Die physikalische Gasphasenabscheidung (PVD) ist ein hochentwickeltes Beschichtungsverfahren, mit dem dünne Materialschichten auf ein Substrat aufgebracht werden.Bei diesem Verfahren wird ein festes Zielmaterial in eine Dampfphase umgewandelt, die dann auf dem Substrat kondensiert und eine dünne, haltbare und oft hochspezialisierte Beschichtung bildet.PVD ist in Branchen wie Elektronik, Optik und Fertigung weit verbreitet, da sich damit hochwertige, korrosionsbeständige und temperaturtolerante Beschichtungen herstellen lassen.Das Verfahren umfasst in der Regel vier Hauptschritte: Verdampfung, Transport, Reaktion und Abscheidung.Jeder Schritt wird sorgfältig kontrolliert, um die gewünschten Eigenschaften der endgültigen Beschichtung, wie Haftung, Dicke und Zusammensetzung, zu gewährleisten.
Die wichtigsten Punkte werden erklärt:
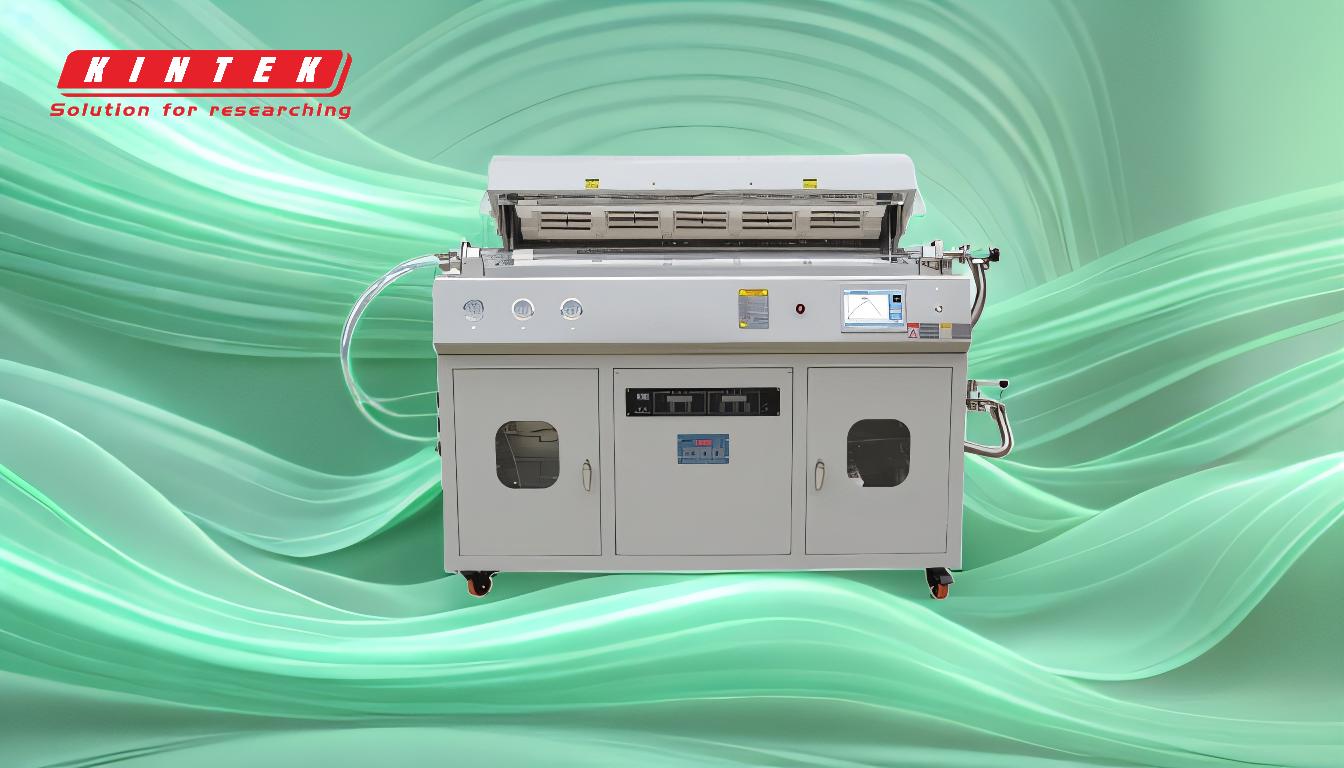
-
Verdampfung des Zielmaterials:
- Der erste Schritt im PVD-Verfahren ist die Verdampfung des Targetmaterials.Dies wird erreicht, indem das feste Target mit einer Hochenergiequelle beschossen wird, z. B. mit einem Elektronen-, Laser- oder Ionenstrahl.Die Energie bewirkt, dass sich die Atome im Target lösen und von einer festen in eine Dampfphase übergehen.
- Das Zielmaterial kann ein Metall, eine Keramik oder eine andere feste Substanz sein, je nach den gewünschten Eigenschaften der endgültigen Beschichtung.Der Verdampfungsprozess wird in der Regel in einer Vakuum- oder Niederdruckumgebung durchgeführt, um die Verunreinigung zu minimieren und einen sauberen Materialtransfer zu gewährleisten.
-
Transport von verdampften Atomen:
- Sobald das Zielmaterial verdampft ist, werden die Atome oder Moleküle durch die Reaktionskammer zum Substrat transportiert.Dieser Transport erfolgt in einer Vakuum- oder Niederdruckumgebung, um Störungen durch Hintergrundgase zu vermeiden.
