Einleitung
Inhaltsübersicht
- Einführung
- Überblick über das kaltisostatische Pressen
- Arten des kaltisostatischen Pressens
- Vorteile des kaltisostatischen Pressens gegenüber dem uniaxialen Gesenkpressen
- Kaltisostatisches Pressen bei der Herstellung komplex geformter Bauteile
- Vergleich von CIP und Spritzgießen für die Großserienproduktion
- Historischer Überblick über die Verwendung von CIP bei der Herstellung von Aluminiumoxid-Keramik
- Einsatz von CIP bei der Herstellung von Zündkerzenisolatoren
- Kaltisostatische Pressen
- Kaltisostatisches Pressen
- WAS IST KALTISOSTATISCHES PRESSEN BESCHREIBUNG
- Kaltisostatisches Pressen
- Prozess des kaltisostatischen Pressens
- Vorteile des kaltisostatischen Pressens für Aluminiumoxid-Keramik
- Nachteile des kaltisostatischen Pressens für Keramiken
- Anwendungen des kaltisostatischen Pressens
- Alternative Komprimierungstechnologien
- Fazit
Kalt-Isostatisches Pressen (CIP)ist ein weit verbreitetes Herstellungsverfahren in verschiedenen Branchen, darunter Keramik, Metallverarbeitung und Pharmazie. Dabei wird aus allen Richtungen gleichmäßiger Druck auf ein Material ausgeübt, das sich in einer flexiblen Form oder einem Beutel befindet. Mit diesem Verfahren lassen sich eine gleichmäßige Dichte erreichen und komplexe Bauteile mit komplizierten Geometrien formen. Das CIP-Verfahren bietet mehrere Vorteile gegenüber dem herkömmlichen einachsigen Gesenkpressen, z. B. die Möglichkeit, komplexere Formen zu formen, und die Verringerung von Verformungen und Rissen aufgrund einer gleichmäßigen Partikelpackung. In diesem Blogbeitrag werden wir uns mit der Anwendung, den Vorteilen und den Grenzen des kaltisostatischen Pressens befassen.
Überblick über das kaltisostatische Pressen
Erläuterung des kaltisostatischen Pressens
Kaltisostatisches Pressen (CIP) ist eine Materialverarbeitungstechnik, bei der auf ein Pulvermaterial in allen Richtungen der gleiche Druck ausgeübt wird. Dieses Verfahren wird eingesetzt, um das Pulver zu einer festen Masse zu verdichten und ein Rohteil mit ausreichender Festigkeit für die Handhabung und Weiterverarbeitung zu schaffen.
Unterscheidung zwischen Nasssack- und Trockensack-Isostatisches Pressen
Eine Variante des kaltisostatischen Pressens ist das Nasssackverfahren. Bei diesem Verfahren wird das Pulver in eine Form gefüllt und außerhalb des Druckbehälters dicht verschlossen. Die Form wird dann in eine Hochdruckflüssigkeit innerhalb des Behälters getaucht, und das Pulver wird durch isostatischen Druck in eine Form gepresst. Die Wet-Bag-Technologie eignet sich ideal für die Produktion mehrerer Formen und kleiner bis großer Mengen.
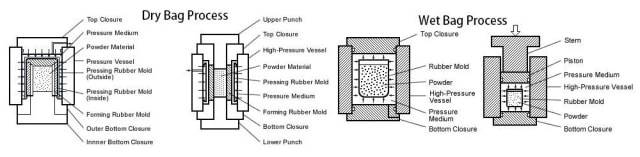
Beim isostatischen Pressen in Trockenbeuteln hingegen wird eine integrierte Form im Druckbehälter selbst hergestellt. Das Pulver wird in die Form gegeben, die Form wird versiegelt, und das Pulver wird unter Druck gepresst. Bei diesem Verfahren muss die Form nicht mehr in eine separate Flüssigkeit getaucht werden, was die Automatisierung erleichtert.
Die Rolle der Pulverqualität und der Werkzeugkonstruktion im Prozess
Die Qualität des Pulvers, das beim kaltisostatischen Pressen verwendet wird, spielt eine entscheidende Rolle für das Endprodukt. Das Pulver sollte die richtige Korngrößenverteilung, Fließfähigkeit und Dichte aufweisen, um eine effiziente und gleichmäßige Verdichtung zu gewährleisten. Darüber hinaus sollte das Werkzeugdesign, einschließlich der verwendeten Form oder des Beutels, sorgfältig auf die spezifischen Anforderungen des Pulvermaterials und die gewünschte Form abgestimmt sein.
Ein geeignetes Werkzeugdesign und die Qualität des Pulvers sind entscheidend, um die gewünschte Dichte und Festigkeit des Endprodukts zu erreichen. Dies ist besonders wichtig in Branchen wie der Luft- und Raumfahrt, der Automobilindustrie und der Medizintechnik, wo qualitativ hochwertige und zuverlässige Komponenten entscheidend sind.
Zusammenfassend lässt sich sagen, dass das kaltisostatische Pressen ein vielseitiges Materialverarbeitungsverfahren ist, das die Verdichtung von Pulvermaterialien zu festen Teilen ermöglicht. Die Wahl zwischen Nasssack- und Trockensacktechnik hängt von den spezifischen Produktionsanforderungen ab. Darüber hinaus spielen die Qualität des Pulvers und die Werkzeugkonstruktion eine wichtige Rolle, um die gewünschten Ergebnisse im Endprodukt zu gewährleisten.
