Die physikalische Gasphasenabscheidung (Physical Vapor Deposition, PVD) ist ein Verfahren zur Herstellung von Dünnfilmbeschichtungen, bei dem feste Materialien in eine Dampfphase überführt und dann auf einem Substrat kondensiert werden.Bei diesem Verfahren werden das Substrat und das Beschichtungsmaterial in eine Vakuumkammer gebracht, in der das Beschichtungsmaterial (Target) durch Techniken wie Sputtern, thermische Verdampfung oder Elektronenstrahlverdampfung verdampft wird.Das verdampfte Material wandert dann durch die Kammer und lagert sich auf dem Substrat ab, wobei ein haltbarer, hochwertiger Dünnfilm entsteht.PVD ist bekannt für seine Fähigkeit, Beschichtungen mit hervorragender Haftung, hoher Schmelzpunkttoleranz und Beständigkeit gegen Korrosion und hohe Temperaturen herzustellen.Das Verfahren arbeitet nach dem Prinzip der "Sichtlinie", d. h. die verdampften Atome gelangen direkt auf das Substrat, was eine präzise und kontrollierte Abscheidung gewährleistet.
Die wichtigsten Punkte werden erklärt:
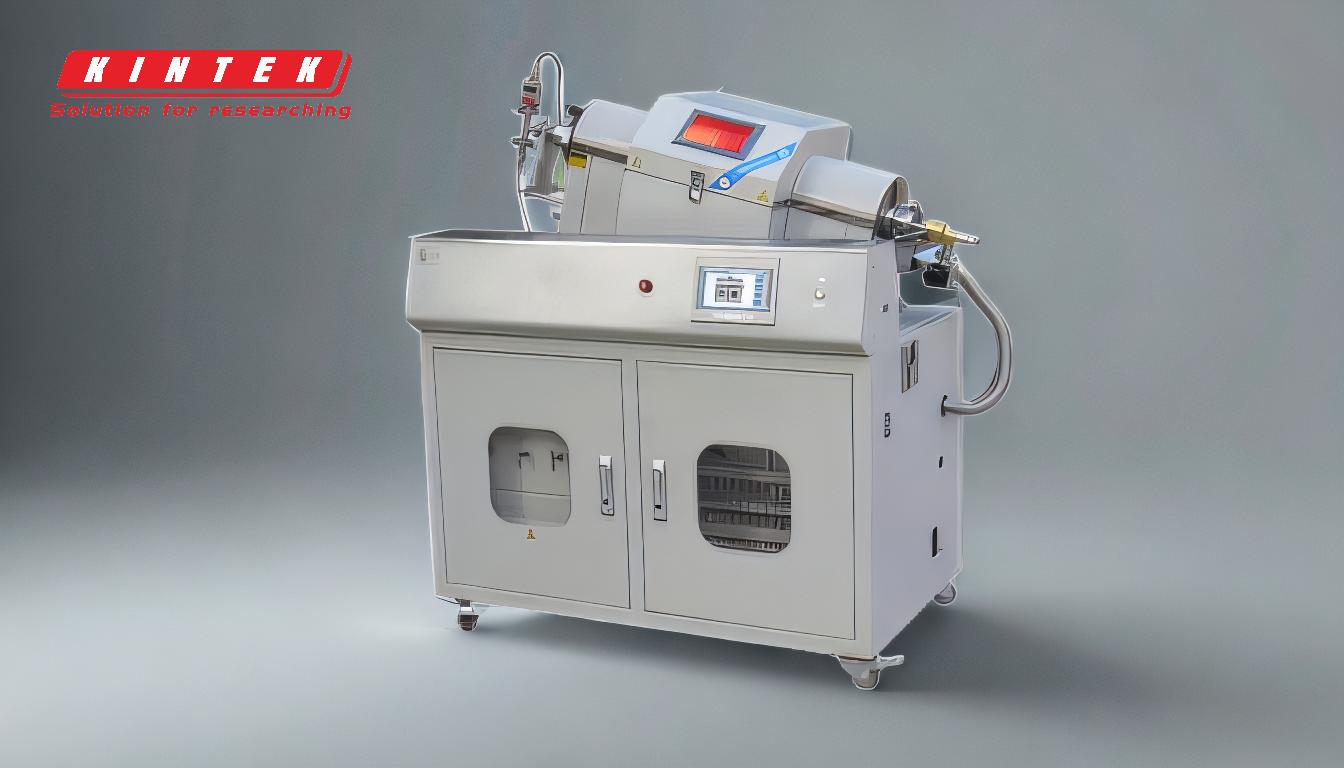
-
Definition von PVD
- Physical Vapor Deposition (PVD) ist ein Beschichtungsverfahren, bei dem feste Materialien in einer Vakuumumgebung verdampft und dann auf einem Substrat kondensiert werden, um einen dünnen Film zu bilden.
- Bei diesem Verfahren wird das Material von einer festen in eine Dampfphase und dann wieder in eine feste Phase auf dem Substrat überführt.
-
Schlüsselkomponenten von PVD
- Vakuumkammer:Das Verfahren findet in einer Niederdruckumgebung statt, um Verunreinigungen zu vermeiden und eine kontrollierte Abscheidung zu gewährleisten.
- Ziel-Material:Das feste Material (z. B. Metalle, Keramik), das verdampft wird, um die Beschichtung zu bilden.
