Grundprinzipien des PVD-Beschichtungsprozesses
Verdampfung
In einer Vakuumumgebung wird das feste Material, das so genannte Target, durch verschiedene Methoden, vor allem durch Erhitzen, in seinen gasförmigen Zustand umgewandelt. Dieser als Verdampfung bezeichnete Prozess ist für das PVD-Beschichtungsverfahren (Physical Vapor Deposition) von grundlegender Bedeutung. Um diese Umwandlung zu erreichen, werden verschiedene Techniken eingesetzt:
-
Thermische Verdampfung: Bei dieser Methode wird das Zielmaterial mit Hilfe eines elektrischen Widerstands oder anderer Heizelemente auf seine Verdampfungstemperatur erhitzt. Sobald das Material seinen Verdampfungspunkt erreicht hat, verwandelt es sich in ein Gas, das dann diffundiert und auf dem Substrat kondensiert und einen dünnen Film bildet.
-
Elektronenstrahlverdampfung: Hier wird ein hochenergetischer Elektronenstrahl auf das Zielmaterial gerichtet, der es zum Verdampfen bringt. Diese Technik eignet sich besonders für Materialien mit hohem Schmelzpunkt, da der örtlich begrenzte Erhitzungseffekt eine präzise Steuerung des Verdampfungsprozesses ermöglicht.
-
Laser-Verdampfung: Bei dieser Methode wird das Zielmaterial mit Hilfe von hochenergetischen Laserimpulsen verdampft. Die Laserverdampfung ist vorteilhaft für die Herstellung komplexer Dünnschichtmaterialien, da sie eine hohe Präzision bietet und für die Verdampfung von Materialien verwendet werden kann, die mit herkömmlichen Methoden schwer zu handhaben sind.
Jede dieser Methoden hat ihre eigenen Vorteile und wird je nach den spezifischen Anforderungen des Beschichtungsprozesses ausgewählt, wie z. B. die Art des verwendeten Materials und die gewünschten Eigenschaften der resultierenden Schicht.
Transport
Nachdem das gasförmige Material in den Dampfzustand überführt wurde, findet eine Diffusion innerhalb der Vakuumkammer statt. Diese Diffusion ist eine kritische Phase im PVD-Prozess, da sie sich direkt auf die Gleichmäßigkeit und Qualität der anschließenden Schichtabscheidung auswirkt. Mehrere Schlüsselfaktoren wirken sich erheblich auf diese Transportphase aus:
-
Gasdruck: Der Druck in der Vakuumkammer spielt eine entscheidende Rolle. Niedrige Drücke verbessern in der Regel die Diffusionseffizienz und sorgen dafür, dass sich das gasförmige Material gleichmäßiger auf dem Substrat ausbreitet. Umgekehrt kann ein höherer Druck zu Kollisionen zwischen den Gasmolekülen führen, was die Gesamtdiffusionsrate verringern und die Gleichmäßigkeit des Films beeinträchtigen kann.
-
Temperatur: Die Temperatur in der Vakuumumgebung ist eine weitere entscheidende Variable. Höhere Temperaturen können den Diffusionsprozess beschleunigen, müssen aber sorgfältig kontrolliert werden, um thermische Schäden am Substrat oder die Bildung ungleichmäßiger Schichten zu vermeiden. Das Gleichgewicht zwischen Temperatur und anderen Prozessparametern ist für eine optimale Diffusion unerlässlich.
-
Position des Substrats: Die räumliche Anordnung des Substrats im Verhältnis zur Quelle des gasförmigen Materials ist ebenfalls von Bedeutung. Durch die richtige Ausrichtung wird sichergestellt, dass das gasförmige Material alle Bereiche des Substrats gleichmäßig erreicht und eine örtlich begrenzte Über- oder Unterabscheidung verhindert wird. Techniken wie das Drehen oder Kippen des Substrats können dazu beitragen, eine gleichmäßigere Abdeckung zu erreichen.
Zusammenfassend lässt sich sagen, dass der Transport von gasförmigem Material im Vakuum ein differenzierter Prozess ist, der eine sorgfältige Kontrolle des Gasdrucks, der Temperatur und der Positionierung des Substrats erfordert, um die erfolgreiche Abscheidung eines hochwertigen Films zu gewährleisten.
Abscheidung
Während der Abscheidungsphase beginnt das gasförmige Material, das zum Substrat transportiert wurde, abzukühlen und zu kondensieren. Diese Abkühlung ist von entscheidender Bedeutung, da sie das Gas in einen festen, dünnen Film verwandelt, der an der Oberfläche des Substrats haftet. Der Abscheidungsprozess ist nicht nur eine physikalische Veränderung, sondern auch ein Umwandlungsprozess, der die Eigenschaften des Substrats je nach der spezifischen Anwendung erheblich verändert.
