Das Sintern von Hochleistungskeramik ist ein entscheidender Schritt bei der Umwandlung eines Grünlings (ungebrannter keramischer Pressling) in ein dichtes, festes und funktionelles Keramikmaterial. Dabei wird der keramische Pulverpressling auf hohe Temperaturen erhitzt, die in der Regel unter seinem Schmelzpunkt liegen, um die Partikelbindung und Verdichtung zu erleichtern. Der Prozess wird von verschiedenen Faktoren wie Temperatur, Druck, Partikelgröße und Atmosphäre beeinflusst, die zusammengenommen die endgültigen Eigenschaften der gesinterten Keramik bestimmen. Zu den wichtigsten Schritten gehören die Vorbereitung des Pulverpresslings, die Entfernung des Bindemittels, das Sintern bei hohen Temperaturen und das kontrollierte Abkühlen. Ziel ist es, eine Keramik mit geringer Porosität und hoher Festigkeit zu erhalten, die die gewünschte Mikrostruktur und die gewünschten mechanischen Eigenschaften aufweist.
Die wichtigsten Punkte werden erklärt:
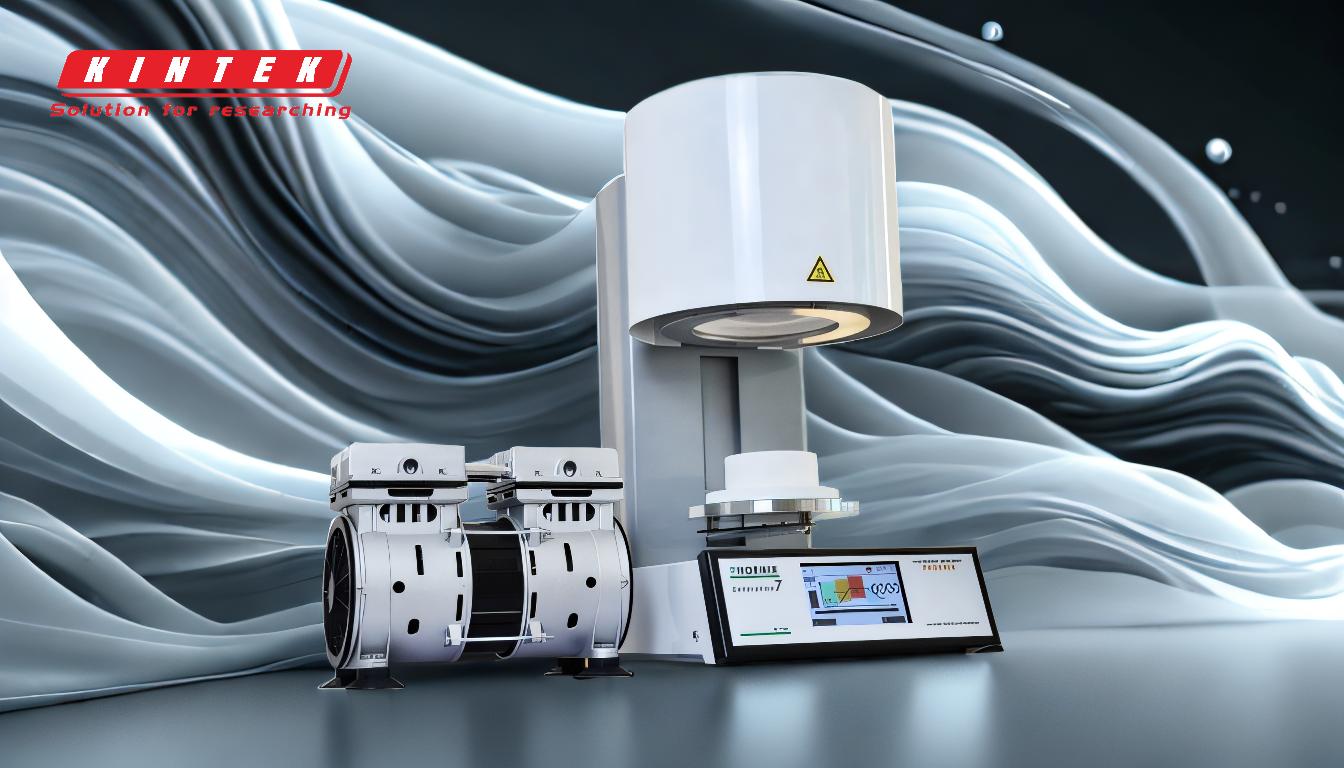
-
Vorbereitung des Pulverpresslings:
- Das Verfahren beginnt mit der Herstellung eines keramischen Pulverpresslings, der oft auch als Grünling bezeichnet wird. Dazu wird das Keramikpulver mit Bindemitteln, Entflockungsmitteln und Wasser zu einem Schlicker vermischt, der dann sprühgetrocknet wird, um ein fließfähiges Pulver zu erhalten.
