Das Feststoffsintern und das Flüssigphasensintern sind zwei unterschiedliche Verfahren zur Verdichtung von pulverförmigen Werkstoffen, die jeweils eigene Mechanismen und Anwendungen haben.Das Festkörpersintern beruht auf der Diffusion von Atomen, um Partikel ohne Schmelzen zu verbinden, und eignet sich daher für Keramiken wie Zirkoniumdioxid und Aluminiumoxid.Beim Flüssigphasensintern hingegen wird ein Material mit niedrigem Schmelzpunkt zugegeben, das bei Sintertemperaturen eine flüssige Phase bildet, die die Umlagerung und Bindung der Teilchen erleichtert.Dieses Verfahren eignet sich besonders für schwer zu verdichtende Keramiken wie Siliziumnitrid und Siliziumkarbid.Die Wahl zwischen diesen Methoden hängt von den Materialeigenschaften, den gewünschten Verdichtungsraten und den Sintertemperaturen ab.
Die wichtigsten Punkte werden erklärt:
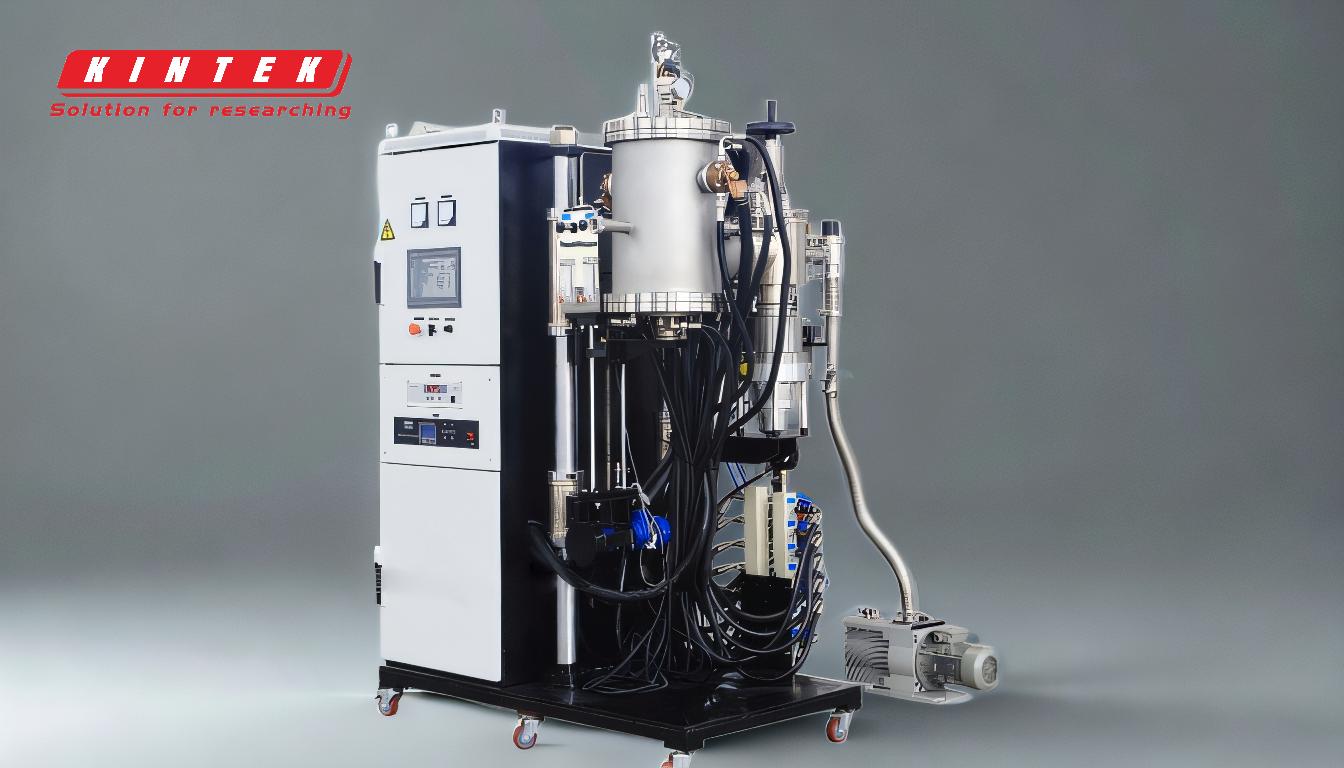
-
Mechanismus der Bindung:
- Festkörpersintern:Bei diesem Verfahren werden pulverförmige Materialien auf eine Temperatur knapp unter ihrem Schmelzpunkt erhitzt.Die Bindung erfolgt durch atomare Diffusion, bei der sich die Atome über die Partikelgrenzen hinweg bewegen, was zu einer Verdichtung und Festigkeit führt.Bei diesem Verfahren gibt es keine flüssige Phase.
- Flüssig-Phasen-Sintern:Hier wird eine kleine Menge eines niedrigschmelzenden Zusatzstoffes zugegeben.Bei Sintertemperaturen bildet dieser Zusatzstoff eine flüssige Phase.Die Flüssigkeit unterstützt die Umlagerung der Partikel aufgrund von Kapillarkräften und verbessert die Verdichtung und Bindung.