Die Art des Gases, das während der Abscheidung verwendet wird, spielt eine entscheidende Rolle bei der Bestimmung der endgültigen Struktur und der Eigenschaften der Schicht. So werden häufig inerte Gase wie Argon und Helium verwendet, um die Reinheit der Schicht zu gewährleisten und sicherzustellen, dass keine unerwünschten chemischen Reaktionen auftreten. Andererseits werden reaktive Gase wie Sauerstoff, Stickstoff und Fluor eingesetzt, um bestimmte Verbindungen wie Oxide, Nitride und Fluoride zu erzeugen und die Funktionalität der Folie für bestimmte Anwendungen zu verbessern.
Darüber hinaus ist der Gasdruck in der Abscheidekammer ein entscheidender Parameter, der sowohl die Abscheiderate als auch die Qualität der Schicht beeinflusst. Niedrigere Gasdrücke führen in der Regel zu dichteren und homogeneren Schichten, was für viele Anwendungen wünschenswert ist. Umgekehrt können höhere Gasdrücke zu raueren Schichten führen, was in bestimmten Fällen von Vorteil sein kann, z. B. wenn eine größere Oberfläche für eine bessere Haftung oder Reaktivität erforderlich ist.
Zusammenfassend lässt sich sagen, dass der Abscheidungsprozess ein ausgeklügeltes Zusammenspiel von Kühlung, Gasart und Druck ist, wobei jeder Faktor sorgfältig gesteuert wird, um die gewünschten Schichteigenschaften zu erreichen. Durch diese sorgfältige Abstimmung wird sichergestellt, dass die entstehenden Dünnschichten die hohen Anforderungen der verschiedenen Industriezweige erfüllen, von der Elektronik bis zur Optik und darüber hinaus.
Hauptarten des PVD-Verfahrens
Verdampfungsbeschichtung
Die Aufdampfung ist eine hochentwickelte Technik zur Herstellung dünner Schichten durch Erhitzen der Zielmaterialien bis zu ihrem Verdampfungspunkt. Dieses Verfahren eignet sich besonders gut für Metalle und bestimmte Legierungen, die durch thermische Energie vom festen in den gasförmigen Zustand überführt werden. Die verdampften Atome kondensieren dann auf dem Substrat und bilden eine gleichmäßige und konforme Dünnschicht. Dieses Verfahren wird in der Regel in einer Hochvakuumumgebung durchgeführt, um Kollisionen und Verunreinigungen zu minimieren und die Reinheit und Integrität der abgeschiedenen Schicht zu gewährleisten.
Einer der Hauptvorteile der Aufdampfung ist die Fähigkeit, hochwertige Schichten mit hervorragender Gleichmäßigkeit und Konformität zu erzeugen. Diese Technik ist vielseitig und eignet sich für eine Vielzahl von Materialien, darunter Metalle, Keramiken und Halbleiter. Das Verfahren erfordert jedoch eine Hochvakuumumgebung und ist sehr empfindlich gegenüber Umweltfaktoren, was seine Anwendbarkeit in bestimmten Szenarien einschränken kann.
Sputtering-Beschichtung
Die Sputtering-Beschichtung ist ein hochentwickeltes Verfahren der physikalischen Gasphasenabscheidung (PVD), bei dem ein Zielmaterial mit hochenergetischen Teilchen, in der Regel Ionen aus einem Plasma, beschossen wird. Dieser Beschuss bewirkt, dass das Zielmaterial Atome oder Moleküle ausstößt, die dann durch das Vakuum wandern und auf einem Substrat kondensieren und einen dünnen Film bilden. Das Verfahren ist vielseitig und lässt sich auf ein breites Spektrum von Materialien anwenden, darunter Metalle, Oxide und Nitride.
Bei der Sputtering-Beschichtung wird das Zielmaterial einem Plasma ausgesetzt, das häufig aus Argon-Ionen und Elektronen besteht. Diese energiereichen Teilchen "schlagen" Atome aus dem Target ab, wodurch eine Wolke von Quellatomen entsteht. Diese Wolke kondensiert dann auf dem Substrat, wo sie einen dünnen Film bildet. Die Wahl des Targetmaterials und die Bedingungen des Plasmas haben einen erheblichen Einfluss auf die Eigenschaften der abgeschiedenen Schicht.
Ein bemerkenswerter Aspekt der Sputterabscheidung ist das Phänomen des Resputterns, bei dem das bereits abgeschiedene Material durch nachfolgenden Ionen- oder Atombeschuss wieder emittiert werden kann. Dies kann sich auf die Gleichmäßigkeit und Dicke der Schicht auswirken und erfordert eine sorgfältige Kontrolle der Abscheidungsparameter, um die gewünschten Ergebnisse zu erzielen.
Die Sputtering-Beschichtung ist in verschiedenen Industriezweigen weit verbreitet, da sie qualitativ hochwertige, dichte Schichten mit hervorragender Haftung auf dem Substrat erzeugen kann. Besonders beliebt ist das Verfahren wegen seiner Anwendbarkeit auf eine Vielzahl von Materialien, was es zu einem vielseitigen Werkzeug bei der Herstellung fortschrittlicher Dünnschichten für Elektronik, Optik und mechanische Komponenten macht.
