Einführung in Spark Plasma Sintering Furnaces (SPS)
Funkenplasma-Sinteröfen (SPS) stellen eine Spitzentechnologie auf dem Gebiet der Materialwissenschaft dar und bieten einen einzigartigen Ansatz zum Sintern durch die Verwendung von Ein-Aus-Gleichstromimpulsen zur Plasmaerzeugung. Dieser umfassende Leitfaden befasst sich mit den Feinheiten der SPS-Technologie und untersucht ihre Komponenten wie die Axialdruckvorrichtung, die wassergekühlte Stanzelektrode und die Vakuumkammer. Durch das Verständnis der Hauptmerkmale und der vielseitigen Anwendungsmöglichkeiten von SPS wird deutlich, wie diese Technologie das schnelle, effiziente und qualitativ hochwertige Sintern verschiedener Materialien, von Metallen und Keramiken bis hin zu Nanomaterialien und Verbundwerkstoffen, revolutioniert.
Hauptmerkmale von Spark Plasma Sintering Öfen
Spark Plasma Sintering (SPS)-Öfen haben den Bereich der Materialwissenschaft mit ihren einzigartigen Fähigkeiten und schnellen Verarbeitungszeiten revolutioniert. Diese Öfen verwenden einen hohen gepulsten Gleichstrom, um Pulverpresslinge zu erhitzen und zu sintern, und bieten gegenüber herkömmlichen Sinterverfahren mehrere deutliche Vorteile. Im Folgenden werden die wichtigsten Merkmale von SPS-Öfen erläutert, darunter Schnellsintern, Reinigungs- und Aktivierungssintern, Feinkornsintern, Sintern mit breitem Temperaturbereich, Dichtesteuersintern und Temperaturgradienten-Sintern.
Schnelles Sintern
Einer der wichtigsten Vorteile von SPS-Öfen ist ihre Fähigkeit, schnell zu sintern. Die Aufheizrate kann 500°C/min überschreiten, was deutlich schneller ist als herkömmliche Verfahren wie Heißpressen, heißisostatisches Pressen (HIP) und druckloses Sintern. Diese schnelle Aufheizrate ermöglicht wesentlich kürzere Sinterzeiten, die den Prozess oft von Stunden auf nur wenige Minuten reduzieren. Die schnellen Aufheiz- und Abkühlraten minimieren auch Vergröberungsprozesse und tragen dazu bei, dass die intrinsischen Nanostrukturen des Materials nach der vollständigen Verdichtung erhalten bleiben.
Reinigen & Aktivierungssintern
SPS-Öfen bieten einen einzigartigen Reinigungs- und Aktivierungssinterungsprozess. Der hohe gepulste Gleichstrom bewirkt eine Reinigung der Partikeloberfläche, wodurch adsorbierte Gase und Oxidschichten entfernt werden. Dieser Reinigungsprozess in Verbindung mit dem Aktivierungseffekt der Partikeloberfläche ermöglicht das Sintern von Materialien, die traditionell schwer zu sintern sind. Diese Eigenschaft ist besonders vorteilhaft für Materialien mit hohen Reinheitsanforderungen oder solche, die empfindlich auf Oberflächenverunreinigungen reagieren.
Feinkörniges Sintern
Der schnelle Temperaturanstieg in SPS-Öfen hemmt das Kornwachstum und ermöglicht so die Regulierung des Gefüges und die Herstellung feinkörniger Sinterkörper. Diese Eigenschaft macht SPS zu einem ausgezeichneten Verfahren für die Herstellung nanokristalliner Werkstoffe. Durch die Steuerung der Sinterparameter können die Forscher die gewünschte Korngröße und Mikrostruktur erreichen, was für die Optimierung der mechanischen, elektrischen und thermischen Eigenschaften des Materials entscheidend ist.
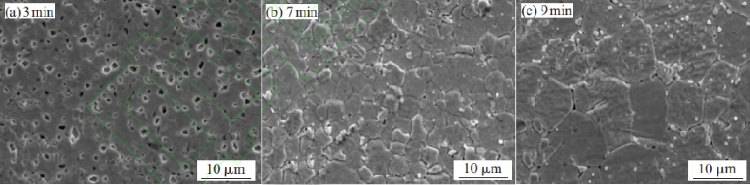
Breites Temperaturspektrum beim Sintern
SPS-Öfen können in einem breiten Temperaturbereich betrieben werden, der von niedrigen Temperaturen bis zu 2300°C reicht. Dieser große Temperaturbereich macht SPS-Öfen vielseitig einsetzbar für das Sintern einer Vielzahl von Materialien, einschließlich Keramik, Metallen und Verbundwerkstoffen. Die Fähigkeit, schnell und effizient hohe Temperaturen zu erreichen, ist besonders nützlich für Materialien, die eine Hochtemperaturverarbeitung benötigen, um eine vollständige Verdichtung und optimale Eigenschaften zu erreichen.
Dichtekontrolle beim Sintern
Ein weiteres bemerkenswertes Merkmal von SPS-Öfen ist ihre Fähigkeit, die Dichte des Sinterkörpers zu steuern. Von porösen Körpern bis hin zu völlig dichten Sinterkörpern bieten SPS-Öfen eine flexible Dichtesteuerung. Erreicht wird dies durch die Einstellung der Sinterparameter, wie z. B. der angewandten Kraft, des Kolbenwegs und des Stroms. Die präzise Steuerung der Dichte ist entscheidend für die Anpassung der Materialeigenschaften an spezifische Anwendungen, z. B. in der Luft- und Raumfahrt, der Automobilindustrie und der Medizintechnik.