Arten des kaltisostatischen Pressens
Detaillierte Beschreibung der Nasssacktechnik
Bei der Nasssacktechnik des kaltisostatischen Pressens wird das Pulvermaterial in eine Form gefüllt und außerhalb des Druckbehälters dicht verschlossen. Die gefüllte Form wird dann in eine Druckflüssigkeit innerhalb des Druckbehälters getaucht. Auf die Außenfläche der Form wird ein isostatischer Druck ausgeübt, der das Pulver zu einer festen Masse komprimiert.
Diese Methode ist nicht so verbreitet wie die andere Art des kaltisostatischen Pressens, aber es gibt weltweit über 3000 Nasssackpressen. Nasssäcke gibt es in verschiedenen Größen, die von 50 mm bis 2000 mm Durchmesser reichen.
Die Verarbeitung von Material mit der Nasssacktechnologie kann zwischen 5 und 30 Minuten dauern und ist damit ein relativ langsamer Prozess. Durch den Einsatz von Hochleistungspumpen und verbesserten Beladungsmechanismen kann der Prozess jedoch beschleunigt werden.
Erläuterung der Trockenbeutel-Presstechnik
Bei der Trockenbeutelpresstechnik wird hingegen eine Form hergestellt, die in den Druckbehälter integriert ist. Bei diesem Verfahren wird das Pulver in die Form gegeben, die dann verschlossen wird. Dann wird Druck ausgeübt und das Teil wird ausgestoßen.
Im Vergleich zum Wet-Bag-Verfahren ist das Dry-Bag-Verfahren automatisierbar und eignet sich für das Pressen großer Stückzahlen bei hohen Produktionsraten. Durch die Integration der Form in den Druckbehälter entfällt der Schritt des Eintauchens, was das Verfahren effizienter macht.
Vergleich der Anwendungen für beide Techniken
Die Wahl zwischen Nasssack- und Trockensackverfahren hängt von den spezifischen Anforderungen der jeweiligen Anwendung ab. Die Nasssacktechnik eignet sich ideal für die Herstellung mehrerer Formen und kleiner bis großer Mengen sowie für das Pressen großer Produkte. Sie ermöglicht die Herstellung komplizierter Formen und erzielt eine hohe Rohdichte.
Das Trockenbeutelpressen hingegen eignet sich besser für die Automatisierung und hohe Produktionsraten. Es lässt sich leichter in den Herstellungsprozess integrieren und macht den Schritt des Eintauchens überflüssig, was zu kürzeren Produktionszeiten führt.
Zusammenfassend lässt sich sagen, dass sowohl das Nassbeutel- als auch das Trockenbeutelverfahren ihre Vorteile haben und für unterschiedliche Anwendungen eingesetzt werden. Die Entscheidung zwischen beiden Verfahren hängt von Faktoren wie der gewünschten Form, der Produktionsmenge und dem erforderlichen Automatisierungsgrad ab.
Vorteile des kaltisostatischen Pressens gegenüber dem uniaxialen Gesenkpressen
Fähigkeit, komplexere Formen zu formen
Das kaltisostatische Pressen (CIP) bietet den Vorteil, dass es im Vergleich zum uniaxialen Gesenkpressen komplexere Formen ermöglicht. Beim CIP wird der Druck gleichmäßig über die gesamte Oberfläche der Form ausgeübt, was die Verdichtung komplizierter und detaillierter Formen ermöglicht. Dies ist besonders vorteilhaft bei der Herstellung von Bauteilen mit komplizierten Geometrien oder Designs, die mit dem uniaxialen Gesenkpressen nur schwer zu erreichen sind.

Verringerung von Verzug und Rissbildung durch gleichmäßige Partikelpackung
Einer der Hauptvorteile des kaltisostatischen Pressens gegenüber dem einachsigen Gesenkpressen ist die Reduzierung von Verformungen und Rissen im Endprodukt. Beim CIP wird der Druck gleichmäßig aufgebracht, was zu einer gleichmäßigeren Partikelpackung und geringeren Druckgradienten führt. Dies führt zu einer homogeneren Dichteverteilung und verringert die Wahrscheinlichkeit von Verformungen und Rissen im fertigen Bauteil. Dieser Vorteil ist vor allem bei komplex geformten Bauteilen entscheidend.
Technisch gesehen bietet das CIP-Verfahren eine höhere und gleichmäßigere Dichte bei einem gegebenen Verdichtungsdruck, was es besonders für spröde oder feine Pulver geeignet macht. Da beim CIP-Verfahren keine Reibung an den Matrizenwänden auftritt, werden außerdem Probleme im Zusammenhang mit der Schmiermittelentfernung vermieden und höhere Pressdichten erzielt.
Darüber hinaus bietet CIP den Vorteil einer gleichmäßigeren Schrumpfung während des Sinterns aufgrund der gleichmäßigen Rohdichte. Dies ist für die Beibehaltung einer guten Formkontrolle und das Erreichen gleichmäßiger Eigenschaften des Endprodukts von wesentlicher Bedeutung. Außerdem benötigt CIP kein Wachsbindemittel wie das uniaxiale Gesenkpressen, so dass keine Entwachsung erforderlich ist.