- Die Transportphase ist entscheidend, da sie bestimmt, wie gleichmäßig das verdampfte Material das Substrat erreicht.Häufig wird die "Sichtlinienmethode" verwendet, bei der sich die verdampften Atome ohne nennenswerte Streuung direkt vom Ziel zum Substrat bewegen.
-
Reaktion (optional):
- Während der Transportphase können die verdampften Atome mit den in die Kammer eingebrachten Gasen, wie Sauerstoff oder Stickstoff, reagieren.Bei dieser Reaktion können Verbindungen wie Oxide, Nitride oder Karbide entstehen, je nach den gewünschten Eigenschaften der Beschichtung.
- Wird zum Beispiel ein Metalltarget verwendet und Sauerstoff zugeführt, kann die resultierende Beschichtung ein Metalloxid sein.Dieser Schritt ist fakultativ und hängt von der jeweiligen Anwendung und den gewünschten Beschichtungseigenschaften ab.
-
Abscheidung auf dem Substrat:
- Der letzte Schritt ist die Abscheidung des verdampften Materials auf dem Substrat.Die Atome oder Moleküle kondensieren auf der Substratoberfläche und bilden einen dünnen Film.Der Abscheidungsprozess wird kontrolliert, um die gewünschte Dicke, Haftung und Gleichmäßigkeit der Beschichtung zu gewährleisten.
- Das Substrat kann je nach Anwendung aus verschiedenen Materialien wie Metallen, Kunststoffen oder Keramiken bestehen.Der Abscheidungsprozess erfolgt häufig bei Temperaturen zwischen 50 und 600 Grad Celsius, je nach den beteiligten Materialien und den gewünschten Eigenschaften der Beschichtung.
-
Kontrolle und Überwachung:
- Der PVD-Prozess wird streng kontrolliert, um die Qualität der Endbeschichtung zu gewährleisten.Parameter wie Temperatur, Druck und Abscheidungsrate werden sorgfältig überwacht und angepasst.
- Zur Messung und Kontrolle der Dicke der abgeschiedenen Schicht werden Geräte wie Quarzkristall-Ratenmessgeräte eingesetzt.Darüber hinaus wird die Reaktionskammer oft auf sehr niedrige Drücke heruntergepumpt, um das Vorhandensein von Hintergrundgasen zu minimieren, die den Abscheidungsprozess stören könnten.
-
Vorteile von PVD:
- Dauerhaftigkeit:PVD-Beschichtungen sind für ihre Härte, Verschleißfestigkeit und Langlebigkeit bekannt und eignen sich daher für hoch beanspruchte Anwendungen.
- Korrosionsbeständigkeit:Die Beschichtungen bieten einen ausgezeichneten Schutz gegen Korrosion, selbst in rauen Umgebungen.
- Hochtemperatur-Toleranz:PVD-Beschichtungen können hohen Temperaturen standhalten und sind daher ideal für Anwendungen in der Luft- und Raumfahrt, in der Automobilindustrie und in industriellen Bereichen.
- Vielseitigkeit:Mit PVD kann eine breite Palette von Materialien, darunter Metalle, Keramiken und Verbundwerkstoffe, auf verschiedenen Substraten abgeschieden werden.
-
Anwendungen von PVD:
- Elektronik:PVD wird für die Abscheidung dünner Schichten in Halbleiterbauelementen, Solarzellen und Displays verwendet.
- Optik:Das Verfahren wird eingesetzt, um reflektierende oder antireflektierende Beschichtungen auf Linsen und Spiegeln herzustellen.
- Herstellung:PVD-Beschichtungen werden auf Schneidwerkzeuge, Formen und andere Komponenten aufgetragen, um deren Leistung und Langlebigkeit zu verbessern.
Zusammenfassend lässt sich sagen, dass das PVD-Verfahren eine äußerst kontrollierte und vielseitige Methode zur Abscheidung dünner Schichten mit außergewöhnlichen Eigenschaften ist.Durch die sorgfältige Steuerung der einzelnen Schritte - Verdampfung, Transport, Reaktion und Abscheidung - können die Hersteller Beschichtungen herstellen, die den spezifischen Anforderungen einer Vielzahl von Anwendungen entsprechen.Die Möglichkeit, Parameter wie Dicke, Haftung und Zusammensetzung zu steuern, macht PVD zu einem wertvollen Werkzeug in der modernen Fertigung und Technologie.
Zusammenfassende Tabelle:
Schritt | Beschreibung |
---|---|
Verdampfung | Das Zielmaterial wird mit Hochenergiequellen wie Elektronenstrahlen oder Lasern verdampft. |
Transport | Die verdampften Atome wandern durch ein Vakuum oder eine Niederdruckumgebung zum Substrat. |
Reaktion | Optionaler Schritt, bei dem verdampfte Atome mit Gasen reagieren und Verbindungen wie Oxide bilden. |
Abscheidung | Das verdampfte Material kondensiert auf dem Substrat und bildet eine dünne, dauerhafte Beschichtung. |
Kontrolle | Parameter wie Temperatur, Druck und Abscheidungsrate werden sorgfältig überwacht. |
Vorteile | Langlebigkeit, Korrosionsbeständigkeit, Hochtemperaturtoleranz und Vielseitigkeit. |
Anwendungen | Elektronik, Optik und Fertigung für verbesserte Leistung und Langlebigkeit. |
Entdecken Sie, wie PVD die Leistung Ihrer Produkte steigern kann. Kontaktieren Sie unsere Experten noch heute !