Temperatur-Gradienten-Sintern
SPS-Öfen können einen Temperaturgradienten in der Form erzeugen, der das gleichzeitige Sintern von Materialien mit unterschiedlichen Schmelzpunkten ermöglicht. Diese Funktion ist besonders nützlich für die Herstellung von funktional abgestuften Materialien (FGM), bei denen verschiedene Schichten oder Bereiche des Materials unterschiedliche Verarbeitungsbedingungen erfordern. Die Fähigkeit, einen Temperaturgradienten (Hunderte von °C/mm) innerhalb der Form zu erzeugen, ermöglicht die Herstellung komplexer, mehrschichtiger Materialien mit maßgeschneiderten Eigenschaften und Funktionalitäten.
Zusammenfassend lässt sich sagen, dass SPS-Öfen eine Reihe von fortschrittlichen Funktionen bieten, die sie zu einem leistungsstarken Werkzeug im Bereich der Materialwissenschaft machen. Ihre Fähigkeit zum Schnellsintern, zum Reinigungs- und Aktivierungssintern, zum Feinkornsintern, zum Sintern in einem weiten Temperaturbereich, zum Dichteregelungssintern und zum Temperaturgradientensintern macht sie vielseitig und effizient für eine Vielzahl von Anwendungen. Da Forschung und Entwicklung auf diesem Gebiet weiter voranschreiten, werden SPS-Öfen eine immer wichtigere Rolle bei der Herstellung von Hochleistungswerkstoffen spielen.
Vielseitigkeit in der Materialverarbeitung mit SPS
Das Spark-Plasma-Sintern (SPS) ist ein hocheffizientes und vielseitiges Verfahren, das zum Sintern einer Vielzahl von Werkstoffen eingesetzt wird, darunter Metalle, Keramiken, Nanomaterialien und Verbundwerkstoffe. Bei dieser Methode werden Gleichstromimpulse zur Erzeugung eines Funkenplasmas zwischen den Partikeln eingesetzt, was eine schnelle Erhitzung und Verdichtung ermöglicht. SPS ist bekannt für seine Fähigkeit, qualitativ hochwertige Materialpräparationen zu erzielen, die erhebliche Vorteile gegenüber herkömmlichen Sinterverfahren aufweisen.
Breite Anwendbarkeit von SPS
Nanomaterialien
Die SPS-Technologie ist besonders effektiv bei der Herstellung von Nanomaterialien. Bei herkömmlichen Sinterverfahren ist es oft schwierig, die Korngröße im Nanometerbereich beizubehalten und eine vollständige Dichte zu erreichen. SPS mit seiner schnellen Erhitzung und den kurzen Synthesezeiten unterdrückt effektiv die Kornvergröberung. Dieser schnelle Prozess ermöglicht auch die Beibehaltung von Defekten und Substrukturen im Pulver, was für die Synthese von metastabilen Materialien und Nanomaterialien von Vorteil sein kann.
Funktionale Gradientenwerkstoffe
Funktionelle Gradientenwerkstoffe (FGM) sind Verbundwerkstoffe mit einer Gradientenverteilung in einer bestimmten Richtung, die häufig unterschiedliche Sintertemperaturen für jede Schicht erfordern. Herkömmliche Verfahren wie die chemische Gasphasenabscheidung (CVD) und die physikalische Gasphasenabscheidung (PVD) sind kostspielig und für die industrielle Produktion schwierig. SPS überwindet diese Herausforderungen, indem es das Sintern von Werkstoffen mit Gradienten in Bezug auf Hitzebeständigkeit, Verschleißfestigkeit, Härte, Leitfähigkeit und Porosität ermöglicht und dabei die Möglichkeit bietet, mehrere Schichten zu verarbeiten.
Elektromagnetische Werkstoffe
SPS wird auch bei der Herstellung verschiedener elektromagnetischer Materialien eingesetzt, darunter thermoelektrische Umwandlungselemente und Materialien, die in der Elektronik verwendet werden, wie supraleitende Materialien, magnetische Materialien, dielektrische Materialien und mehr. Diese Werkstoffe sind von entscheidender Bedeutung für Anwendungen, die von der Energiespeicherung bis zur Biomedizintechnik reichen.
Intermetallische Verbindungen
Intermetallische Verbindungen, die für ihre Sprödigkeit und ihren hohen Schmelzpunkt bekannt sind, erfordern spezielle Verfahren für ihre Herstellung. SPS bietet eine effiziente Methode zur Herstellung dieser Verbindungen, indem es die Selbsterhitzung und die Oberflächenaktivierung zwischen den Partikeln nutzt und so eine schnelle Sinterung bei niedrigen Temperaturen ermöglicht.
Hochdichte, feinkörnige Keramiken und Cermets
Das SPS-Verfahren verkürzt die Sinterzeiten erheblich und senkt die Temperaturen, indem es die im Inneren der einzelnen Pulverpartikel und in den Lücken zwischen ihnen erzeugte Wärme nutzt. Dies macht SPS zu einem hervorragenden Verfahren für die Herstellung von hochdichten, feinkörnigen Keramiken und Cermets, die für verschiedene industrielle Anwendungen unerlässlich sind.