Gepulste Laserabscheidung (PLD)
Die gepulste Laserabscheidung (PLD) ist ein hochentwickeltes Verdampfungsverfahren, bei dem hochenergetische Laserpulse eingesetzt werden, um ein Zielmaterial in einer Vakuumkammer zu verdampfen. Diese Methode eignet sich besonders gut für die Herstellung komplexer Dünnschichtmaterialien und wird daher in verschiedenen wissenschaftlichen und industriellen Anwendungen bevorzugt eingesetzt.
Das PLD-Verfahren beginnt damit, dass der Laserstrahl das Material anvisiert, so dass es verdampft und eine Plasmastrahlung bildet. Dieses Plasma lagert sich dann auf einem Substrat ab, wo es sich zu einem dünnen Film verdichtet. Die Komplexität dieses Prozesses, der Verdampfung, Ablation, Plasmabildung und Exfoliation umfasst, erfordert eine sorgfältige Optimierung. Trotz des erhöhten Zeit- und Arbeitsaufwands, der zur Beherrschung der zahlreichen Variablen erforderlich ist, bietet PLD mehrere Vorteile.
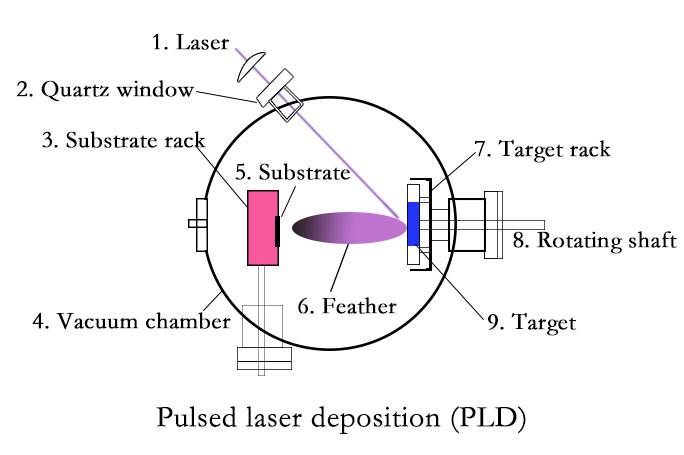
Einer der Hauptvorteile von PLD sind die hohen Abscheideraten, die den Prozess im Vergleich zu anderen Verfahren erheblich rationalisieren. Außerdem werden bei PLD keine Filamente benötigt, was die Wartung vereinfacht und mögliche Verunreinigungsquellen reduziert. Dadurch eignet sich PLD besonders für Anwendungen, die hohe Präzision und Reinheit erfordern, wie z. B. in der Elektronik- und Optikindustrie.
Zusammenfassend lässt sich sagen, dass die Komplexität des PLD-Verfahrens zwar eine sorgfältige Kontrolle erfordert, aber seine Fähigkeit, hochwertige, komplexe dünne Schichten effizient und mit minimalem Wartungsaufwand herzustellen, es zu einem wertvollen Werkzeug im Bereich der PVD-Beschichtungsverfahren macht.
Chemische Gasphasenabscheidung (CVD)
Die chemische Gasphasenabscheidung (Chemical Vapor Deposition, CVD) unterscheidet sich zwar grundlegend von der physikalischen Gasphasenabscheidung (Physical Vapor Deposition, PVD), aber es gibt Fälle, in denen diese beiden Techniken kombiniert werden, um bessere Schichteigenschaften zu erzielen. CVD, ein Vakuumabscheideverfahren, ist bekannt für die Herstellung hochwertiger, leistungsfähiger fester Materialien, insbesondere dünner Schichten, die in der Halbleiterindustrie verwendet werden. Bei diesem Verfahren wird ein Wafer (Substrat) einem oder mehreren flüchtigen Vorläufersubstanzen ausgesetzt, die auf der Substratoberfläche reagieren und/oder sich zersetzen, um die gewünschte Schicht zu bilden. Dieses Verfahren ist vielseitig und kann Materialien in verschiedenen Formen abscheiden, darunter monokristalline, polykristalline, amorphe und epitaktische Strukturen.
Im Gegensatz zum PVD-Verfahren, das auf physikalischen Prozessen wie Verdampfung oder Sputtern beruht, nutzt CVD chemische Reaktionen zur Abscheidung von Materialien. Dieser chemische Ansatz ermöglicht eine bessere Kontrolle über die Zusammensetzung und die Eigenschaften der abgeschiedenen Schicht. Bei bestimmten Anwendungen können jedoch durch den komplementären Einsatz von CVD und PVD Schichten mit verbesserten Eigenschaften erzielt werden, wie z. B. bessere Haftung, bessere mechanische Eigenschaften oder gleichmäßigere Beschichtungen. So können z. B. erste PVD-Schichten verwendet werden, um eine aufnahmefähigere Oberfläche für nachfolgende CVD-Schichten zu schaffen und so die Gesamtqualität der Schicht zu optimieren.
