Die PVD-Beschichtung (Physical Vapor Deposition) ist ein hochentwickeltes Verfahren, mit dem dünne, haltbare und stark haftende Schichten auf verschiedene Substrate aufgebracht werden können.Bei diesem Verfahren wird eine Hochvakuumumgebung geschaffen, ein Zielmaterial verdampft und auf ein Substrat aufgebracht, um eine Schutz- oder Funktionsschicht zu bilden.PVD-Beschichtungen werden aufgrund ihrer außergewöhnlichen Härte, Verschleißfestigkeit und ihres Korrosionsschutzes häufig in Branchen wie der Luft- und Raumfahrt, der Automobilindustrie und der Elektronik eingesetzt.Der Prozess umfasst in der Regel Schritte wie Verdampfung, Transport, Reaktion und Abscheidung, wobei Techniken wie Sputtern und thermische Verdampfung häufig eingesetzt werden.
Die wichtigsten Punkte werden erklärt:
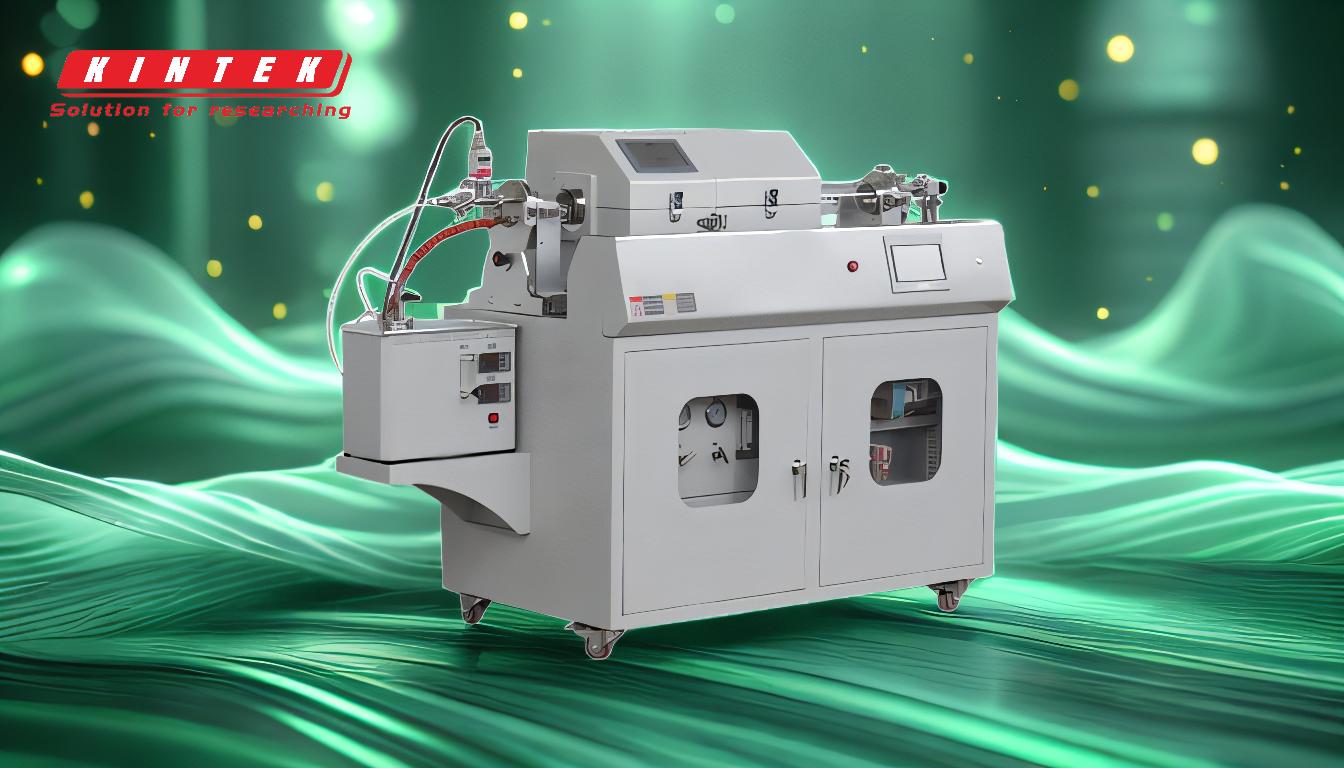
-
Vorbereitung der Vakuumkammer:
- Das PVD-Verfahren beginnt damit, dass das Zielmaterial (das zu beschichtende Material) und das Substrat (das Material, auf das beschichtet werden soll) in eine Vakuumkammer gebracht werden.
- Die Kammer wird dann evakuiert, um eine Hochvakuumumgebung zu schaffen, in der Regel mit einem Druck von 10^-2 bis 10^-6 Torr, was den Bedingungen im Weltraum nahe kommt.
- Diese Vakuumumgebung ist entscheidend, um Verunreinigungen zu vermeiden und die Reinheit der Beschichtung zu gewährleisten.