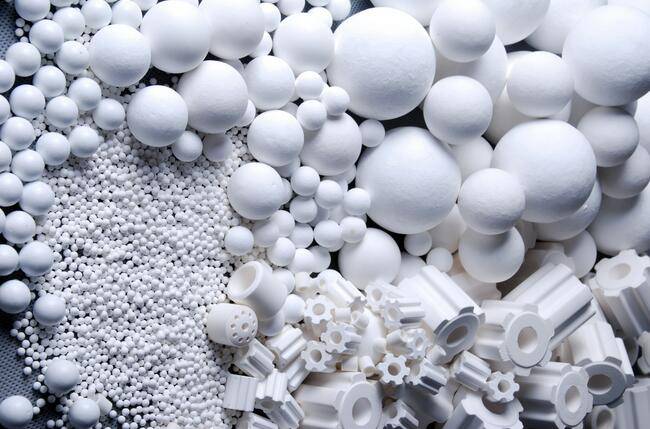
Vorteile von SPS
- Kürzere Zykluszeiten: SPS verkürzt die Sinterzyklen von Stunden oder Tagen auf nur wenige Minuten, was die Produktivität und die Fähigkeit zur schnellen Materialentwicklung erhöht.
- Niedrigere Sintertemperaturen: Es ermöglicht das Sintern bei niedrigeren Temperaturen im Vergleich zu konventionellen Verfahren, was besonders bei hitzeempfindlichen Materialien von Vorteil ist.
- Hochpräzise Prozesssteuerung: SPS bietet eine genaue Kontrolle über Sinterparameter wie Temperatur und Druck, was optimale Ergebnisse gewährleistet und die Entwicklung einzigartiger chemischer Zusammensetzungen ermöglicht, die mit herkömmlichen Methoden nicht möglich sind.
- Vielseitigkeit: Es kann eine Vielzahl von Materialien verdichten, von Metallen mit niedrigem Schmelzpunkt bis hin zu Ultrahochtemperaturkeramiken, und sogar ungleiche Materialien verbinden, die eine ungleichmäßige Temperaturverteilung erfordern.
Anwendungen von SPS
Die SPS-Technologie findet in verschiedenen Bereichen Anwendung, darunter:
- Energiespeicherung: Lithium-Ionen-Batterien mit hoher Kapazität und andere fortschrittliche Energiespeichermaterialien.
- Biomedizinische Technik: Poröse Keramiken für die Verabreichung von Medikamenten und Gerüste für die Gewebezüchtung.
- Hochleistungskeramik: Hochtemperatursupraleiter und piezoelektrische Hochleistungskeramik.
- Intermetallische Werkstoffe: Hochwertige Legierungen mit verbesserten mechanischen, thermischen und elektrischen Eigenschaften.
- Verbundwerkstoffe: Verstärkte Keramiken und Metalle mit verbesserten mechanischen Eigenschaften.
Zusammenfassend lässt sich sagen, dass das Funkenplasmasintern ein äußerst vielseitiges und effizientes Verfahren zum Sintern verschiedener Werkstoffe ist, das erhebliche Vorteile in Bezug auf die Prozesssteuerung, die Energieeffizienz und die Fähigkeit zur Herstellung hochwertiger Werkstoffe für eine breite Palette von Anwendungen bietet.
Bedienerfreundlichkeit und Sicherheitsmerkmale von SPS-Öfen
Spark Plasma Sintering (SPS)-Öfen sind bekannt für ihre fortschrittliche Bedienerfreundlichkeit und ihre robusten Sicherheitsmerkmale, die sie zu einer bevorzugten Wahl für verschiedene industrielle Anwendungen machen. Bei der Entwicklung dieser Öfen wurde besonderer Wert auf benutzerfreundliche Schnittstellen und umfassende Sicherheitsmechanismen gelegt, um einen effizienten und sicheren Betrieb zu gewährleisten.
Benutzerfreundliches Design und Kontrollsysteme
Die SPS-Öfen sind mit hochmodernen Steuerungssystemen ausgestattet, die den Bedienungskomfort erhöhen. Ein bemerkenswertes Merkmal ist die Integration von Touchscreen-Oberflächen und speicherprogrammierbaren Steuerungen (SPS) zur zentralen Steuerung. Dadurch können die Bediener die Ofenparameter leicht überwachen und einstellen, was die Komplexität des Betriebs reduziert und das Potenzial für menschliche Fehler minimiert. Das Allen-Bradley-SPS-System ist beispielsweise für seine einfache Programmierung und Änderung bekannt, was die Verwaltung des Ofenbetriebs weiter vereinfacht.
Der Schaltschrank dieser Öfen ist so konzipiert, dass alle elektrischen Steuerungen in einem Standard-NEMA-12-Schrank untergebracht sind, wodurch die Einhaltung von Sicherheitsstandards wie NFPA 70 gewährleistet wird. Diese zentrale Steuerung erhöht nicht nur die Sicherheit, sondern vereinfacht auch die Wartung und Fehlersuche. Die integrierte Verriegelung des elektrischen Hauptschalters sorgt für zusätzliche Sicherheit, indem sie unbefugte oder versehentliche Eingriffe verhindert.
Fortschrittliche Sicherheitsmechanismen
Sicherheit steht beim Betrieb von SPS-Öfen an erster Stelle, und diese Systeme sind mit mehreren Schutzschichten ausgestattet. Zu den wichtigsten Sicherheitsmerkmalen gehören Alarme bei Übertemperatur und Überdruck, die das Bedienpersonal in Echtzeit auf mögliche Gefahren aufmerksam machen. Darüber hinaus gibt es mechanische, automatische Druckschutzsysteme, die vor druckbedingten Problemen schützen und die Integrität des Ofens und der zu verarbeitenden Materialien gewährleisten.