Die Integration von CVD und PVD ist besonders vorteilhaft bei komplexen Mikroherstellungsprozessen, bei denen die Kombination von chemischen und physikalischen Abscheidetechniken spezifische Herausforderungen bewältigen kann, die keine der beiden Methoden allein bewältigen könnte. Dieser hybride Ansatz erweitert nicht nur die Palette der Materialien, die abgeschieden werden können, sondern verbessert auch die Funktionalität und Leistung des Endprodukts.
Anwendung von Gasen im PVD-Prozess
Inerte Gase
Inertgase wie Argon (Ar) und Helium (He) spielen als Trägergase eine entscheidende Rolle bei der Sputterbeschichtung. Diese Gase werden bevorzugt, weil sie die Sputtereffizienz des Zielmaterials erhöhen, ohne chemische Reaktionen auszulösen. Diese nicht reaktive Eigenschaft stellt sicher, dass die Reinheit der abgeschiedenen Schicht erhalten bleibt, was für die Erzielung hochwertiger Beschichtungen unerlässlich ist.
Die Verwendung von Inertgasen ist nicht auf die Sputterabscheidung beschränkt; sie werden auch eingesetzt, um unerwünschte chemische Reaktionen zu verhindern, die eine Probe beeinträchtigen können. Zu diesen unerwünschten Reaktionen gehören in der Regel Oxidation und Hydrolyse, die in der Regel durch die Anwesenheit von Sauerstoff und Feuchtigkeit in der Luft ausgelöst werden. Durch den Ersatz dieser reaktiven Elemente durch Inertgase bleibt die Integrität der Probe erhalten.
Vor allem Argon ist aufgrund seines großen natürlichen Vorkommens und seiner relativ geringen Kosten das am häufigsten verwendete Inertgas in verschiedenen Anwendungen. Es macht etwa 1 % der Erdatmosphäre aus und ist damit für die industrielle Nutzung leicht verfügbar. Argon ist das am häufigsten verwendete Gas, aber auch andere Edelgase wie Helium und Neon können je nach den spezifischen Anforderungen des Prozesses verwendet werden.
Es sei darauf hingewiesen, dass der Begriff "Inertgas" kontextabhängig ist. Obwohl Edelgase oft als inert gelten, können sie unter bestimmten Bedingungen reagieren, wenn auch mit geringer Wahrscheinlichkeit. Diese Eigenschaft ist weitgehend auf die vollständigen Valenzschalen dieser Gase zurückzuführen, die sie im Allgemeinen nicht reaktiv machen. Dies ist jedoch keine absolute Regel, da auch Edelgase unter bestimmten Bedingungen Verbindungen bilden können.
Bei der Angabe der Reinheit von Edelgasen ist es üblich, den Verunreinigungsgrad in Teilen pro Million (ppm) anzugeben. Ein Verunreinigungsgrad von 100 ppm bedeutet zum Beispiel, dass von einer Million Molekülen des Inertgases 100 Fremdmoleküle sind. Dieses Maß ist entscheidend für die Wirksamkeit des Inertgases bei der Aufrechterhaltung der Reinheit des abgeschiedenen Films.
Zusammenfassend lässt sich sagen, dass Inertgase wie Argon und Helium bei der Sputterdeposition und anderen Verfahren, bei denen die Reinheit und Unversehrtheit der Materialien von größter Bedeutung ist, unverzichtbar sind. Aufgrund ihrer nicht reaktiven Eigenschaften und ihrer Verfügbarkeit eignen sie sich ideal für eine Vielzahl von industriellen Anwendungen.
Reaktive Gase
Reaktive Gase spielen eine entscheidende Rolle bei der Herstellung verschiedener dünner Schichten in PVD-Verfahren. Diese Gase, zu denen Sauerstoff (O₂), Stickstoff (N₂) und Fluor (F₂) gehören, sind für die Herstellung von Oxid-, Nitrid- bzw. Fluoridschichten unerlässlich. Die Einführung dieser reaktiven Gase ist oft notwendig, um die gewünschte chemische Zusammensetzung und die gewünschten Eigenschaften der abgeschiedenen Schichten zu erreichen.
Bei der Herstellung dünner Schichten aus Aluminiumoxid (Al₂O₃) wird beispielsweise in der Regel Sauerstoff als Reaktionsgas eingesetzt. Dadurch wird sichergestellt, dass die Aluminiumatome in der Dampfphase mit dem Sauerstoff reagieren und eine stabile und gleichmäßige Al₂O₃-Schicht bilden. Die Verwendung reaktiver Gase ist nicht auf Aluminiumoxid beschränkt, sondern gilt auch für andere Materialien wie Siliziumnitrid (Si₃N₄) und Titandioxid (TiO₂), bei denen Stickstoff bzw. Sauerstoff eingesetzt wird.
