Thermisches Verdampfen und Magnetronsputtern sind beides weit verbreitete Verfahren zur Dünnschichtabscheidung, die jeweils unterschiedliche Vorteile und Einschränkungen aufweisen.Die thermische Verdampfung wird wegen ihrer hohen Abscheidungsraten, ihrer Einfachheit und ihrer Kosteneffizienz bevorzugt und ist daher ideal für Anwendungen, bei denen Geschwindigkeit und Materialausnutzung im Vordergrund stehen, z. B. in der Optik, Elektronik und bei Solarzellen.Es ist besonders für Materialien mit niedrigem Schmelzpunkt geeignet und bietet eine hervorragende Gleichmäßigkeit.Andererseits zeichnet sich das Magnetronsputtern durch die Herstellung hochwertiger Schichten mit hervorragender Dichte, Haftung und Oberflächenmorphologie aus und ist daher die bevorzugte Wahl für Anwendungen, die eine präzise Stöchiometrie, geringe Oberflächenrauheit und verbesserte Schichteigenschaften erfordern.Die Wahl zwischen den beiden Verfahren hängt von den spezifischen Anforderungen der Anwendung ab, z. B. von der Schichtqualität, der Abscheidungsrate und der Materialverträglichkeit.
Die wichtigsten Punkte werden erklärt:
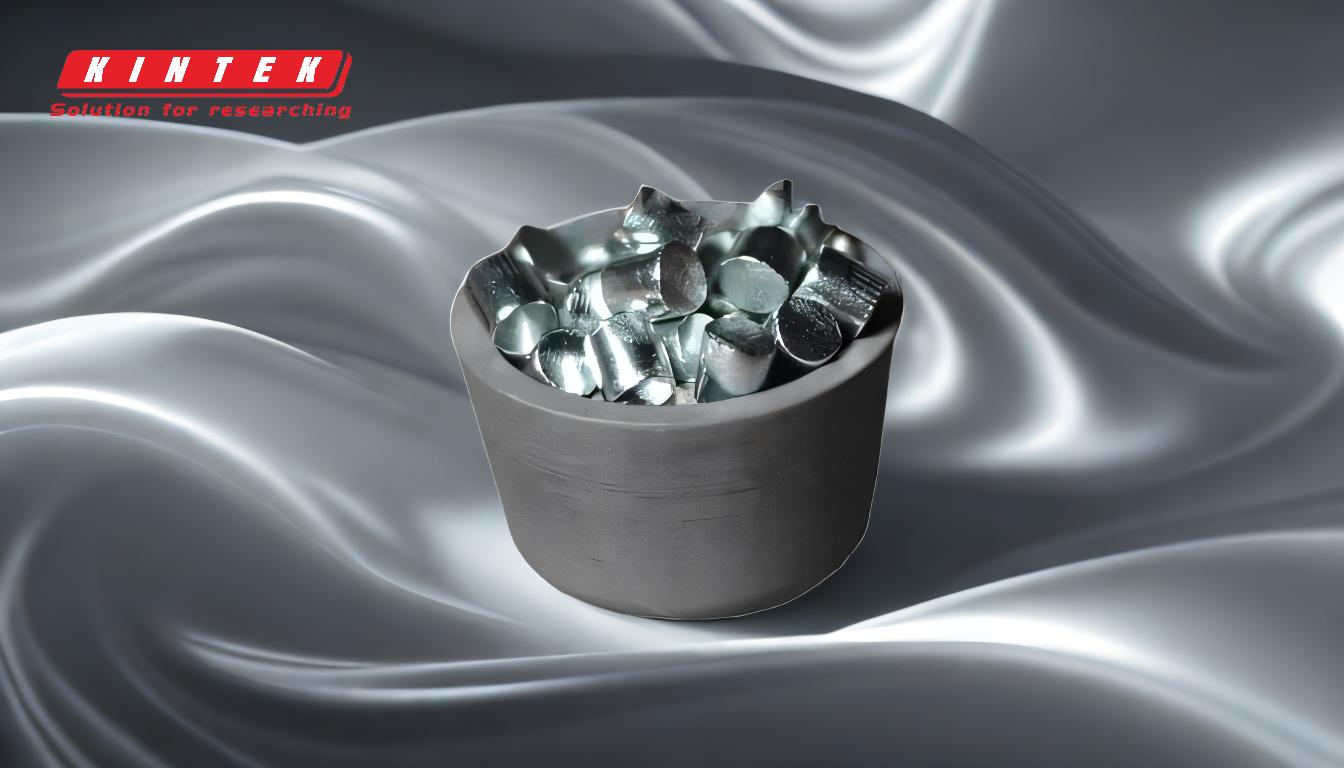
-
Ablagerungsrate und Wirkungsgrad:
- Thermische Verdampfung:Bietet im Vergleich zum Magnetron-Sputtern deutlich höhere Abscheideraten und ist damit schneller und effizienter für Anwendungen, bei denen es auf Geschwindigkeit ankommt.Dies ist besonders vorteilhaft in Branchen wie der Optik- und Elektronikindustrie, wo oft eine schnelle Produktion erforderlich ist.