Die Öfen verfügen auch über Verriegelungsfunktionen, die einen Betrieb unter unsicheren Bedingungen verhindern. Verriegelungen werden beispielsweise eingesetzt, um den Ofen bei Strom- oder Wassermangel, unzureichendem Druck oder Übertemperatur abzuschalten. Diese Verriegelungen sind von entscheidender Bedeutung, um Unfälle zu vermeiden und sowohl die Anlage als auch das Bedienpersonal zu schützen.
Ein weiteres wichtiges Sicherheitsmerkmal sind die Fernsteuerungsmöglichkeiten, die eine Ferndiagnose von Störungen und Programmaktualisierungen ermöglichen. Dies erhöht nicht nur die Effizienz der Wartung, sondern verringert auch das Risiko, dass die Techniker gefährlichen Bedingungen ausgesetzt sind.
Integration von Thermoelementen
Eine genaue Temperaturregelung ist bei Sinterprozessen unerlässlich, und SPS-Öfen verwenden hochwertige Thermoelemente, wie z. B. Typ "S" und Typ "K", zur präzisen Temperaturüberwachung und -regelung. Diese Thermoelemente sind in entsprechende Buchsenfelder zur Arbeitsüberwachung und -kontrolle integriert und gewährleisten, dass der Sinterprozess innerhalb sicherer und optimaler Temperaturbereiche bleibt.
Fazit
Zusammenfassend lässt sich sagen, dass die Bedienerfreundlichkeit und die Sicherheitsmerkmale der SPS-Öfen so konzipiert sind, dass sie ein nahtloses und sicheres Sintererlebnis bieten. Mit benutzerfreundlichen Steuerungssystemen, fortschrittlichen Sicherheitsmechanismen und präziser Temperaturregelung sind diese Öfen ideal für eine Vielzahl von Anwendungen bei der Verarbeitung von Metallen, Keramiken, Nanomaterialien und mehr. Die Integration von moderner Technologie und robusten Sicherheitsprotokollen sorgt dafür, dass die Bediener effizient arbeiten und gleichzeitig die Risiken minimieren können.
Fortschrittliche Steuerungs- und Überwachungssysteme in SPS
Fortschrittliche Steuerungs- und Überwachungssysteme sind ein wesentlicher Bestandteil des Spark Plasma Sintering (SPS)-Prozesses. Sie ermöglichen eine präzise Regelung von Temperatur, Druck und Strom sowie eine umfassende Datenerfassung zur Verfolgung und Analyse der Sinterparameter. Diese Systeme sind entscheidend für die Gewährleistung der Qualität und Reproduzierbarkeit der gesinterten Materialien.
Automatisierte Programmsteuerung
Das SPS-Verfahren beginnt mit dem Einfüllen einer bekannten Menge getrockneter und gemahlener Pulverproben in eine zylindrische Matrize, die mit einer Graphitplatte ausgekleidet ist, die eine einfache Entnahme des Sinterkörpers ermöglicht. Die Matrize wird dann in der SPS-Kammer platziert, und das für das Experiment erforderliche spezifische Zeit-Temperatur-Profil wird eingestellt. Die Atmosphäre in der Kammer wird je nach Bedarf aufrechterhalten, sei es Vakuum, Argon oder eine andere kontrollierte Umgebung. Die Leistung wird im Auto-Modus auf Maximum eingestellt, und die erforderliche Last wird auf den Stempel aufgebracht. Die z-Achse wird auf Null gesetzt, und der Timer wird aktiviert, bevor die Taste SINTER gedrückt wird, um den Sinterprozess zu starten.
Für die Temperaturmessung verwendet die SPS zwei Arten von Instrumenten: Thermoelemente für Sintertemperaturen unter 1000°C und Pyrometer für Temperaturen über 1000°C. Ein hoher Gleichstromimpuls wird zwischen Graphitelektroden geleitet, und gleichzeitig wird von Beginn des Sinterzyklus an ein axialer Druck angelegt. Die Probe wird durch Joule'sche Erwärmung und Funkenbildung zwischen den Partikeln erhitzt, was zu einem schnelleren Wärme- und Stofftransport in kürzester Zeit führt. Nach dem Sintern wird der Strom abgeschaltet, und die Probe kann abkühlen.
Computergesteuerte Kontrollsysteme
Das Steuersystem der SPS ist in der Regel computergestützt und verfügt über ein automatisches PLC-Flachbildschirm-Touch-Computer-Steuersystem, das ein manuelles Umschalten in den Automatikbetrieb ermöglicht. Die Software des Steuersystems wird im eigenen Haus entwickelt und bietet eine benutzerfreundliche Schnittstelle mit Echtzeitüberwachung der Ofenbedingungen. Das System ist stabil und zuverlässig, reagiert schnell und hat eine hohe Antistörungsfähigkeit. Die Software zeigt einen farbigen Simulationsbildschirm mit integrierter Temperaturanzeige und Vakuumventilsteuerung für eine intuitive Bedienung.
Das Gerät kann verschiedene Kurven zur Analyse verwenden, z. B. Temperatur-, Leistungs-, Vakuum-, Wassertemperatur-, Luftdruck- und Sinterzeitkurven. Diese Kurven bieten eine benutzerfreundliche Möglichkeit, den Sinterprozess auf der Grundlage historischer Daten zu analysieren. Das System kann über die USB-Schnittstelle automatisch Excel-Dateien für weitere Analysen erzeugen.