Die Wahl des reaktiven Gases und seiner Konzentration kann die Eigenschaften der Schicht, einschließlich ihrer Dichte, Härte und chemischen Stabilität, erheblich beeinflussen. Höhere Sauerstoffkonzentrationen können beispielsweise zu poröseren und weniger dichten Schichten führen, während niedrigere Konzentrationen zu einer unvollständigen Oxidation führen können, was die Gesamtqualität der Schicht beeinträchtigt.
Zusammenfassend lässt sich sagen, dass der gezielte Einsatz reaktiver Gase ein entscheidender Aspekt von PVD-Verfahren ist, der die Herstellung von Hochleistungsdünnschichten mit maßgeschneiderten Eigenschaften für verschiedene Anwendungen ermöglicht.
Organische Gase
In bestimmten Spezialanwendungen spielen organische Gase wie Ethylen und Propylen eine entscheidende Rolle bei der Herstellung von Polymerfilmen und Verbundwerkstoffen. Diese Gase werden häufig in den PVD-Prozess eingebracht, um die Bildung spezifischer Filmstrukturen zu erleichtern, die mit inerten oder reaktiven Gasen allein nicht erreicht werden können.
Die Verwendung organischer Gase in PVD-Verfahren ist besonders vorteilhaft für die Herstellung von Polymerfilmen, die bestimmte chemische Funktionalitäten erfordern. Mit Ethylen lassen sich zum Beispiel Polyethylenfolien herstellen, die für ihre hervorragenden mechanischen Eigenschaften und ihre chemische Beständigkeit bekannt sind. Aus Propylen lassen sich Polypropylenfolien herstellen, die sehr hitze- und chemikalienbeständig sind.
Darüber hinaus können organische Gase mit anderen Gasen kombiniert werden, um Verbundfolien herzustellen, die eine Mischung von Eigenschaften aus organischen und anorganischen Komponenten aufweisen. Dieser hybride Ansatz ermöglicht die individuelle Anpassung der Folieneigenschaften, so dass die Folien für bestimmte Anwendungen in Branchen wie der Elektronik, der Optik und dem Maschinenbau maßgeschneidert werden können.
Zusammenfassend lässt sich sagen, dass die Einbeziehung organischer Gase in PVD-Verfahren neue Möglichkeiten für die Herstellung fortschrittlicher Polymerfolien und Verbundwerkstoffe eröffnet und die Entwicklung von Materialien mit einzigartigen und verbesserten Eigenschaften ermöglicht.
Regulierung des Gasdrucks
Der Gasdruck innerhalb des PVD-Prozesses spielt eine entscheidende Rolle bei der Bestimmung der Abscheidungsrate und der Qualität der Schicht. Dieser Parameter beeinflusst direkt das Verhalten des gasförmigen Materials auf seinem Weg vom Target zum Substrat.
Bei niedrigerem Gasdruck neigt das gasförmige Material dazu, gleichmäßiger zu diffundieren, was zu einer besseren Verdichtung und Homogenität der Schicht führt. Der Grund dafür ist, dass der reduzierte Druck die Kollisionen zwischen den Gasmolekülen minimiert, was einen geordneteren Abscheidungsprozess ermöglicht. Folglich weist die entstehende Schicht weniger Defekte und eine gleichmäßigere Struktur auf.
Umgekehrt können höhere Gasdrücke zu einer größeren Rauheit der Schicht führen. Unter diesen Bedingungen stößt das gasförmige Material häufiger zusammen, was den geordneten Abscheidungsprozess stören kann. Das Ergebnis ist ein weniger gleichmäßiger Film mit potenziell höherer Oberflächenrauheit. Es sei jedoch darauf hingewiesen, dass höhere Drücke auch die Abscheiderate erhöhen können, wenn auch auf Kosten der Schichtqualität.
Gasdruck | Filmqualität | Abscheiderate |
---|---|---|
Niedriger | Bessere Verdichtung und Homogenität | Langsamer |
Höher | Erhöhte Rauhigkeit | Schneller |
Der optimale Gasdruck wird häufig durch die spezifischen Anforderungen der Anwendung bestimmt, wobei ein Gleichgewicht zwischen dem Bedarf an qualitativ hochwertigen Schichten und dem Wunsch nach einer effizienten Abscheidungsrate besteht. Dieses empfindliche Gleichgewicht ist entscheidend für das Erreichen der gewünschten Eigenschaften des Endprodukts.
Anwendungsbereiche des PVD-Beschichtungsverfahrens
Elektronikindustrie
Im Bereich der Halbleiterbauelemente, integrierten Schaltkreise und Displays spielt das PVD-Verfahren (Physical Vapor Deposition) eine zentrale Rolle bei der Herstellung verschiedener Schichten. PVD wird insbesondere zur Herstellung von drei Haupttypen von Schichten eingesetzt: leitende Schichten, isolierende Schichten und optische Schichten.
