Die Sinterbeschichtung ist ein spezielles Verfahren zur Herstellung dichter, haltbarer und funktioneller Beschichtungen auf Substraten durch Verschmelzen von Partikeln, ohne dass das Grundmaterial geschmolzen wird.Bei diesem Verfahren wird eine Pulvermischung hergestellt, in die gewünschte Form gepresst und die Partikel werden durch Hitze und Druck miteinander verbunden.Das Ergebnis ist eine kohäsive Beschichtung mit geringer Porosität und verbesserten mechanischen Eigenschaften.Das Sintern ist in Branchen wie der Pulvermetallurgie, der Keramik und der additiven Fertigung weit verbreitet, um Beschichtungen mit hoher Festigkeit, Verschleißfestigkeit und thermischer Stabilität herzustellen.Im Folgenden werden die wichtigsten Schritte und Grundsätze des Sinterbeschichtungsprozesses im Detail erläutert.
Die wichtigsten Punkte werden erklärt:
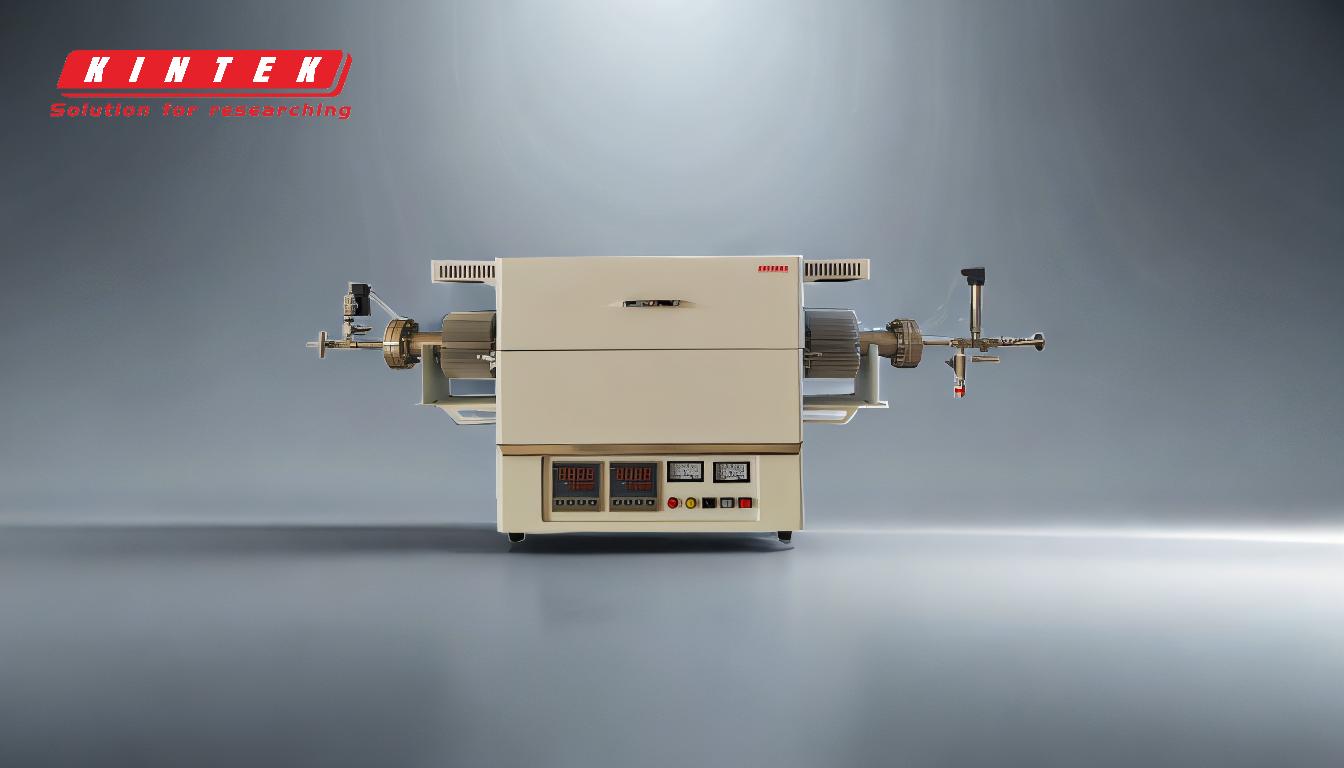
-
Herstellung des Pulvergemischs
- Das Verfahren beginnt mit der Herstellung einer Pulvermischung, die in der Regel das Ausgangsmaterial (z. B. Metall, Keramik oder Kunststoff) und ein Bindemittel (z. B. Wachs oder Polymer) enthält.
- Das Bindemittel sorgt dafür, dass die Pulverteilchen in der ersten Phase der Formgebung aneinander haften.
- Die Pulvermischung wird häufig so angepasst, dass die endgültige Beschichtung bestimmte Eigenschaften wie Härte, Wärmeleitfähigkeit oder Korrosionsbeständigkeit aufweist.
-
Verdichtung und Formgebung
- Das Pulvergemisch wird mit Hilfe von Methoden wie Presswerkzeugen, Kaltverschweißungen oder 3D-Lasern in die gewünschte Form gebracht.