Die Temperaturregelung erfolgt bei Temperaturen bis zu 1700°C über ein Thermoelement, bei Temperaturen über 1700°C über Infrarotinstrumente. Das System unterstützt verschiedene Kommunikationsschnittstellen wie RS232, RS422, CAN, LAN und USB, die eine einfache Vernetzung mit anderen Geräten ermöglichen. Die Software-Steuerungsschnittstelle ist visualisiert und zeigt den Arbeitsablauf dynamisch an, was die Bedienung erleichtert und intuitiv ist. Die Software ist zudem lebenslang kostenlos aufrüstbar.
Steuerungen und Datenerfassung
Ähnlich wie bei anderen Prüfkammern gibt es auch bei SPS verschiedene Steuerungen, die von vollständig manuellen bis hin zu vollautomatischen Systemen reichen. Bei automatisierten Steuerungen kann der Benutzer die Parameter des Prozesses einstellen, und während des Verfahrens nimmt das System Anpassungen bei Druck, Temperatur und anderen programmierten Faktoren vor. Diese Steuerungssysteme sind mit anpassbarer Software und einer Vielzahl von Datenerfassungsmethoden konfigurierbar. Die Wahl des Steuergeräts richtet sich nach der Kritikalität der Anwendung und der Größe der Vakuumkammer. Kleinere Kammern benötigen möglicherweise nur ein einfaches Messgerät zur Überwachung von Pumpen und Druck, während größere Kammern ein aggressiveres und ausgeklügeltes System erfordern können.
Komponenten der Sintermaschine
Die SPS-Maschine wird von mehreren Komponenten unterstützt, darunter eine einachsige Presse, Stempelelektroden, eine Vakuumkammer, eine kontrollierte Atmosphäre, ein Gleichstromimpulsgenerator sowie Positions-, Temperatur- und Druckmessgeräte. Die Steuerung der Sintertemperatur wird durch die Einstellung von Parametern wie Haltezeit, Rampenrate, Pulsdauer sowie Pulsstrom und -spannung erreicht. Die Gleichstromimpulsentladung erzeugt Funkenplasma, Funkenschlagdruck, Joule-Erwärmung und einen elektrischen Felddiffusionseffekt. Bei SPS wird das Sintern durch die Ein-Aus-Gleichstromimpulsspannung unterstützt, was sich vom herkömmlichen Heißpressen unterscheidet. Die Anwendung von Druck unterstützt das plastische Fließen des Materials, und der Fluss des Gleichstromimpulsstroms durch die Partikel wird in detaillierten Diagrammen dargestellt.
Zusammenfassend lässt sich sagen, dass fortschrittliche Steuerungs- und Überwachungssysteme in SPS unerlässlich sind, um präzise und reproduzierbare Sinterergebnisse zu erzielen. Diese Systeme ermöglichen Anpassungen in Echtzeit und eine umfassende Datenerfassung, wodurch die Qualität und Konsistenz der gesinterten Materialien gewährleistet wird. Durch die Integration von computergestützter Steuerung, anpassbarer Software und fortschrittlichen Datenerfassungsmethoden verschiebt die SPS-Technologie die Grenzen der Materialwissenschaft und -technik immer weiter.
Anwendungen des Spark-Plasma-Sinterns in der Materialwissenschaft
Spark Plasma Sintering (SPS) ist ein vielseitiges und fortschrittliches Sinterverfahren, das den Bereich der Materialwissenschaften revolutioniert hat. Durch die Kombination von einachsigem Druck, gepulstem Gleichstrom und schneller Erwärmung ermöglicht SPS die Synthese einer breiten Palette von Materialien mit einzigartigen Eigenschaften und Strukturen. Dieser Abschnitt befasst sich mit den vielfältigen Anwendungen von SPS, einschließlich Sintern, Fügen, Formen, Oberflächenmodifizierung und der Synthese von Materialien wie Festelektrolyten und elektrothermischen Materialien.
Sintern moderner Werkstoffe
SPS ist besonders für seine Fähigkeit bekannt, hochschmelzende Materialien und Nanomaterialien effizient zu sintern. Die schnellen Heizraten (bis zu 1000°C/min) und die kurzen Verarbeitungszeiten von SPS tragen dazu bei, die Nanostruktur von Pulvern zu erhalten, das Kornwachstum zu verhindern und die Eigenschaften von Partikeln in Nanogröße zu bewahren. Dies macht SPS zu einem idealen Verfahren für die Herstellung hochdichter, feinkörniger Keramiken und Cermets. So kann beispielsweise Titannitrid, ein Material, das für seine schlechten Sintereigenschaften und Sprödigkeit bekannt ist, mit SPS auf ein hohes Niveau verdichtet werden, wobei unter Drücken von 1-5 GPa Dichten nahe den theoretischen Werten erreicht werden.
Fügen und Umformen
Neben dem Sintern wird SPS auch zum Verbinden unterschiedlicher Materialien und zum Formen komplexer Formen eingesetzt. Der während des Prozesses angelegte Gleichstrom erhitzt nicht nur das Material, sondern verbessert auch die Diffusionsbindung zwischen den Partikeln, was das Verbinden von Materialien erleichtert, die traditionell schwer zu verbinden sind, wie z. B. Keramik mit Metall. Diese Fähigkeit ist besonders in der Luft- und Raumfahrt- sowie in der Automobilindustrie nützlich, wo die Nachfrage nach leichten, hochfesten Verbundwerkstoffen hoch ist.