Leitfähige Folien
Leitende Schichten sind wichtig, um den Stromfluss in elektronischen Geräten zu gewährleisten. Diese Schichten bestehen in der Regel aus Metallen wie Aluminium, Kupfer und Gold, die mit Techniken wie thermischer Verdampfung oder Sputtern abgeschieden werden. Die Wahl des Metalls und der Abscheidungsmethode kann sich erheblich auf die Leitfähigkeit, die Haftung und die Gesamtleistung der Schicht auswirken.
Isolierende Schichten
Isolierschichten hingegen sind entscheidend, um elektrische Kurzschlüsse zu verhindern und empfindliche Bauteile zu schützen. Materialien wie Siliziumdioxid (SiO₂) und Siliziumnitrid (Si₃N₄) werden üblicherweise zur Herstellung dieser Folien verwendet. Das PVD-Verfahren ermöglicht eine präzise Kontrolle der Schichtdicke und -gleichmäßigkeit, was für die Integrität und Zuverlässigkeit des Geräts von entscheidender Bedeutung ist.
Optische Folien
Optische Folien sollen die Interaktion des Lichts mit der Oberfläche des Geräts steuern, die Klarheit des Displays verbessern und Blendeffekte reduzieren. Diese Folien umfassen häufig Antireflexionsbeschichtungen und Schichten zur Verbesserung der Lichtdurchlässigkeit. Das PVD-Verfahren ermöglicht die Herstellung dieser Schichten mit spezifischen optischen Eigenschaften, wie Brechungsindex und Durchlässigkeit, die auf die Anforderungen des Geräts zugeschnitten sind.
Zusammenfassend lässt sich sagen, dass das PVD-Verfahren in der Elektronikindustrie unverzichtbar ist, da es eine vielseitige und präzise Methode zur Herstellung von leitenden, isolierenden und optischen Schichten bietet, die für moderne elektronische Geräte von grundlegender Bedeutung sind.
Optische Geräte
Das PVD-Verfahren (Physical Vapor Deposition) spielt eine entscheidende Rolle bei der Herstellung optischer Beschichtungen, die für die Verbesserung der Leistung verschiedener optischer Geräte unerlässlich sind. Zu diesen Beschichtungen gehören Antireflexbeschichtungen, Filme zur Verbesserung der Lichtdurchlässigkeit und Schutzschichten, die alle dazu dienen, die Interaktion des Lichts mit der Oberfläche des Geräts zu optimieren.
Arten von optischen Beschichtungen
-
Antireflexionsbeschichtungen: Diese Beschichtungen sind so konzipiert, dass sie die Lichtreflexion minimieren und so die Lichtmenge, die durch die optische Oberfläche hindurchgeht, erhöhen. Dies ist besonders wichtig bei Anwendungen wie Kameralinsen, Brillen und Sonnenkollektoren.
-
Filme zur Verbesserung der Durchlässigkeit: Diese Folien sind so konzipiert, dass sie die Durchlässigkeit für bestimmte Wellenlängen des Lichts erhöhen, was für Geräte wie optische Filter und Sensoren entscheidend ist.
-
Schutzschichten: Diese Beschichtungen schützen das darunter liegende Material vor Umwelteinflüssen wie Feuchtigkeit, Staub und mechanischen Beschädigungen und gewährleisten so die Langlebigkeit und Leistung des optischen Geräts.
Vorteile von PVD bei optischen Beschichtungen
- Präzision: Das PVD-Verfahren ermöglicht eine präzise Steuerung der Schichtdicke, was für das Erreichen der gewünschten optischen Eigenschaften entscheidend ist.
- Langlebigkeit: PVD-beschichtete optische Geräte weisen im Vergleich zu den mit anderen Verfahren beschichteten Geräten eine überragende Haltbarkeit auf und eignen sich daher ideal für den langfristigen Einsatz in verschiedenen Umgebungen.
- Vielseitigkeit: Mit dem PVD-Verfahren lässt sich eine breite Palette von Beschichtungen herstellen, die den spezifischen Anforderungen verschiedener optischer Anwendungen gerecht werden.
Anwendungen in optischen Geräten
Gerätetyp | Zweck der Beschichtung |
---|---|
Kameraobjektive | Antireflexionsbeschichtungen für eine bessere Abbildung |
Brillengläser | Antireflektierende und kratzfeste Schichten |
Solarpaneele | Antireflexionsbeschichtungen zur Maximierung der Energieerfassung |
Optische Filter | Verbesserung der Durchlässigkeit für bestimmte Wellenlängen |
Sensoren | Schutzschichten zur Gewährleistung einer gleichbleibenden Leistung |
Das PVD-Verfahren verbessert nicht nur die Funktionalität dieser Geräte, sondern verlängert auch ihre Lebensdauer, was es zu einer unverzichtbaren Technologie in der optischen Industrie macht.