- Substrat:Der Gegenstand oder die Oberfläche, auf die das verdampfte Material aufgebracht wird.
- Energiequelle:Methoden wie Sputtern, Elektronenstrahlen, Laserstrahlen oder Bogenentladungen werden zur Verdampfung des Zielmaterials verwendet.
-
Stadien des PVD-Prozesses
- Verdampfung:Das Zielmaterial wird mit Hilfe von Hochenergieverfahren von der festen in die dampfförmige Phase überführt.
- Transport:Die verdampften Atome durchqueren die Vakuumkammer in einer "Sichtlinie".
- Ablagerung:Die verdampften Atome kondensieren auf dem Substrat und bilden einen dünnen Film.
-
Methoden der PVD
- Sputtern:Hochenergetische Ionen beschießen das Zielmaterial und stoßen Atome aus, die sich dann auf dem Substrat ablagern.
- Thermische Verdampfung:Das Targetmaterial wird erhitzt, bis es verdampft, und der Dampf kondensiert auf dem Substrat.
- Elektronenstrahlverdampfung:Ein Elektronenstrahl wird verwendet, um das Zielmaterial zu erhitzen und zu verdampfen.
- Bogenentladung:Ein elektrischer Lichtbogen verdampft das Zielmaterial, das sich dann auf dem Substrat ablagert.
-
Vorteile von PVD
- Hochwertige Beschichtungen:PVD erzeugt dünne Schichten mit hervorragender Haftung, Gleichmäßigkeit und Haltbarkeit.
- Material Vielseitigkeit:Er eignet sich für Materialien mit hohem Schmelzpunkt, wie z. B. Titan und Keramiken.
- Korrosions- und Temperaturbeständigkeit:PVD-Beschichtungen sind äußerst korrosionsbeständig und können hohen Temperaturen standhalten.
- Präzision:Die "Sichtlinie" des PVD-Verfahrens ermöglicht eine präzise Steuerung des Abscheidungsprozesses.
-
Anwendungen von PVD
- Industrielle Werkzeuge:PVD wird zur Beschichtung von Schneidwerkzeugen, Formen und Gesenken verwendet, um deren Härte und Verschleißfestigkeit zu erhöhen.
- Elektronik:Es wird bei der Herstellung von Halbleitern, Sonnenkollektoren und optischen Beschichtungen verwendet.
- Dekorative Beschichtungen:PVD wird verwendet, um dauerhafte, kratzfeste Oberflächen für Schmuck, Uhren und Unterhaltungselektronik herzustellen.
- Medizinische Geräte:PVD-Beschichtungen verbessern die Biokompatibilität und Verschleißfestigkeit von medizinischen Implantaten und Instrumenten.
-
Herausforderungen und Überlegungen
- Kosten:PVD-Anlagen und -Verfahren können teuer sein, da sie eine Vakuumumgebung und Hochenergiequellen benötigen.
- Komplexität:Das Verfahren erfordert eine genaue Kontrolle von Parametern wie Temperatur, Druck und Energiezufuhr.
- Beschränkungen des Substrats:Die "Sichtlinie" von PVD kann die Beschichtung komplexer Geometrien oder Innenflächen erschweren.
-
Zukünftige Trends bei PVD
- Nanotechnologie:PVD wird eingesetzt, um nanostrukturierte Beschichtungen mit einzigartigen Eigenschaften zu erzeugen, z. B. erhöhte elektrische Leitfähigkeit oder antibakterielle Wirkung.
- Hybride Verfahren:Kombination von PVD mit anderen Techniken, wie der chemischen Gasphasenabscheidung (CVD), um multifunktionale Beschichtungen zu erzielen.
- Nachhaltigkeit:Entwicklung energieeffizienterer PVD-Verfahren und Verwendung umweltfreundlicher Materialien.
Durch das Verständnis der Theorie und der Mechanik des PVD-Verfahrens können die Käufer von Anlagen und Verbrauchsmaterialien fundierte Entscheidungen über dessen Anwendung in verschiedenen Branchen treffen.Die Fähigkeit des Verfahrens, Hochleistungsbeschichtungen herzustellen, macht es zu einem wertvollen Instrument zur Verbesserung der Haltbarkeit und Funktionalität einer Vielzahl von Produkten.
Zusammenfassende Tabelle:
Aspekt | Einzelheiten |
---|---|
Definition | Beschichtungsverfahren, bei dem feste Materialien verdampft und auf einem Substrat kondensiert werden. |
Wichtige Komponenten | Vakuumkammer, Targetmaterial, Substrat, Energiequelle. |
Prozess-Schritte | Verdampfung, Transport, Ablagerung. |
Verfahren | Sputtern, thermische Verdampfung, Elektronenstrahlverdampfung, Bogenentladung. |
Vorteile | Hochwertige Beschichtungen, Vielseitigkeit der Materialien, Korrosionsbeständigkeit, Präzision. |
Anwendungen | Industriewerkzeuge, Elektronik, dekorative Beschichtungen, medizinische Geräte. |
Herausforderungen | Hohe Kosten, Komplexität des Prozesses, Substratbeschränkungen. |
Zukünftige Trends | Nanotechnologie, Hybridverfahren, Nachhaltigkeit. |
Sind Sie bereit, Ihre Produkte mit PVD-Beschichtungen zu veredeln? Kontaktieren Sie uns noch heute um mehr zu erfahren!