Zusammenfassend lässt sich sagen, dass die Vorteile des kaltisostatischen Pressens gegenüber dem uniaxialen Gesenkpressen in der Möglichkeit liegen, komplexere Formen zu formen, und in der Verringerung von Verformungen und Rissen aufgrund einer gleichmäßigen Partikelpackung. Diese Vorteile machen CIP zu einem bevorzugten Verfahren für die Herstellung von Bauteilen mit komplizierten Geometrien und zur Erzielung hochwertiger, homogener Produkte.
Kaltisostatisches Pressen bei der Herstellung komplex geformter Bauteile
Vergleich von CIP und Spritzgießen für die Großserienproduktion
Wenn komplex geformte Bauteile benötigt werden, die die Möglichkeiten des einachsigen Gesenkpressens übersteigen, und ein großer Produktionsdurchsatz erforderlich ist, sind KVP und Spritzgießen die beiden wichtigsten Optionen. CIP war das erste in der Literatur beschriebene Hightech-Verfahren zur Herstellung von Aluminiumoxidkeramik, das Daubenmeyer 1934 vorstellte. In der Tat sind Zündkerzenisolatoren wahrscheinlich das weltweit am meisten produzierte CIP-gefertigte Keramikteil. Ein erheblicher Teil der jährlich hergestellten 3 Milliarden Zündkerzenisolatoren wird im CIP-Verfahren hergestellt. Wie beim einachsigen Gesenkpressen besteht das CIP-Rohmaterial in der Regel aus einfachem gemahlenem Bayer-Aluminiumoxid, gemahlenem und sprühgetrocknetem Bayer-Aluminiumoxid oder in seltenen Fällen aus sprühgetrockneten High-Tech-SolGel-Nanopulvern. Im Allgemeinen ist das CIP-Verfahren in der Industrie jedoch nicht so verbreitet wie das Spritzgießen. CIP wird im Allgemeinen nur verwendet, wenn sehr komplexe Formen erforderlich sind und das Spritzgießen aus irgendeinem Grund nicht praktikabel ist.
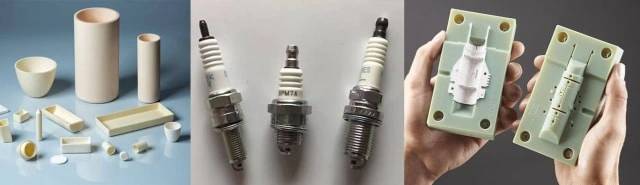
Historischer Überblick über die Verwendung von CIP bei der Herstellung von Aluminiumoxidkeramik
Das kalt-isostatische Pressen (CIP) ist eine pulverbasierte, endkonturnahe Technologie zur Herstellung von Metall- und Keramikkomponenten. Das CIP-Verfahren wird häufig für die Verarbeitung von Keramiken eingesetzt, ist aber bei Metallen nicht so weit verbreitet. Jüngste Entwicklungen im Bereich der Prozessfähigkeit und der Pulvermetallurgie haben jedoch dazu geführt, dass CIP zunehmend für die Herstellung von Hochleistungsmetallteilen eingesetzt wird. Vorteile wie Festkörperverfahren, gleichmäßiges Gefüge, Formkomplexität, niedrige Werkzeugkosten und Skalierbarkeit des Prozesses haben CIP zu einem praktikablen Verfahren für Metalle gemacht. Darüber hinaus hat die Möglichkeit, endkonturnahe Teile mit minimalem Materialabfall herzustellen, die Akzeptanz des Verfahrens in Nischenanwendungen wie der Luft- und Raumfahrt und der Automobilindustrie erhöht.
Einsatz von CIP bei der Herstellung von Zündkerzenisolatoren
Das kaltisostatische Pressen (CIP) wird seit Jahrzehnten von Herstellern in aller Welt erfolgreich eingesetzt. CIP wird zur Verfestigung von Metall- und Keramikpulvern verwendet, um ein "grünes" Teil herzustellen, das weiterverarbeitet werden kann, z. B. durch Walzen, Bearbeiten oder Sintern.
Bei typischen Drücken von 1.035 bis 4.138 bar (15.000 bis 60.000 psi) und einer Umgebungstemperatur von bis zu 93°C (200°F) kann CIP 95% der theoretischen Dichte für Keramik erreichen.
Ein bewährtes Verfahren für Hochleistungsteile Zu den gängigen Anwendungen für das kaltisostatische Pressen gehören die Konsolidierung von Keramikpulvern, das Verdichten von Graphit, feuerfesten Materialien und elektrischen Isolatoren sowie von anderen Feinkeramiken für zahnmedizinische und medizinische Anwendungen.
Die Technologie dehnt sich auf neue Anwendungen aus, wie z. B. das Pressen von Sputtertargets, Beschichtungen von Ventilteilen in einem Motor, um den Verschleiß der Zylinderköpfe zu minimieren, Telekommunikation, Elektronik, Luft- und Raumfahrt und Automobilbau.