- Das sprühgetrocknete Pulver wird in eine Form gepresst, um eine zusammenhängende Gestalt zu erhalten. Der Grünling hat eine gewisse Anfangsporosität, die die Endporosität nach dem Sintern beeinflusst.
-
Entfernen des Bindemittels (Entbindern):
- Vor dem Sintern wird der Grünling bei niedriger Temperatur erhitzt, um die organischen Bindemittel und andere flüchtige Bestandteile zu entfernen. Dieser Schritt ist entscheidend, um Defekte wie Rissbildung oder Aufblähung während des Hochtemperatursinterprozesses zu vermeiden.
- Der Entbinderungsprozess muss sorgfältig kontrolliert werden, um eine vollständige Entfernung der Bindemittel zu gewährleisten, ohne den Grünling zu beschädigen.
-
Sintern bei hoher Temperatur:
- Das Herzstück des Sinterprozesses ist das Erhitzen des Grünlings auf eine Temperatur knapp unter seinem Schmelzpunkt. Diese hohe Temperatur begünstigt die Diffusion der Partikel, was zu einer Verdichtung und zur Bildung starker Bindungen zwischen den Keramikpartikeln führt.
- Die Sintertemperatur, die Sinterdauer und die Atmosphäre (z. B. Luft, Vakuum oder Inertgas) sind entscheidende Parameter, die die endgültigen Eigenschaften der Keramik beeinflussen. Höhere Temperaturen und längere Sinterzeiten führen im Allgemeinen zu einer stärkeren Verdichtung, müssen aber gegen das Risiko eines übermäßigen Kornwachstums abgewogen werden.
-
Partikelverschmelzung und Verdichtung:
- Während des Sinterns verdichten und verschmelzen die Partikel durch Mechanismen wie Festkörperdiffusion, Korngrenzenwanderung und in einigen Fällen durch Flüssigphasensintern (LPS). LPS beinhaltet das Vorhandensein einer flüssigen Phase, die die Umlagerung und Verdichtung der Partikel fördert.
- Die Entscheidung zwischen Feststoffsintern und LPS hängt von der Materialzusammensetzung und den gewünschten Eigenschaften des Endprodukts ab.
-
Abkühlung und Erstarrung:
- Nach dem Sintern wird die Keramik mit einer kontrollierten Geschwindigkeit abgekühlt, damit sie zu einer einheitlichen Masse erstarrt. Die Abkühlgeschwindigkeit kann sich auf die Mikrostruktur und die mechanischen Eigenschaften der Keramik auswirken, z. B. auf die Zugfestigkeit und die Kerbschlagarbeit.
- Durch die richtige Abkühlung wird sichergestellt, dass die Keramik ihre gewünschten Eigenschaften beibehält und thermische Spannungen vermieden werden, die zu Rissen führen könnten.
-
Post-Sintering-Verfahren:
- Nach dem Sintern kann das keramische Teil einer zusätzlichen Bearbeitung mit Diamantwerkzeugen oder Ultraschallverfahren unterzogen werden, um präzise Abmessungen und Oberflächengüten zu erzielen.
