Die physikalische Gasphasenabscheidung (PVD) ist ein vakuumbasiertes Beschichtungsverfahren, mit dem dünne Materialschichten auf ein Substrat aufgebracht werden.Bei diesem Verfahren wird ein festes Vorläufermaterial in eine Dampfphase umgewandelt, in der Regel durch Methoden wie thermisches Verdampfen oder Sputtern, und dann wird der Dampf auf dem Substrat kondensiert, um eine dünne, haltbare und leistungsstarke Beschichtung zu bilden.PVD wird häufig in Branchen eingesetzt, die präzise, hochwertige Beschichtungen benötigen, z. B. in der Elektronik, Optik und Werkzeugherstellung, da sich mit diesem Verfahren dünne Schichten mit hervorragender Haftung, Gleichmäßigkeit und Beständigkeit gegen Verschleiß und Korrosion herstellen lassen.
Die wichtigsten Punkte erklärt:
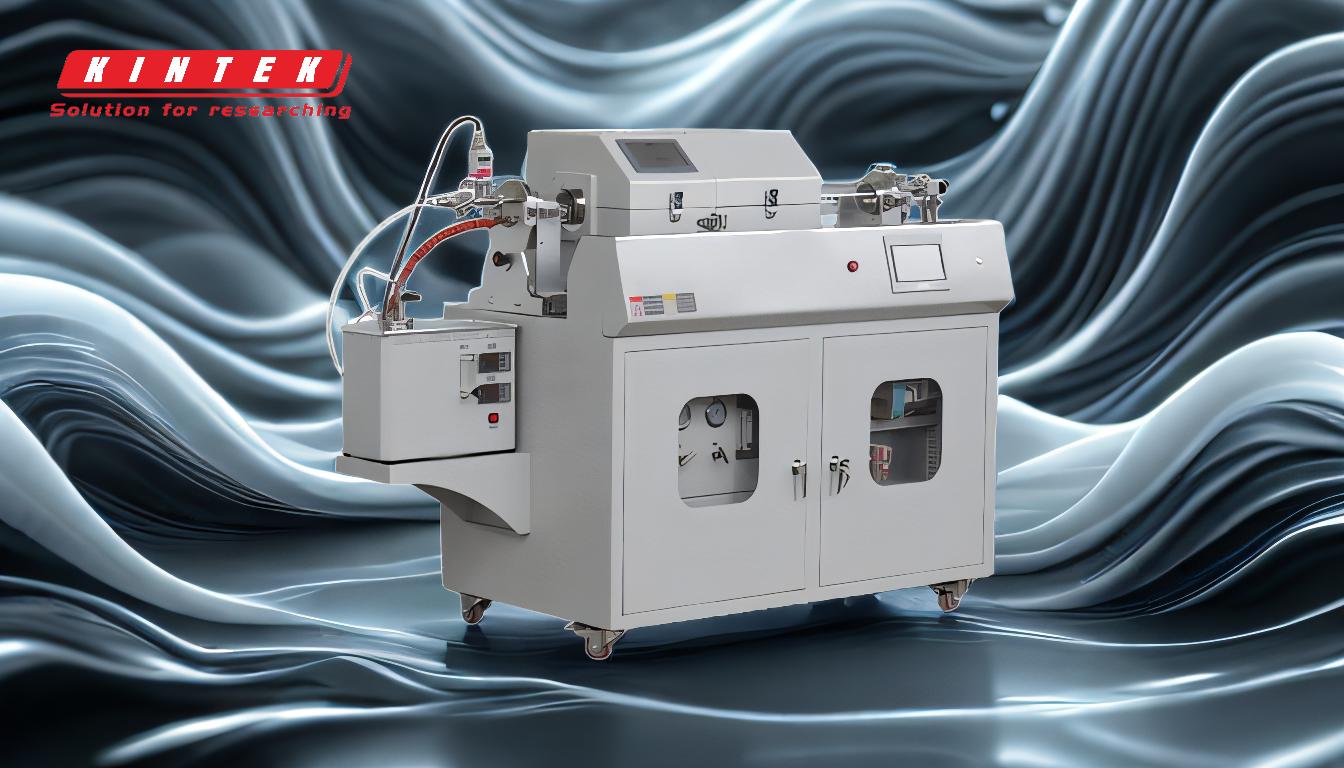
-
Grundlegendes Konzept von PVD:
- PVD ist ein vakuumbasiertes Verfahren, bei dem ein festes Material (Vorläufer oder Target) verdampft und dann auf ein Substrat aufgebracht wird, um eine dünne Schicht zu bilden.
- Die Verdampfung des festen Materials kann durch Methoden wie thermisches Verdampfen, Sputtern oder Laserablation erfolgen.
- Der Prozess findet in einer Vakuumkammer statt, um Verunreinigungen zu minimieren und eine genaue Kontrolle über die Abscheidung zu gewährleisten.