Kaltisostatische Pressen
EPSI-Kaltisostatische Pressen (CIP) werden zur Herstellung von ungesinterten oder grün eingefärbten Metallpulverkomponenten in einem vorbereitenden Verdichtungsschritt vor dem Walzen, Bearbeiten oder Sintern eingesetzt. Unsere CIP-Systeme werden von Unternehmen auf der ganzen Welt zur effektiven Herstellung einwandfreier Komponenten für die Luft- und Raumfahrt, das Militär, die Industrie und die Medizintechnik eingesetzt. Technologieführer auf der ganzen Welt wissen, dass unsere kaltisostatischen Pressen so konstruiert sind, dass die Teile leicht entnommen werden können und eine ausreichende Grünfestigkeit für die weitere Bearbeitung und das Sintern aufweisen.
Kaltisostatisches Pressen
Kaltisostatisches Pressen hat den Vorteil, dass es sich für die Herstellung von Teilen eignet, bei denen die hohen Anschaffungskosten für Presswerkzeuge nicht gerechtfertigt sind oder wenn sehr große oder komplexe Presslinge benötigt werden. Eine Vielzahl von Pulvern kann im kommerziellen Maßstab isostatisch gepresst werden, darunter Metalle, Keramiken, Kunststoffe und Verbundwerkstoffe. Die für die Verdichtung erforderlichen Drücke reichen von weniger als 5.000 psi bis zu mehr als 100.000 psi (34,5 bis 690 MPa). Pulver werden in elastomeren Formen entweder im Nass- oder im Trockensackverfahren verdichtet.
Bei der Auswahl von Dienstleistungen im Bereich des isostatischen Kaltpressens sind die Materialeigenschaften zu berücksichtigen. Aluminium- und Magnesiumlegierungen, Hartmetalle und Schneidwerkzeuge, Kohlenstoff und Graphit, Keramik und Verbundwerkstoffe sind nur einige der Materialien und Komponenten, die mit CIP hergestellt werden können. Einige Dienstleister für kaltisostatisches Pressen sind auf Beschichtungen und thermische Spritzschichten, Kupferlegierungen oder Diamant und diamantähnliche Materialien spezialisiert. Andere arbeiten mit elektronischen oder elektrischen Materialien, Sprengstoffen oder Pyrotechnik oder speziellen und geschützten Materialien.
WAS IST KALTISOSTATISCHES PRESSEN BESCHREIBUNG
Kaltisostatisches Pressen (CIP) ist ein Verfahren zur Formung und Verdichtung von Pulvern zu Komponenten unterschiedlicher Größe und Form. Beim kaltisostatischen Pressen in nassen Beuteln (CIP) wird das Material vorgeformt und dann in einem flexiblen Beutel oder einer Form versiegelt. Der Beutel wird in einem Druckbehälter mit einer Hydraulikflüssigkeit (z. B. Öl oder Wasser) gefüllt. Die Flüssigkeit wird mit einem Druck beaufschlagt, der in der Regel zwischen 10.000 und 60.000 psi liegt und sich gleichmäßig auf das Material verteilt. Diese Methode hilft, Verformungen zu verringern, die Genauigkeit zu verbessern und das Risiko von Lufteinschlüssen und Hohlräumen zu reduzieren. Es wird häufig bei der Herstellung von Komponenten für die Medizintechnik, die Luft- und Raumfahrt und die Automobilindustrie eingesetzt.
Die Kontrolle der Abmessungen ist beim CIP-Verfahren geringer als beim uniaxialen Pressen. Wenn Sie z. B. einen Durchmesser von genau 5 mm benötigen, müssen Sie vorher einige Versuche, Fehler und Berechnungen in Ihrer Form und Ihrem Füllverfahren durchführen, um dieses Ziel zu erreichen. Aber wenn man das geschafft hat, ist es ein sehr wiederholbarer Prozess, der einige deutliche Vorteile bietet. Dazu gehört auch die Möglichkeit, Pellets mit sehr großem Aspektverhältnis zu pressen. Zündkerzen sind ein Beispiel für ein gängiges Produkt, das in industriellem Maßstab kaltisostatisch gepresst wird.
Kaltisostatisches Pressen
Das kaltisostatische Pressen (CIP) wird bei Raumtemperatur durchgeführt und verwendet eine Form aus einem elastomeren Material wie Urethan, Gummi oder Polyvinylchlorid. Die Flüssigkeit beim kaltisostatischen Pressen ist normalerweise Öl oder Wasser. Der Flüssigkeitsdruck während des Vorgangs liegt in der Regel zwischen 60.000 lbs/in2 (400 MPa) und 150.000 lbs/in2 (1000 MPa). Ein Nachteil dieses Herstellungsverfahrens ist die geringe geometrische Genauigkeit aufgrund der flexiblen Form. Zunächst wird das Pulver durch kaltes isostatisches Pressen auf eine sehr gleichmäßige Dichte verdichtet. Anschließend wird der Grünling in der Regel auf konventionelle Weise gesintert, um das gewünschte Teil herzustellen.
