Unter Sintern in einem Induktionsofen versteht man den Prozess des Verdichtens und Verbindens von Pulverpartikeln zu einer festen Masse durch Wärmezufuhr, in der Regel unterhalb des Schmelzpunkts des Materials.Dieser Prozess ist entscheidend für die Herstellung der Ofenauskleidung, die während des Betriebs hohen Temperaturen und mechanischen Belastungen standhalten muss.Der Sinterprozess in einem Induktionsofen umfasst drei wichtige Phasen: Einbrennen, Halbsintern und vollständiges Sintern.Jede Phase wird sorgfältig kontrolliert, um sicherzustellen, dass die Auskleidung eine gleichmäßige, dauerhafte und leistungsstarke Mikrostruktur erhält.Induktionsöfen mit ihrer präzisen Temperaturregelung und gleichmäßigen Erwärmung eignen sich hervorragend für Sinterprozesse und gewährleisten die Integrität und Langlebigkeit der Auskleidung.
Die wichtigsten Punkte erklärt:
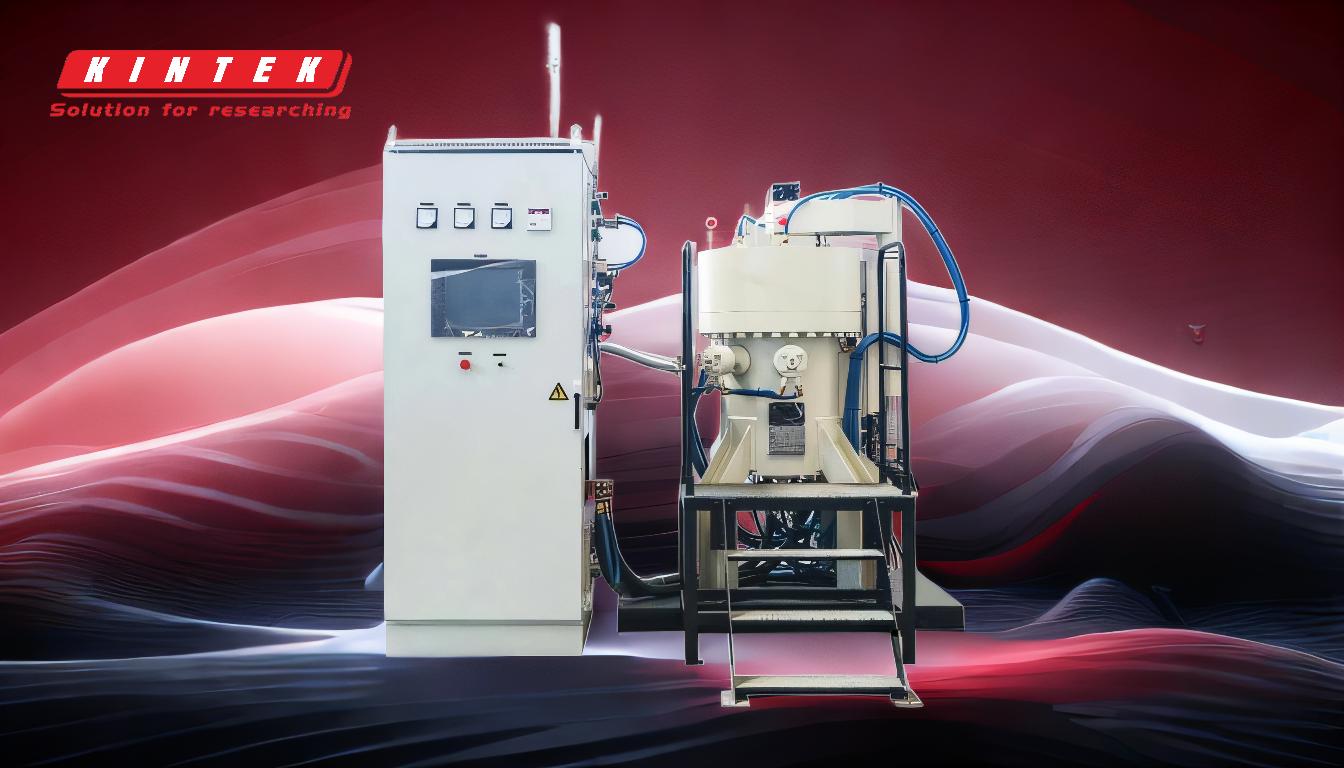
-
Definition des Sinterns in Induktionsöfen:
- Unter Sintern versteht man das Verdichten und Verbinden von Pulverpartikeln zu einer festen Masse unter Einsatz von Wärme, in der Regel unterhalb des Schmelzpunktes des Materials.
- In Induktionsöfen wird das Sintern in erster Linie zur Herstellung der feuerfesten Auskleidung verwendet, die während des Betriebs hohen Temperaturen und mechanischen Belastungen standhalten muss.
-
Etappen des Sinterprozesses:
-
Backen Bühne:
- Die Ofenauskleidung wird mit kontrollierter Geschwindigkeit auf etwa 600 °C erhitzt.
- In dieser Phase wird dem feuerfesten Material die Feuchtigkeit entzogen, was Risse verhindert und die strukturelle Integrität gewährleistet.
