methoden in eine Dampfphase umgewandelt:
-
Transport von verdampftem Material:
- Die verdampften Atome oder Moleküle bewegen sich durch die Vakuumkammer zum Substrat.
- Die Vakuumumgebung sorgt dafür, dass sich die verdampften Partikel in einer geraden Linie bewegen, was eine präzise Steuerung des Abscheidungsprozesses ermöglicht.
-
Kondensation auf dem Substrat:
- Das verdampfte Material kondensiert auf dem Substrat und bildet einen dünnen, gleichmäßigen Film.
- Die Haftung des Films auf dem Substrat ist in der Regel stark, was zu dauerhaften Beschichtungen führt.
-
Kontrolle der Filmdicke und -rate:
- Ein Quarzkristall-Überwachungsgerät wird häufig verwendet, um die Abscheidungsrate und die Dicke der Schicht zu messen und zu kontrollieren.
- Auf diese Weise wird sichergestellt, dass die Beschichtung den gewünschten Spezifikationen für die jeweilige Anwendung entspricht.
-
Unter-Verfahren der PVD:
- Thermische Verdampfung:Geeignet für Materialien mit niedrigerem Schmelzpunkt.Das Zielmaterial wird erhitzt, bis es verdampft, und der Dampf kondensiert auf dem Substrat.
- Sputtern:Ideal für Materialien mit höherem Schmelzpunkt.Hochenergetische Ionen beschießen das Target und stoßen Atome aus, die sich dann auf dem Substrat ablagern.
- Ionenplattieren:Kombiniert Verdampfung und Ionisierung zur Verbesserung von Haftung und Filmdichte.
-
Anwendungen und Vorteile:
- PVD-Beschichtungen werden in einer Vielzahl von Branchen eingesetzt, z. B. in der Elektronik (für Halbleiterbauelemente), in der Optik (für Antireflexbeschichtungen) und in der Fertigung (für verschleißfeste Werkzeuge).
- Das Verfahren erzeugt Beschichtungen mit hervorragender Haftung, hoher Reinheit und präziser Kontrolle der Schichtdicke und eignet sich daher für Anwendungen, die Haltbarkeit, Korrosionsbeständigkeit oder thermische Stabilität erfordern.
-
Vorteile von PVD:
- Hohe Adhäsion:Die Beschichtungen haften fest auf dem Substrat und gewährleisten eine lang anhaltende Leistung.
- Hohe Reinheit:Die Vakuumumgebung minimiert die Verunreinigung, was zu hochreinen Beschichtungen führt.
- Präzision:Das Verfahren ermöglicht eine präzise Kontrolle der Schichtdicke und der Zusammensetzung.
- Vielseitigkeit:PVD kann bei einer Vielzahl von Materialien eingesetzt werden, darunter Metalle, Keramiken und Verbundwerkstoffe.
-
Herausforderungen und Überlegungen:
- Kosten:PVD-Anlagen und -Verfahren können teuer sein, vor allem bei groß angelegten Anwendungen.
- Komplexität:Das Verfahren erfordert spezielle Geräte und Fachkenntnisse, um optimale Ergebnisse zu erzielen.
- Grenzen des Materials:Einige Materialien sind aufgrund ihrer physikalischen Eigenschaften (z. B. Schmelzpunkt, Dampfdruck) für bestimmte PVD-Verfahren nicht geeignet.
Zusammenfassend lässt sich sagen, dass PVD ein vielseitiges und präzises Verfahren zur Abscheidung dünner Schichten mit hervorragenden Eigenschaften ist.Seine Fähigkeit, hochwertige Beschichtungen in einer kontrollierten Umgebung herzustellen, macht es zu einem wertvollen Verfahren für ein breites Spektrum industrieller Anwendungen.
Zusammenfassende Tabelle:
Aspekt | Einzelheiten |
---|---|
Prozess | Umwandlung von festem Material in Dampf, der dann auf einem Substrat kondensiert und einen dünnen Film bildet. |
Wichtigste Methoden | Thermisches Verdampfen, Sputtern, Ionenplattieren |
Anwendungen | Elektronik, Optik, Werkzeugbau |
Vorteile | Hohe Adhäsion, hohe Reinheit, präzise Dickenkontrolle, Vielseitigkeit |
Herausforderungen | Hohe Kosten, Komplexität, Materialbeschränkungen |
Entdecken Sie, wie PVD Ihre industriellen Anwendungen verbessern kann. Kontaktieren Sie uns noch heute für fachkundige Beratung!