Verfahren des kaltisostatischen Pressens
Erläuterung des CIP-Verfahrens
Kaltisostatisches Pressen (CIP) ist ein Verfahren zur Verarbeitung von Werkstoffen, bei dem Pulver durch Einschließen in eine Elastomerform verdichtet werden. Die Form besteht aus Materialien wie Urethan, Gummi oder Polyvinylchlorid, die eine geringe Verformungsresistenz aufweisen. Anschließend wird gleichmäßig Flüssigkeitsdruck auf die Form ausgeübt, um sie zu komprimieren. Dieses Verfahren basiert auf dem Pascal'schen Gesetz, das besagt, dass der Druck, der auf eine eingeschlossene Flüssigkeit ausgeübt wird, in alle Richtungen übertragen wird, ohne dass sich die Größe ändert.
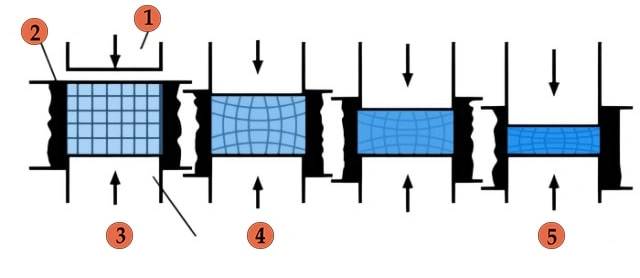
CIP kann für verschiedene Materialien wie Kunststoffe, Graphit, pulverförmige Metallurgie, Keramik und Sputtertargets verwendet werden. Es wird üblicherweise verwendet, um ein "rohes" Teil mit ausreichender Festigkeit für die Handhabung und Verarbeitung zu erhalten, das dann weiter gesintert werden kann, um die endgültige Festigkeit zu erreichen.
Automatisierung des CIP-Prozesses
Das CIP-Verfahren kann mit speziellen Geräten automatisiert werden. Das zu verarbeitende Material wird in einer Elastomerform versiegelt und in eine Druckkammer gelegt. Ein flüssiges Medium, z. B. Wasser oder Öl, wird in die Kammer gepumpt, und die Form wird von allen Seiten gleichmäßig mit hohem Druck beaufschlagt. Diese Automatisierung gewährleistet eine gleichmäßige und präzise Druckbeaufschlagung, was zu qualitativ hochwertigen Endprodukten führt.
Die Automatisierung des CIP-Prozesses bietet mehrere Vorteile. Sie verbessert die Effizienz, indem sie die manuelle Arbeit reduziert und die Produktionsrate erhöht. Außerdem wird eine gleichmäßige Druckanwendung gewährleistet, was die Gesamtqualität und Zuverlässigkeit der Endprodukte verbessert. Darüber hinaus ermöglicht die Automatisierung eine bessere Kontrolle und Überwachung der Prozessparameter, was zu einer verbesserten Prozessoptimierung und Kosteneinsparungen führt.
Druckbeaufschlagungs- und Druckentlastungszyklen bei CIP
Das CIP-Verfahren umfasst Druckbeaufschlagungs- und Druckentlastungszyklen, um die gewünschte Verdichtung des Pulvers zu erreichen. Während des Druckbeaufschlagungszyklus wird das flüssige Medium in die Druckkammer gepumpt, wodurch ein gleichmäßiger Druck auf die Elastomerform ausgeübt wird. Durch diesen Druck werden die Pulver verdichtet und es entsteht ein hochkompakter Feststoff.
Nachdem die gewünschte Verdichtung erreicht ist, beginnt der Druckentlastungszyklus. Der Druck in der Kammer wird allmählich abgelassen, so dass sich die Form entspannen kann und das verdichtete Material entnommen werden kann. Dieser Zyklus stellt sicher, dass das verdichtete Material leicht und ohne Verformung oder Beschädigung aus der Form entnommen werden kann.
Die Druckbeaufschlagungs- und Druckentlastungszyklen werden sorgfältig gesteuert, um die gewünschte Dichte und Festigkeit des verdichteten Materials zu erreichen. Die Parameter, wie z. B. die Höhe des Drucks, die Dauer und die Änderungsrate, können je nach den spezifischen Anforderungen des zu verarbeitenden Materials angepasst werden.
Zusammenfassend lässt sich sagen, dass das kaltisostatische Pressen (CIP) eine vielseitige Methode zur Verdichtung von Pulvern und zur Formgebung von Materialien ist. Durch das Einschließen von Pulvern in eine Elastomerform und die Anwendung eines gleichmäßigen Drucks können mit CIP hochkompakte Feststoffe für verschiedene Anwendungen hergestellt werden. Die Automatisierung des CIP-Prozesses bietet eine höhere Effizienz und Kontrolle, während die Zyklen zur Druckbeaufschlagung und Druckentlastung die gewünschte Dichte und Festigkeit des verdichteten Materials gewährleisten.
Vorteile des kaltisostatischen Pressens für Aluminiumoxid-Keramik
Vergleich von CIP mit einachsigem Gesenkpressen und anderen keramischen Formgebungsverfahren
Kaltisostatisches Pressen (CIP) ist eine pulverbasierte, endkonturnahe Technologie zur Herstellung von Metall- und Keramikteilen. Das CIP-Verfahren wird häufig für die Verarbeitung von Keramiken eingesetzt, ist aber bei Metallen nicht so weit verbreitet. Jüngste Entwicklungen im Bereich der Prozessfähigkeit und der Pulvermetallurgie haben jedoch dazu geführt, dass CIP zunehmend für die Herstellung von Hochleistungsmetallteilen eingesetzt wird. Vorteile wie die Verarbeitung im festen Zustand, die einheitliche Mikrostruktur, die Komplexität der Form, die niedrigen Werkzeugkosten und die Skalierbarkeit des Prozesses haben CIP zu einer praktikablen Verarbeitungsmethode für Metalle gemacht.
