Die Standarddicke der Beschichtung liegt in der Regel im Bereich von 0,0005 Zoll bis 0,0015 Zoll (0,012 mm bis 0,038 mm) für technische Anwendungen.Dieser Schichtdickenbereich wird häufig gewählt, um ein Gleichgewicht zwischen Haltbarkeit, Funktionalität und Kosteneffizienz herzustellen.Außerdem kann die Härte der Beschichtung zwischen 48 bis 52 Rockwell C aber bei einer Wärmebehandlung bei etwa 750°F (400°C) eine Stunde lang, kann die Härte erheblich ansteigen auf 58 bis 64 Rockwell C .Durch diese Wärmebehandlung werden die mechanischen Eigenschaften der Beschichtung verbessert, so dass sie sich besser für anspruchsvolle Anwendungen eignet.
Die wichtigsten Punkte erklärt:
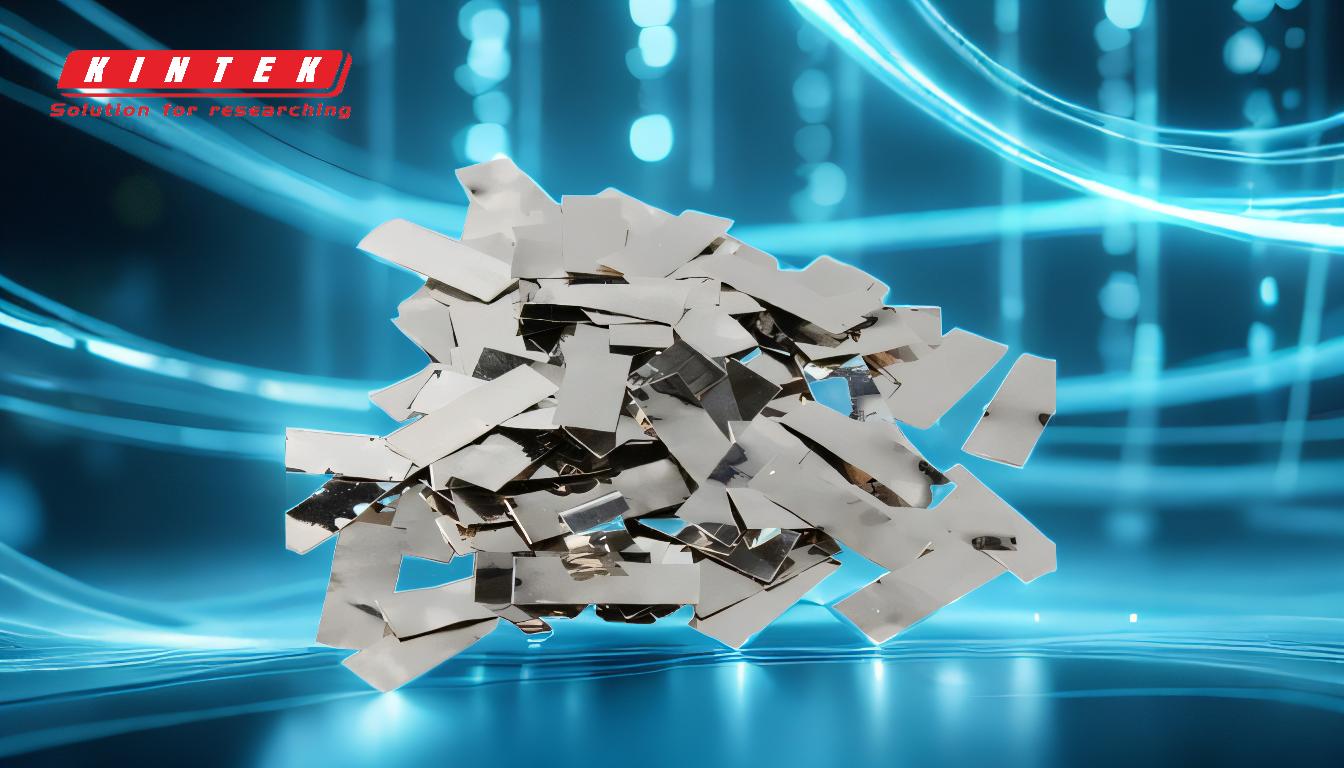
-
Standard-Dickenspektrum:
- Die typische Dicke für Beschichtungen in technischen Anwendungen beträgt 0,0005 Zoll bis 0,0015 Zoll (0,012 mm bis 0,038 mm) .Dieser Bereich ist weithin akzeptiert, da er für die meisten industriellen Anwendungen ausreichenden Schutz und Leistung bietet.
