Eine Vakuumumgebung ist für die Abscheidung dünner Schichten unerlässlich, um hochwertige, reine und haftende Schichten zu gewährleisten. Zu den Hauptgründen für die Verwendung eines Vakuums gehören die Verringerung der Dichte der Gasmoleküle, wodurch die verdampften Atome längere Strecken ohne Zusammenstöße zurücklegen können (langer mittlerer freier Weg), und die Minimierung der Verunreinigung durch unerwünschte Stoffe wie Sauerstoff, Stickstoff und Kohlendioxid. Diese Verunreinigungen können den Abscheidungsprozess stören, die Schichthaftung schwächen oder Verunreinigungen einbringen. Darüber hinaus ermöglicht das Vakuum eine präzise Steuerung der Gas- und Dampfzusammensetzung, erleichtert eine Niederdruck-Plasmaumgebung und gewährleistet eine effiziente Steuerung des Massenstroms, was alles entscheidend ist, um gleichmäßige und leistungsstarke Dünnschichten zu erzielen.
Die wichtigsten Punkte werden erklärt:
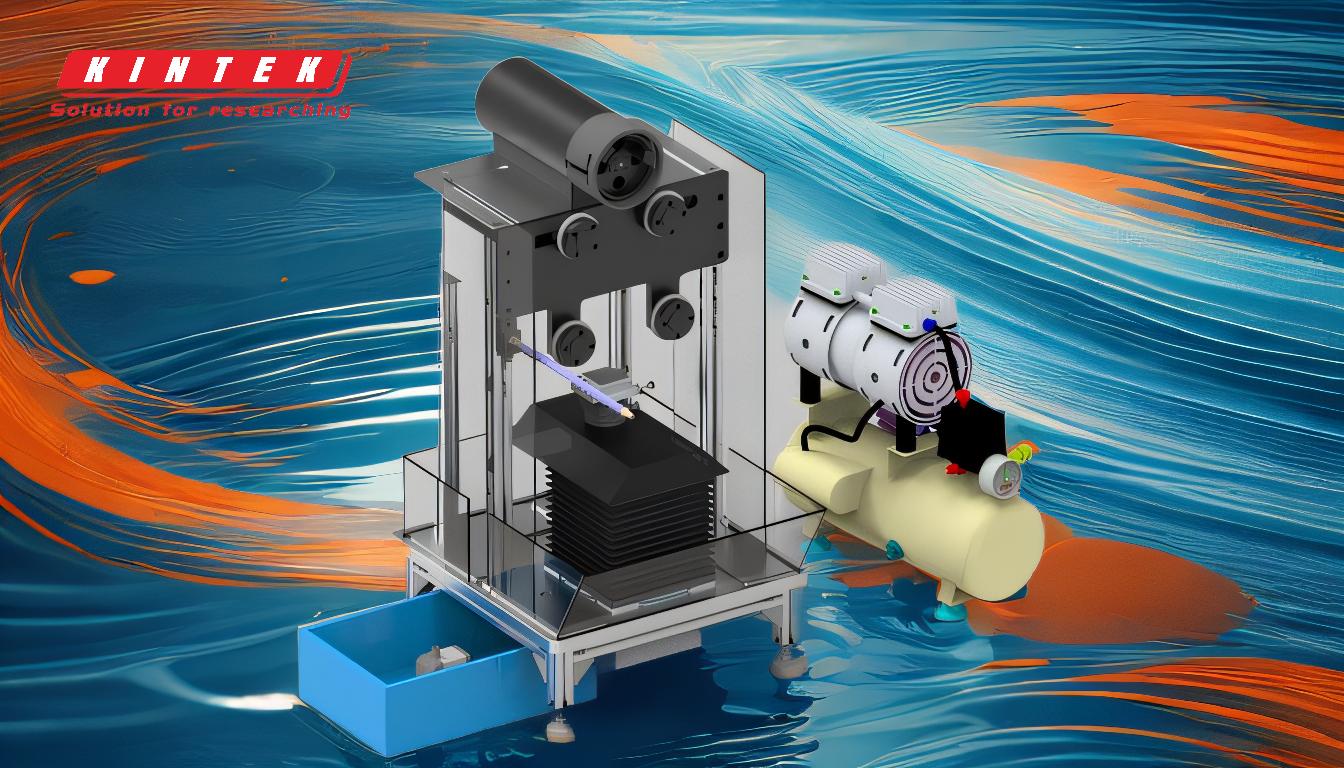
-
Langer mittelfreier Weg für verdampfte Atome:
- In einem Vakuum ist der Gasdruck erheblich reduziert, wodurch die Dichte der Gasmoleküle in der Kammer abnimmt.
- Durch diese Verkleinerung können die verdampften Atome oder Moleküle längere Strecken zurücklegen, ohne mit anderen Teilchen zusammenzustoßen, so dass sie das Substrat gleichmäßig erreichen.
- Ohne Vakuum würden die Atome bei häufigen Zusammenstößen streuen, was zu ungleichmäßiger Abscheidung und möglicher Keimbildung von Partikeln im Dampf führen würde, die Ruß oder andere Defekte bilden.
-
Minimierung der Kontamination:
- Eine Vakuumumgebung reduziert das Vorhandensein von unerwünschten Stoffen wie Sauerstoff, Stickstoff, Kohlendioxid und Wasserdampf.
- Diese Verunreinigungen können mit dem Filmmaterial reagieren und zu Verunreinigungen, Oxidation oder anderen chemischen Reaktionen führen, die die Qualität des Films beeinträchtigen.
