Selektives Lasersintern (SLS) und Elektronenstrahlschmelzen (EBM) sind beides Technologien der additiven Fertigung (3D-Druck), unterscheiden sich jedoch erheblich in ihren Verfahren, Materialien und Anwendungen.SLS verwendet einen Hochleistungslaser, um pulverförmiges Material, in der Regel Polymere oder Metalle, Schicht für Schicht zu sintern und so ein 3D-Objekt zu erzeugen.EBM hingegen verwendet einen Elektronenstrahl, um Metallpulver in einer Vakuumumgebung zu schmelzen, wodurch es sich für Anwendungen mit hoher Festigkeit und hohen Temperaturen eignet.Während SLS vielseitig ist und mit einer Reihe von Materialien arbeitet, ist EBM eher auf Metallteile spezialisiert, insbesondere in der Luft- und Raumfahrt und der Medizintechnik.Beide Technologien machen Formen überflüssig, aber EBM bietet höhere Präzision und bessere mechanische Eigenschaften für Metallteile.
Die wichtigsten Punkte werden erklärt:
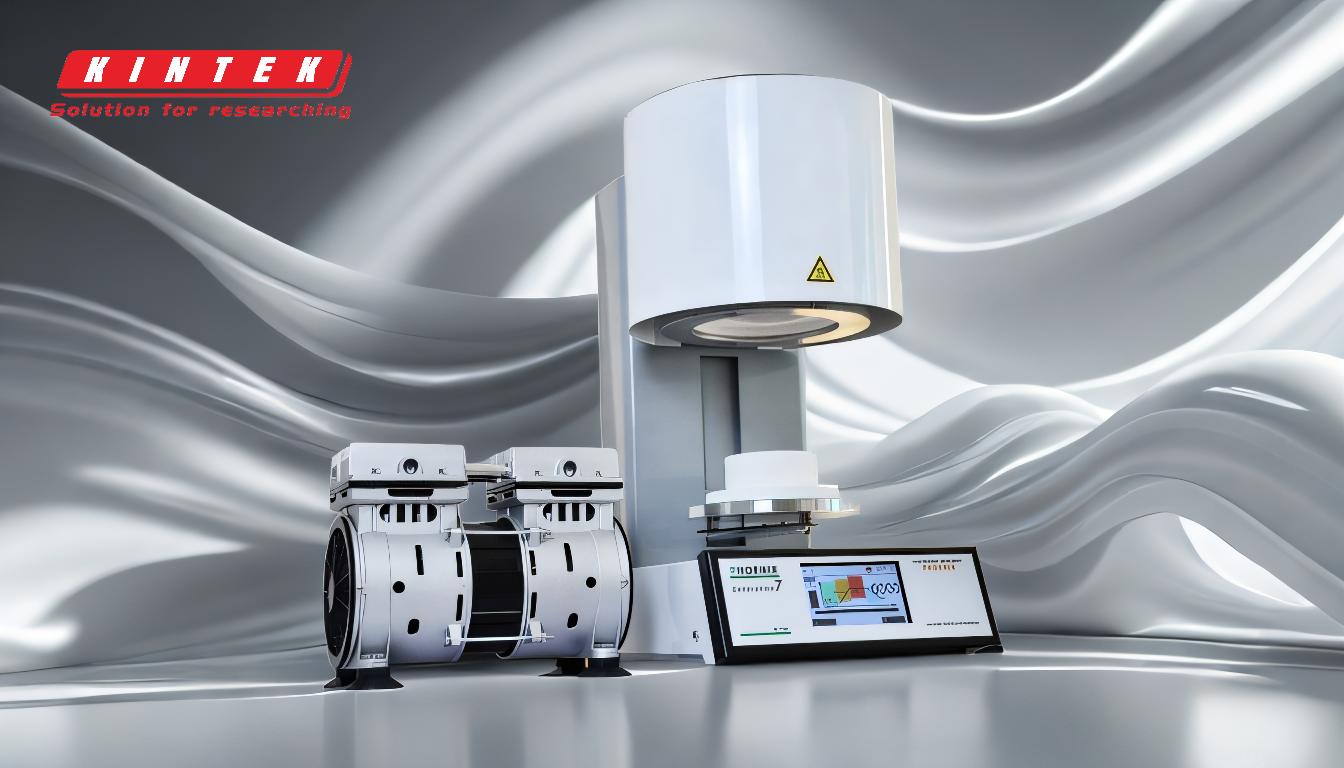
-
Mechanismus des Prozesses:
- Selektives Laser-Sintern (SLS):Verwendet einen Hochleistungslaser, um pulverförmiges Material selektiv Schicht für Schicht zu sintern (zu verschmelzen), um ein 3D-Objekt zu erstellen.Der Laser erhitzt das Pulver gerade genug, um die Partikel zu verbinden, ohne sie vollständig zu schmelzen.
- Elektronenstrahlschmelzen (EBM):Verwendet einen hochenergetischen Elektronenstrahl zum vollständigen Schmelzen von Metallpulver in einer Vakuumkammer.Der Elektronenstrahl tastet das Pulverbett ab und schmilzt das Material Schicht für Schicht auf, so dass ein dichtes, hochfestes Teil entsteht.