- In einigen Fällen werden die Keramikteile für den Zusammenbau mit anderen Komponenten metallisiert und gelötet, um ihre Funktionalität in bestimmten Anwendungen zu verbessern.
-
Faktoren, die das Sintern beeinflussen:
- Temperatur: Bestimmt die Kinetik der Sinterung und die endgültigen Materialeigenschaften. Höhere Temperaturen erhöhen im Allgemeinen die Verdichtung, können aber auch zu Kornwachstum führen.
- Druck: Die Anwendung von Druck während des Sinterns kann die Porosität verringern und die Verdichtung erhöhen, insbesondere bei Verfahren wie Heißpressen oder Funkenplasmasintern.
- Partikelgröße: Kleinere Partikel haben eine höhere Oberflächenenergie, was zu einer schnelleren Verdichtung und einem besseren Sinterverhalten führt.
- Atmosphäre: Die Sinteratmosphäre (z. B. Luft, Vakuum oder Inertgas) kann die Oxidation, Reduktion oder andere chemische Reaktionen während des Sinterns beeinflussen.
- Zusammensetzung: Die Homogenität und die chemische Zusammensetzung des Keramikpulvers beeinflussen das Sinterverhalten und die endgültigen Eigenschaften des Materials.
-
Optimierung der Sinterparameter:
- Der optimale Sinterprozess wird durch das Abwägen von Faktoren wie Temperatur, Druck und Zeit bestimmt, um die gewünschten Produkteigenschaften zu erreichen. Feinere Pulver und höhere Temperaturen können die Verdichtung erhöhen, aber die Menge der flüssigen Phase muss sorgfältig kontrolliert werden, um Defekte zu vermeiden.
- Die Wahl des Sinterverfahrens (z. B. konventionelles Sintern, Heißpressen oder Spark-Plasma-Sintern) hängt von den spezifischen Anforderungen der Anwendung und des zu verarbeitenden Materials ab.
Wenn die Hersteller diese Schlüsselaspekte des Sinterprozesses verstehen und kontrollieren, können sie Hochleistungskeramiken mit maßgeschneiderten Eigenschaften für eine Vielzahl von Anwendungen herstellen, von elektronischen Komponenten bis hin zu Strukturmaterialien.
Zusammenfassende Tabelle:
Schritt | Beschreibung |
---|---|
Vorbereitung des Pulvers Kompakt | Mischen des Keramikpulvers mit Bindemitteln, Entflockungsmitteln und Wasser, um eine Aufschlämmung zu bilden. |
Entfernen von Bindemitteln (Entbindern) | Erhitzen des Grünlings zur Entfernung organischer Bindemittel, um Defekte während des Sinterns zu vermeiden. |
Sintern bei hoher Temperatur | Erhitzen bis knapp unter den Schmelzpunkt, um die Partikelbindung und Verdichtung zu ermöglichen. |
Partikelverschmelzung und Verdichtung | Die Partikel verbinden sich durch Festkörperdiffusion oder Flüssigphasensintern (LPS). |
Abkühlung und Erstarrung | Durch kontrollierte Abkühlung werden das gewünschte Mikrogefüge und die mechanischen Eigenschaften sichergestellt. |
Post-Sintering-Prozesse | Spanende Bearbeitung, Metallisierung oder Hartlöten für präzise Abmessungen und Funktionalität. |
Faktoren, die die Sinterung beeinflussen | Temperatur, Druck, Partikelgröße, Atmosphäre und Materialzusammensetzung. |
Optimierung der Parameter | Abstimmung von Temperatur, Druck und Zeit für maßgeschneiderte Keramikeigenschaften. |
Benötigen Sie Hilfe bei der Optimierung Ihres keramischen Sinterprozesses? Kontaktieren Sie noch heute unsere Experten für maßgeschneiderte Lösungen!