Die Imprägnierungsmethode ist eine weit verbreitete Technik bei der Katalysatorherstellung, bei der ein poröses Trägermaterial mit einer Lösung getränkt wird, die die aktive Metallvorstufe enthält.Die Lösung dringt in die Poren des Trägers ein, und nach dem Trocknen und Kalzinieren zersetzt sich die Metallvorstufe und bildet den aktiven Katalysator.Diese Methode ermöglicht eine genaue Kontrolle der Metallbeladung und -verteilung und ist daher für verschiedene industrielle Anwendungen geeignet.Das Verfahren umfasst mehrere Schritte, darunter die Vorbereitung des Trägers, die Imprägnierung, die Trocknung und die Kalzinierung, von denen jeder einzelne optimiert werden kann, um die gewünschten Katalysatoreigenschaften zu erzielen.
Die wichtigsten Punkte werden erklärt:
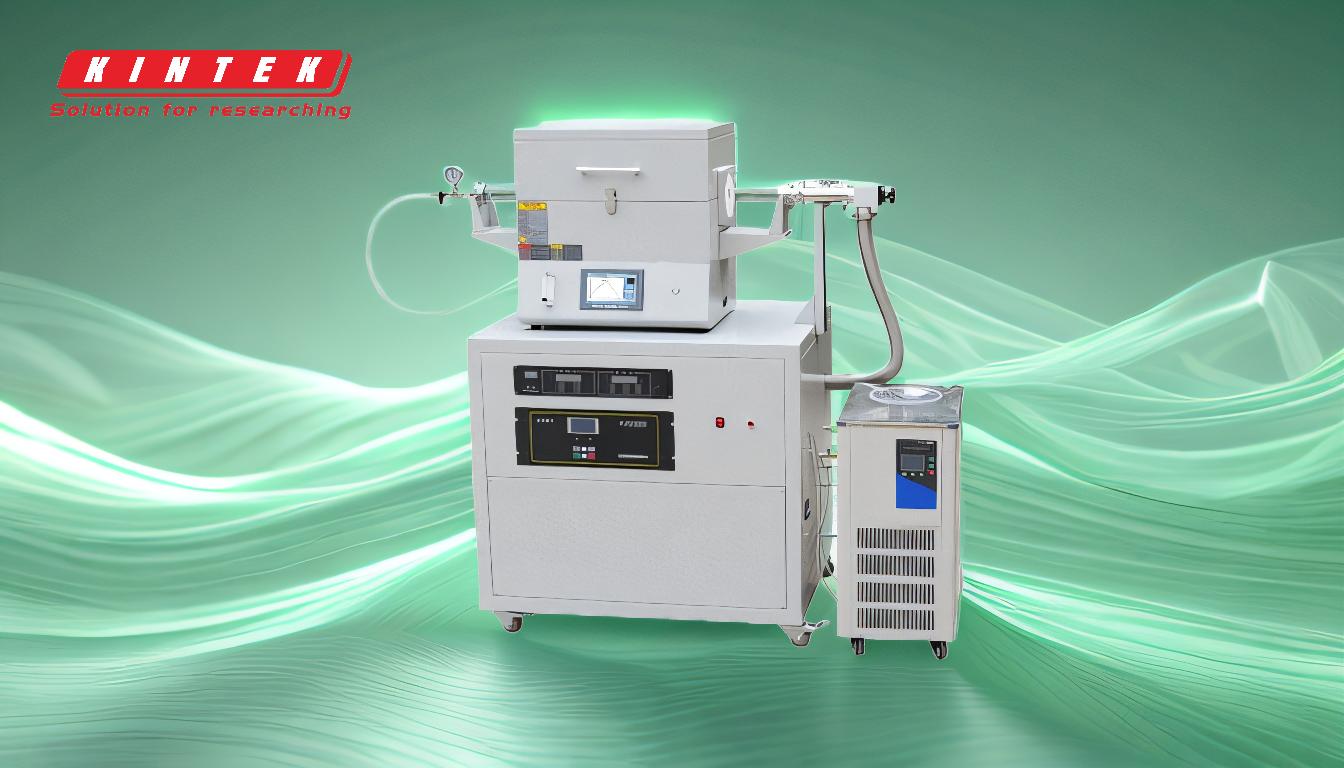
-
Unterstützungsmaterial Vorbereitung:
- Das Trägermaterial, häufig ein poröser Feststoff mit großer Oberfläche wie Aluminiumoxid, Siliziumdioxid oder Zeolithe, wird vorbereitet, um sicherzustellen, dass es die Metallvorläuferlösung wirksam adsorbieren kann.
- Der Träger wird in der Regel vorbehandelt, um Verunreinigungen zu entfernen und eine einheitliche Porenstruktur zu schaffen, die für eine gleichmäßige Verteilung des aktiven Metalls entscheidend ist.
-
Imprägnierungsverfahren:
- Der Träger wird in eine Lösung getaucht, die den Metallvorläufer (z. B. Metallsalze wie Nitrate, Chloride oder Acetate) enthält.