-
Semi-Sintering-Stufe:
- Die Temperatur wird auf 900°C erhöht und eine Zeit lang gehalten.
- Anschließend wird die Temperatur schneller auf 1200 °C erhöht und erneut gehalten.
- In dieser Phase beginnt die Bindung der Partikel und es entsteht eine halbfeste Struktur.
-
Vollständige Sinterungsphase:
- Die Endtemperatur wird auf der Grundlage der Materialeigenschaften und der gewünschten Auskleidungsmerkmale eingestellt.
- In dieser Phase wird sichergestellt, dass die Auskleidung ein vollständig gebundenes, dichtes und dauerhaftes Gefüge erhält.
-
Backen Bühne:
-
Bedeutung des Sinterns für Ofenauskleidungen:
- Eine gut gesinterte Auskleidung hat eine dreischichtige Struktur, die optimale thermische und mechanische Eigenschaften bietet.
- Eine ordnungsgemäße Sinterung erhöht die Widerstandsfähigkeit der Auskleidung gegen Temperaturschocks, Erosion und chemische Reaktionen mit geschmolzenen Metallen.
- Der Sinterprozess wirkt sich direkt auf die Lebensdauer der Auskleidung und die Gesamtleistung des Ofens aus.
-
Die Rolle von Induktionsöfen beim Sintern:
- Induktionsöfen bieten eine präzise Temperaturkontrolle und eine gleichmäßige Erwärmung, die für gleichmäßige Sinterergebnisse unerlässlich sind.
- Das elektromagnetische Feld in Induktionsöfen erzeugt Wirbelströme, die eine gleichmäßige Zusammensetzung und Temperaturverteilung im Auskleidungsmaterial gewährleisten.
- Induktionsöfen können Temperaturen von bis zu 1650°C erreichen und eignen sich zum Sintern einer breiten Palette von feuerfesten Materialien.
-
Vorteile von Induktionsöfen zum Sintern:
- Einheitliche Heizung:Sorgt für eine gleichmäßige Sinterung über die gesamte Auskleidung und verringert so das Risiko von Schwachstellen.
- Energie-Effizienz:Induktionsöfen haben einen hohen Wirkungsgrad mit über 95 % effektiver Leistung.
- Automatisierung und Steuerung:Fortschrittliche Steuersysteme ermöglichen eine präzise Regelung von Heizraten, Temperaturen und Haltezeiten.
- Langlebigkeit:Induktionsöfen sind für den 24-Stunden-Dauerbetrieb ausgelegt und damit ideal für industrielle Sinterprozesse.
-
Wichtige Prozessparameter:
- Temperaturkontrolle:Die genaue Regelung der Heizraten und Haltezeiten ist entscheidend für das Erreichen der gewünschten Auskleidungseigenschaften.
- Material-Zusammensetzung:Die chemische Zusammensetzung des feuerfesten Materials, insbesondere Elemente mit hoher Sauerstoffaffinität, muss sorgfältig kontrolliert werden.
- Physikalische Eigenschaften:Faktoren wie Schmelzpunkt, Benetzbarkeit und Oberflächenspannung beeinflussen den Sinterprozess.
- Reinheit und Fließfähigkeit:Die Sicherstellung der Reinheit und Fließfähigkeit des geschmolzenen Materials während des Sinterns verbessert die Leistung der Auskleidung.
-
Praktische Überlegungen zum Sintern in Induktionsöfen:
- Ofen Design:Der Ofen muss mit einem hochwertigen Induktor, einer Stromversorgung und einem Kontrollsystem ausgestattet sein, um den Sinterprozess zu unterstützen.
- Auskleidungsmaterialien:Die Wahl der feuerfesten Materialien und ihre Verträglichkeit mit dem Sinterprozess sind entscheidend.
- Wartung:Regelmäßige Inspektion und Wartung der Ofenauskleidung sind notwendig, um eine langfristige Leistung zu gewährleisten.
Wenn die Käufer von Anlagen und Verbrauchsmaterialien diese wichtigen Punkte verstehen, können sie fundierte Entscheidungen über den Sinterprozess in Induktionsöfen treffen und so eine optimale Leistung und Langlebigkeit der Ofenauskleidung gewährleisten.
Zusammenfassende Tabelle:
Aspekt | Einzelheiten |
---|---|
Definition | Verdichten und Verbinden von Pulverpartikeln durch Wärmezufuhr unterhalb des Schmelzpunktes. |
Wichtige Stufen | Backen (600°C), Halbsintern (900°C-1200°C), Vollsintern. |
Bedeutung | Verbessert die Haltbarkeit der Auskleidung, die Temperaturwechselbeständigkeit und die Lebensdauer des Ofens. |
Vorteile | Gleichmäßige Erwärmung, Energieeffizienz, präzise Steuerung und Langlebigkeit. |
Wichtige Parameter | Temperaturkontrolle, Materialzusammensetzung, physikalische Eigenschaften, Reinheit. |
Praktische Überlegungen | Konstruktion des Ofens, Auskleidungsmaterialien und regelmäßige Wartung. |
Sind Sie bereit, Ihren Sinterprozess zu optimieren? Kontaktieren Sie noch heute unsere Experten für maßgeschneiderte Lösungen!