-
Verdampfung des Zielmaterials:
- Das Zielmaterial wird mit Hilfe von Hochenergiequellen wie Elektronenstrahlen, Ionen oder Photonen verdampft.Dieser Schritt wird als Verdampfung bezeichnet.
- Bei Techniken wie dem Sputtern wird das Zielmaterial mit hochenergetischen Ionen (häufig Argon-Ionen) beschossen, um Atome von der Zieloberfläche zu lösen, wodurch ein Plasma aus Atomen oder Molekülen entsteht.
- Bei der thermischen Verdampfung wird das Zielmaterial auf eine hohe Temperatur erhitzt, bis es verdampft.
-
Transport von verdampftem Material:
- Die verdampften Atome oder Moleküle werden dann durch die Vakuumkammer zum Substrat transportiert.
- Dieser Transport erfolgt in einer chemisch inerten Atmosphäre, die häufig mit Inertgasen wie Argon erzeugt wird, um unerwünschte chemische Reaktionen während des Prozesses zu verhindern.
-
Reaktion (fakultativ):
- Je nach den gewünschten Eigenschaften der Beschichtung kann das verdampfte Material mit ausgewählten Gasen (wie Stickstoff, Sauerstoff oder Methan) reagieren und Verbindungen wie Metalloxide, Nitride oder Karbide bilden.
- Dieser Reaktionsschritt bestimmt die Schlüsseleigenschaften der Beschichtung, wie Härte, Farbe und chemische Beständigkeit.
-
Abscheidung auf dem Substrat:
- Das verdampfte Material kondensiert auf dem Substrat und bildet einen dünnen, gleichmäßigen Film, der fest mit der Oberfläche verbunden ist.
- Der Abscheidungsprozess wird sorgfältig kontrolliert, um die gewünschte Dicke und Gleichmäßigkeit der Beschichtung zu gewährleisten, die in der Regel im Bereich von wenigen Mikrometern liegt.
- Das Ergebnis ist eine stark haftende Beschichtung, die das darunter liegende Material durchdringt und Probleme wie Abblättern oder Absplittern verhindert.
-
Spülung und Kühlung:
- Nach Abschluss der Beschichtung wird die Kammer mit Inertgas gespült, um eventuelle Dampfreste zu entfernen.
- Das beschichtete Substrat wird dann abgekühlt, bevor es aus der Kammer entfernt wird.
-
Bei der PVD-Beschichtung verwendete Techniken:
- Sputtern:Ein weit verbreitetes PVD-Verfahren, bei dem hochenergetische Ionen das Zielmaterial beschießen, wodurch Atome herausgeschleudert werden und sich auf dem Substrat ablagern.
- Thermische Verdampfung:Das Zielmaterial wird erhitzt, bis es verdampft, und der Dampf kondensiert dann auf dem Substrat.
- Lichtbogen-Aufdampfung:Verdampfen des Zielmaterials mit Hilfe eines Lichtbogens, häufig verwendet für harte Beschichtungen wie Titannitrid.
-
Anwendungen und Vorteile von PVD-Beschichtungen:
- PVD-Beschichtungen werden in einer Vielzahl von Anwendungen eingesetzt, darunter Schneidwerkzeuge, medizinische Geräte und dekorative Oberflächen.
- Die Beschichtungen bieten eine hervorragende Verschleißfestigkeit, Korrosionsschutz und ästhetische Attraktivität.
- Das Verfahren ist umweltfreundlich, da es ohne schädliche Chemikalien auskommt und keine nennenswerten Abfälle erzeugt.
Durch die Befolgung dieser Schritte entsteht bei der PVD-Beschichtung eine dauerhafte, hochleistungsfähige Schicht, die die Eigenschaften des Substrats verbessert und damit für anspruchsvolle Anwendungen in verschiedenen Branchen geeignet ist.
Zusammenfassende Tabelle:
Schritt | Beschreibung |
---|---|
1.Vorbereitung | Zielmaterial und Substrat werden in eine Hochvakuumkammer gebracht. |
2.Verdampfung | Das Zielmaterial wird mit Hochenergiequellen wie Elektronenstrahlen verdampft. |
3.Transport | Die verdampften Atome werden durch eine Inertgasatmosphäre transportiert. |
4.Reaktion (fakultativ) | Verdampftes Material reagiert mit Gasen und bildet Verbindungen wie Nitride oder Oxide. |
5.Abscheidung | Der Dampf kondensiert auf dem Substrat und bildet eine dünne, gleichmäßige Schicht. |
6.Spülung und Kühlung | Die Kammer wird gespült, und das beschichtete Substrat wird gekühlt. |
7.Techniken | Sputtern, thermisches Verdampfen und Lichtbogenaufdampfung werden häufig verwendet. |
8.Anwendungen | Verwendet für Schneidwerkzeuge, medizinische Geräte und dekorative Beschichtungen. |
Möchten Sie Ihre Materialien mit PVD-Beschichtungen veredeln? Kontaktieren Sie noch heute unsere Experten um mehr zu erfahren!