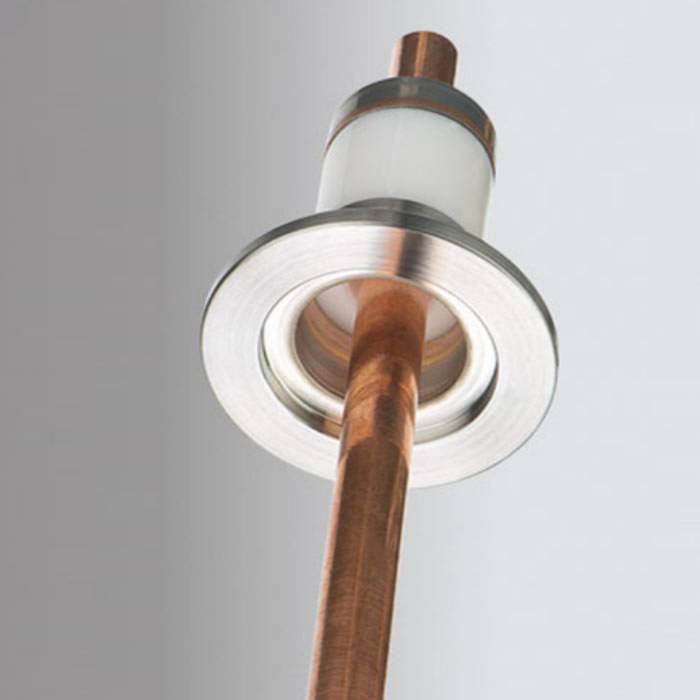
Modifizierung der Oberfläche
SPS kann auch zur Oberflächenmodifizierung eingesetzt werden, um die Oberflächeneigenschaften von Werkstoffen zu verbessern, ohne deren Eigenschaften zu beeinträchtigen. Durch die Steuerung der Stromdichte und des Drucks können bestimmte Oberflächenschichten so zugeschnitten werden, dass sie die gewünschten Eigenschaften wie erhöhte Härte, Verschleißfestigkeit oder Korrosionsbeständigkeit aufweisen. Diese Anwendung ist besonders vorteilhaft für Werkzeugmaterialien und Komponenten, die rauen Umgebungen ausgesetzt sind.
Synthese von Funktionswerkstoffen
Eine der bedeutendsten Anwendungen von SPS ist die Synthese von Funktionsmaterialien, einschließlich Festelektrolyten und elektrisch-thermischen Materialien. Festelektrolyte, die für Anwendungen in Festkörperbatterien und Brennstoffzellen entscheidend sind, erfordern einen hohen Grad an Verdichtung und Reinheit. SPS erleichtert die Synthese dieser Materialien mit minimaler Korngrenzensegregation und hervorragender Ionenleitfähigkeit. In ähnlicher Weise können elektrische Thermomaterialien, die in verschiedenen Heizanwendungen eingesetzt werden, durch präzise SPS-Verarbeitungsparameter mit kontrollierter Wärmeleitfähigkeit und elektrischem Widerstand synthetisiert werden.
Industrielle Bedeutung und Zukunftsaussichten
Die industrielle Bedeutung der SPS liegt in ihrer Fähigkeit, Hochleistungsmaterialien mit geringerem Energieverbrauch und kürzeren Verarbeitungszeiten herzustellen. Die Technologie eignet sich besonders für die Herstellung von Nanomaterialien, amorphen Massenlegierungen und funktionalen Gradientenmaterialien, deren Synthese mit herkömmlichen Methoden schwierig ist. Da die Forschung weiterhin neue Anwendungen erforscht und die Verarbeitungsparameter optimiert, wird das Spark Plasma Sintering eine entscheidende Rolle in der Zukunft der Materialwissenschaft spielen und den Fortschritt in verschiedenen High-Tech-Industrien vorantreiben.
Zusammenfassend lässt sich sagen, dass das Spark-Plasma-Sintern eine transformative Technologie in der Materialwissenschaft ist, die ein breites Spektrum an Anwendungen bietet, vom Sintern und Fügen bis hin zur Oberflächenmodifikation und der Synthese fortschrittlicher Funktionswerkstoffe. Seine Fähigkeit, Werkstoffe mit hoher Effizienz und Präzision zu verarbeiten, macht es zu einem unverzichtbaren Werkzeug für Forscher und industrielle Praktiker gleichermaßen.
Herausforderungen und Überlegungen beim Einsatz der SPS-Technologie
Die Spark Plasma Sintering (SPS)-Technologie hat den Bereich der Materialwissenschaft revolutioniert, da sie die Synthese fortschrittlicher Materialien mit einzigartigen Eigenschaften ermöglicht. Die Anwendung von SPS bringt jedoch eine Reihe von Herausforderungen und Überlegungen mit sich, die berücksichtigt werden müssen, um optimale Sinterergebnisse zu erzielen. Dieser Abschnitt befasst sich mit den kritischen Aspekten der Werkzeugauswahl und -wartung sowie mit den allgemeineren Überlegungen für einen effektiven SPS-Betrieb.