Mechanische Komponenten
Im Bereich der Oberflächenbehandlung mechanischer Komponenten spielen PVD-Verfahren (Physical Vapor Deposition) eine entscheidende Rolle bei der Verbesserung ihrer Langlebigkeit und Leistung. PVD-Verfahren werden sorgfältig eingesetzt, um die Verschleißfestigkeit, Korrosionsbeständigkeit und Oxidationsbeständigkeit dieser Komponenten zu erhöhen. Dies führt zu einer erheblichen Verlängerung ihrer Lebensdauer und macht sie in anspruchsvollen industriellen Umgebungen zuverlässiger und langlebiger.
Bei der Anwendung von PVD in mechanischen Komponenten geht es nicht nur um das Aufbringen einer Schutzschicht, sondern um die Integration fortschrittlicher Materialwissenschaften, um Oberflächen zu schaffen, die extremen Bedingungen standhalten. So sind beispielsweise Bauteile in Automotoren, Luft- und Raumfahrtturbinen und Industriemaschinen oft harten Bedingungen ausgesetzt, die zu einer schnellen Abnutzung führen können. Durch das Aufbringen von PVD-Beschichtungen werden diese Komponenten gegen den durch Reibung, chemische Reaktionen und hohe Temperaturen verursachten Verschleiß gestärkt.
Darüber hinaus können PVD-Beschichtungen auf die spezifischen Anforderungen verschiedener mechanischer Komponenten zugeschnitten werden. Ganz gleich, ob es sich um ein hochpräzises Werkzeug in der Fertigung oder ein kritisches Teil in einem medizinischen Gerät handelt, die Möglichkeit, die Beschichtung individuell anzupassen, stellt sicher, dass jedes Bauteil unter seinen eigenen Bedingungen optimal funktioniert. Dieses Maß an individueller Anpassung wird erreicht, indem die Beschichtungsparameter, wie z. B. die Art des Zielmaterials, der Gasdruck und die Temperatur, variiert werden, um die Eigenschaften des entstehenden Films fein abzustimmen.
Zusammenfassend lässt sich sagen, dass der Einsatz von PVD-Verfahren bei der Oberflächenbehandlung mechanischer Komponenten eine strategische Investition in die Verbesserung ihrer Haltbarkeit und Leistung ist, die letztlich zur Effizienz und Zuverlässigkeit verschiedener industrieller Anwendungen beiträgt.
Dekorative Beschichtungen
Mit dem PVD-Verfahren lassen sich dekorative Schichten herstellen, die die Ästhetik verschiedener Produkte verbessern. Diese Folien, die sich durch ihren metallischen Glanz und ihre leuchtenden Farben auszeichnen, werden häufig in Bereichen wie Schmuck, Uhren und Haushaltsgegenständen eingesetzt. Das Verfahren ermöglicht eine präzise Kontrolle der Schichtdicke und der Gleichmäßigkeit und stellt sicher, dass das Endprodukt die hohen Anforderungen an die Optik und Haltbarkeit erfüllt, die in diesen Branchen gelten.
In der Schmuckbranche bieten PVD-Beschichtungen eine anspruchsvolle Oberfläche, die das Aussehen von Edelmetallen zu einem Bruchteil der Kosten imitieren kann. Dies ist besonders vorteilhaft für die Großserienproduktion, bei der die Beibehaltung eines luxuriösen Aussehens von entscheidender Bedeutung ist. Uhren wiederum profitieren von PVD-Beschichtungen, die nicht nur ihr Aussehen verbessern, sondern auch kratz- und korrosionsbeständig sind und so die Lebensdauer dieser Zeitmesser verlängern.
Auch Haushaltsprodukte wie Küchengeräte und Dekorationsartikel erhalten durch PVD-Beschichtungen ein modernes und elegantes Aussehen. Die Möglichkeit, verschiedene Farben und Muster in die Beschichtungen einzubringen, eröffnet eine breite Palette von Designmöglichkeiten und macht PVD zu einem vielseitigen Werkzeug für die Herstellung von Konsumgütern.
Darüber hinaus ist das PVD-Verfahren umweltfreundlich, da es unter Vakuumbedingungen abläuft, wodurch Abfälle minimiert und die mit herkömmlichen Beschichtungsmethoden verbundenen Umweltbelastungen verringert werden. Dieser Nachhaltigkeitsaspekt macht das Verfahren für Branchen interessant, in denen sowohl Ästhetik als auch Umweltverantwortung von größter Bedeutung sind.
Vorteile und Herausforderungen des PVD-Verfahrens
Vorteile
PVD-Beschichtungsverfahren bieten mehrere überzeugende Vorteile, die sie zu einer bevorzugten Wahl in verschiedenen Branchen machen. Einer der wichtigsten Vorteile ist die Herstellung vonhochwertigen Schichten. Diese Folien weisen eine außergewöhnlicheHaftung,Gleichmäßigkeitundstrukturelle Integritätdie für die Verbesserung der Leistung der beschichteten Materialien entscheidend sind. In der Elektronikindustrie beispielsweise sorgen PVD-beschichtete leitfähige Folien für eine hervorragende elektrische Leitfähigkeit und minimale Signalverluste, während bei optischen Geräten die Beschichtungen für präzise optische Eigenschaften sorgen, die die Leistung der Geräte verbessern.