- Dieser Schritt stellt sicher, dass die Pulverpartikel dicht gepackt und gleichmäßig verteilt sind, was für eine homogene Beschichtung entscheidend ist.
- Die Verdichtung erfolgt in der Regel in einer kontrollierten Atmosphäre, um Verunreinigungen und Oxidation zu vermeiden.
-
Erhitzung und Verfestigung
- Das verdichtete Pulver wird auf eine Temperatur knapp unter dem Schmelzpunkt des Ausgangsmaterials erhitzt.
- Durch diese Erhitzung wird die Diffusion von Atomen über die Partikelgrenzen hinweg aktiviert, wodurch die Partikel zusammenwachsen und sich verdichten.
- In einigen Fällen wird das Flüssigphasensintern (LPS) eingesetzt, bei dem ein sekundäres Material mit einem niedrigeren Schmelzpunkt schmilzt und die Lücken zwischen den Partikeln füllt, wodurch der Bindungsprozess beschleunigt wird.
-
Entfernung des Bindemittels
- Mit steigender Temperatur verdampft oder verbrennt das Bindemittel und hinterlässt eine poröse Struktur des Ausgangsmaterials.
- Dieser Schritt ist entscheidend, um sicherzustellen, dass die endgültige Beschichtung frei von Verunreinigungen ist und eine einheitliche Zusammensetzung aufweist.
-
Partikelfusion und Verdichtung
- Bei höheren Temperaturen beginnen die Primärteilchen an ihren Oberflächen zu verschmelzen und bilden eine feste Masse mit geringerer Porosität.
- Der Verschmelzungsprozess wird durch atomare Diffusion angetrieben, die die Bindungen zwischen den Partikeln stärkt und die mechanischen Eigenschaften der Beschichtung verbessert.
- Das Ergebnis ist eine dichte, kohäsive Beschichtung, die fest auf dem Substrat haftet.
-
Abkühlung und Erstarrung
- Nach Abschluss des Schmelzvorgangs muss das Material abkühlen und zu einer einheitlichen Masse erstarren.
- Eine kontrollierte Abkühlung ist wichtig, um thermische Spannungen zu vermeiden und sicherzustellen, dass die Beschichtung ihre gewünschten Eigenschaften behält.
- Das Endprodukt ist eine harte, dauerhafte Beschichtung mit verbesserter Festigkeit, Verschleißfestigkeit und thermischer Stabilität.
-
Anwendungen von Sinterbeschichtungen
- Sinterbeschichtungen sind in Branchen wie der Luft- und Raumfahrt, der Automobilindustrie und der Elektronik für Anwendungen, die Hochleistungsmaterialien erfordern, weit verbreitet.
- Beispiele sind verschleißfeste Beschichtungen für Schneidwerkzeuge, Wärmedämmschichten für Motorkomponenten und korrosionsbeständige Beschichtungen für Industrieanlagen.
- Das Verfahren wird auch in der additiven Fertigung eingesetzt, um komplexe, hochfeste Teile mit präzisen Geometrien herzustellen.
-
Vorteile von Sinterbeschichtungen
- Das Sinterverfahren ermöglicht die Herstellung von Beschichtungen mit maßgeschneiderten Eigenschaften, wie Härte, Porosität und Wärmeleitfähigkeit.
- Es ist kostengünstig für die Herstellung großer Mengen hochwertiger Beschichtungen.
- Das Verfahren kann für eine breite Palette von Materialien eingesetzt werden, darunter Metalle, Keramik und Verbundwerkstoffe.
Durch diese Schritte erreichen Sinterbeschichtungen ein ausgewogenes Verhältnis von Festigkeit, Haltbarkeit und Funktionalität, was sie zu einer wertvollen Lösung für eine Vielzahl von industriellen Anwendungen macht.
Zusammenfassende Tabelle:
Schritt | Beschreibung |
---|---|
1.Zubereitung des Pulvers | Primärmaterial (z. B. Metall, Keramik) mit einem Bindemittel (z. B. Wachs) mischen. |
2.Verdichtung und Formgebung | Verdichten Sie das Pulver mit Presswerkzeugen oder 3D-gedruckten Lasern in die gewünschte Form. |
3.Erhitzung und Verfestigung | Erhitzen bis unter den Schmelzpunkt, um die Partikelbindung und Verdichtung zu ermöglichen. |
4.Entfernung des Bindemittels | Das Bindemittel verdampft und hinterlässt eine poröse Struktur des Primärmaterials. |
5.Partikelfusion | Die Partikel verschmelzen an der Oberfläche und bilden eine dichte, kohäsive Schicht. |
6.Abkühlung und Erstarrung | Die kontrollierte Abkühlung gewährleistet, dass die Beschichtung ihre Festigkeit und Haltbarkeit behält. |
7.Anwendungen | Wird in der Luft- und Raumfahrt, der Automobilindustrie und der Elektronik für verschleißfeste Beschichtungen verwendet. |
8.Vorteile | Maßgeschneiderte Eigenschaften, kostengünstig und kompatibel mit Metallen, Keramiken usw. |
Entdecken Sie, wie Sinterbeschichtungen Ihre industriellen Anwendungen verbessern können. Kontaktieren Sie uns noch heute !