Auswahl der Form und Wartung
Die Wahl des Formmaterials ist ein entscheidender Faktor in der SPS-Technologie. Traditionell wird Graphit aufgrund seiner hohen Temperaturbeständigkeit, seiner hervorragenden elektrischen und thermischen Leitfähigkeit und seiner chemischen Stabilität bevorzugt. Graphitformen haben jedoch Einschränkungen wie geringe mechanische Festigkeit, kurze Lebensdauer und mögliche Verunreinigung der gesinterten Materialien. Diese Probleme machen die Erforschung alternativer Formwerkstoffe erforderlich.
Jüngste Fortschritte haben zur Entwicklung alternativer Formmaterialien wie Hartmetall, leitfähiger Keramik und Kohlefasergraphit geführt. Jedes dieser Materialien bietet einzigartige Vorteile, birgt aber auch Herausforderungen. Formen aus Sinterkarbid bieten zum Beispiel eine höhere Festigkeit, können sich aber bei hohen Temperaturen verformen. Leitfähige Keramiken bieten ein Gleichgewicht der Eigenschaften, sind aber oft teuer. Formen aus Kohlefasergraphit vereinen die Vorteile von Graphit mit verbesserten mechanischen Eigenschaften, erfordern aber eine sorgfältige Handhabung, um Schäden zu vermeiden.
Die Unversehrtheit der Form ist entscheidend für gleichbleibende Sinterergebnisse. Regelmäßige Inspektionen und der Austausch abgenutzter Formen sind unerlässlich, um Unregelmäßigkeiten im Sinterprozess zu vermeiden. Darüber hinaus kann eine ordnungsgemäße Reinigung und Konditionierung der Formen zwischen den Einsätzen ihre Lebensdauer verlängern und die Qualität der gesinterten Materialien erhalten.
Erzielung optimaler Sinterergebnisse
Um optimale Sinterergebnisse zu erzielen, müssen mehrere Aspekte berücksichtigt werden. Dazu gehören die Auswahl geeigneter Sinterparameter, die Kontrolle der Sinterumgebung und das Verständnis des Sintermechanismus.
Sinterparameter
Die Sinterparameter, wie Temperatur, Druck und Verweilzeit, spielen eine entscheidende Rolle bei der Bestimmung der endgültigen Eigenschaften des gesinterten Materials. Die schnellen Aufheiz- und Abkühlgeschwindigkeiten, die mit SPS erreicht werden können, können zu Mikrostrukturen führen, die nicht im Gleichgewicht sind, was für die Erzielung einzigartiger Materialeigenschaften von Vorteil sein kann. Diese Raten müssen jedoch sorgfältig kontrolliert werden, um übermäßiges Kornwachstum oder andere Defekte zu vermeiden.
Sinterumgebung
Die Sinterumgebung, einschließlich der Atmosphäre und der Temperaturgradienten, kann den Sinterprozess erheblich beeinflussen. Die Kontrolle der Atmosphäre kann Oxidation und andere chemische Reaktionen verhindern, die das Material zersetzen könnten. Temperaturgradienten innerhalb der Form können zu einer ungleichmäßigen Verdichtung führen, was eine sorgfältige Planung und Optimierung der Sinteranlage erfordert.
Verstehen des Sintermechanismus
Der Sintermechanismus bei SPS beinhaltet die Erzeugung eines Funkenplasmas zwischen den Partikeln, was eine schnelle Erwärmung und Verdichtung ermöglicht. Die genauen Mechanismen, die diesen Prozess steuern, sind jedoch noch nicht vollständig verstanden und Gegenstand laufender Forschung. Finite-Elemente-Simulationen haben sich als wertvolles Instrument zur Untersuchung des Sinterprozesses erwiesen, das Einblicke in die Temperatur- und elektrischen Feldverteilungen innerhalb des Materials ermöglicht.
Zukünftige Richtungen
Die kontinuierliche Verbesserung der SPS-Technologie erfordert ständige Forschung und Entwicklung. Zu den Schlüsselbereichen für künftige Untersuchungen gehören die Entwicklung neuer Formwerkstoffe mit verbesserten Eigenschaften, die Optimierung der Sinterparameter durch fortschrittliche Simulationstechniken und ein tieferes Verständnis des Sintermechanismus.
Zusammenfassend lässt sich sagen, dass die SPS-Technologie zwar erhebliche Vorteile für die Synthese fortschrittlicher Werkstoffe bietet, aber auch einige Herausforderungen und Überlegungen mit sich bringt, die berücksichtigt werden müssen, um optimale Ergebnisse zu erzielen. Durch eine sorgfältige Auswahl und Wartung der Formen, die Kontrolle der Sinterparameter und ein besseres Verständnis des Sintermechanismus können wir die Grenzen dessen, was mit der SPS-Technologie möglich ist, weiter verschieben.
Zukünftige Trends und Innovationen in der SPS-Technologie
Die Spark Plasma Sintering (SPS)-Technologie, die für ihre schnellen Sinterfähigkeiten bekannt ist, ist aufgrund ihrer Fähigkeit, hochwertige Materialien mit einzigartigen Eigenschaften herzustellen, ein Schwerpunkt im Bereich der Materialwissenschaften. Im Zuge der Weiterentwicklung der Forschung zeichnen sich mehrere Trends und Innovationen ab, die eine Steigerung der Effizienz, eine Ausweitung der Anwendungen und eine Verbesserung der Sicherheit der SPS-Technologie versprechen.