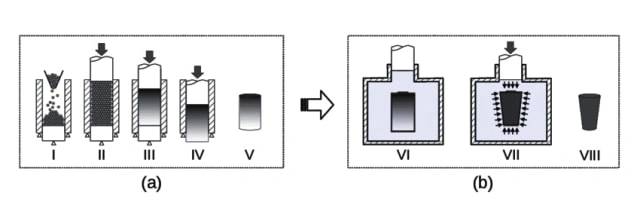
Einige der wichtigsten Vorteile von CIP für Aluminiumoxid-Keramik im Vergleich zum uniaxialen Formpressen sind folgende:
-
Es sind komplexere Formen möglich: CIP ermöglicht die Herstellung komplexerer Formen als das uniaxiale Gesenkpressen. Dies liegt daran, dass beim CIP flexible Formen verwendet werden, die komplizierte Designs und Formen aufnehmen können.
-
Stark reduzierte Pressdruckgradienten: Durch das CIP-Verfahren werden die Druckgradienten beim Pressen erheblich reduziert, was dazu beiträgt, Verformungen und Risse während des Formprozesses zu minimieren. Dadurch wird sichergestellt, dass die endgültigen keramischen Komponenten eine verbesserte Maßgenauigkeit und strukturelle Integrität aufweisen.
Vorteile von CIP für komplexe Teile mit kleinen Produktionsserien
CIP bietet mehrere Vorteile für die Herstellung komplexer Teile mit kleinen Produktionsserien. Zu diesen Vorteilen gehören:
-
Niedrige Formkosten: CIP erfordert geringe Formkosten und ist daher ideal für die Herstellung komplexer Teile mit kleinen Produktionsserien. Im Gegensatz zu anderen keramischen Formgebungsverfahren sind für CIP keine teuren Formen erforderlich, was zu einer Senkung der Herstellungskosten beiträgt.
-
Keine Formkosten für Post-CIP: Zusätzlich zu den niedrigen Formkosten entfällt bei CIP auch der Bedarf an Formen für Nach-CIP-Prozesse. Dies führt zu einer weiteren Senkung der Produktionskosten und ermöglicht eine größere Flexibilität bei der Herstellung komplexer Teile.
-
Keine Größenbeschränkung: Beim CIP-Verfahren gibt es keine Größenbeschränkungen, mit Ausnahme der Grenzen der Presskammer. Dadurch eignet es sich für die Herstellung sehr großer Bauteile, insbesondere solcher mit komplexen Formen. Tatsächlich wurden bereits Bauteile mit einem Gewicht von über 1 Tonne erfolgreich mit CIP hergestellt.
-
Kurze Bearbeitungszyklen: Das CIP-Verfahren zeichnet sich durch kurze Zykluszeiten aus, da es keine Trocknung und keinen Binderausbrand erfordert. Dies bedeutet, dass die geformten keramischen Komponenten im Vergleich zu anderen Verfahren schneller gesintert werden können, was zu einer höheren Produktionseffizienz führt.
Das CIP-Verfahren bietet zwar zahlreiche Vorteile für Aluminiumoxidkeramik, doch sind auch einige seiner Grenzen zu beachten. Dazu gehören die begrenzte Kontrolle der Abmessungen, die im Vergleich zum Pulverspritzguss (PIM) geringere Formkomplexität und die Notwendigkeit von Pulvern mit ausgezeichneter Fließfähigkeit.
Insgesamt ist das kaltisostatische Pressen ein vielseitiges und kostengünstiges Verfahren zur Herstellung von Aluminiumoxidkeramik mit komplexen Formen und kleinen Produktionsmengen. Seine Vorteile in Bezug auf die Komplexität der Formen, die geringeren Druckgradienten, die niedrigen Formkosten und die kürzeren Bearbeitungszeiten machen es zu einer beliebten Wahl in verschiedenen Branchen wie der Automobilindustrie, der Luft- und Raumfahrt und der Telekommunikation.
Nachteile des kaltisostatischen Pressens für Keramiken
Herausforderungen bei der Maßkontrolle und Formkomplexität
Das kaltisostatische Pressen (CIP) ist ein Verfahren zur Pulververdichtung, das zur Herstellung von sinterfähigen Teilen verwendet wird. Bei der Anwendung von CIP für Keramik gibt es jedoch einige Herausforderungen im Zusammenhang mit der Maßkontrolle und der Formkomplexität.
Die im Vergleich zum mechanischen Pressen oder Strangpressen geringere Genauigkeit der gepressten Oberflächen in der Nähe des flexiblen Beutels macht häufig eine Nachbearbeitung erforderlich. Dies bedeutet, dass zusätzliche Schritte erforderlich sein können, um die gewünschten Abmessungen und Formen der Keramikteile zu erreichen.
