Wirbelschichtreaktoren (FBR) werden aufgrund ihrer Vorteile, wie gleichmäßige Partikelmischung, Temperaturgradienten und kontinuierlicher Betrieb, in verschiedenen Industriezweigen eingesetzt.Sie sind jedoch auch mit einigen bemerkenswerten Nachteilen verbunden.Dazu gehören die Vergrößerung des Reaktorbehälters, ein höherer Pumpbedarf und Druckabfall, Partikeleintrag, Erosion der internen Komponenten und Druckverlustszenarien.Darüber hinaus stehen Wirbelschichtpyrolyseure, eine spezielle Art von FBR, vor Herausforderungen wie dem Bedarf an kleinen Partikelgrößen, großen Mengen an Inertgasen und hohen Betriebskosten.Das Verständnis dieser Nachteile ist entscheidend, um fundierte Entscheidungen zu treffen, wenn FBRs für bestimmte Anwendungen in Betracht gezogen werden.
Die wichtigsten Punkte werden erklärt:
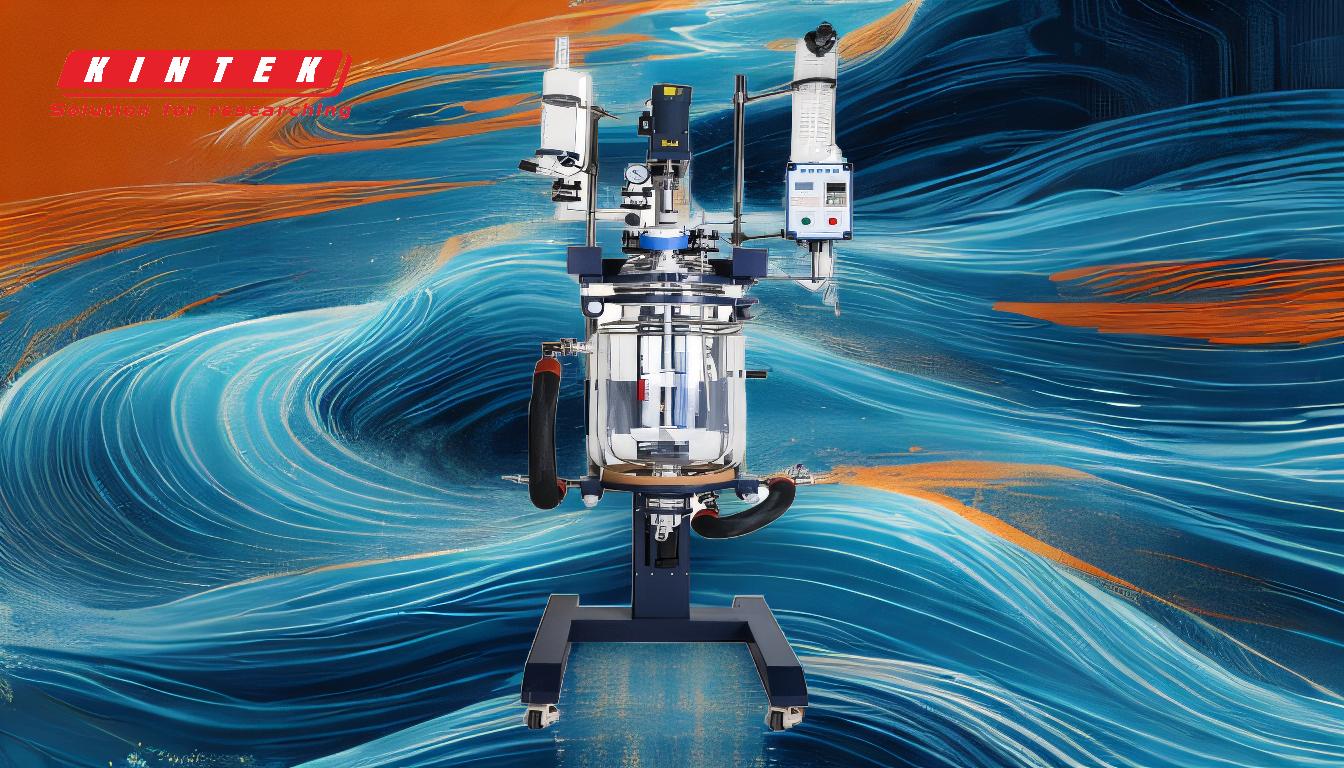
-
Vergrößerung des Reaktorbehälters:
- Wirbelschichtreaktoren erfordern im Vergleich zu anderen Reaktortypen häufig größere Behälter.Dies ist darauf zurückzuführen, dass die Wirbelschichtpartikel untergebracht und die richtigen Misch- und Reaktionsbedingungen gewährleistet werden müssen.Die größere Größe kann zu höheren Investitionskosten und größerem Platzbedarf führen, was nicht für alle Anwendungen praktikabel sein dürfte.