-
Verwendete Materialien:
- SLS:Funktioniert in erster Linie mit Polymeren (z. B. Nylon, Polyamid) und einigen Metallpulvern.Es ist vielseitig und kann eine breite Palette von Materialien verarbeiten, einschließlich Verbundwerkstoffen.
- EBM:Ausschließlich für Metallpulver, wie Titan, Kobalt-Chrom und Nickelbasislegierungen.Es ist ideal für die Herstellung hochfester, hochtemperaturbeständiger Teile.
-
Umweltbedingungen:
- SLS:Arbeitet in einer kontrollierten Atmosphäre, in der Regel Stickstoff oder Argon, um eine Oxidation des Materials zu verhindern.Ein Vakuum ist nicht erforderlich.
- EBM:Erfordert eine Hochvakuum-Umgebung, um Verunreinigungen zu vermeiden und die Funktionsfähigkeit des Elektronenstrahls zu gewährleisten.Dies macht das Verfahren komplexer und teurer.
-
Präzision und Oberflächengüte:
- SLS:Erzeugt Teile mit guter Oberflächengüte und mäßiger Präzision.Die Oberfläche muss jedoch möglicherweise nachbearbeitet werden (z. B. Schleifen oder Beschichten), um glattere Oberflächen zu erzielen.
- EBM:Bietet höhere Präzision und bessere mechanische Eigenschaften aufgrund des vollständigen Aufschmelzens des Metallpulvers.Die Teile haben eine rauere Oberfläche als beim SLS-Verfahren, sind aber stabiler und haltbarer.
-
Anwendungen:
- SLS:Geeignet für die Herstellung von Prototypen, Funktionsteilen und Kleinserien.Wird häufig in der Automobil-, Luft- und Raumfahrt- sowie in der Konsumgüterindustrie verwendet.
- EBM:Ideal für Hochleistungsanwendungen wie Komponenten für die Luft- und Raumfahrt, medizinische Implantate und Turbinenschaufeln, bei denen Festigkeit und Wärmebeständigkeit entscheidend sind.
-
Kosten und Produktionsgeschwindigkeit:
- SLS:Im Allgemeinen schneller und kostengünstiger für die Herstellung von Prototypen und Kleinserien.Es werden keine Gussformen benötigt, was die Vorlaufkosten reduziert.
- EBM:Teurer aufgrund der Vakuumumgebung und der speziellen Ausrüstung.Es ist zwar langsamer, erzeugt aber Teile mit besseren mechanischen Eigenschaften, was die höheren Kosten für kritische Anwendungen rechtfertigt.
-
Nachbearbeitungsanforderungen:
- SLS:Die Teile müssen unter Umständen nur minimal nachbearbeitet werden, z. B. durch das Entfernen von Stützen oder die Oberflächenbearbeitung.Der Prozess ist jedoch relativ einfach.
- EBM:Die Teile müssen oft wärmebehandelt oder bearbeitet werden, um die gewünschten mechanischen Eigenschaften und die gewünschte Oberflächenbeschaffenheit zu erreichen.Die Vakuumumgebung macht auch die Nachbearbeitung komplexer.
Durch das Verständnis dieser wichtigen Unterschiede können Käufer von Geräten und Verbrauchsmaterialien fundierte Entscheidungen treffen, die auf den spezifischen Anforderungen ihrer Projekte basieren, wie z. B. Materialeigenschaften, Präzision und Anwendungsanforderungen.
Zusammenfassende Tabelle:
Aspekt | Selektives Laser-Sintern (SLS) | Elektronenstrahlschmelzen (EBM) |
---|---|---|
Prozess-Mechanismus | Verwendet einen Hochleistungslaser, um pulverförmiges Material Schicht für Schicht zu sintern. | Verwendet einen Elektronenstrahl, um Metallpulver im Vakuum vollständig zu schmelzen. |
Verwendete Materialien | Polymere (z. B. Nylon, Polyamid) und einige Metallpulver. | Ausschließlich für Metallpulver (z. B. Titan, Kobalt-Chrom, Nickelbasis-Legierungen). |
Umgebungsbedingungen | Arbeitet in einer kontrollierten Atmosphäre (Stickstoff/Argon). | Erfordert eine Hochvakuumumgebung. |
Präzision und Oberflächengüte | Gute Oberflächengüte, mäßige Präzision.Kann Nachbearbeitung erfordern. | Höhere Präzision, stärkere Teile.Rauere Oberflächengüte, aber bessere mechanische Eigenschaften. |
Anwendungen | Prototyping, Funktionsteile, Kleinserienfertigung (Automobil, Luft- und Raumfahrt, Konsumgüter). | Hochleistungsanwendungen (Luft- und Raumfahrt, medizinische Implantate, Turbinenschaufeln). |
Kosten und Produktionsgeschwindigkeit | Schneller und kostengünstiger für die Herstellung von Prototypen und Kleinserien. | Teurer und langsamer, aber ideal für kritische Anwendungen. |
Nachbearbeitungen | Geringfügig (Entfernen von Trägern, Oberflächenbearbeitung). | Aufgrund der Vakuumumgebung ist oft eine Wärmebehandlung oder Bearbeitung erforderlich. |
Benötigen Sie Hilfe bei der Auswahl der richtigen 3D-Drucktechnologie für Ihr Projekt? Kontaktieren Sie unsere Experten noch heute!