Das Sintern ist ein entscheidender Prozess in der Pulvermetallurgie, bei dem Metallpulver auf Temperaturen unterhalb ihres Schmelzpunktes erhitzt werden, wodurch sich die Partikel verbinden und eine zusammenhängende Form bilden.Dieser Prozess beinhaltet mehrere physikalische und chemische Veränderungen, einschließlich der Entfernung von Wasser, organischen Stoffen und adsorbierten Gasen, sowie Spannungsabbau, Reduzierung von Oberflächenoxiden, Materialwanderung, Rekristallisation und Kornwachstum.Diese Veränderungen führen zu verbesserten Materialeigenschaften wie geringerer Porosität, höherer Festigkeit, Haltbarkeit, Leitfähigkeit und Korrosionsbeständigkeit.Das Sintern ermöglicht auch eine bessere Kontrolle über den Herstellungsprozess, was zu gleichmäßigeren Produkten führt und gleichzeitig energieeffizient und umweltfreundlich ist.
Die wichtigsten Punkte erklärt:
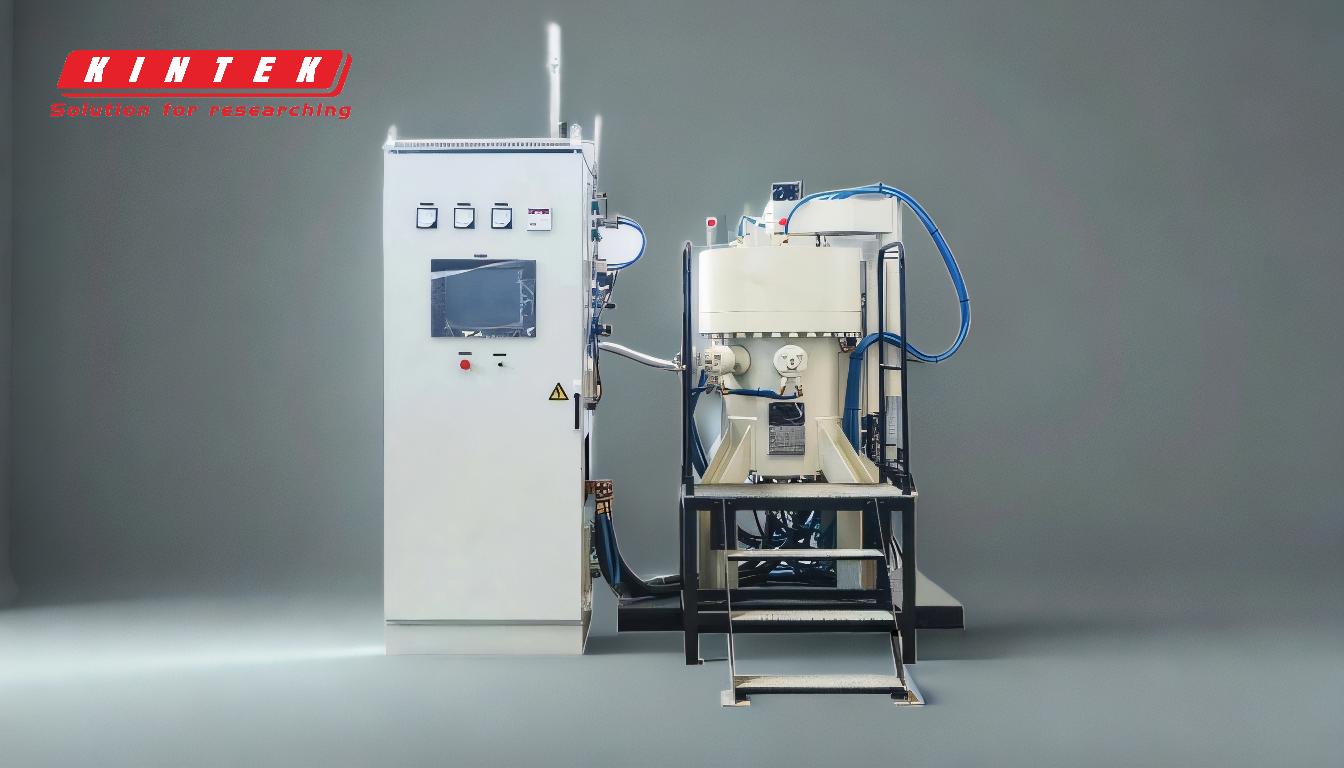
-
Bindung von Teilchen:
- Beim Sintern werden Metallpulverpartikel auf eine Temperatur unterhalb ihres Schmelzpunkts erhitzt, wodurch sie sich chemisch verbinden.Durch diese Bindung entsteht eine kohärente Form, die für die Herstellung fester Metallteile aus Pulvern unerlässlich ist.