- Die Lösung kann entweder durch Kapillarwirkung oder unter Vakuum in die Poren des Trägers eindringen, wodurch sichergestellt wird, dass die Metallvorstufe gleichmäßig auf dem Träger verteilt wird.
- Die Konzentration des Metallvorläufers in der Lösung bestimmt die endgültige Metallbeladung des Katalysators.
-
Trocknung:
- Nach der Imprägnierung wird der nasse Träger getrocknet, um das Lösungsmittel zu entfernen, wobei der Metallvorläufer in den Poren zurückbleibt.
- Die Trocknungsbedingungen (Temperatur, Zeit und Atmosphäre) werden sorgfältig kontrolliert, um die Migration des Metallvorläufers an die Oberfläche zu verhindern, was zu einer ungleichmäßigen Verteilung führen könnte.
-
Kalzinierung:
- Das getrocknete Material wird dann bei hohen Temperaturen (in der Regel 300-600 °C) in einer oxidierenden Atmosphäre kalziniert.
- Während der Kalzinierung zersetzt sich der Metallvorläufer und bildet das aktive Metalloxid oder die Metallphase.
- Der Kalzinierungsschritt trägt auch zur Stabilisierung der Katalysatorstruktur und zur Entfernung etwaiger restlicher organischer Verbindungen bei.
-
Reduktion (falls zutreffend):
- Bei Katalysatoren, die eine metallische aktive Phase erfordern, wird nach der Kalzinierung ein Reduktionsschritt durchgeführt.
- Der Katalysator wird bei erhöhten Temperaturen mit einem reduzierenden Gas (z. B. Wasserstoff) behandelt, um das Metalloxid in den metallischen Zustand zu überführen.
-
Vorteile der Imprägnierungsmethode:
- Präzise Kontrolle:Die Methode ermöglicht eine genaue Kontrolle der Metallbeladung und -verteilung, was für das Erreichen der gewünschten katalytischen Aktivität und Selektivität entscheidend ist.
- Vielseitigkeit:Es kann mit einer breiten Palette von Trägermaterialien und Metallvorläufern verwendet werden und eignet sich daher für verschiedene katalytische Anwendungen.
- Skalierbarkeit:Das Verfahren ist leicht skalierbar und eignet sich daher für die Katalysatorproduktion im industriellen Maßstab.
-
Beschränkungen und Überlegungen:
- Porenverstopfung:Eine zu hohe Konzentration des Metallvorläufers kann zur Verstopfung der Poren führen, wodurch die effektive Oberfläche des Katalysators verringert wird.
- Verteilung der Metalle:Eine ungleichmäßige Trocknung oder Kalzinierung kann zu einer ungleichmäßigen Metallverteilung führen, die die Leistung des Katalysators beeinträchtigt.
- Kosten:Das Verfahren kann kostenintensiv sein, da hochreine Ausgangsstoffe und kontrollierte Verarbeitungsbedingungen erforderlich sind.
-
Anwendungen:
- Die Imprägnierungsmethode wird bei der Herstellung von Katalysatoren für verschiedene industrielle Prozesse eingesetzt, darunter Erdölraffination, chemische Synthese und Umweltkatalyse.
- Beispiele hierfür sind Katalysatoren für die Wasserstoffbehandlung, Oxidationskatalysatoren und Autoabgaskatalysatoren.
Zusammenfassend lässt sich sagen, dass die Imprägnierungsmethode eine vielseitige und weit verbreitete Technik für die Katalysatorvorbereitung ist, die eine genaue Kontrolle über die Metallbeladung und -verteilung ermöglicht.Allerdings ist eine sorgfältige Optimierung der einzelnen Schritte erforderlich, um die gewünschten Katalysatoreigenschaften und -leistungen zu erzielen.
Zusammenfassende Tabelle:
Wichtige Schritte | Beschreibung |
---|---|
Vorbereitung des Trägers | Vorbehandlung poröser Materialien wie Aluminiumoxid oder Siliziumdioxid für eine gleichmäßige Metallverteilung. |
Imprägnierungsverfahren | Eintauchen des Trägers in eine Metallvorläuferlösung für eine gleichmäßige Durchdringung. |
Trocknen | Entfernen des Lösungsmittels unter kontrollierten Bedingungen, um eine ungleichmäßige Verteilung zu verhindern. |
Kalzinierung | Erhitzung zur Zersetzung des Vorläufers in die aktive Metallphase. |
Reduktion (falls erforderlich) | Umwandlung von Metalloxiden in metallische Zustände unter Verwendung reduzierender Gase wie Wasserstoff. |
Vorteile | Präzise Steuerung, Vielseitigkeit und Skalierbarkeit für industrielle Anwendungen. |
Beschränkungen | Risiko der Porenverstopfung, ungleichmäßige Verteilung und höhere Kosten. |
Anwendungen | Einsatz in der Erdölraffination, der chemischen Synthese und der Umweltkatalyse. |
Entdecken Sie, wie das Imprägnierverfahren Ihre Katalysatorvorbereitung optimieren kann. Kontaktieren Sie unsere Experten noch heute !