-
Temperatur-Anforderungen:
- Festkörpersintern:Erfordert in der Regel höhere Temperaturen, da er ausschließlich auf atomarer Diffusion beruht.Das Fehlen einer flüssigen Phase bedeutet, dass das Material nahe an seinem Schmelzpunkt erhitzt werden muss, um eine ausreichende atomare Mobilität zu erreichen.
- Flüssigphasensintern:Im Vergleich zum Feststoffsintern wird im Allgemeinen bei niedrigeren Temperaturen gearbeitet.Durch das Vorhandensein einer flüssigen Phase wird die für die Umlagerung und Bindung der Partikel benötigte Energie reduziert, wodurch das Verfahren energieeffizienter ist.
-
Material Eignung:
- Festkörpersintern:Am besten geeignet für Materialien, die allein durch Diffusion verdichtet werden können, wie z. B. Zirkoniumdioxid und Tonerde.Diese Werkstoffe haben relativ niedrige Schmelzpunkte und können ohne Flüssigphase effektiv verdichtet werden.
- Flüssigphasensintern:Ideal für schwerer zu verdichtende Materialien wie Siliziumnitrid und Siliziumkarbid.Diese Materialien haben hohe Schmelzpunkte und erfordern zusätzliche Mechanismen, wie das Vorhandensein einer flüssigen Phase, um eine effektive Verdichtung zu erreichen.
-
Verdichtungsrate:
- Festkörpersintern:Die Verdichtungsrate ist im Allgemeinen langsamer, da sie auf der Diffusion von Atomen beruht, die im Vergleich zu den Mechanismen in der Flüssigphase ein langsamerer Prozess ist.
- Flüssigphasensintern:Bietet eine schnellere Verdichtungsrate aufgrund der erhöhten Mobilität der Partikel in Gegenwart einer flüssigen Phase.Dies macht es besonders nützlich, wenn eine schnelle Verdichtung gewünscht ist.
-
Anwendungen:
- Festkörpersintern:Wird häufig bei der Herstellung von keramischen Komponenten verwendet, bei denen hohe Reinheit und strukturelle Integrität entscheidend sind.Beispiele sind medizinische Implantate, Schneidwerkzeuge und elektronische Substrate.
- Flüssig-Phasen-Sintern:Wird häufig bei der Herstellung von Hochleistungskeramik und Verbundwerkstoffen verwendet, die eine hohe Festigkeit und Zähigkeit erfordern.Zu den Anwendungen gehören Komponenten für die Luft- und Raumfahrt, Schneidwerkzeuge und verschleißfeste Teile.
-
Vorteile und Beschränkungen:
-
Festkörpersintern:
- Vorteile:Erzeugt hochreine Materialien mit minimaler Kontamination.Geeignet für Materialien, die keine schnelle Verdichtung erfordern.
- Beschränkungen:Langsameres Verfahren und erfordert höhere Temperaturen, die energieintensiv sein können.
-
Flüssig-Phasen-Sintern:
- Vorteile:Schnellere Verdichtung, niedrigere Sintertemperaturen und effektiv für hochschmelzende Materialien.
- Beschränkungen:Potenzielle Verunreinigung durch die flüssige Phase und eventuell erforderliche Nachsinterung zur Entfernung von Flüssigkeitsresten.
-
Festkörpersintern:
Zusammenfassend lässt sich sagen, dass die Wahl zwischen Feststoffsintern und Flüssigphasensintern von den spezifischen Materialeigenschaften und den gewünschten Ergebnissen des Sinterprozesses abhängt.Das Feststoffsintern ist ideal für Werkstoffe, die allein durch Diffusion verdichtet werden können, während das Flüssigphasensintern besser für schwerer zu verdichtende Werkstoffe geeignet ist, die von der Anwesenheit einer flüssigen Phase profitieren.Das Verständnis dieser Unterschiede ist entscheidend für die Auswahl des geeigneten Sinterverfahrens für eine bestimmte Anwendung.
Zusammenfassende Tabelle:
Aspekt | Festphasen-Sintern | Flüssig-Phasen-Sintern |
---|---|---|
Mechanismus | Diffusion von Atomen ohne Schmelzen | Flüssige Phase unterstützt die Umlagerung und Bindung von Teilchen |
Temperatur | Höhere Temperaturen (nahe dem Schmelzpunkt) | Niedrigere Temperaturen aufgrund der flüssigen Phase |
Material Eignung | Zirkoniumdioxid, Tonerde (niedrigere Schmelzpunkte) | Siliziumnitrid, Siliziumkarbid (hohe Schmelzpunkte) |
Verdichtungsrate | Langsamer (beruht auf atomarer Diffusion) | Schneller (verstärkt durch flüssige Phase) |
Anwendungen | Medizinische Implantate, Schneidwerkzeuge, elektronische Substrate | Luft- und Raumfahrtkomponenten, verschleißfeste Teile, Schneidewerkzeuge |
Vorteile | Hohe Reinheit, minimale Verunreinigung | Schnellere Verdichtung, niedrigere Temperaturen, effektiv für Materialien mit hohem Schmelzpunkt |
Beschränkungen | Langsamerer Prozess, energieintensiv | Mögliche Verunreinigung, Nachsinterung kann erforderlich sein |
Benötigen Sie Hilfe bei der Auswahl des richtigen Sinterverfahrens für Ihre Materialien? Kontaktieren Sie noch heute unsere Experten für maßgeschneiderte Lösungen!