- Der Prozess wird durch die Verringerung der Oberflächenenergie vorangetrieben, die die Partikel dazu bringt, zusammenzuwachsen und stärkere Bindungen einzugehen.
-
Physikalische und chemische Veränderungen:
- Verdunstung von Wasser und organischer Materie:Feuchtigkeit oder organische Substanzen, die im Pulver vorhanden sind, werden in den ersten Phasen des Sinterns verdampft oder verbrannt.
- Entfernung von adsorbierten Gasen:An der Oberfläche der Pulverteilchen adsorbierte Gase werden freigesetzt, wodurch ein dichteres Material entsteht.
- Stressabbau:Die inneren Spannungen in den Pulverpartikeln werden abgebaut, was zu einer stabileren und gleichmäßigeren Struktur führt.
- Reduktion von Oberflächenoxiden:Die Oberflächenoxide auf den Pulverpartikeln werden reduziert, was die Bindung zwischen den Partikeln verbessert.
- Werkstoff-Migration:Atome wandern über die Partikelgrenzen, was zu einer Verdichtung und der Bildung einer festen Struktur führt.
- Rekristallisation und Kornwachstum:Es bilden sich neue Körner und wachsen, was die Mikrostruktur und die Eigenschaften des Materials erheblich verändern kann.
-
Mikrostrukturelle Veränderungen:
- Korngröße und Kornform:Der Sinterprozess beeinflusst die Größe und Form der Körner im Material.Es können sich größere Körner bilden, die die mechanischen Eigenschaften beeinflussen können.
- Porengröße und -verteilung:Die Porosität wird verringert, da sich die Poren verkleinern oder schließen, was zu einem Material mit höherer Dichte führt.Durch diese Verringerung der Porosität werden Eigenschaften wie Festigkeit, Leitfähigkeit und Korrosionsbeständigkeit verbessert.
- Form und Verteilung der Korngrenzen:Die Form und die Verteilung der Korngrenzen werden verändert, was sich auf die mechanischen und thermischen Eigenschaften des Materials auswirken kann.
-
Verbesserung der Materialeigenschaften:
- Stärke und Langlebigkeit:Durch die Verringerung der Porosität verbessert das Sintern die Festigkeit und Haltbarkeit des Materials.Die geringere Porosität führt auch zu besseren mechanischen Eigenschaften.
- Leitfähigkeit und Korrosionsbeständigkeit:Die Verringerung der Oberflächenporosität verbessert die elektrische Leitfähigkeit und die Korrosionsbeständigkeit.
- Zugfestigkeit:Die Zugfestigkeit des Materials wird durch die Verdichtung und Bindung der Partikel verbessert.
-
Vorteile für Umwelt und Herstellung:
- Energie-Effizienz:Das Sintern benötigt weniger Energie als das Schmelzen desselben Metalls und ist damit eine umweltfreundlichere Option.
- Prozesskontrolle:Der Sinterprozess ermöglicht eine bessere Kontrolle über den Herstellungsprozess, was zu konsistenteren und zuverlässigeren Produkten führt.
-
Koaleszenz und Reversion:
- Unter bestimmten äußeren Bedingungen können Metallpulverpartikel koaleszieren, d. h. sie verschmelzen vorübergehend.Sobald diese Bedingungen jedoch beseitigt sind, kehren die Teilchen in ihr normales Verhalten zurück, so dass die Integrität des gesinterten Materials erhalten bleibt.
Zusammenfassend lässt sich sagen, dass das Sintern Metallpulver durch eine Reihe physikalischer und chemischer Veränderungen in feste, dauerhafte Materialien mit verbesserten Eigenschaften verwandelt.Dieses Verfahren ist nicht nur effizient und kontrollierbar, sondern auch umweltfreundlich, was es zu einer bevorzugten Methode in der Pulvermetallurgie macht.
Zusammenfassende Tabelle:
Hauptaspekt | Beschreibung |
---|---|
Bindung von Partikeln | Metallpulver verbinden sich unterhalb des Schmelzpunkts chemisch und bilden eine feste Struktur. |
Physikalische und chemische Veränderungen | Verdampfen von Wasser, Entfernen von Gasen, Reduzieren von Oxiden und Migrieren von Material. |
Mikrostrukturelle Veränderungen | Verringert die Porosität, verändert die Korngröße und verbessert die Korngrenzenverteilung. |
Verbesserung der Materialeigenschaften | Verbessert die Festigkeit, Haltbarkeit, Leitfähigkeit und Korrosionsbeständigkeit. |
Vorteile für die Umwelt | Energieeffizient und ermöglicht eine präzise Steuerung der Fertigungsprozesse. |
Erfahren Sie, wie das Sintern Ihren Fertigungsprozess optimieren kann. Kontaktieren Sie unsere Experten noch heute !