Anforderungen an die in CIP verwendeten Pulver
Einer der Nachteile des kaltisostatischen Pressens besteht darin, dass für vollautomatische Trockensackpressen normalerweise relativ teures sprühgetrocknetes Pulver benötigt wird. Dies kann die Gesamtkosten des Prozesses erhöhen, da spezielle Pulver verwendet werden müssen.
Außerdem sind die Produktionsraten beim CIP-Verfahren im Vergleich zum Strangpressen oder Matrizenpressen geringer. Das bedeutet, dass das Verfahren im Hinblick auf die Volumenproduktion möglicherweise nicht so effizient ist.
Zusammenfassend lässt sich sagen, dass das kaltisostatische Pressen zwar Vorteile bietet, wie z. B. die Möglichkeit, große oder komplexe Presslinge herzustellen und eine Vielzahl von Pulvern zu verwenden, aber auch einige Nachteile hat. Dazu gehören Herausforderungen bei der Maßkontrolle und der Formkomplexität sowie der Bedarf an speziellen Pulvern und geringere Produktionsraten im Vergleich zu anderen Umformverfahren.
Anwendungen des kaltisostatischen Pressens
Häufige Anwendung von CIP in der Massenproduktion von Hochleistungskeramik
Kaltisostatisches Pressen (CIP) ist eine pulverbasierte, endkonturnahe Technologie, die häufig für die Verarbeitung von Keramik verwendet wird. Es hat den Vorteil, dass Teile hergestellt werden können, bei denen die hohen Anschaffungskosten für Pressformen nicht gerechtfertigt sind oder wenn sehr große oder komplexe Presslinge benötigt werden.

Eine Vielzahl von Pulvern kann im kommerziellen Maßstab isostatisch gepresst werden, darunter Metalle, Keramiken, Kunststoffe und Verbundwerkstoffe. Die für die Verdichtung erforderlichen Drücke reichen von weniger als 5.000 psi bis zu mehr als 100.000 psi. Die Pulver werden in elastomeren Formen entweder in einem Nass- oder Trockensackverfahren verdichtet.
CIP wird in großem Umfang für die Verdichtung von keramischen Pulvern, Graphit, feuerfesten Materialien, elektrischen Isolatoren und für die Verdichtung von Hochleistungskeramik eingesetzt. Materialien wie Siliziumnitrid, Siliziumkarbid, Bornitrid, Borcarbid, Titanborid und Spinell können mit CIP verarbeitet werden.
Die Technologie dehnt sich auf neue Anwendungen aus, wie z. B. die Komprimierung von Sputtertargets, die Beschichtung von Ventilkomponenten zur Verringerung des Zylinderverschleißes in Motoren und verschiedene Anwendungen in der Telekommunikation, Elektronik, Luft- und Raumfahrt sowie in der Automobilindustrie.
Beispiele für durch CIP hergestellte Komponenten
CIP wird häufig für die Konsolidierung keramischer Pulver, die Verdichtung von Graphit, feuerfesten Materialien und elektrischen Isolatoren sowie für andere Feinkeramiken für zahnmedizinische und medizinische Anwendungen eingesetzt. Es wird auch zum Pressen von Sputtertargets, zur Beschichtung von Ventilteilen in Motoren zur Minimierung des Verschleißes der Zylinderköpfe und für verschiedene Anwendungen in der Telekommunikations-, Elektronik-, Luft- und Raumfahrt- sowie in der Automobilindustrie verwendet.
CIP-Anlagen werden zur Senkung der Produktionskosten eingesetzt und sind für die Herstellung von Fertigwaren aus Rohstoffen unerlässlich. Bei diesem Verfahren werden Pulver in einer Elastomerform eingeschlossen, die Form wird in eine Druckkammer gestellt, ein flüssiges Medium hineingepumpt und die Form wird von allen Seiten gleichmäßig mit hohem Druck beaufschlagt. Das CIP-Verfahren kann für pulverförmige Metallurgie, Hartmetalle, feuerfeste Materialien, Graphit, Keramik, Kunststoffe und andere Materialien eingesetzt werden.
Bei der Auswahl von Dienstleistungen im Bereich des kaltisostatischen Pressens ist es wichtig, die Materialeigenschaften zu berücksichtigen. Aluminium- und Magnesiumlegierungen, Hartmetalle und Schneidwerkzeuge, Kohlenstoff und Graphit, Keramik, Verbundwerkstoffe und andere Werkstoffe können mit CIP hergestellt werden. Einige Dienstleister für kaltisostatisches Pressen sind auf Beschichtungen und thermische Spritzschichten, Kupferlegierungen, Diamanten und diamantähnliche Werkstoffe, elektronische oder elektrische Werkstoffe, Sprengstoffe oder Pyrotechnik sowie spezielle und geschützte Werkstoffe spezialisiert.
Das kaltisostatische Pressen wird bei Raumtemperatur durchgeführt und verwendet eine Form aus einem Elastomer wie Urethan, Gummi oder Polyvinylchlorid. Die beim isostatischen Kaltpressen verwendete Flüssigkeit ist in der Regel Öl oder Wasser, und der Flüssigkeitsdruck während des Vorgangs liegt normalerweise zwischen 60.000 lbs/in2 und 150.000 lbs/in2. Ein Nachteil dieses Herstellungsverfahrens ist die geringe geometrische Genauigkeit aufgrund der flexiblen Form.