- Magnetronzerstäubung:Es ist zwar langsamer, bietet aber eine bessere Kontrolle über die Folieneigenschaften, was für Anwendungen, die hohe Präzision und Qualität erfordern, unerlässlich ist.
-
Folienqualität und -eigenschaften:
- Thermische Verdampfung:Im Vergleich zu gesputterten Schichten sind die erzeugten Schichten weniger dicht und haben eine größere Korngröße.Dies kann zu einer geringeren Haftung und Oberflächenrauhigkeit führen, was für Anwendungen, die eine hohe Schichtqualität erfordern, ungeeignet sein kann.
- Magnetron-Sputtern:Erzeugt dichtere Filme mit kleinerer Korngröße, besserer Haftung und Eigenschaften, die denen von Schüttgut ähneln.Dies macht es ideal für Anwendungen, bei denen Filmqualität, Dichte und Oberflächenmorphologie entscheidend sind.
-
Material-Kompatibilität:
- Thermische Verdampfung:Es ist sowohl mit Metallen als auch mit Nichtmetallen kompatibel und eignet sich besonders für Materialien mit niedrigem Schmelzpunkt.Es können auch Legierungen hergestellt und sequenzielle Beschichtungen durchgeführt werden, was Flexibilität bei der Materialauswahl bietet.
- Magnetron-Sputtern:Wird in erster Linie bei Metallen verwendet, bietet aber eine größere Vielseitigkeit in Bezug auf Farboptionen und Modulation, was für Anwendungen, die besondere ästhetische oder funktionale Eigenschaften erfordern, von Vorteil ist.
-
Kosten und Komplexität:
- Thermische Verdampfung:Relativ einfach und kostengünstig, mit geringem Stromverbrauch.Es handelt sich um ein schonendes Verfahren, bei dem verdampfte Partikel mit geringer Energie erzeugt werden, was es für empfindliche Anwendungen geeignet macht.
- Magnetron-Sputtern:Komplexer und in der Regel teurer, da spezielle Geräte und ein höherer Stromverbrauch erforderlich sind.Die Investition ist jedoch gerechtfertigt, wenn es um Anwendungen geht, die hochwertige Folien mit präzisen Eigenschaften erfordern.
-
Gleichmäßigkeit und Richtungsabhängigkeit:
- Thermische Verdampfung:Hervorragende Gleichmäßigkeit bei der Verwendung von planetarischen Substratbefestigungen und Gleichmäßigkeitsmasken.Außerdem bietet es eine gute Richtwirkung, was bei der Beschichtung komplexer Geometrien von Vorteil ist.
- Magnetron-Sputtering:Es kann zwar eine hohe Gleichmäßigkeit erreichen, erfordert aber unter Umständen eine ausgefeiltere Einrichtung und Steuerung, um den gleichen Grad an Richtungsabhängigkeit zu erreichen wie die thermische Verdampfung.
-
Anwendungen und Industrieeinsatz:
- Thermische Verdampfung:Weit verbreitet in Branchen, in denen hohe Abscheideraten und Materialeffizienz im Vordergrund stehen, wie z. B. bei der Herstellung von optischen Beschichtungen, elektronischen Komponenten und Solarzellen.
- Magnetron-Sputtering:Bevorzugt in Industrien, die hochwertige Folien mit präzisen Eigenschaften benötigen, wie z. B. bei der Herstellung von Halbleitergeräten, Schutzbeschichtungen und dekorativen Oberflächen.
Zusammenfassend lässt sich sagen, dass die Wahl zwischen thermischer Verdampfung und Magnetronsputtern von den spezifischen Anforderungen der jeweiligen Anwendung abhängt.Die thermische Verdampfung eignet sich besser für eine schnelle und kostengünstige Produktion, während das Magnetronsputtern die Methode der Wahl ist, wenn es um eine hochwertige und präzise Schichtabscheidung geht.Beide Techniken haben ihre eigenen Vorteile und Grenzen, und die Entscheidung sollte auf Faktoren wie Schichtqualität, Abscheidungsrate, Materialkompatibilität und Kostenerwägungen beruhen.
Zusammenfassende Tabelle:
Aspekt | Thermische Verdampfung | Magnetronzerstäubung |
---|---|---|
Abscheiderate | Hoch | Mäßig |
Filmqualität | Weniger dicht, größere Korngrößen | Dichtere, kleinere Körnungen |
Material-Kompatibilität | Metalle, Nichtmetalle, niedrige Schmelzpunkte | Hauptsächlich Metalle, vielseitige Farboptionen |
Kosten | Geringe Kosten, einfache Einrichtung | Höhere Kosten, komplexer Aufbau |
Einheitlichkeit | Hervorragend mit planetarischer Aufhängung | Hoch, erfordert aber eine anspruchsvolle Kontrolle |
Anwendungen | Optik, Elektronik, Solarzellen | Halbleiter, Schutzschichten |
Sind Sie noch unsicher, welche Dünnschichttechnik für Ihr Projekt die richtige ist? Kontaktieren Sie noch heute unsere Experten für eine persönliche Beratung!