- Dünnere Beschichtungen (näher an 0,0005 Zoll) werden häufig für Anwendungen verwendet, bei denen nur eine minimale Materialzugabe erforderlich ist, während dickere Beschichtungen (bis zu 0,0015 Zoll) für anspruchsvollere Umgebungen gewählt werden.
-
Härte der Beschichtung:
- Die Härte des Beschichtungsmaterials liegt normalerweise zwischen 48 bis 52 Rockwell C in seinem unbehandelten Zustand.Dieser Härtegrad ist für viele allgemeine Anwendungen ausreichend.
- Die Härte ist ein entscheidender Faktor, denn sie bestimmt die Verschleiß-, Abrieb- und Verformungsbeständigkeit der Beschichtung, die für mechanisch beanspruchte Bauteile unerlässlich ist.
-
Wärmebehandlung und Härteerhöhung:
- Wenn die Beschichtung wärmebehandelt wird bei 750°F (400°C) eine Stunde lang, kann die Härte deutlich auf 58 bis 64 Rockwell C .
- Durch die Wärmebehandlung wird das Mikrogefüge der Beschichtung verändert, wodurch sich ihre mechanischen Eigenschaften wie Härte, Verschleißfestigkeit und Haltbarkeit verbessern.Dadurch eignet sich die Beschichtung für härtere Betriebsbedingungen, z. B. in Umgebungen mit hoher Beanspruchung oder hohen Temperaturen.
-
Überlegungen zur Anwendung:
-
Die Wahl der Beschichtungsdicke und -härte hängt von den spezifischen Anforderungen der Anwendung ab.Zum Beispiel:
- Dünnere Beschichtungen werden häufig in der Elektronik oder bei Präzisionsbauteilen verwendet, bei denen die Maßhaltigkeit entscheidend ist.
- Dickere Beschichtungen werden bevorzugt für schwere Maschinen oder Automobilteile verwendet, die rauen Bedingungen ausgesetzt sind.
- Wärmebehandelte Beschichtungen sind ideal für Anwendungen, die eine erhöhte Verschleißfestigkeit erfordern, wie z. B. Schneidwerkzeuge oder Industrieanlagen.
-
Die Wahl der Beschichtungsdicke und -härte hängt von den spezifischen Anforderungen der Anwendung ab.Zum Beispiel:
-
Abwägung von Kosten und Leistung:
- Stärkere Beschichtungen und Wärmebehandlungsverfahren erhöhen die Material- und Verarbeitungskosten.Daher sollte bei der Wahl der Schichtdicke und der Härte ein Gleichgewicht zwischen Leistungsanforderungen und Budgetbeschränkungen gefunden werden.
- Bei kostensensiblen Anwendungen kann eine unbehandelte Beschichtung mit Standardstärke ausreichen, während Hochleistungsanwendungen die zusätzlichen Kosten einer Wärmebehandlung rechtfertigen können.
Durch die Kenntnis dieser Schlüsselpunkte können die Käufer von Geräten und Verbrauchsmaterialien fundierte Entscheidungen über die Beschichtungsspezifikationen treffen, die ihren spezifischen Anforderungen entsprechen.
Zusammenfassende Tabelle:
Parameter | Einzelheiten |
---|---|
Standard-Dicke | 0,0005 Zoll bis 0,0015 Zoll (0,012 mm bis 0,038 mm) |
Unbehandelt Härte | 48 bis 52 Rockwell C |
Wärmebehandelte Härte | 58 bis 64 Rockwell C (nach Wärmebehandlung bei 750°F/400°C für 1 Stunde) |
Anwendungen | Elektronik, Präzisionskomponenten, Schwermaschinen, Automobilteile |
Kostenüberlegungen | Stärkere Beschichtungen und Wärmebehandlungen erhöhen die Kosten, verbessern aber die Leistung. |
Benötigen Sie Hilfe bei der Auswahl der richtigen Beschichtung für Ihre Anwendung? Kontaktieren Sie noch heute unsere Experten für maßgeschneiderte Lösungen!