Zusammenfassend lässt sich sagen, dass das kaltisostatische Pressen (CIP) eine wertvolle Technik für die Massenproduktion von Hochleistungskeramik und anderen Materialien ist. Es bietet Vorteile wie Festkörperverarbeitung, einheitliches Gefüge, komplexe Formen, niedrige Werkzeugkosten und Skalierbarkeit des Prozesses. Das CIP-Verfahren ist in verschiedenen Industriezweigen weit verbreitet und dehnt sich immer weiter auf neue Anwendungen aus.
Alternative Komprimierungstechnologien
Überblick über andere Verdichtungstechnologien
Auf dem Gebiet der Materialverarbeitung gibt es mehrere leistungsstarke Verdichtungstechniken. Zwei dieser Verfahren, das kaltisostatische Pressen (CIP) und das heißisostatische Pressen (HIP), sind in verschiedenen Branchen weit verbreitet. Beide Verfahren zielen darauf ab, die Materialeigenschaften zu verbessern, unterscheiden sich jedoch in ihren Betriebsbedingungen und bieten einzigartige Vorteile.
Einführung der Stoßwellenverdichtung als Alternative
Während CIP und HIP effektive Verdichtungstechniken sind, wurden alternative Technologien entwickelt, um spezifische Herausforderungen zu bewältigen. Eine solche Alternative ist die Stoßwellenverdichtung, auch bekannt als Schockverdichtung.
Bei der Schockwellenverdichtung wird eine kurze Hochdruck-Stoßwelle erzeugt, die die Partikel stark verformen oder sogar lokal schmelzen kann. Dieser Prozess kann dazu führen, dass das Material völlig dicht und kompakt wird, ohne dass es zu einem nennenswerten Kornwachstum kommt. Schockwellen zeichnen sich durch sehr hohe Drücke, mittlere Temperaturen, sehr kurze Reaktionszeiten und sehr hohe Dehnungsgeschwindigkeiten aus.
Verschiedene Methoden wie Luftkanonen und explosive Stoßwellen, die bisher für die Verdichtung von Pulvern im Mikrometerbereich verwendet wurden, werden nun auch für die Verdichtung von Nanopulvern eingesetzt. Diese alternativen Verdichtungstechnologien mit sehr kurzen Heizzeiten haben sich als erfolgreich erwiesen, um völlig dichte und kompakte Materialien ohne Vergröberung der Nanokörner zu erhalten.
Ein Beispiel für die Stoßwellenverdichtung ist die Verwendung eines ebenen Stoßwellenverdichtungsgeräts, das mit einer Luftkanone ausgestattet ist. Dieses Gerät erzeugt eine kurze Hochdruck-Stoßwelle, mit der Partikel verformt und die volle Dichte und Verdichtung erreicht werden kann. Diese alternativen Verdichtungstechnologien bieten eine effiziente Möglichkeit zur Verarbeitung von Materialien mit minimalem Kornwachstum und verbesserten Materialeigenschaften.
In der Gummiindustrie werden fortschrittliche Kompressionspressen für die effiziente Vulkanisierung von Gummi eingesetzt. Durch die Anwendung kontrollierter Druckkräfte auf Gummimaterialien testen diese Maschinen die physikalischen Eigenschaften von Gummiprodukten wie Festigkeit, Elastizität und Haltbarkeit und stellen sicher, dass sie den ASTM-Normen entsprechen und von hoher Qualität sind.
Insgesamt bieten alternative Verdichtungstechnologien wie die Stoßwellenverdichtung innovative Lösungen, um völlig dichte und kompakte Materialien mit verbesserten Eigenschaften zu erhalten. Diese Technologien bieten einzigartige Vorteile und können in verschiedenen Industriezweigen zur Verbesserung der Materialverarbeitungsmöglichkeiten eingesetzt werden.
Schlussfolgerung
Zusammengefasst,Das kaltisostatische Pressen (CIP) ist ein äußerst vielseitiges und effizientes Verfahren zur Herstellung komplex geformter Bauteile, insbesondere bei der Produktion von Hochleistungskeramik. Im Gegensatz zum herkömmlichen einachsigen Gesenkpressen ermöglicht das CIP die Herstellung komplizierterer Formen und verringert aufgrund der gleichmäßigen Partikelpackung das Risiko von Verformungen und Rissen. Obwohl die Kontrolle der Abmessungen und die Anforderungen an das Pulver eine Herausforderung darstellen, bietet das CIP-Verfahren erhebliche Vorteile für kleine Produktionsserien und wird in der Massenproduktion von Hochleistungskeramik häufig eingesetzt. Als Alternative zu CIP ist die Stoßwellenverdichtung für bestimmte Verdichtungsanwendungen ebenfalls eine Überlegung wert.
Kontaktieren Sie uns für eine kostenlose Beratung
Die Produkte und Dienstleistungen von KINTEK LAB SOLUTION werden von Kunden auf der ganzen Welt anerkannt. Unsere Mitarbeiter helfen Ihnen gerne bei allen Fragen weiter. Kontaktieren Sie uns für eine kostenlose Beratung und sprechen Sie mit einem Produktspezialisten, um die am besten geeignete Lösung für Ihre Anwendungsanforderungen zu finden!