- Durch die Aufrechterhaltung eines hohen Vakuums bleibt die Reinheit der abgeschiedenen Schicht erhalten, was eine starke Haftung und die gewünschten Materialeigenschaften gewährleistet.
-
Kontrolle der Gas- und Dampfzusammensetzung:
- Im Vakuum kann die Zusammensetzung der Gase und Dämpfe in der Kammer genau kontrolliert werden.
- Diese Kontrolle ist von entscheidender Bedeutung für Verfahren wie Sputtern oder chemische Gasphasenabscheidung (CVD), bei denen bestimmte Gase eingeführt werden, um den Abscheidungsprozess zu erleichtern.
- Ein Vakuum sorgt dafür, dass nur die gewünschten Gase vorhanden sind und Störungen durch atmosphärische Gase ausgeschlossen werden.
-
Niederdruck-Plasmaumgebung:
- Viele Verfahren zur Dünnschichtabscheidung, wie die plasmaunterstützte chemische Gasphasenabscheidung (PECVD), erfordern eine Niederdruck-Plasmaumgebung.
- Ein Vakuum ermöglicht die Erzeugung dieses Plasmas, das für die Aktivierung chemischer Reaktionen oder ionisierender Gase zur Abscheidung von Schichten bei niedrigeren Temperaturen unerlässlich ist.
- Die Abwesenheit von atmosphärischen Gasen gewährleistet eine stabile Plasmabildung und eine effiziente Abscheidung.
-
Effiziente Massendurchflussregelung:
- Ein Vakuum ermöglicht eine präzise Steuerung des Gas- und Dampfstroms in die Prozesskammer.
- Diese Kontrolle ist entscheidend, um eine gleichmäßige Schichtdicke und -zusammensetzung auf dem Substrat zu erreichen.
- Ohne Vakuum könnte ein unkontrollierter Gasfluss zu ungleichmäßiger Abscheidung und schlechter Schichtqualität führen.
-
Hohe thermische Verdampfungsrate:
- Bei physikalischen Aufdampfverfahren (PVD) wie der thermischen Verdampfung ist ein Vakuum erforderlich, um hohe Verdampfungsraten zu erzielen.
- Der reduzierte Druck verhindert Wärmeverluste und sorgt dafür, dass das Material effizient verdampft und sich gleichmäßig auf dem Substrat ablagert.
- Atmosphärischer Druck würde die Verdunstung behindern und zu einer unvollständigen oder ungleichmäßigen Filmbildung führen.
-
Verhinderung von Filmoxidation und anderen Reaktionen:
- Viele Materialien, die bei der Dünnschichtabscheidung verwendet werden, reagieren stark mit Sauerstoff oder Feuchtigkeit in der Luft.
- Ein Vakuum eliminiert diese reaktiven Gase und verhindert Oxidation oder andere unerwünschte chemische Reaktionen während der Abscheidung.
- Dies ist vor allem bei Metallen und Halbleitern wichtig, wo selbst Spuren von Sauerstoff die elektrischen oder optischen Eigenschaften verändern können.
-
Verbesserte Filmhaftung und Reinheit:
- Durch die Verringerung von Verunreinigungen und die Gewährleistung einer gleichmäßigen Abscheidung verbessert eine Vakuumumgebung die Haftung der Schicht auf dem Substrat.
- Eine starke Haftung ist entscheidend für die Haltbarkeit und Leistung der Dünnschicht in Anwendungen wie Elektronik, Optik und Beschichtungen.
- Ein hoher Reinheitsgrad gewährleistet, dass die Folie die gewünschten mechanischen, elektrischen oder optischen Eigenschaften aufweist, ohne durch Verunreinigungen gestört zu werden.
Zusammenfassend lässt sich sagen, dass die Verwendung eines Vakuums bei der Dünnschichtabscheidung unverzichtbar ist, um hochwertige, gleichmäßige und reine Schichten zu erhalten. Es stellt sich zentralen Herausforderungen wie der Kontrolle von Verunreinigungen, der Streuung von Partikeln und der präzisen Prozesssteuerung und ist damit eine grundlegende Voraussetzung für moderne Abscheidetechniken.
Zusammenfassende Tabelle:
Hauptvorteil | Erläuterung |
---|---|
Langer mittelfreier Weg für verdampfte Atome | Verringert die Gasdichte, so dass die Atome längere Strecken ohne Zusammenstöße zurücklegen können. |
Minimierung der Kontamination | Eliminiert unerwünschte Stoffe wie Sauerstoff, Stickstoff und Kohlendioxid. |
Kontrolle der Gas- und Dampfzusammensetzung | Ermöglicht die präzise Steuerung von Gasen für Prozesse wie Sputtern oder CVD. |
Niederdruck-Plasmaumgebung | Erleichtert die stabile Plasmabildung für Techniken wie PECVD. |
Effiziente Massendurchflussregelung | Sorgt für eine gleichmäßige Schichtdicke und -zusammensetzung auf dem gesamten Substrat. |
Hohe thermische Verdampfungsrate | Ermöglicht eine effiziente Verdampfung für PVD-Techniken wie die thermische Verdampfung. |
Verhinderung der Oxidation des Films | Beseitigt reaktive Gase und verhindert Oxidation oder unerwünschte chemische Reaktionen. |
Verbesserte Filmhaftung und Reinheit | Gewährleistet starke Haftung und hohe Reinheit für langlebige, leistungsstarke Folien. |
Erfahren Sie, wie eine Vakuumumgebung Ihren Dünnschichtabscheidungsprozess optimieren kann kontaktieren Sie unsere Experten noch heute !