Industrialisierung und Massenproduktion
Einer der wichtigsten Trends in der SPS-Technologie ist ihr Übergang zur Industrialisierung. Im Vergleich zu herkömmlichen Sinterverfahren bietet die SPS erhebliche Vorteile in Form von Energie- und Zeiteinsparungen, erhöhter Produktionseffizienz und besserer Kontrolle der Produktleistung. Länder wie Japan haben bereits industrielle Anwendungen von SPS erreicht, vor allem bei der Herstellung von magnetischen Werkstoffen, Hartlegierungen und Gradienten-Funktionswerkstoffen. Das japanische Unternehmen Ohta Seiki hat beispielsweise die Massenproduktion von 100%igen WC-Superhartstoffen mit Hilfe von SPS erfolgreich umgesetzt und beliefert weltweit über 40 Hersteller. Im Gegensatz dazu befindet sich die SPS-Technologie in anderen Regionen, z. B. in China, noch weitgehend in der Laborforschungsphase und konzentriert sich auf die Aufbereitung und Prozessforschung neuer Materialien.
Diversifizierung der gesinterten Formen
Derzeit ist die SPS aufgrund der Beschränkungen des Sintermechanismus und der Graphitformen auf die Herstellung einfacher zylindrischer Proben beschränkt. Es gibt jedoch einen zunehmenden Trend zur Entwicklung der SPS-Technologie zur Herstellung komplexerer Formen und Strukturen. Dieser Fortschritt würde die Anwendbarkeit der SPS in verschiedenen technischen Bereichen erheblich erweitern und die Herstellung komplizierter Komponenten ermöglichen, die derzeit nicht realisierbar sind.
Materialsynthese und Verbindung
Die SPS-Technologie wird nicht nur für das Sintern von Schüttgut verwendet, sondern auch für die Synthese von Pulvern, insbesondere von solchen, die mit herkömmlichen Methoden nur schwer zu gewinnen sind. So wurde SPS beispielsweise zur Synthese von Ultrahochtemperatur-ZrC-Pulver eingesetzt, wobei eine hohe Reinheit und eine feine Korngröße von etwa 100 nm erreicht wurde. Darüber hinaus wird SPS für die Materialverbindung (Schweißen) erforscht, einschließlich Keramik-Keramik- und Keramik-Metall-Verbindungen. Die Fähigkeit, Materialien ohne Zwischenschicht durch Selbstdiffusion zu verbinden, die durch das elektrische Feld der SPS verstärkt wird, eröffnet neue Möglichkeiten für die Schaffung robuster und dauerhafter Verbundstrukturen.
Optimierung der Leistung von Sinterwerkzeugen
Graphit wird zwar aufgrund seiner hohen Temperaturbeständigkeit und seiner hervorragenden elektrischen und thermischen Leitfähigkeit häufig für SPS verwendet, hat aber auch seine Grenzen, wie z. B. die geringe Festigkeit und die mögliche Verunreinigung der gesinterten Materialien. Es gibt einen Trend zur Entwicklung neuer Formenmaterialien, die eine höhere Festigkeit, Wiederverwendbarkeit und geringere Verunreinigung bieten. Materialien wie Sinterkarbidformen, leitfähige Keramikformen und Kohlenstofffaser-Graphit-Formen werden erforscht, obwohl Herausforderungen wie die Verformung bei hohen Temperaturen und hohe Kosten bestehen bleiben.
Fortschritte bei der Simulation und Modellierung
Das Verständnis des komplexen Sinterprozesses in der SPS ist entscheidend für die Optimierung seiner Parameter und die Vorhersage der Ergebnisse. Die Finite-Elemente-Simulation hat sich in dieser Hinsicht als wertvolles Werkzeug erwiesen, mit dem Forscher die Temperatur- und elektrischen Feldverteilungen während des Sinterns analysieren können. Software wie ABAQUS, MATLAB und MSC.MARC werden für die Simulation des Sinterprozesses eingesetzt und geben Aufschluss über die Auswirkungen der verschiedenen Parameter und helfen bei der theoretischen Ausrichtung der Produktion.
Verbesserte Sicherheitsmerkmale
Mit der Weiterentwicklung der SPS-Technologie liegt der Schwerpunkt zunehmend auf der Verbesserung ihrer Sicherheitsmerkmale. Dazu gehören die Entwicklung von sichereren Betriebsprotokollen, die Verbesserung der Zuverlässigkeit von SPS-Anlagen und die Gewährleistung, dass die Technologie in einem breiteren Spektrum von Umgebungen eingesetzt werden kann, ohne die Sicherheit zu beeinträchtigen.
Zusammenfassend lässt sich sagen, dass die Zukunft derSPS-Technologiesieht vielversprechend aus, denn die laufende Forschung und Entwicklung zielt darauf ab, die Effizienz zu verbessern, die Materialanwendungen zu erweitern und die Sicherheitsmerkmale zu verbessern. Diese Fortschritte werden den Bereich der Materialwissenschaft revolutionieren und die Herstellung von Hochleistungsmaterialien und -komponenten ermöglichen, die bisher unerreichbar waren. Da die SPS-Technologie weiter ausreift, wird sie zweifellos eine entscheidende Rolle bei der Gestaltung der Zukunft der Fertigung und der Materialinnovation spielen.
Kontaktieren Sie uns für eine kostenlose Beratung
Die Produkte und Dienstleistungen von KINTEK LAB SOLUTION werden von Kunden auf der ganzen Welt anerkannt. Unsere Mitarbeiter helfen Ihnen gerne bei allen Fragen weiter. Kontaktieren Sie uns für eine kostenlose Beratung und sprechen Sie mit einem Produktspezialisten, um die am besten geeignete Lösung für Ihre Anwendungsanforderungen zu finden!