Ein weiterer bemerkenswerter Vorteil ist dieUmweltfreundlichkeit von PVD-Verfahren. Im Gegensatz zu einigen anderen Beschichtungsmethoden arbeitet PVD unter Vakuumbedingungen, wodurch die Freisetzung schädlicher Stoffe in die Umwelt minimiert wird. Dies macht PVD zu einer nachhaltigen Option, insbesondere in Branchen mit strengen Umweltvorschriften. Außerdem wird durch die Verwendung von Inertgasen wie Argon und Helium sichergestellt, dass die Reinheit der Schichten erhalten bleibt, ohne dass reaktive Nebenprodukte entstehen, die die Umwelt belasten könnten.
DieVielseitigkeit von PVD-Verfahren ist ebenfalls eine wichtige Stärke. PVD kann auf eine Vielzahl von Materialien angewendet werden, darunter Metalle, Keramiken und Polymere, und eignet sich daher für die unterschiedlichsten Anwendungen. Ob es um die Herstellung dünner Schichten für Halbleiter, die Verbesserung der Haltbarkeit mechanischer Komponenten oder die Herstellung dekorativer Beschichtungen für Konsumgüter geht, PVD bietet eine flexible Lösung, die auf spezifische Anforderungen zugeschnitten werden kann. Der Einsatz reaktiver Gase wie Sauerstoff und Stickstoff ermöglicht beispielsweise die Herstellung komplexer Oxid- und Nitridschichten, wodurch sich die Palette der möglichen Anwendungen noch erweitert.
Zusammenfassend lässt sich sagen, dass die Kombination aus hochwertiger Schichtherstellung, Umweltverträglichkeit und breiter Anwendbarkeit PVD-Beschichtungsverfahren zu einer äußerst vorteilhaften Technologie für zahlreiche Branchen macht.
Herausforderungen
Eine der größten Herausforderungen im Zusammenhang mit PVD-Verfahren (Physical Vapor Deposition) sind die erheblichenKosten der Ausrüstung. Fortgeschrittene PVD-Systeme, wie z. B. die Elektronenstrahlverdampfung oder die gepulste Laserabscheidung, erfordern hochentwickelte Maschinen und präzise Kontrollsysteme, die für kleinere Betriebe unerschwinglich sein können. Außerdem erfordern Wartung und Kalibrierung dieser Systeme spezielle Fachkenntnisse, was die Gesamtkosten weiter in die Höhe treibt.
Eine weitere kritische Herausforderung istAbscheidungsraten. Die Erzielung optimaler Abscheideraten ist für eine effiziente Produktion von entscheidender Bedeutung, kann aber durch eine Vielzahl von Faktoren beeinflusst werden, darunter Gasdruck, Substrattemperatur und die Art des verwendeten Zielmaterials. Langsame Abscheideraten können zu längeren Verarbeitungszeiten führen, was die Betriebskosten erhöht und möglicherweise die Qualität der abgeschiedenen Schicht beeinträchtigt. Umgekehrt können höhere Abscheideraten zu Schichten mit suboptimalen Eigenschaften führen, z. B. mit geringerer Dichte oder erhöhter Rauheit.
Kontrolle der Schichtdicke ist ebenfalls eine große Hürde bei PVD-Verfahren. Die Gewährleistung einer gleichmäßigen Schichtdicke auf dem Substrat ist für die Leistung und Zuverlässigkeit des Endprodukts von entscheidender Bedeutung. Die genaue Kontrolle der Schichtdicke kann jedoch eine Herausforderung sein, insbesondere bei komplexen Geometrien oder großflächigen Substraten. Schwankungen in der Schichtdicke können zu Unstimmigkeiten in den Eigenschaften der Schicht führen, z. B. in den optischen, mechanischen oder elektrischen Merkmalen, was sich nachteilig auf die beabsichtigte Anwendung auswirken kann.
Um diesen Herausforderungen zu begegnen, konzentrieren sich die laufenden Forschungen und technologischen Fortschritte auf die Entwicklung kostengünstigerer Anlagen, die Optimierung der Abscheidungsparameter und die Verbesserung der Kontrollmechanismen für die Schichtdicke. Diese Bemühungen zielen darauf ab, die Effizienz und Zuverlässigkeit von PVD-Prozessen zu verbessern und sie für verschiedene Branchen zugänglicher und effektiver zu machen.
Kontaktieren Sie uns für eine kostenlose Beratung
Die Produkte und Dienstleistungen von KINTEK LAB SOLUTION werden von Kunden auf der ganzen Welt anerkannt. Unsere Mitarbeiter helfen Ihnen gerne bei allen Fragen weiter. Kontaktieren Sie uns für eine kostenlose Beratung und sprechen Sie mit einem Produktspezialisten, um die am besten geeignete Lösung für Ihre Anwendungsanforderungen zu finden!