-
Höhere Pumpenanforderungen und Druckabfall:
- FBRs erfordern in der Regel eine höhere Pumpleistung, um den fluidisierten Zustand der Partikel aufrechtzuerhalten.Dies führt zu einem höheren Energieverbrauch und höheren Betriebskosten.Außerdem kann der Druckabfall über dem Bett beträchtlich sein, so dass robuste und teure Pumpensysteme erforderlich sind, um die gewünschten Durchflussraten aufrechtzuerhalten.
-
Partikeleintrag:
- Eine der Herausforderungen bei FBRs ist das Mitreißen von Feinpartikeln im Gasstrom.Dies kann zum Verlust wertvoller Reaktanten oder Produkte führen und erfordert unter Umständen zusätzliche Ausrüstung wie Zyklone oder Filter, um die mitgerissenen Partikel abzufangen und zu recyceln.Dies erhöht die Komplexität und die Kosten des Systems.
-
Erosion der internen Komponenten:
- Die ständige Bewegung von Partikeln in einem Wirbelbett kann zur Erosion von internen Komponenten wie Reaktorwänden, Verteilerplatten und Wärmetauschern führen.Diese Erosion kann zu häufigen Wartungsarbeiten und zum Austausch von Teilen führen, wodurch sich die Gesamtbetriebskosten und die Ausfallzeiten erhöhen.
-
Druckverlust-Szenarien:
- FBRs sind anfällig für Druckverlustszenarien, die den Fluidisierungsprozess stören und die Gesamtleistung des Reaktors beeinträchtigen können.Die Beherrschung und Abschwächung dieser Druckverluste erfordert eine sorgfältige Konstruktion und Überwachung, was die Komplexität und die Kosten des Systems erhöht.
-
Anforderung an kleine Partikelgrößen:
- Wirbelschicht-Pyrolyseure, eine spezielle Art von FBR, erfordern kleine Partikelgrößen, um eine optimale Leistung zu erzielen.Dies erfordert zusätzliche Verarbeitungsschritte zur Reduzierung der Partikelgröße, was die Gesamtkosten und die Komplexität des Systems erhöhen kann.
-
Große Menge an Inertgasen:
- Der Betrieb von Wirbelschicht-Pyrolyseuren erfordert oft eine große Menge an Inertgasen, um die gewünschten Reaktionsbedingungen aufrechtzuerhalten.Dies kann zu höheren Betriebskosten und dem Bedarf an zusätzlicher Infrastruktur für die Gasförderung und -lagerung führen.
-
Hohe Betriebskosten:
- Die Kombination aus höherem Pumpenbedarf, Partikeleintrag, Erosion interner Komponenten und dem Bedarf an kleinen Partikelgrößen und Inertgasen trägt zu den hohen Betriebskosten von FBRs bei.Diese Kosten können ein erheblicher Nachteil sein, insbesondere bei Anwendungen, bei denen Kosteneffizienz ein entscheidender Faktor ist.
Zusammenfassend lässt sich sagen, dass Wirbelschichtreaktoren zwar eine Reihe von Vorteilen bieten, wie z. B. eine gleichmäßige Durchmischung und Temperaturgradienten, dass sie aber auch mit erheblichen Nachteilen verbunden sind, die sorgfältig abgewogen werden müssen.Dazu gehören die Vergrößerung des Reaktors, ein höherer Pumpenbedarf, Partikelmitriss, Erosion der internen Komponenten, Druckverlustszenarien und hohe Betriebskosten.Die Kenntnis dieser Nachteile ist für fundierte Entscheidungen bei der Auswahl und Auslegung von FBRs für bestimmte Anwendungen unerlässlich.
Zusammenfassende Tabelle:
Benachteiligung | Beschreibung |
---|---|
Vergrößerung des Reaktorbehälters | Größere Behälter erhöhen die Kapitalkosten und den Platzbedarf. |
Höhere Anforderungen an das Pumpen | Erfordert mehr Energie und robuste Systeme zur Aufrechterhaltung der Fluidisierung. |
Partikelverschleppung | Feine Partikel können entweichen und erfordern zusätzliche Ausrüstung zur Rückgewinnung. |
Erosion der internen Komponenten | Kontinuierliche Partikelbewegung führt zu Verschleiß und damit zu häufiger Wartung. |
Druckverlust-Szenarien | Druckverluste können die Fluidisierung stören und erfordern eine sorgfältige Planung und Überwachung. |
Erfordernis einer kleinen Partikelgröße | Zusätzliche Verarbeitung erforderlich, um die Partikelgröße zu reduzieren, was die Kosten erhöht. |
Große Menge an Inertgasen | Hohe Betriebskosten aufgrund des Bedarfs an Inertgasen. |
Hohe Betriebskosten | Die Kombination dieser Faktoren führt zu erheblichen Betriebskosten. |
Benötigen Sie Hilfe bei der Entscheidung, ob Wirbelschichtreaktoren das Richtige für Ihre Anwendung sind? Kontaktieren Sie unsere Experten noch heute!