-
Beteiligte Schritte bei PVD:
- Verdampfung:Das feste Vorläufermaterial wird mit Hilfe von Energiequellen wie Hochleistungselektrizität, Lasern oder thermischer Erwärmung in eine Dampfphase umgewandelt.
- Transport:Die verdampften Atome oder Moleküle wandern durch die Vakuumkammer zum Substrat.
- Kondensation:Der Dampf kondensiert auf dem Substrat und bildet eine dünne, gleichmäßige Schicht.
- Kontrolle:Die Schichtdicke und die Abscheiderate werden mit Hilfe von Geräten wie Quarzkristall-Monitoren überwacht und gesteuert.
-
Schlüsselmethoden der PVD:
- Thermische Verdampfung:Das Targetmaterial wird erhitzt, bis es verdampft, und der Dampf wird auf dem Substrat abgeschieden.
- Sputtern:Hochenergetische Ionen beschießen das Zielmaterial und lösen Atome heraus, die sich dann auf dem Substrat ablagern.
- Laserablation:Mit Hilfe eines Lasers wird das Zielmaterial verdampft, das sich dann auf dem Substrat ablagert.
-
Vorteile von PVD:
- Hochwertige Beschichtungen:PVD erzeugt dünne Schichten mit hervorragender Haftung, Gleichmäßigkeit und Haltbarkeit.
- Vielseitigkeit:Es kann eine breite Palette von Materialien abscheiden, darunter Metalle, Keramiken und Legierungen.
- Materialien mit hohem Schmelzpunkt:PVD ist in der Lage, Materialien mit hohen Schmelzpunkten zu bearbeiten, die mit anderen Methoden nur schwer zu verarbeiten sind.
- Korrosions- und Verschleißbeständigkeit:Die Beschichtungen sind äußerst korrosions- und verschleißfest und widerstehen hohen Temperaturen.
-
Anwendungen von PVD:
- Elektronik:Wird für die Abscheidung von leitenden und isolierenden Schichten in Halbleitergeräten verwendet.
- Optik:Angewandt bei der Herstellung von Antireflexions- und Reflexionsschichten für Linsen und Spiegel.
- Werkzeugbau:Verbessert die Haltbarkeit und Leistung von Schneidwerkzeugen und Formen.
- Dekorative Beschichtungen:Wird zur Herstellung kratzfester und ästhetisch ansprechender Oberflächen auf Konsumgütern verwendet.
-
Ökologische und betriebliche Erwägungen:
- Vakuum Bedingungen:PVD erfordert eine Hochvakuumumgebung, um Verunreinigungen zu vermeiden und eine genaue Kontrolle über den Abscheidungsprozess zu gewährleisten.
- Niedrige Temperaturen:Im Gegensatz zu einigen anderen Beschichtungsverfahren arbeitet PVD bei relativ niedrigen Temperaturen und eignet sich daher für temperaturempfindliche Substrate.
- Energie-Effizienz:PVD erfordert zwar erhebliche Energie für die Verdampfung, gilt aber im Allgemeinen als umweltfreundlich, da keine schädlichen Nebenprodukte entstehen.
-
Herausforderungen und Beschränkungen:
- Komplexe Ausrüstung:PVD-Systeme sind oft komplex und erfordern erhebliche Investitionen in Ausrüstung und Wartung.
- Begrenzte Abscheideraten:Die Abscheideraten können im Vergleich zu anderen Beschichtungsmethoden langsamer sein, was den Produktionsdurchsatz beeinträchtigen kann.
- Einschränkungen des Substrats:Das Verfahren ist möglicherweise nicht für alle Substratmaterialien geeignet, insbesondere nicht für solche, die den Vakuumbedingungen nicht standhalten.
Wenn man diese Kernpunkte versteht, kann man das Arbeitskonzept von PVD und seine Bedeutung in der modernen Fertigung und Technologie nachvollziehen.Die Fähigkeit des Verfahrens, qualitativ hochwertige, dauerhafte Beschichtungen mit präziser Kontrolle herzustellen, macht es zu einer wertvollen Technik in verschiedenen Branchen.
Zusammenfassende Tabelle:
Aspekt | Einzelheiten |
---|---|
Verfahren | Umwandlung von festem Material in Dampf, Ablagerung auf dem Substrat im Vakuum. |
Wichtigste Methoden | Thermisches Verdampfen, Sputtern, Laserablation. |
Vorteile | Hochwertige Beschichtungen, Vielseitigkeit, Korrosions- und Verschleißfestigkeit. |
Anwendungen | Elektronik, Optik, Werkzeugherstellung, dekorative Beschichtungen. |
Herausforderungen | Komplexe Ausrüstung, langsamere Abscheidungsraten, Substratbeschränkungen. |
Auswirkungen auf die Umwelt | Energieeffizient, keine schädlichen Nebenprodukte, arbeitet bei niedrigen Temperaturen. |
Entdecken Sie, wie PVD Ihren Fertigungsprozess verbessern kann. Kontaktieren Sie unsere Experten noch heute !