Das Magnetronsputtern ist eine vielseitige und weit verbreitete Technik für die Abscheidung dünner Schichten in verschiedenen Industriezweigen wie der Mikroelektronik, der Optik und der Bearbeitung.Die Dicke der durch Magnetronsputtern hergestellten Schichten reicht in der Regel von Angström bis zu Mikrometern und wird von Faktoren wie Sputterdauer, Materialmasse, Energieniveau der Beschichtungspartikel und Prozessparametern wie Target-Substrat-Abstand, Ionenenergie und Gasdruck beeinflusst.Mit diesem Verfahren lassen sich sowohl Einstoff- als auch Mehrstoffschichten herstellen, so dass es sich für Anwendungen von Halbleiterbauelementen bis hin zu dekorativen und funktionellen Schichten eignet.
Die wichtigsten Punkte werden erklärt:
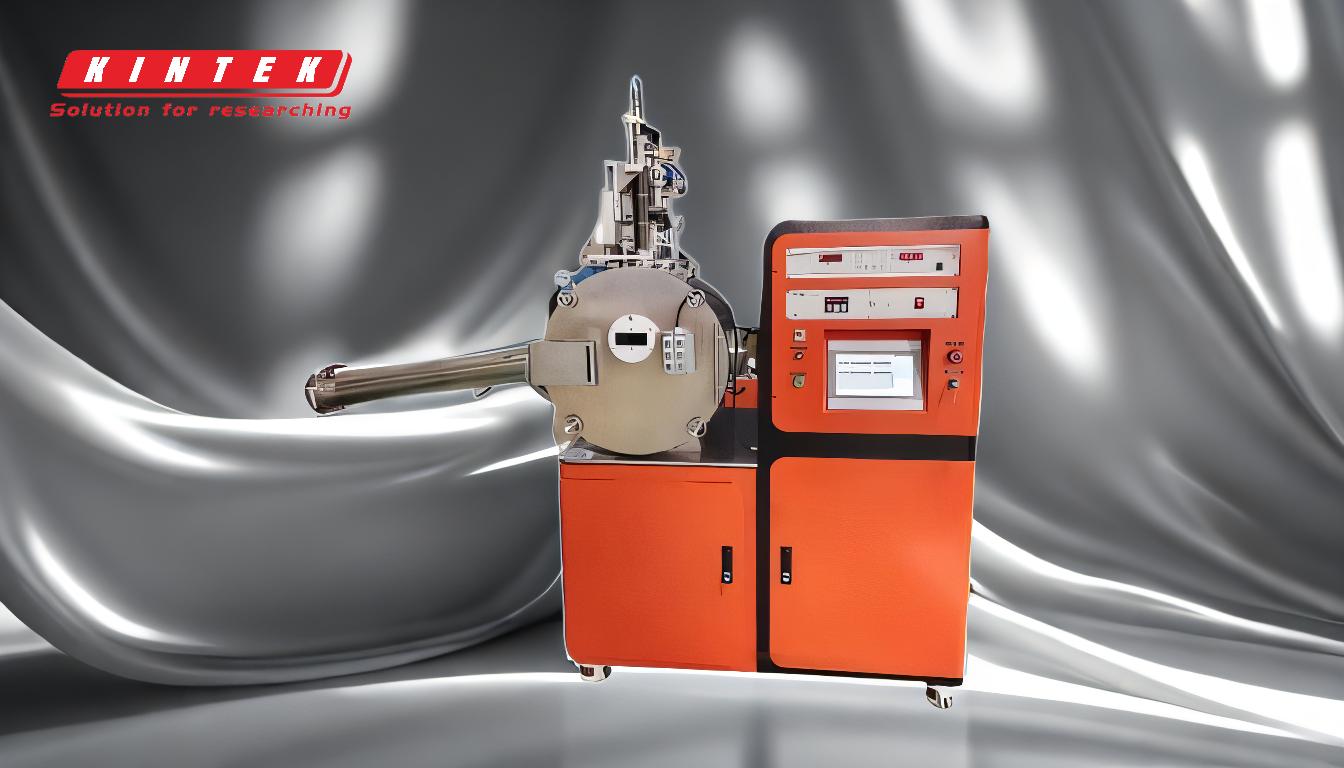
-
Dickenbereich von Magnetron-Sputter-Schichten:
- Durch Magnetronsputtern werden Schichten mit Dicken von Angström bis zu Mikrometern .
- Dieser Bereich ermöglicht eine präzise Kontrolle der Schichtdicke und eignet sich daher für Anwendungen, die ultradünne oder dickere Funktionsschichten erfordern.
-
Faktoren, die die Beschichtungsdicke beeinflussen:
- Sputtern Dauer:Längere Sputterzeiten führen im Allgemeinen zu dickeren Schichten.
- Werkstoff Masse:Schwerere Materialien benötigen möglicherweise mehr Energie zum Sputtern, was sich auf die Abscheidungsrate und die Schichtdicke auswirkt.
- Energieniveaus von Beschichtungspartikeln:Höhere Energieniveaus (im Bereich von zehn bis tausenden von Elektronenvolt) können die Abscheiderate erhöhen und die Schichtdicke beeinflussen.
-
Prozess-Parameter:
- Ziel-Substrat-Abstand:Geringere Abstände können die Abscheiderate erhöhen, aber die Gleichmäßigkeit beeinträchtigen.
- Ionenenergie:Eine höhere Ionenenergie kann die Filmdichte und die Haftung verbessern, kann aber auch die Gleichmäßigkeit der Schichtdicke beeinträchtigen.
- Gasdruck:Ein optimaler Gasdruck ist entscheidend für eine gleichbleibende Schichtdicke und Qualität.
-
Anwendungen, die bestimmte Schichtdickenbereiche erfordern:
- Halbleiterindustrie:Dünne Schichten im Bereich von Angström bis Nanometer werden für integrierte Schaltkreise und die Herstellung von Festplatten verwendet.
- Optische Filme:Beschichtungen mit präziser Dickenkontrolle sind für Anwendungen wie strahlungsarmes Glas und transparentes, leitfähiges Glas unerlässlich.
- Dekorative und funktionelle Folien:Dickere Beschichtungen (bis zu Mikron) werden für hochwertige Dekorationen, verschleißfeste Folien und superharte Folien auf Werkzeugen und Formen verwendet.
-
Gleichmäßigkeit und Kontrolle:
- Das Erreichen einer gleichmäßigen Schichtdicke ist beim Magnetron-Sputtern von entscheidender Bedeutung.Faktoren wie Target-Erosion, Temperatur und geometrische Parameter (z. B. Target-Substrat-Ausrichtung) spielen eine wichtige Rolle bei der Gewährleistung einer gleichmäßigen Schichtqualität.
- Fortgeschrittene Systeme beinhalten oft Echtzeit-Überwachungs- und Feedback-Mechanismen, um die Schichtdicke über große Substrate hinweg gleichmäßig zu halten.
-
Mehrschichtige und zusammengesetzte Beschichtungen:
- Durch Magnetronsputtern lassen sich ein- oder mehrlagige Schichten , die die Schaffung komplexer Strukturen mit maßgeschneiderten Eigenschaften ermöglichen.
- So können Schichtfolien beispielsweise Materialien mit unterschiedlichen Brechungsindizes für optische Anwendungen kombinieren oder harte und schmierende Schichten für verschleißfeste Beschichtungen integrieren.
-
Industrie-spezifische Beispiele:
- Mikroelektronik:Für die Abscheidung dünner Schichten in integrierten Schaltungen und Speichergeräten.
- Optik:Wird bei der Herstellung von Antireflexionsbeschichtungen, Spiegeln und optischen Filtern verwendet.
- Bearbeitung:Wird für die Ablagerung superharter und selbstschmierender Filme auf Schneidwerkzeugen und Formen verwendet.
- Automobilindustrie und Luft- und Raumfahrt:Wird für verschleißfeste und schützende Beschichtungen auf kritischen Komponenten verwendet.
-
Forschung und Entwicklung:
- Das Magnetronsputtern ist für die Weiterentwicklung von Forschungsbereichen wie Hochtemperatur-Supraleiterschichten, ferroelektrischen Schichten und Solarzellenmaterialien von entscheidender Bedeutung.
- Seine Fähigkeit, Schichten mit präziser Dicke und Zusammensetzung herzustellen, macht es zu einem Schlüsselinstrument für die Entwicklung von Materialien der nächsten Generation.
Zusammenfassend lässt sich sagen, dass das Magnetronsputtern eine außergewöhnliche Flexibilität bei der Steuerung der Schichtdicke bietet, was es für eine breite Palette von Industrie- und Forschungsanwendungen unverzichtbar macht.Durch das Verständnis und die Optimierung der Faktoren, die die Schichtdicke beeinflussen, können Hersteller und Forscher die Beschichtungen so anpassen, dass sie den spezifischen Leistungsanforderungen entsprechen.
Zusammenfassende Tabelle:
Aspekt | Einzelheiten |
---|---|
Dickenbereich | Angström bis Mikrometer |
Wichtige Einflussfaktoren | Sputterdauer, Materialmasse, Energieniveaus, Prozessparameter |
Anwendungen | Mikroelektronik, Optik, Bearbeitung, dekorative Folien |
Gleichmäßigkeit & Kontrolle | Echtzeit-Überwachung, Target-Substrat-Ausrichtung, Gasdruckoptimierung |
Mehrschichtige Beschichtungen | Ein-Material- oder Verbundfolien für maßgeschneiderte Eigenschaften |
Industrie Beispiele | Halbleiterbauelemente, optische Filter, verschleißfeste Werkzeuge |
Optimieren Sie Ihren Dünnschichtabscheidungsprozess mit Magnetronsputtern. Kontaktieren Sie unsere Experten noch heute !